Oerlikon’s Industrie 4.0 solution for quality control and processes.
The Oerlikon Manmade Fibers segment technology offers cost-efficient and high-quality manmade fiber production. With innovative Industrie 4.0 solutions, the company is setting new standards with regards to customer benefits.
With the Plant Operation Center (POC), for example, manufacturers can maintain a holistic overview of manmade fiber system production – from the polycondensation and the spinning system through to texturing and the downstream further processes. With this, processes can be optimized, production optimally planned and the product quality improved. To this end, the concept is already supporting the rising need for greater flexibility and higher quality in production processes.
Global competition within the manmade fiber industry and the changing expectations of consumers with regards to fashion detailing are today increasingly presenting yarn manufacturers with challenges. Special production runs, such as spun-dyed products and special yarn cross-sections, must be flexibly, quickly and efficiently manufactured in small batches; here, the production of standard products must not suffer. Optimum planning of product switch-overs must ensure there is no risk of waste, quality errors or over- and under-production.
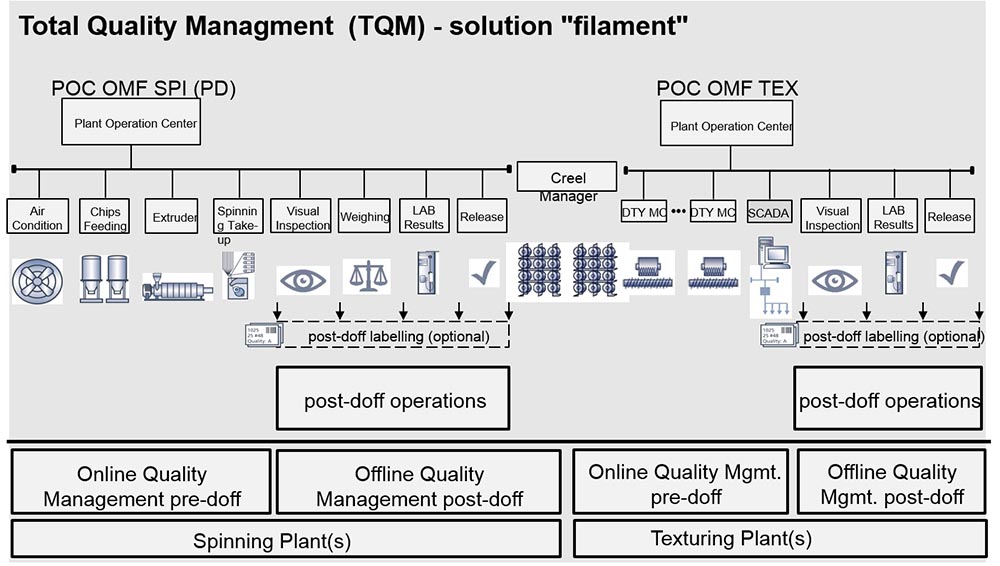
Modular system maintains workflow overview
The modular structure of the POC system guarantees customer success. With its more than 20 modules – for example, for quality control, maintenance and production planning and recipe management – the workflow management system can be optimally tailored to customer requirements. Oerlikon Manmade Fibers has successfully implemented more than 250 POC-equipped installations.
The primary focus is on the traceability of all process data from the polycondensation system to the yarn in real time and the potential direct reaction to deviations in machine efficiency or product quality. Here, not only can data from the in-house laboratory be directly integrated, but also – with the corresponding link – the data from the downstream processes such as texturing, for example. Equally, the POC is able to monitor auxiliary systems such as air-conditioning and compressed air provision.
In detail: POC modules
The modular structure permits yarn manufacturers to adapt their “own” Plant Operation Center precisely to their requirements. As a total concept, the POC assumes a major share of the functions provided by a manufacturing execution system, including the link to superordinate systems and to corresponding interfaces for automation systems, such as package handling and storage in the spinning system. To this end, the control of automation systems within the spinning process is part of the concept. Each individual module provides concrete potential production cost savings.
1. Production planning
Production orders are optimally prepared and integrated into the production process, therefore ensuring transparent production. With this, over- and under-production are avoided – even in the case of small batches.
2. Recipe management
Machine settings optimized to the respective product are stored in the recipe management system and transferred to the production system error-free when switching products. As a result, the product quality is guaranteed even in the event of frequent product switch-overs.
3. Quality control
The integration of data measured in the laboratory helps ensure high product quality. In addition to 100% traceability for each individual product unit (package) throughout the entire manufacturing process, a so-called cyber-physical system also provides fast identification of, and reaction to, potential quality deviations. When integrating further processing procedures such as texturing, functions like the creel management system can be used to efficiently optimize product quality.
