Trends in Automotive Textiles Are Smart, Functional and Sustainable
In the transport sector, three key trends of development for automotive textiles are taking the lead – materials with characteristics that provide smartness, lighter weights, and reductions in environmental impact. Real market needs are driving the research and development (R&D) yielding innovation across smart textiles, such as Flexible Hybrid Electronics (FHE), used to achieve lightness and reduce fuel consumption, and natural fibers that bring about more sustainable composites. In examining these three areas, we will highlight some of the new developments that are emerging.
In the transport sector, three key trends of development for automotive textiles are taking the lead – materials with characteristics that provide smartness, lighter weights, and reductions in environmental impact. Real market needs are driving the research and development (R&D) yielding innovation across smart textiles, such as Flexible Hybrid Electronics (FHE), used to achieve lightness and reduce
fuel consumption, and natural fibers that bring about more sustainable composites. In examining these three areas, we will highlight some of the new developments that are emerging.
Smart Materials
Smart textiles for the transport market is estimated to be worth $1.04 billion in 2024 globally, and this is expected to rise to $3.92 billion by 2029, growing at a CAGR of 25.51% during that time according to a report by Mordor Intelligence. Causing growth is Internet of Things (IoT), miniaturization of electronics and other components, and the crucial growth of electric vehicles (EVs) – themselves seeing tremendous growth projected to be around $623.3 billion in 2024, growing to $906.7 billion by 2028 at a CAGR of 9.82%.
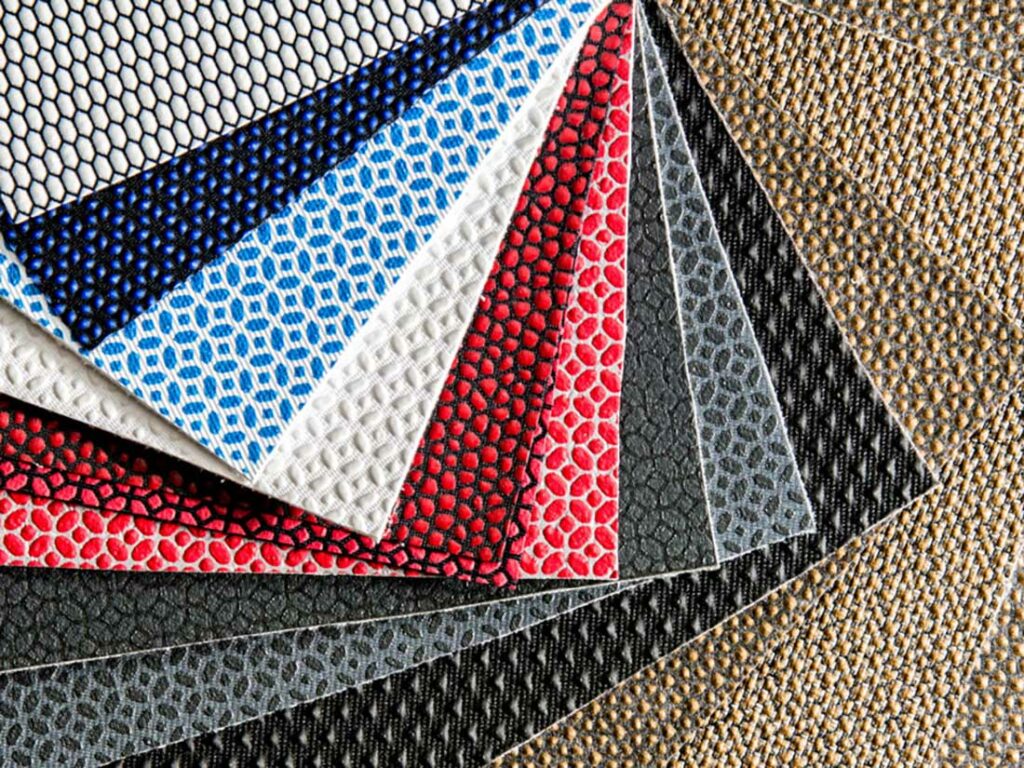
Mayer TechConcepts specializes in coating and printing including smart textiles for applications that includes the automotive sector. Exhibiting earlier this year at TechTextil Frankfurt, the company showcased examples of their innovations in the market. In one development, a car seat uses Alcantara (also referred to as synthetic leather) that has been printed with a lily pattern and red quilting edges. The headrest uses an artificial leather with a larger lily motif, with the colour enhanced by backlighting. Backlighting is also employed in the side bolsters that house the touch-activated switch functions for the backrest.
