Demand is Growing for Lightweight Materials in Automotive and Other Transportation Markets
In the new era of mobility, with electrification at the forefront, original equipment manufacturers (OEMs) are looking for lightweight and high-strength materials for environmentally friendly and high-performance vehicles, with the aim of reducing weight and therefore carbon dioxide (CO2) emissions that contribute to global warming.
OEMs are continuing to prioritize mass reduction in vehicles, driving demand for lightweight alternatives, such as high-strength steels, aluminum and composites. Nonwovens, too, can be of value in the transportation sector by helping to make vehicles lighter, quieter and more comfortable as well as saving resources.
Non-Metallic Components
With an eye on efforts to reduce fuel emissions, the transportation sector is looking to increase the use of non-metallic components of vehicles, as well as railway carriages, aircraft and maritime vessels, by replacing metal components with nonwovens or fibrous composites that can reduce overall vehicle weight, thereby resulting in increased fuel efficiency.
In volume terms, the amount of textiles/nonwovens used in the average vehicle is relatively small compared with the overall vehicle weight, although the figure is growing.
As a result of higher demand for increased comfort and improved safety, the use of fiber-based materials has increased from 20 kg in a mid-size car in 2000 to around 40 kg today, according to the latest
estimates.
While woven and knitted fabrics continue to dominate this total amount of textiles used within the automotive industry, nonwovens are becoming an increasingly attractive option for designers owing to their low weight and lower cost, as well as other key properties such as sound insulation.
However, achieving scale in sustainable production will be essential for the widespread adoption of nonwovens, emphasizing the need for support in integrating these lightweight materials into mass-produced vehicles.
A number of automakers have made some undertakings to use more recycled materials in their latest models.
Many Different Uses
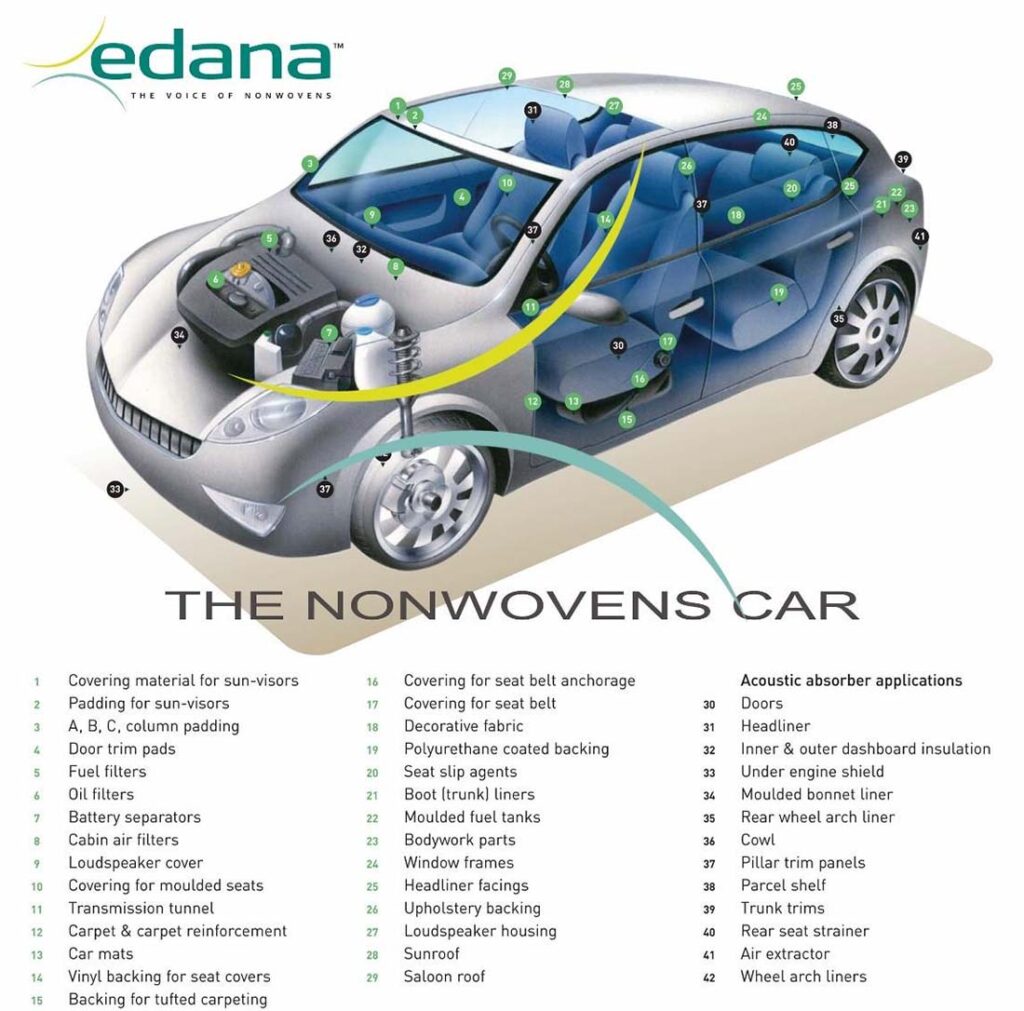
At present, nonwovens or composites that include nonwovens are used in around 40 different components in passenger vehicles, including seats, floorcoverings, headliners, trunk liners and hood liners, as well as underbody and wheel arch materials. They are also used in vehicle batteries, belts and tubes and single-use items such as filters.
