Developing Initiatives Show Promise
End-of-life options for nonwoven fabrics are very much dependent on their end-use application, with around 50% of them being employed in durable products such as filter media, construction materials, floor and wall coverings and geotextiles. Once at the end of their useful life, such materials, are theoretically recyclable using established mechanical tearing processes, but the reality is inevitably much more complex.
Filter Bags
Many hundreds of heavy-duty needlepunched filter bags, for example, can be used at a single site in industries such as power generation, cement manufacturing and waste incineration. These filter bags can be up to 40 feet long and need to be replaced at regular intervals, suggesting the potential for establishing some kind of circular system.
They are, however, extremely difficult to clean and can contain heavy metals, dioxins and other toxic substances, depending on the application. Cleaning processes would therefore have to be extremely aggressive, consuming a lot of energy and producing a large amount of waste, while at the same time severely damaging and reducing the value of the materials being recovered. When all other costs are factored in, such recycling is a far from practical exercise.
Geotextiles
Similar cost obstacles exist for geotextiles, which are buried under structures and intended to remain there for many decades. This means that no thought was given at all to the recyclability of the materials that may now be nearing their end-of-life and recovery is generally in the hands of independent reclamation companies who have no idea of what they’re dealing with.
Manufacturers of new geotextiles, however, are now facing impossible demands from specifiers for products that are both 100% plastic-free and at the same time have a guaranteed performance life of 50, or even 100 years.
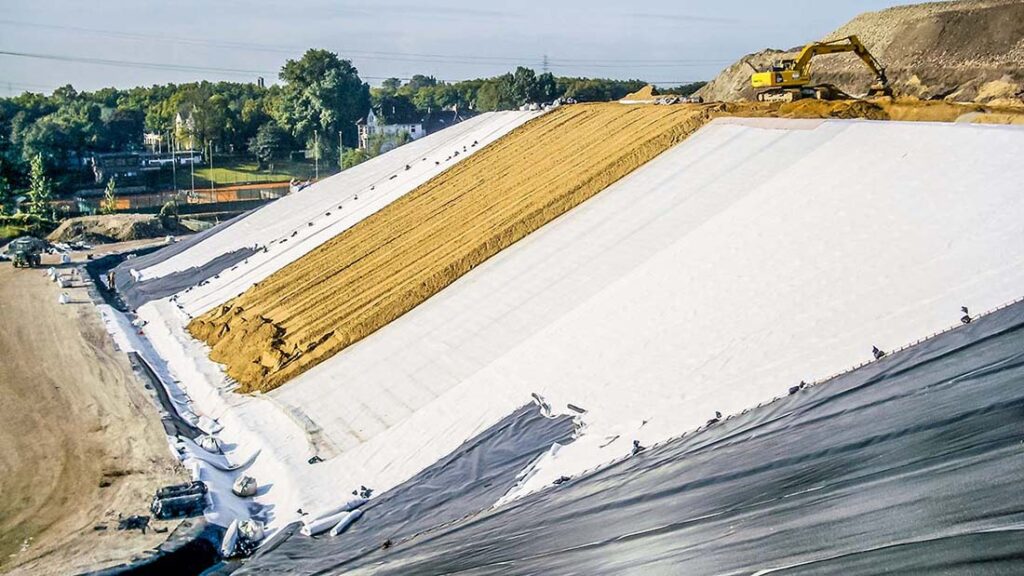
Chris Quirk, managing director of Naue Geosynthetics UK, has outlined this dilemma following his company’s introduction of a high-performance range of geotextiles called GreenLine, which are available in a weight range of 300-1,000gsm and based on PLA.
“The problem we face is that under the current European Union Construction Pro-
ducts Directive, geotextiles based on bio-plastics, as well as recycled products, can only receive a durability rating of five years,” Quirk says. “This is as opposed to virgin plastics like polypropylene which can have guaranteed durability of up to 100 years. “It means that our new PLA products can only be used in temporary works at present, although we know that PLA has far greater durability than the guarantee we are allowed to give.”