A further development shown was the inside panel for a car door. Here the textile has been printed with a 3D heating paste that uses carbon nanotubes coupled with printed touch sensors. The development uses CERAPUR, a patented 3D hard ceramic coating that provides surface protection for sensitive materials as well as providing a technical aesthetic. It has the capability to be electrically conductive providing heating or lighting.
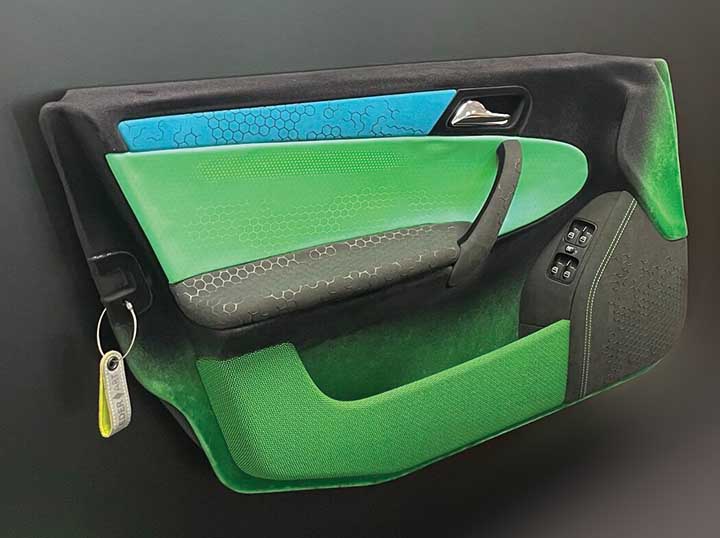
Lighting is achieved using a base layer printed with the desired visualization points, this is glued to a second layer that sits on top and contains the corresponding perforations. In a recent development directed at sustainability, a bio-polyurethane using rice and coconut oil is used.
FORVIA is a relatively young automotive technology company launched in 2022, bringing together Faurecia and HELLA. Future mobility lies at the core, with smart systems and sustainability providing the primary direction. FORVIA’s VIBE® technology offers occupants an immersive driving experience that promises enhanced safety, comfort as well as entertainment integrated into the smart seating. This looks to the EV market in particular as it senses and analyses occupants seated position to actively detect and offer guidance or take action against stress or poor back posture for example. The integration of intelligent actuators is an important aspect of the system and a primary focus of the company’s 40 filed patents. VIBE® is set to make its debut in a next-generation premium SUV end of 2025.
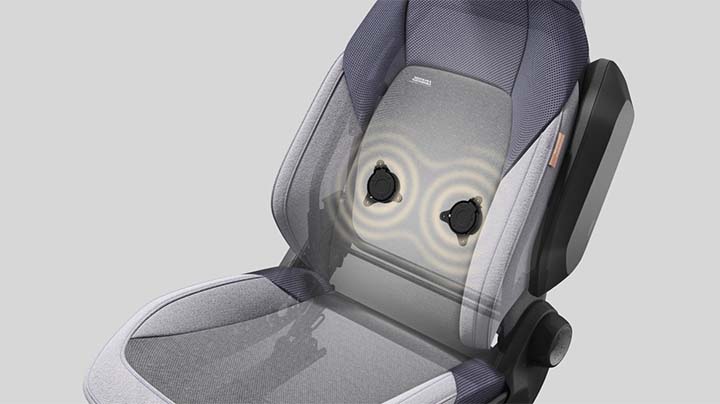
with a premium German OEM to introduce VIBE®, its cutting-edge immersive technology that redefines consumers’ time behind the wheel. Photo courtesy FORVIA
Vibe can be set up with an Advanced Driver Assistance System (ADAS) that includes haptic alerts for driver blind spots, lane changing, speed limit and drowsiness. Alongside the safety and wellness features is the entertainment in the form of 4D sound technology. This uses an algorithm that automatically generates a tactile vibration that synchronizes with the music being played to deliver an immersive haptic experience – hence the term 4D. There is also a wellness package aimed at reducing stress and drowsiness. This has been developed in partnership with Aurasen, curated with leading haptic artists to provide relaxation, recovery, and energy-enhancing programs.
Lighter Weight Vehicles
“We are on the brink of mass-producing composites that can be decomposed and recycled,” announced Ed van Hinte in his book written with Adriaan Beukers titled Designing Lightness – structures for saving energy (2020). The development of composites for the automotive sector in particular is focused on offering weight reduction that reduces energy and environmental impacts. The global automotive lightweight materials market size was given a value of $72.16 billion in 2022 and is expected to reach $137.8 billion by 2032, growing at a CAGR of 6.7% during that period with North America the fastest growing region according to a report by Spherical Insights.
