Coloration Leaders Committed to Sustainable Change
Many new companies are suddenly gaining traction in the development of sustainable new dyes and finishing treatments, as outlined by Geoff Fisher in his article here of this issue of International Fiber Journal.
However, two of the leading conventional textile coloration and specialty chemicals businesses – Archroma and DyStar – are both well placed to capitalize on considerable global resources and vast know-how banks in the pursuit of sustainable new solutions for the industry.
Both companies have assumed their current structures through a succession of mergers and acquisitions and some of the most significant have taken place since the formation of Archroma in 2013.
Archroma has Heritage
Archroma can trace its heritage back to the establishment of Kern & Sandoz in 1886 to produce textile dyes in Basel, Switzerland. This company grew over the decades and in 1995 Clariant was formed as a spin-off from Sandoz and in 1997 acquired the specialty chemicals business of Hoechst.
In 2013 New York-headquartered SK Capital Partners acquired the then Textile Chemicals, Paper Specialties and Emulsions businesses from Clariant and the three divisions were combined into an integrated company and renamed Archroma.
In July 2015 Archroma acquired the global textile chemicals business of BASF, and between 2014 and 2018, M. Dohmen, an international group specializing in the production of textile dyes and chemicals for the automotive, carpet and apparel sectors. Finally, in February 2023, Archroma acquired Huntsman Textile Effects, bringing together the two global leaders in coloration technologies for the textile industry.
By 2022, Archroma’s annual sales were $1.4 billion, with 39% achieved in Asia, 32% in EMEA and 29% in the Americas. Meanwhile, in its financial year to June 30, 2022, the turnover of Huntsman Textile Effects was $772 million.
EarthColors
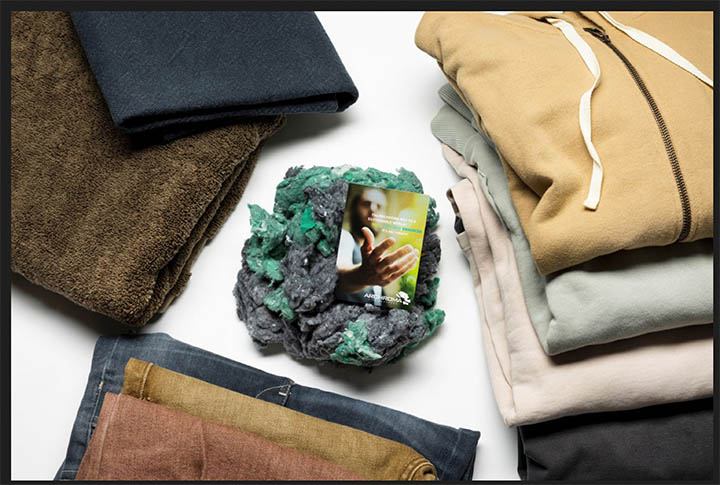
Among notable product developments from Archroma in recent years has been the successful EarthColors range of Diresul dyes created from agricultural and herbal waste, with raw materials largely supplied from Spain.
Earth-Oak is 100% derived from almond-shell residues supplied by an agricultural cooperative, while Earth-Cotton is derived from cotton plant residues provided by a supply chain supported by Cotton Incorporated. Residues derived from the extraction of premature grapefruit and bitter orange fruit in southern Spain are employed for Earth-Sand dyes and residues obtained after the extraction of
sugar from beetroot provide the coloring for Earth-Clay.
Both Earth-Forest and Earth-Stone shades are obtained from the residues remaining after the extraction of saw palmetto fruits which are primarily used for herbal extracts.
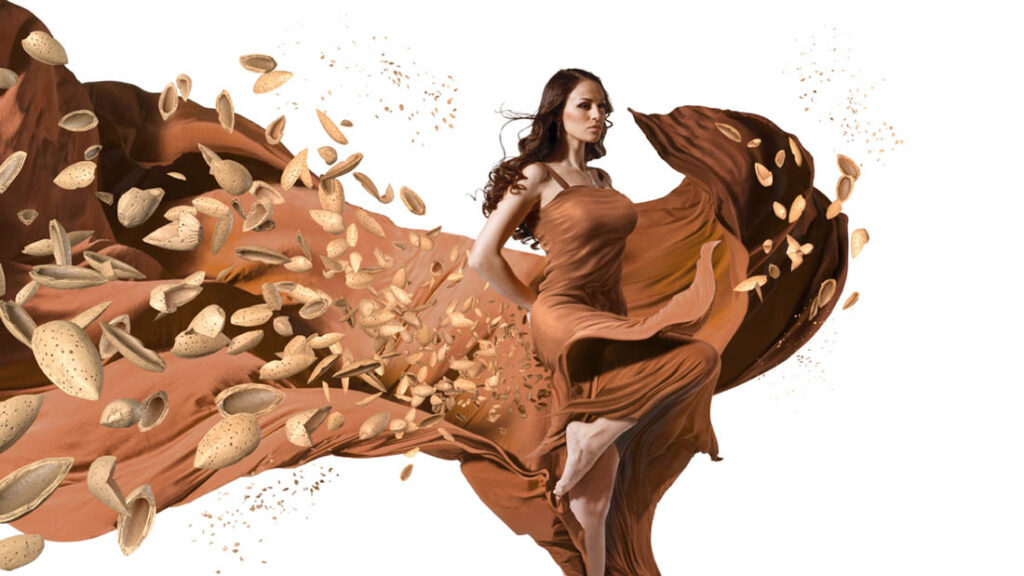
FiberColors Range
The recently-launched and patent-pending FiberColors range is based on a method for using waste cotton and/or polyamide fibers and their blends into a feedstock to replace a major part of the petroleum-based raw material usually used to make dyes – with a purity of more than 95%.