Meanwhile there is a rise in the application of bans on the use of plastics in construction works, notably in National Parks in Europe, California and New Zealand.
“It’s a tick-box exercise for contractors who ask for both no plastic and a 100-years guarantee,” Quirk observed. “For some challenging applications, fossil-based plastic will always have to be used and there is good bio-based plastic too, but this is not understood by regulators.”
Automotive
Many nonwoven-based automotive interior components are now being both made from recycled materials and marketed as suitable for recycling and in July 2023 the European Commission published its proposal for an End-of-Life Vehicles Directive. This will mandate the reuse, recycling and recovery targets for plastic and fibers from the more than six million vehicles that are scrapped in the European Union each year.
What currently happens to such waste is far from ideal.
In many instances, metals, tires and glass account for 80-90% of the materials from end-of-life vehicles that are recycled through traditional mechanical recycling streams, while the other 10-20% is rather tragically referred to as ‘automotive shredder residue’ (ASR). This consists of mixed plastic and other non-recycled materials that today generally end up in landfills or are recovered through waste-to-energy technologies – including the many nonwovens and technical textiles employed in vehicles such as interior surface fabrics, insulating materials, filters, cords and belts.
Value
Even ASR, however, can potentially be given a second life, and this was the aim of chemicals major Eastman, working in a 2023 project with the United States Automotive Materials Partnership (USAMP), the automotive scrap recycler Padnos and global automotive interiors supplier Yanfeng. In this project, Padnos, headquartered in Holland, Michigan, supplied a plastic-rich fraction of ASR as a sustainable feedstock for Eastman’s carbon renewal technology (CRT).
Eastman has subsequently demonstrated the conversion of the ASR feedstock into a synthesis gas (syngas) which is then used downstream in the production of its polyester and cellulosic thermoplastics.
Resins from this production process were further formulated and then supplied to Yanfeng and molded into demonstration components meeting the requirements of OEM vehicle manufacturers Ford, GM and Stellantis, demonstrating proof of concept for a truly circular solution.
The study proved the feasibility of Eastman’s CRT, which breaks down the plastic-rich ASR into molecular building blocks. By recycling these complex plastics into their monomers, the company can replace fossil-based feedstock and create polymers without compromising performance, for use in new automotive applications.
This is a pragmatic potential solution to an existing industry practice, but the system must adapt to the circular economy.
AHPs
The other 50% of nonwovens produced globally are meanwhile used in absorbent hygiene products (AHPs) and other single-use consumer items, where end-of-life options are also exceedingly limited, despite ongoing small-scale industry initiatives.
The considerable post-consumer waste AHPs generate is estimated to be in the region of 30 million tons each year, most of which is either incinerated or sent to landfill. Considering the $65 billion baby diaper market alone, this equates to 1.5 billion diapers that are disposed of globally on a daily basis – 18,000 each second – and this is waste that is not currently in a fit state to be recycled by simple recovery of its constituent parts.
Pilot Projects
Various projects have been established in recent years, such as the pilot diaper collection bins in Amsterdam by Procter & Gamble and partners, while FaterSMART has operated a diaper recycling plant in Contarina, Italy, for the past decade, with an annual capacity of 10,000 tons.
Ontex and Les Alchimistes in France operate a regional diaper collection scheme with the goal of dealing with 500 million diapers by 2030 and the scheme is currently being expanded to Belgium.
In Australia, Kimberly-Clark has established a collection and recycling scheme in Australia in which around 1.5 billion diapers are being collected annually.
Waste-to-Energy
Most recent, Kimberly-Clark’s Huggies brand is partnering with select Bright Horizons childcare centers in Boston to collect used diapers & wipes, and turn the waste into electricity, heat or fuel. Waste-to-
energy technology, a process managed by Covanta, offsets the use of fossil fuels and reduces carbon emissions and methane generation from landfills at many facilities around North America, including Boston.