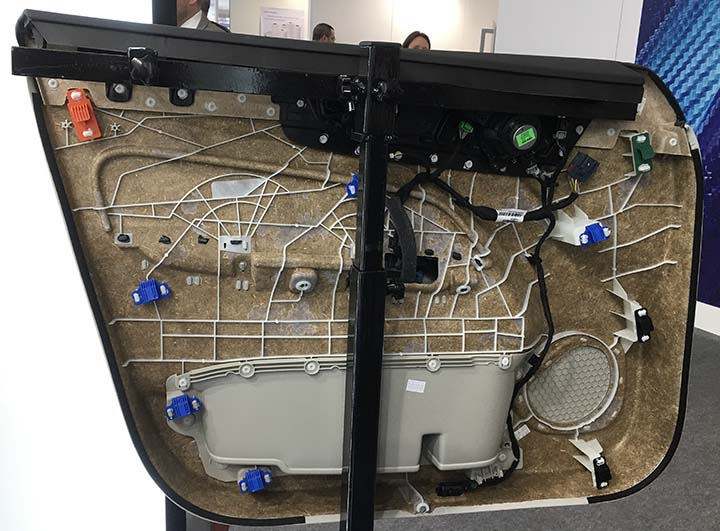
Replacing synthetic fibers with natural fibers in nonwovens for the automotive sector is extending from its use in mats, seating and acoustic lining to structural elements most notably composites. Natural fiber reinforced polymer composites (NFRPCs) can provide environmental benefit through the inherent lightness, renewability and biodegradability of the fibers. Hemp, kenaf, jute and flax are some of the primary fibers, with potential also seen in pineapple, sisal and agave leaf fibers.
Located in France, EcoTechnilin has been developing NFRPCs for automotive interiors of many of the leading car manufacturers primarily in Europe, but also is looking to the North American market. In Normandy region, 60% of the world’s flax is grown therefore this is a primary fiber used in their composites for interior trim parts, engine, passenger glove and trunk compartments as well as rocker panels. These conform to reinforcement needs while bringing a weight and carbon footprint reduction to the vehicle. The company’s next ambition is to see the NFRPC embraced as an aesthetic to be seen, encouraging even more widespread use and reducing the number of materials and processes needed in the automotive interior.
Topp Textil showcased a viable hemp solution that is still in development for automotive interiors at recent expos. Their laminated hemp fabrics produce sustainable and high-quality interior surfaces. The company sees clear potential for hemp in the composites sector and presented hemp developments for composite components, most recently at JEC World. Hemp can easily achieve the mechanical strength of glass fibres and would be an ideal basis for bio-based or recycling-optimized composites. “We are confident it’s the right way for innovations,” as an alternative to cotton, says Elvan Sentürk, Head of Application Projects, at Techtextil Frankfurt.
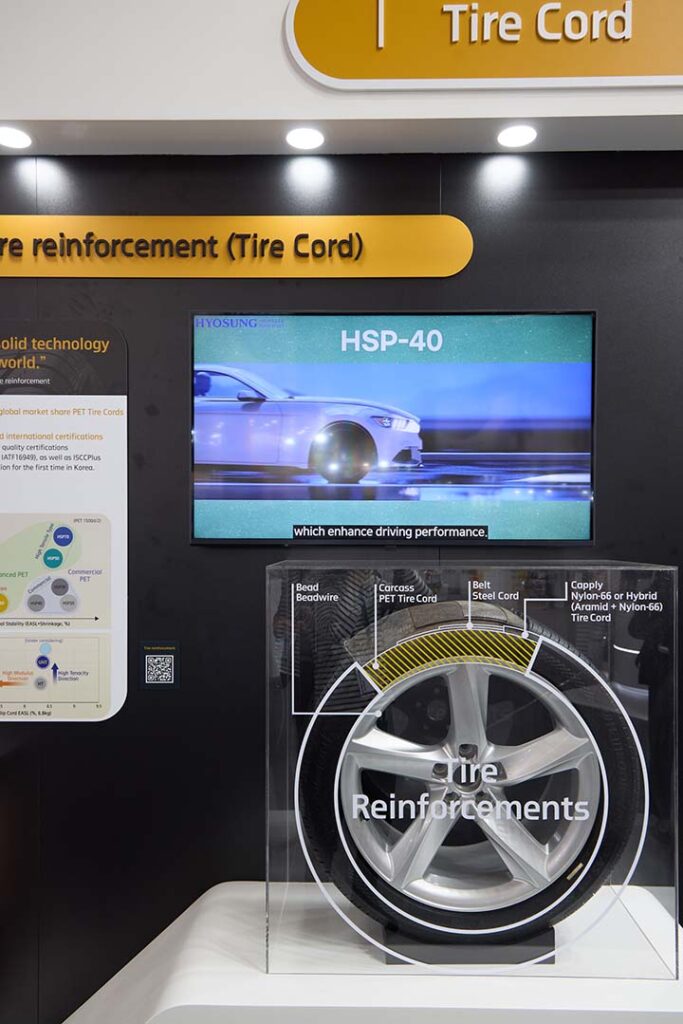
Hyosung Advanced Materials have developed a number of advances for tire reinforcement, a market area that they have been supplying since 1968 with the claim that 50% of all passenger cars now use their PET tirecords. They offer a number of fiber options such as aramid, nylon, steel cord, bead wire, PET and Lyocell. Typically, the outer tread making contact with the road is made from rubber. This is followed by the ‘carcass,’ an inner layer that is load and shock absorbing usually using a polyester. The belt is located between the tread and the carcass, and its function is to resist puncture and improve safety using nylon tirecords and steel cords. A cap ply helps the tire to maintain its shape while the bead wire comes in contact with the rim, providing reinforcement and preventing air leakage from within the tyre.