Further, nonwovens are easy to handle during vehicle assembly: they are tailor-made for their function and can be heat-formed, embossed, lined, coated and printed. And owing to their versatility and numerous benefits they are also widely used in the design and construction of other vehicles and transportation modes, such as aircraft, trains, boats, spacecraft and satellites.
The consumption of automotive nonwovens is currently estimated at around 40 m2 per vehicle; visible nonwovens account for only 10% of the entire amount of the total flat textile surfaces in vehicles, or around 4 m2. However, the gradual replacement of traditional textiles and even non-traditional materials, particularly certain hard plastic or metal components, with nonwovens is ongoing.
In addition, a number of automakers have made some undertakings to use more recycled materials in their latest models, aiming for acoustic performance, light weight, and recycled and recyclable content. However, the development of these eco-designed products has been hampered by higher costs and potential risks linked with using recycled materials, according to Refashion, the French textile, household linen and footwear industry’s eco-organization.
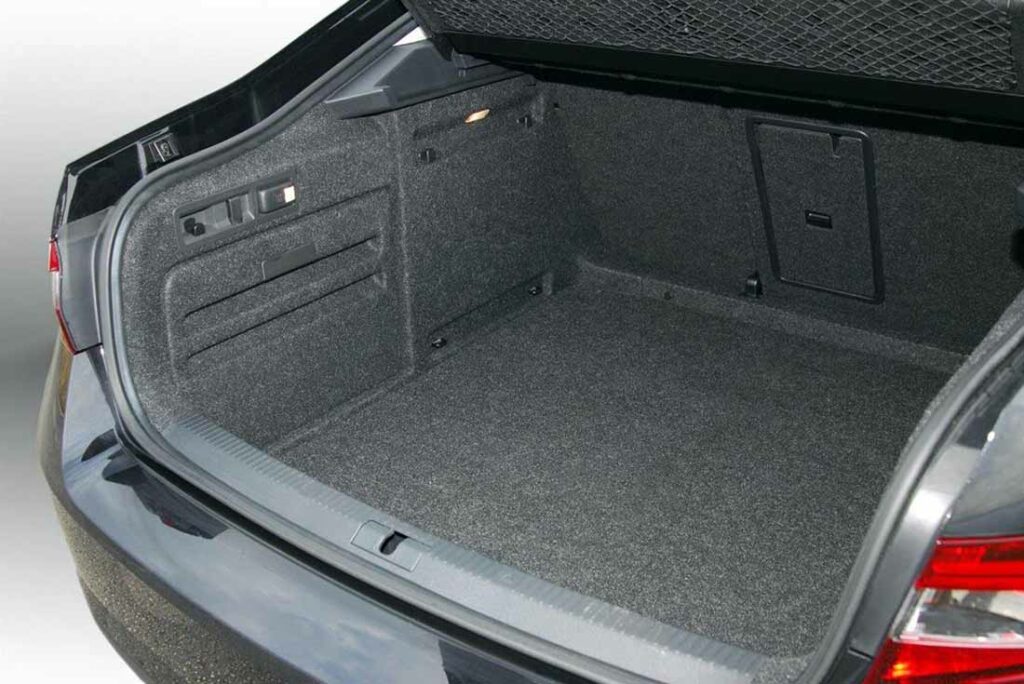
Acoustic Insulation
A major application for lightweight nonwovens in internal combustion engine vehicles is in insulating materials for absorbing engine noise and dampening the vibrations caused by it.
