Some 1,335,000 tons of nonwoven fabric will be consumed by the wipes manufacturers in 2016.
North America’s nonwovens industry body INDA is heavily involved in ensuring the healthy growth of flushable wipes, despite a number of problems
The market for disposable wipes based on nonwoven fabrics is currently very healthy and not least, that for flushable products that has gained momentum over the past decade.
It has been estimated that about 1,335,000 tons of nonwoven fabric will be consumed by the wipes manufacturers in 2016. Of this figure, 580,000 tons will be produced in Asia, 414,000 tons in NAFTA and 341,000 tons in Europe. CAGR is an overall 8%, but 14% in Asia.
Meanwhile, the retail value of the sales of flushable wipes in 2015 was $1.4 billion – up from $796 million in 2010. And all the indications are that sales will almost double again by 2020, when the market will be worth $2.7 billion.
Attention
Flushable wipes, however, represent just 7% of the overall nonwoven wipes market, yet in recent years have achieved 99% of the attention – a lot of it negative and reflecting badly on the industry as a whole.
Horror stories of non-flushable wipes and other materials combining with grease to create so-called “fatbergs” in sewer systems have made the headlines in many countries and in the U.S. there have been 15 class action lawsuits brought against the big-name brand owners, converters and retailers, all citing alleged damage caused by flushable wipes clogging pipes.
Wrong target
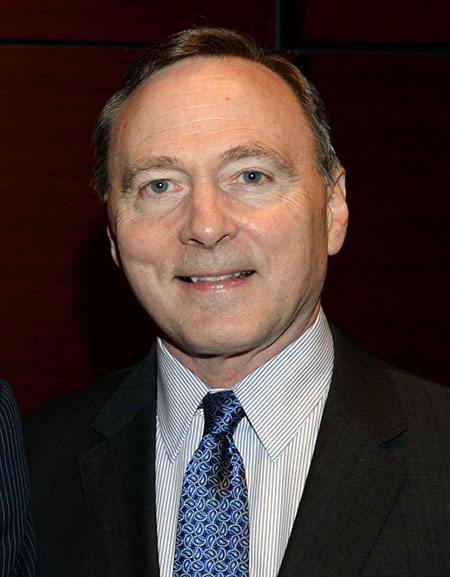
“There is no such damage,” said Dave Rousse, president of nonwovens industry body INDA. “War has been declared on wipes marketed as flushable, but they are shooting at the wrong target and damning the good guys will make the problem worse. The problem is not flushable wipes, but wipes, cloth and paper towels, and feminine care products and other items getting flushed that should not be. We’ve had one case dismissed and one settled for essentially a two hundred dollar repair bill. The plaintiff attorneys will soon see that chasing the flushable wipes ambulance won’t result in a payday. However, proving damage from non-flushable wipes, and having those wipes not labeled with the “Do Not Flush” symbol in accordance with the industry’s Code of Practice, may soon appear to be the more fruitful ambulance to chase. I would encourage all converters, brand owners and product managers to avoid unnecessary business risk and quickly get their non-flushable wipes in compliance with the industry’s Code of Practice for proper labeling of wipes.”
Pathways
The Code of Practice he refers to has been developed by members of INDA and EDANA (the European industry body) and relates to communicating appropriate disposal pathways for nonwoven disposable wipes, in order to protect wastewater systems. It contains a well-designed decision tree to direct a wipes brand owner to the proper labeling protocol.
If the wipe is intended to clean human waste in a bathroom setting and be marketed as “Flushable,” it must pass all seven tests of the INDA/EDANA Flushability Assessment Guidelines.
“I think we as an industry are largely there on this one,” Rousse said.
“I am aware of no wipe in the U.S. that is marketed as flushable and does not pass the assessment tests, but we are not there on the next important element of the decision tree and we need to be if we are to line up with our commitment to be responsible marketers of our products. If a wipe is not designed to be disposed of via the toilet, but it could be flushed because of its use in a bathroom or because it comes in contact with human waste, then it must prominently display the “Do Not Flush” symbol on primary and secondary packaging.”
Engagement
INDA currently has a number of initiatives in play in its constructive engagement with the Wastewater sector in North America. These were detailed by Rousse at the dedicated World of Wipes (WOW) conference and exhibition held in Chicago in June.
The issue is complex and not likely to be easily or quickly resolved, but the demand for flushable products certainly won’t go away, and has meanwhile resulted in the development of specific new technologies for the production of truly dispersible nonwoven fabrics.
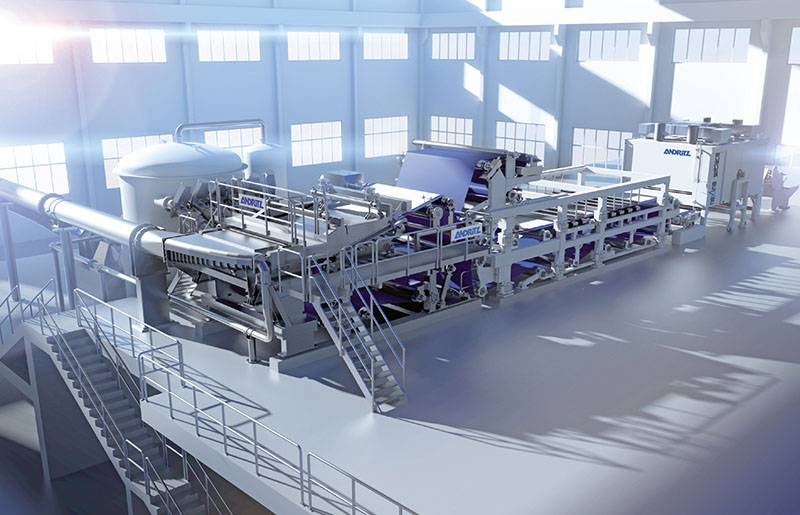
Wetlace
Andritz Nonwoven, for example, has been supplying its Wetlace line as a complete solution for flushable wipes from a single supplier since the mid-1990s.
Over the past decade Andritz has integrated the technologies of Küsters, Perfojet and Asselin-Thibeau and now has more than 220 complete nonwovens in operation globally, with more than 130 designed specifically for the production of wipes.
With operating speeds of up to 300 m/min, the Wetlace system accommodates fabrics in the weight range of 40-80gsm.
One such line has recently been supplied to the leading Turkish nonwovens producer Akinal Sentetik Tekstil.
The highly flexible technology combines wet forming and hydroentanglement and is especially suitable for the production of flushable wipes that are dispersible and 100% biodegradable without any chemical binder. Start-up of the line is scheduled for 2016.
The Andritz neXline Wetlace is designed for high production capacities of up to 15,000 tons per year and integrates stock preparation, wet forming, and hydroentanglement.
The Wetlace technology fulfils the highest environmental standards for the end products and produces certificated nonwovens quality according to the latest INDA/EDANA guidelines for flushable wipes.
Suominen
Andritz is also the main supplier and integrator of the new wetlaid production line that is currently being completed by nonwovens manufacturer Suominen, in Bethune, South Carolina – a project with a price-tag of some €50 million ($56 million).
In addition to flushable wipes, the new line will supply nonwovens for several applications, including household and workplace wipes, medical and personal care products.
“It is not by chance that Suominen is investing in these carefully selected market segments,” said Saara Söderberg, the company’s vice-president of marketing and product management. “They are growing markets and we know what the needs are in these applications. This new production line will take wetlaid technology to a totally new level in the industry and will provide customers with unique advantages through adding exquisite capabilities for designing nonwovens substrates.”
The first products from the new line are expected to be shipped in the first quarter of 2017.