Ford has launched a wide range of biomaterial products that include wheat straw for storage bins and cup holders, kenaf plant door bolsters, rice hulls for electrical harnesses, tomato skins for wiring brackets and storage bins.
A key driver of R&D is lowering the environmental impact of the tire and contributing to a more sustainable automotive sector. The company produce an ultra-tensile (UT) steel cord for use in lightweight tires for the EV market, for example. New developments include a bio-PET yarn that is manufactured from ethylene glycol extracted from sugar cane or corn, contributing a 16% reduction in greenhouse gas emissions compared with existing polyester tirecords by company estimates. Lyocell tirecords have also been developed as a replacement for nylon in applications where high speed and durability are key factors. The raw material is extracted from wood and does not emit carbon bisulfide or sulfureted hydrogen during production. This reduces water contamination during the processing. This development using Lyocell has the potential for a 30% reduction in greenhouse gas emissions.
Reducing Environmental Impacts
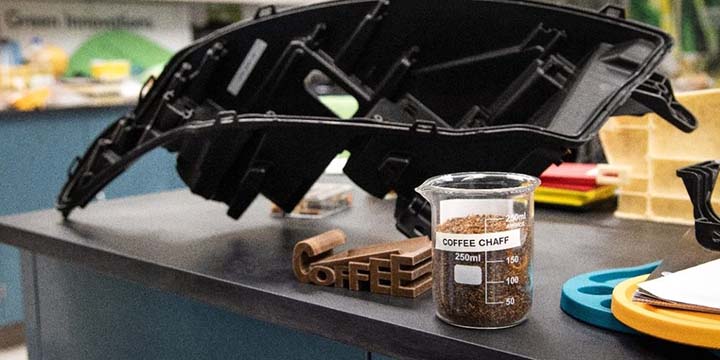
The automotive sector has long been interested in the potential for biomaterials in reducing environmental impact and vehicle weight with some of the biggest names in the sector already involved. Recently retired from the Ford Motor Company where she served as Technical Fellow of Sustainability, Dr. Deborah Mielewski initiated the biomaterials program at Ford research in 2001. While there, she showed that soy-based foam could meet all of the requirements for automotive seating, resulting in the launch of the foam in the 2008 Mustang.
Since then, Ford has launched a wide range of biomaterial products that include wheat straw for storage bins and cup holders, kenaf plant door bolsters, rice hulls for electrical harnesses, tomato skins for wiring brackets and storage bins. In a collaboration with McDonald’s, the dried skin of the coffee bean, the coffee chaff, is used in a composite for car headlight housing. The coffee chaff comes away naturally during the roasting, this is taken and heated to a higher temperature under low oxygen missing it with polymers and other additives to make pellets that are then used in the composite. The resulting components Ford estimates to be 20% lighter and needing around 25% less energy during the moulding process.
The development of biomaterials received an impetus in Europe in 2022 when the EU adopted the Sustainable Products Initiative (SPI) – otherwise known as the ‘Green Deal.’ The conservation of resources and product lifecycle have risen as important considerations in new material development. In the development of synthetic leathers, a textile substrate is commonly used as a base material with a polymer layer then applied. The polymer layer usually consists of an adhesive layer and a top layer that is usually embossed. Woven, knitted, or nonwoven fabrics made of PET, PET/cotton, or polyamide are often used as the textile substrate, while PVC and various polyurethanes are generally used for coatings.