The resulting range includes five dyes covering a palette of brown, olive, maroon, blue grey and dark grey shades. The dyes are synthesized with a minimum content of 50% waste-based raw material and
especially suitable for dyeing cellulose fibers such as cotton, viscose, linen and kapok. They can be used in continuous, exhaust, denim and garment dyeing and printing.
The development now enables brands to turn their own pre- and post-consumer textile waste into new dyes and create completely new collections. Many other Archroma developments are centered on enhancing recipe formulations to enable customers to achieve savings in water, energy and raw materials.
Awareness
“We continue to operate against a backdrop of heightened environmental awareness, extreme weather events and growing economic and geopolitical instability,” says Archroma CEO Mark Garrett, in his introduction to the company’s 2023 Sustainability report. “This is changing how people shop and how investment decisions are made, and prompting a global move towards the circular economy and the production of goods that are safer and more durable, repairable and recyclable.
“Within this complex landscape, we see the green shoots of opportunity and recovery. Archroma remains committed to working with stakeholders to nurture this new growth by advancing our industry towards a more sustainable future. We believe that this can only be achieved through a shared journey where transparency, ethics and inclusion are valued. These principles guide our innovation efforts and our interactions with customers, partners, employees and the world around us.”
DyStar Eco-Growth
Tracing an earlier arc of mergers and acquisitions is DyStar, which since 2010 has been jointly owned by China’s Zheijang Longsheng Group and India’s Kiri Industries and operates as a subsidiary of Zheijang Longsheng with corporate headquarters now in Singapore.
Today, DyStar has 13 production sites and 1,700 employees operating in 50 countries and in 2022 had annual sales of $899 million.
DyStar was also founded in 1995, as a joint venture between Hoechst, Bayer Textile Dyes and Mitsubishi, with headquarters then in Frankfurt, Germany. In 2000, DyStar integrated the textile dyes business of BASF including ICI/Zeneca Dyes and Mitsui into the company, establishing itself as a coloration specialist.
Further acquisitions have included Color Solutions in 2022, Boehm Group, Rotta Group and Yorkshire Americas in 2005, Texanlab in 2007, Lenmar Chemicals in 2013 and Emerald Performance Materials in 2016.
Influenced by the need to evaluate and improve the industry’s impact on the environment, DyStar released its first Sustainability and Carbon Footprint report in 2011 and founded its Sustainable Textile Solutions division a year later.
Cadira
All of DyStar’s Cadira modules designed for the coloration of virtually all commonly used textile fibers have been developed to enable savings on water, energy, waste, greenhouse gas emissions and process time. Among notable recent developments is Eco-Advanced Indigo Dyeing which enables dyers to reduce water usage by up to 90% and energy consumption by up to 30% during the production process.
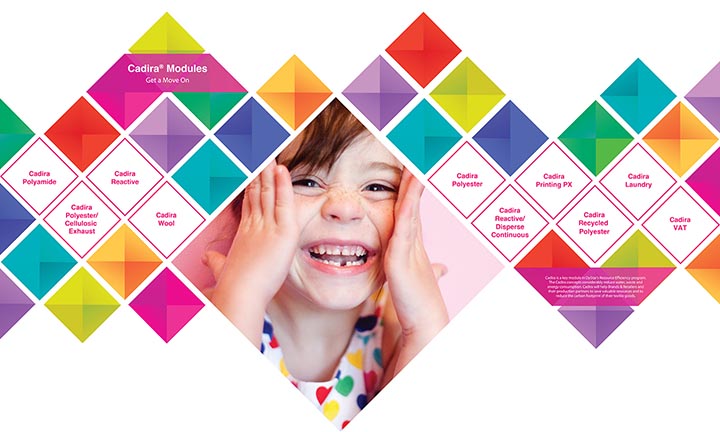
It is applicable in the traditional indigo dyeing process for sulfur dyes and colored denim and has already been proven to substantially reduce the effluent load in production, helping customers deliver consistency in quality while achieving less wastewater treatment in the effluent.