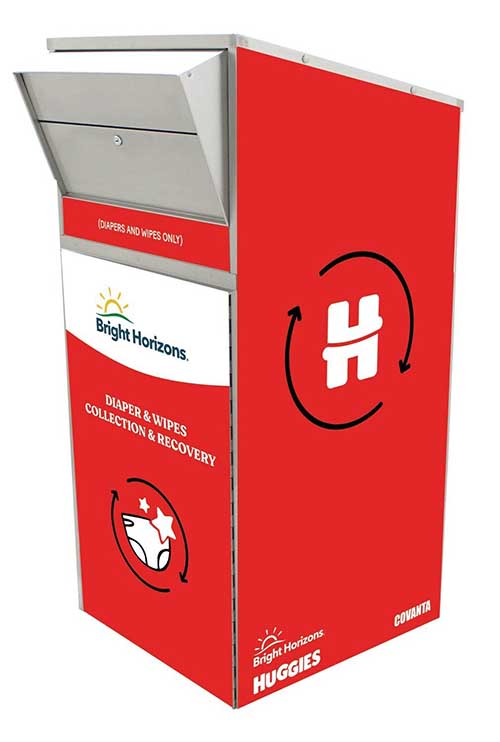
Waste-to-energy takes non-hazardous waste – otherwise destined for landfill – and combusts it, generating steam for electricity production. The resulting ash is also processed to recover metal for recycling while all gases are collected, filtered, and cleaned to minimize environmental impact. The pilot will run at select Boston-area Bright Horizons centers and pending outcomes, Huggies and Bright Horizons could expand it to other cities.
Biochar
Dyper, headquartered in Scottsdale, Arizona, is already running diaper collections in 21 U.S. cities through its Redyper system, with the waste having initially been separated by a combination of composting and pyrolysis, with carbon sequestration.
The company has subsequently developed a process for turning used diapers into biochar, which it believes is a potentially economic and realistic solution to this major consumer waste stream. This is the first time biochar will be used to address disposable diaper waste.
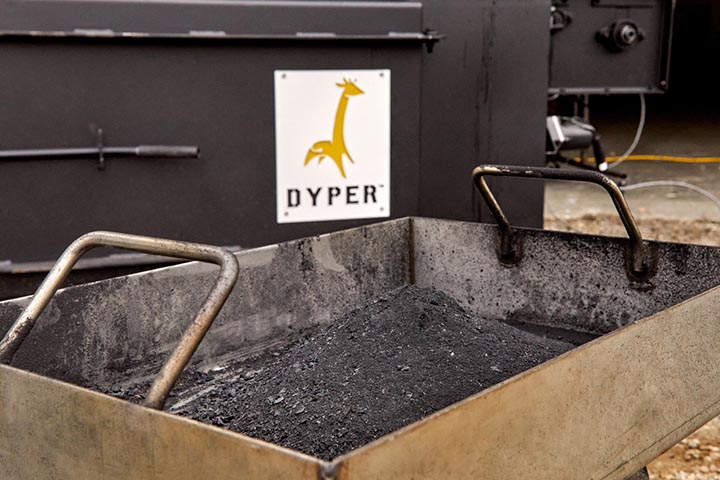
Biochar is a carbon-rich product which allows for waste to be transformed into a reusable commodity that can improve soil, assist in air and water purification and be used as an additive in paints and inks for improved pigmentation.
“While there are no silver bullets to solving the plastic diaper dilemma, we feel it is our obligation to continuously look for solutions,” said Sergio Radovcic, founder and CEO of Dyper. “We’ve started with composting, fully aware of the inherent difficulties of doing it at scale. With this innovation, we will bring modular disposal technology to complement or replace composting closer to the consumer, reducing processing and transfer times.”
Potential
Redyper composts diaper waste to create topsoil and Byochar™ reduces the processing time for this from several months to minutes. In addition, an efficient Byochar™ reactor needs less space and electricity than a traditional composting facility. The reactors have the capacity to process two tons of diapers per day – 7,200 diapers every 10 hours, or 12 diapers a minute. Converting Dyper diapers and wipes to biochar yields an 80% reduction in mass –100 pounds of dry diapers yields approximately 20 pounds of biochar. The potential impact – and scale are enormous.