This is not ideal as they are not biodegradable and recycling by type can be very costly, or even impossible. The German Institutes of Textile and Fiber Research Denkendorf, together with the Freiberg Institute GmbH (FILK) in a German Federation of Industrial Research Associations (AiF) project to develop a synthetic leather in which both the fiber material and the coating polymer are identical. The base layer consists of an aliphatic polyester polybutylene succinate (PBS) that can be produced from biogenic sources and is now available to scale in several grades. Both the fiber material and the coating can be processed thermoplastically, and subsequent product recycling is facilitated by the thermoplastic properties.
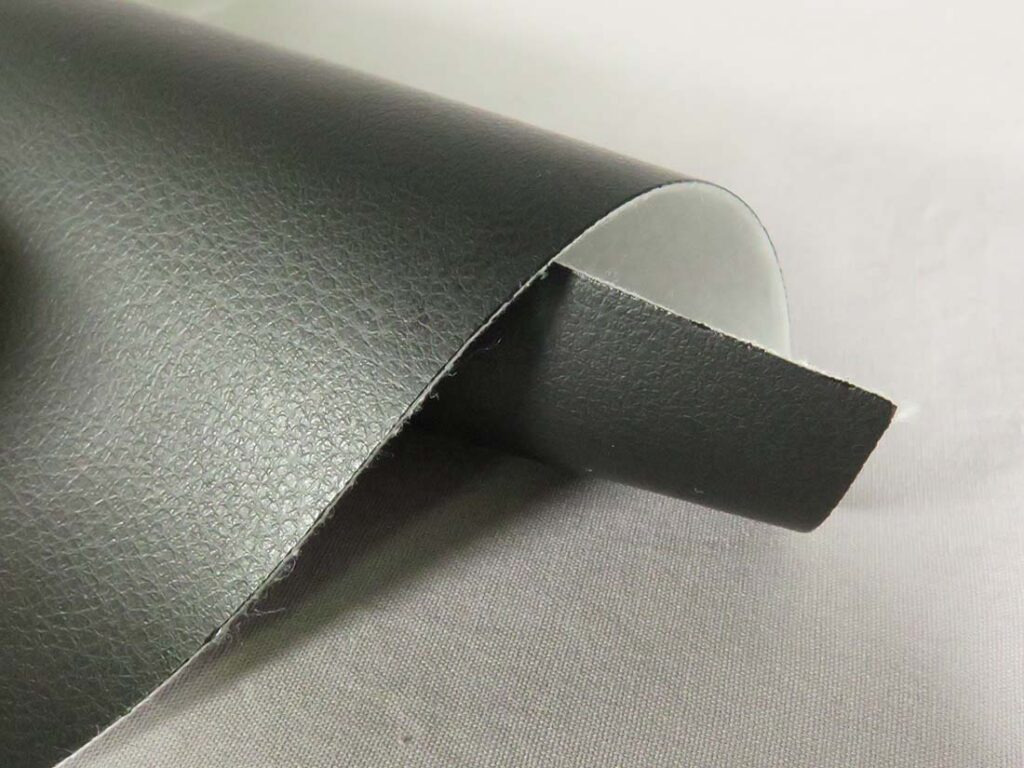
In order to realize a successful primary spinning process and to obtain PBS filaments with good textile mechanical properties, process adjustments had to be made in the cooling shaft at the DITF. In the end, it was possible to spin POY yarns at relatively high speeds of up to 3,000 m/min, which had a tenacity of just under 30 cN/tex when stretched. The yarns could be easily processed into pure PBS fabrics. These in turn were used at FILK as a textile base substrate for the subsequent extrusion coating, where PBS was also used as a thermoplastic. With optimized production steps, PBS composite materials with the typical structure of artificial leather can be produced. Purity and biodegradability have yielded positive results, fulfilling the requirements for a closed loop recycling process.
Mycellium continues to attract interest and development with Antolin developing mycelium-based materials derived from fungi for use in automotive components. The mycelium binds with vegetable residues in order to produce a material that is structural. The company are enthusiastic that this form of production is carbon neutral because the material development occurs organically directly in the mould, as opposed to the conventional injection moulding process needed for plastics. Antolin see this as contributing to decarbonization and leveraging natural resources, giving a second life to waste of natural origin that can be used in an industrial setting and to scale.
Smartness, lightness and sustainability have been discussed here as three different trends on the rise. There are already developments bringing these three together for a positive for consumer and environment, as well as the design potential for exciting new innovations. More are on the horizon, as they make their way out of research and development and into new vehicles of productions lines in various countries.