PS2
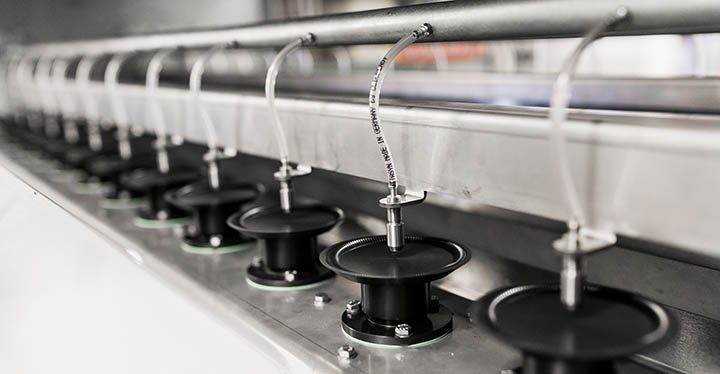
DyStar has also worked with Germany’s RotaSpray on the development of the PS2 process for dyeing denim yarns and fabrics. This combines the use of the RotaSpray RotoDyer – based on rotating atomizers – with a range of DyStar’s dyes and process auxiliaries.
A common problem with denim dyeing is the limitation in other dyes that can be combined successfully with indigo and sulfur dyes to provide specific shades and effects. PS2 overcomes these limitations and allows a previously un-achievable variety of colors in the continuous dyeing of warp yarns, particularly for small lots that are typically prone to inconsistent dyeing when processed on traditional, larger-scale equipment.
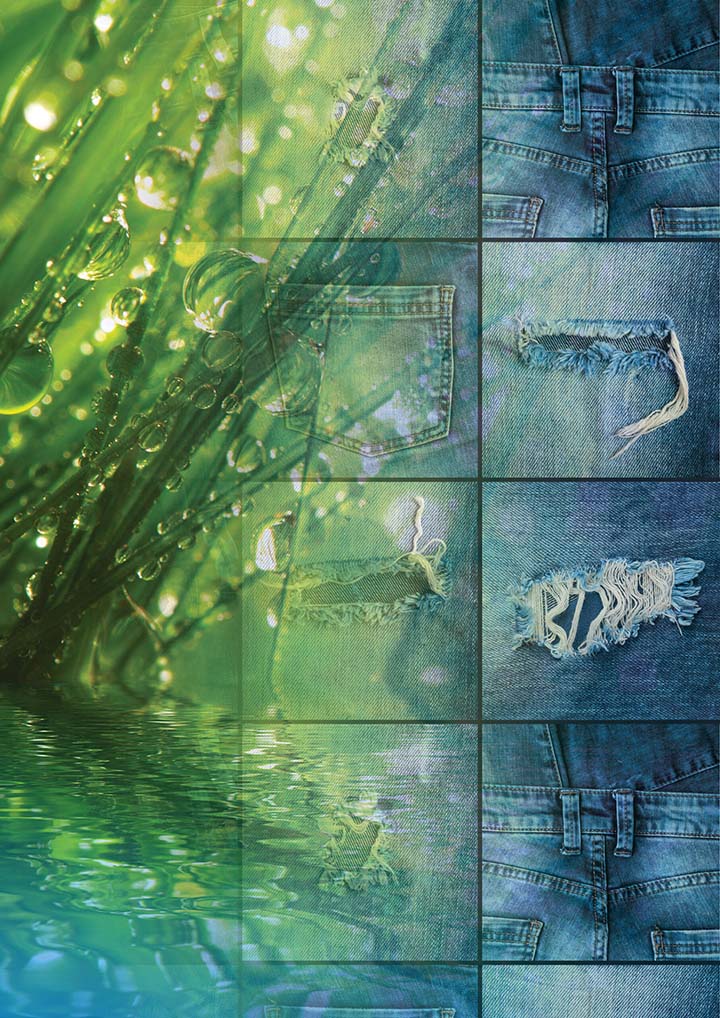
Mixtures of indigo, sulfur and vat dyes can now be applied in a single step, without fear of the differences in affinity and exhaustion behavior of the dyes leading to a non-uniform finish. In addition, when using reactive and vat dyes, the contactless application of the process prevents contamination, which otherwise can result in undesirable hydrolysis, and removes the need for an intermediate drying stage.
PS2 has already been successfully adopted by a number of major denim manufacturers, including Artistic Fabric Mills and Nishat Mills in Pakistan, Arvind in India, Mou Fung in China and Orta in Turkey.
No Compromise
“We acknowledge that challenges are increasing in making our global supply chain cleaner, better and more efficient,” says DyStar CEO Eric Hopmann in the company’s combined 2022-23 Sustainability Report. “Water consumption in many regions poses a real threat and energy supply is becoming more expensive. We are determined to help our customers by offering new solutions without compromising quality and performance.
“One of the key opportunities ahead lies in striking the right balance between improving our environmental footprint and managing costs effectively. DyStar, with its established setup, is well-equipped to meet these challenges. By leveraging our expertise, expanding into differentiated product categories and embracing biotechnologies, we aim to address emerging market demands and meet the evolving needs of the market.”