This is obviously unnecessary in electric vehicles (EVs), but noise reduction becomes even more critical for EVs because external as well as internal noise sources are more audible to drivers and passengers. In addition, without excess heat from the engine, the cabin of an EV can be significantly cooler than that of a conventional vehicle, which requires different insulating solutions.
While needle punched nonwoven layers have been used for several decades as acoustic insulation components for the interior of vehicles, they are now increasingly employed as undershields and outer wheel arch liners, replacing the heavier polyvinyl chloride layers and providing a significant reduction in weight.
Switzerland-based Autoneum, a leading supplier of vehicle acoustic and thermal insulation, is now offering its lightweight Propylat technology to reduce both interior and exterior noise of vehicles.
The technology was originally developed by Germany’s Borgers Automotive, which was acquired by Autoneum in early 2023. It is characterized by a flexible material composition of natural and synthetic fibers with a high recycled content and is said to contribute to significant waste reduction owing to its complete vertical integration.
The company said Propylat-based products not only contribute to reducing pass-by noise and improving driver comfort but are also up to 50% lighter than equivalent plastic alternatives, which results in a lower vehicle weight and, consequently, less fuel and energy consumption as well as lower CO2 emissions.
Propylat technology consists of a mixture of recycled synthetic and natural fibers, including cotton, jute, flax or hemp, which are consolidated using thermoplastic binding fibers without adding any chemical binders.
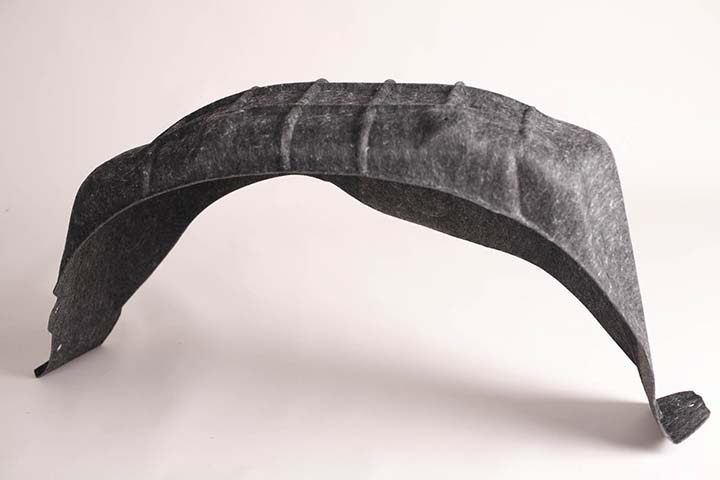
Owing to the flexible technology, fiber composition and the variable density and thickness of the porous material, the properties of the respective Propylat variant, for example with regards to acoustic performance, can be tailored to individual customer requirements.
This allows the technology to be applied in a variety of interior and exterior components, such as wheelhouse outer liners, trunk trim, underbody systems and carpets. For instance, Propylat-based wheelhouse outer liners are said to significantly reduce rolling noise, both inside and outside the vehicle, while at the same time offering protection against stone chipping and spray water.
Moreover, the Propylat PET variant, which consists of 100% polyethylene terephthalate, of which up to 70% are recycled fibers, is fully recyclable at the end of product life.
Integrated Damping Function
Earlier, Autoneum added an integrated damping function to fiber-based trim components, such as carpets or inner dashes, to improve their acoustic performance. Owing to the use of particle dampers, the company’s Zeta-Light not only insulates and absorbs airborne noise but also reduces low-frequency vibrations of the vehicle body, independent of temperature.
The technology is designed to improve the acoustic comfort of vehicle occupants while contributing to significant weight savings. It also simplifies parts logistics and the assembly process as well as recyclability in production and at the end of the vehicle’s life.