4. Efficiency monitoring
The statistics module continually monitors the production efficiency of individual products or entire machines and plants. In this way, production process malfunctions that can result in lower yields or high waste rates, for example, are identified early on and can be alleviated quickly.
5. Alarms and maintenance planning
As a result of managing the alarms and the maintenance planning tailored to the production process, the POC system supports the customer in minimizing downtimes and unplanned interruptions and hence also production waste. At the same time, personnel deployment and system utilization are optimized. Malfunctions in the plant are transparently displayed using monitors or mobile devices, which ensures a stable production process leading to a high yarn quality. The result is swift alleviation and optimum planning of necessary maintenance during the production process according to specialist staff availability. In parallel, shift planning is supported in keeping with actual staff requirements.
6. Performance monitoring
For fast real-time monitoring of production plant efficiency, the data can be displayed according to key performance indicators on the customer network and also on mobile devices. As a result, the management is able to check on the system at any time – even outside the plant. However, if unplanned machine downtimes or process problems nevertheless occur, Oerlikon Manmade Fibers customer service experts can use the remote support function to log into the system directly and provide the system operator with swift support.
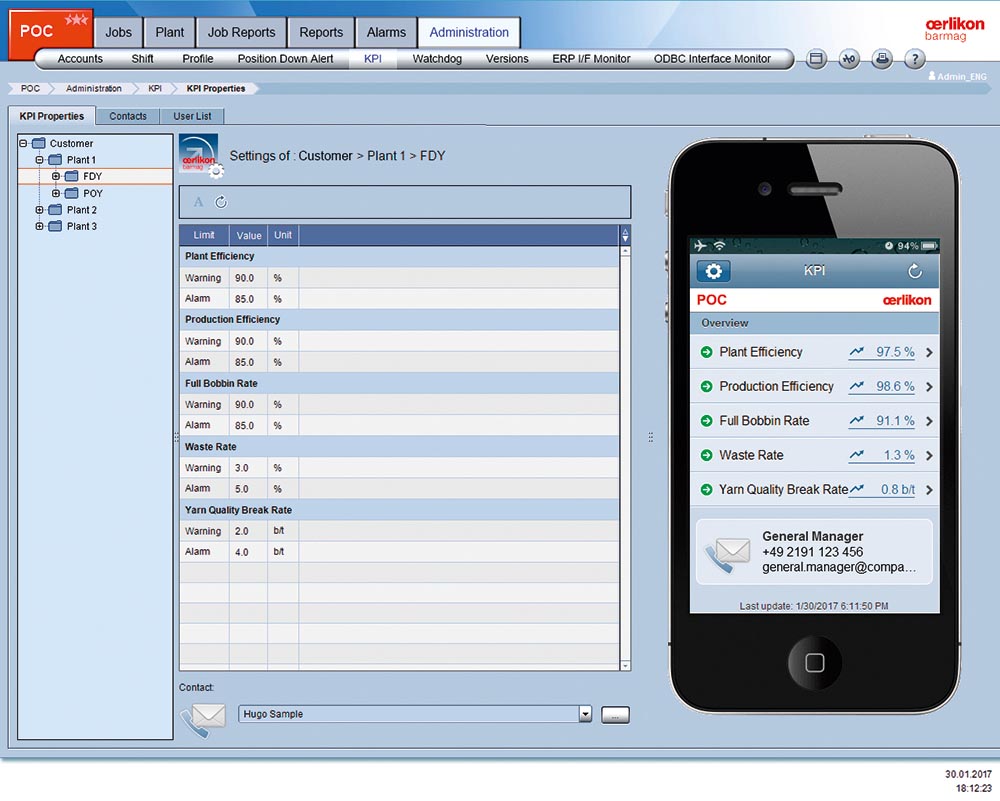
Upgrading existing systems using a POC
A POC system is not only a process monitoring option for new systems: connecting existing manmade fiber systems to a POC system is usually unproblematic. For this reason, increases in quality and efficiency, and hence also in competitiveness, can be achieved even in the case of older systems.
Entering the future of Industrie 4.0
Oerlikon Manmade Fibers provided an insight into potential future Industrie 4.0 solutions at last year’s trade fairs, including ITMA Asia in Shanghai and India ITME in Mumbai. Linked to future-oriented service and automation solutions, Oerlikon prepares its customers for the future of manmade fiber production. And it goes without saying that the end results are improved yarn quality and production efficiency.