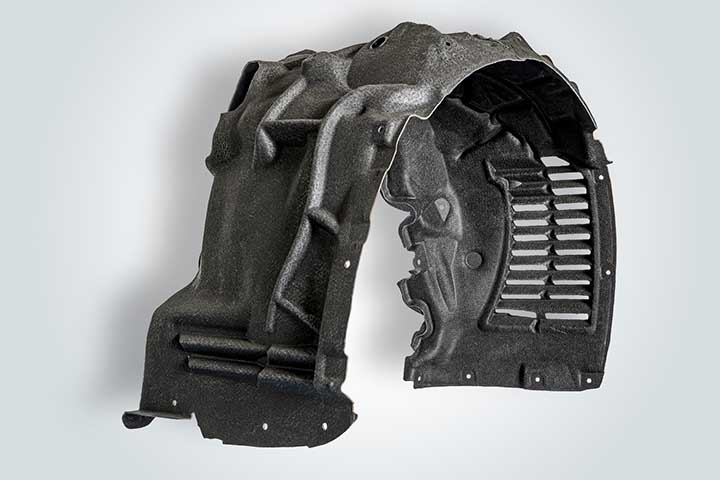
The integrated particle dampers developed by Autoneum complement the sound-insulating and absorbing properties of fiber-based, lightweight and sustainable technologies, such as Hybrid-Acoustics Eco+ or Prime-Light, with a new function for damping low-frequency vibrations of the vehicle body.
Compared with conventional damping alternatives, Zeta-Light allows for the reduction of both noise and vibration in a wider frequency range and at lower weight. In addition, the acoustic performance of the particle dampers is not affected by temperature, said Autoneum.
With Zeta-Light, small particles are enclosed in thin nonwoven capsules and integrated into the vehicle body side of noise-insulating components such as carpets or inner dashes. The capsule transfers the vibrations of the vehicle body to the particles and sets them in motion. Damping is achieved through collisions and friction between the individual particles.
Sustainable Solutions
Freudenberg Performance Materials showed several sustainable solutions for the automotive sector at this year’s Techtextil exhibition held in Frankfurt am Main, Germany.
A highlight at the trade fair was a novel polyester nonwoven material for car seat padding. Also available as a nonwoven composite with polyurethane foam, the material is said to be not only easier for automotive seat manufacturers to handle during the mounting process, but also ensures better dimensional stability as well as providing soft and flexible padding.
Further, the material is single origin and has low volatile organic compounds, ensuring a lower environmental impact. It also has a minimum of 25% recycled content, for example, by reusing nonwoven clippings and waste, and is fully recyclable. The company said full supply chain transparency enables customers to easily trace and verify the content of the nonwoven and thus ensures a responsible production process.
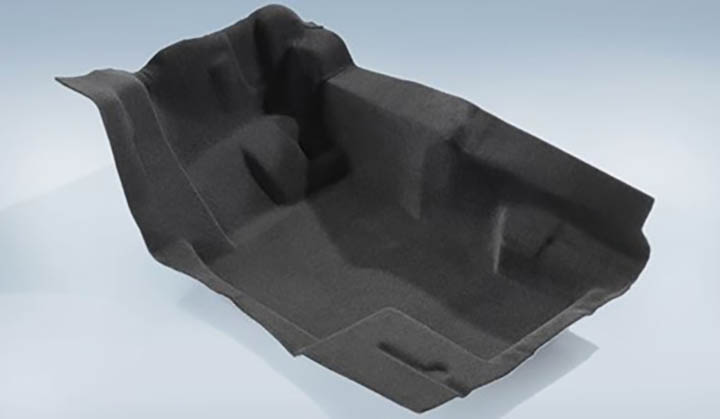
Freudenberg also showed several other nonwoven solutions made of up to 80% recycled materials that can be used in car seat manufacturing. For example, nonwovens based on its Lutraflor technology can be used for automotive carpets, insert mats and interior and trunk linings.
Made from recycled polyester, the material has a high-quality appearance, an environmentally friendly production process and excellent formability, while completely eliminating the use of latex and other chemical binders, the company stated. And compared with conventional automotive carpets, these nonwovens provide weight savings of up to 40%.
Lightweight Veils
UK-based Technical Fibre Products (TFP), part of the James Cropper group, showed its portfolio of lightweight nonwovens at the JEC World trade fair held in March in Paris, France.
Featuring nonwoven veils as light as 2 g/ m2, TFP’s products offer improved finish, enhanced fabrication and superior composites across industries including aerospace and advanced air mobility, wind energy, automotive applications and sporting goods.
Incorporated at the surface of the composite, on top of the structural component, TFP veils are highly porous and feature consistent fiber distribution and weight, ensuring a uniform resin wet-out and zero dry spots, the company stated.
Easy to handle and incorporate, the nonwovens minimize print-through from the underlying reinforcement, reducing the need for further processing of the finished part.
TFP’s lightweight nonwovens are accredited to AS 9100 and are already used extensively in the aerospace industry as an adhesive carrier or support for a fragile material.