Advanced fibers are now critical to the marketing campaigns of fabric mills supplying the $60 billion denim apparel market. Differentiation is the key in this highly competitive field and companies are quick to jump on any new development that can provide it.Over the past decade, huge vertically-integrated capacities for the production of denim have been built up by companies in the three major manufacturing countries of the Indian subcontinent – Bangladesh, India and Pakistan – with Turkish manufacturers also hugely influential, especially in supplying to neighboring Europe.
Their latest developments were showcased at Denim Première Vison, held in London, UK, in December, where the sheer scale of some of these enterprises became apparent.
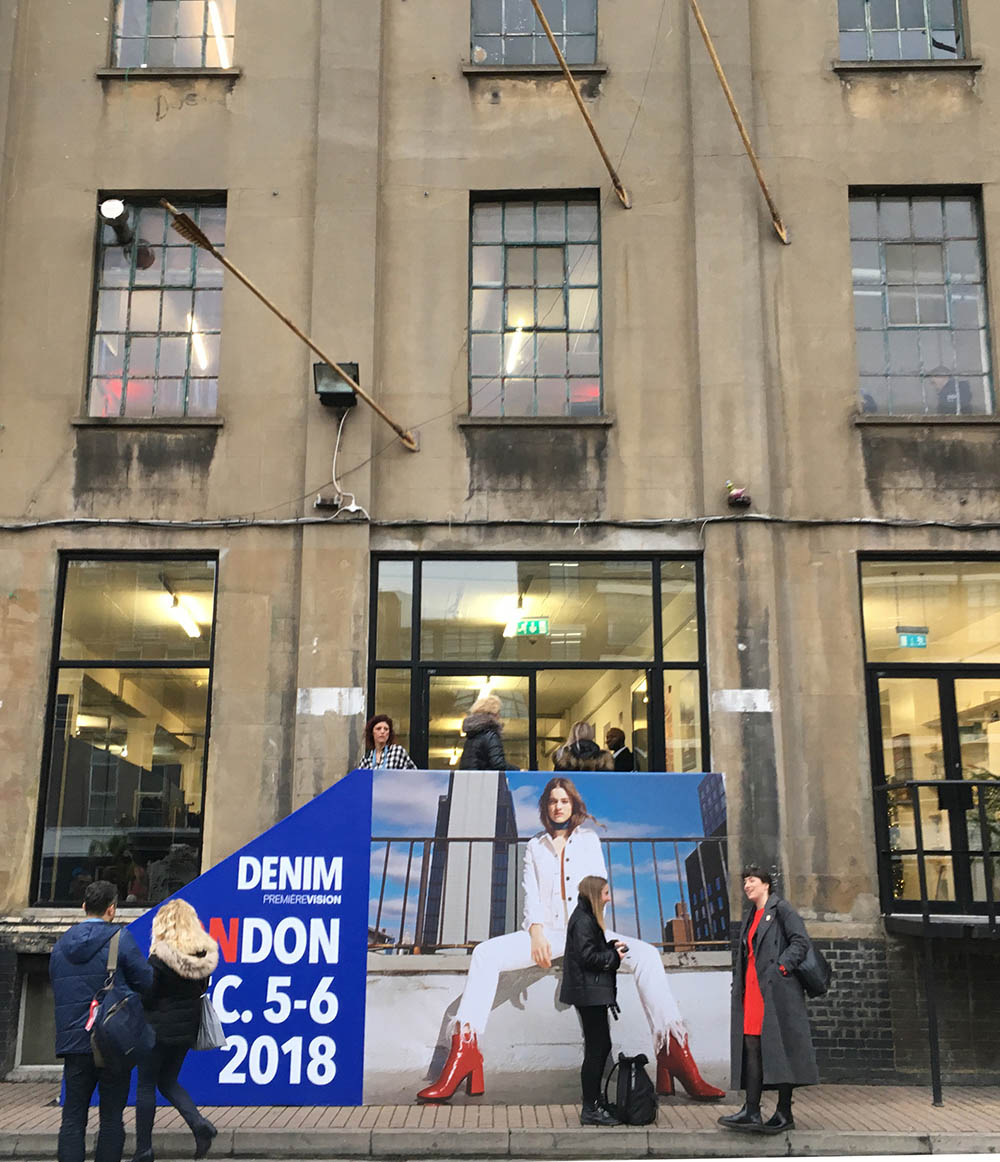
Karachi’s ascendance
In particular the region around Pakistan’s capital Karachi is now dense with denim manufacturers. They include Artistic Milliners, which has the ability to produce some 66 million meters of fabrics and more than 21 million finished garments a year.
Denim Clothing Company, which commenced operations in 2005, has quickly risen to become a supplier to leading brands with a capacity of 18 million garments annually, while Soorty’s finished denim fabric capacity alone is 66 million square meters.
Then there is Artistic Fabric & Garment Industries (AFGI), which in recent years has expanded its capacity to 50 million meters of fabric and 25 million garments per year; Kassim, which makes 30 million meters of denim per year; and Denim International, which is currently expanding capacity to around 10 million denim garments annually.
All of these companies are huge employers; Soorty, for example, employs some 22,000 people across its textile and garment operations.
White Oak closure
The still-mighty US denim brands long ago ceded their fabric production to overseas producers and, sadly, even the White Oak manufacturing plant of Cone Mills in Greensboro, North Carolina, was forced to quietly close in December 2017, when the company opted to locate its manufacturing in Mexico.
Cone’s White Oak plant was famously granted the US rights to manufacture all the shrink-to-fit selvedge denim for authentic Levi 501s more than a century ago, and had lovingly restored and maintained its 1940s shuttle looms, installed on a special wooden floor to absorb their vibrations.
When it came to vintage denim, it didn’t get more authentic, but the company’s parent, International Textile Group, said changes in market demand had significantly reduced order volume, with consumers no longer willing to pay premium prices for domestically-produced fabric and companies simply not buying enough to keep those historic looms running.
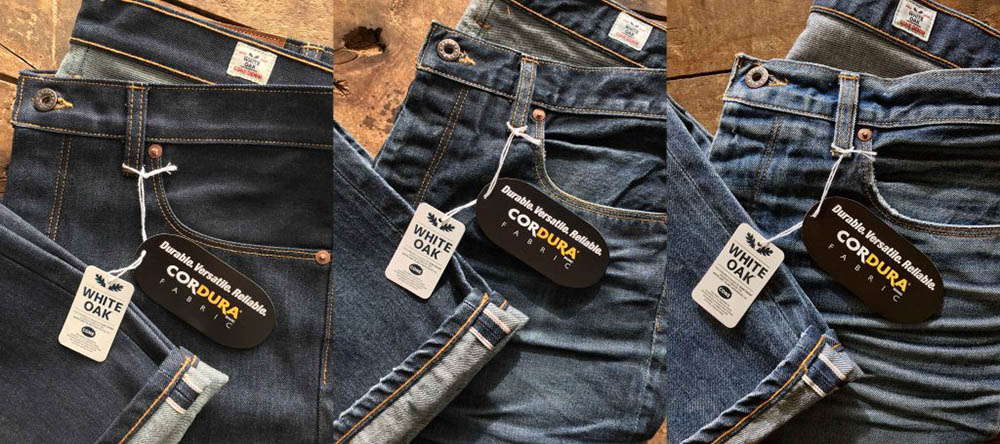
Market size
An annual 1.28 billion denim garments, primarily pairs of jeans, are estimated to have been sold globally in 2018, with a retail value of around $60 billion. North America remains the biggest market for denim, buying 39% of the total, followed by Western Europe with 20%, Japan and South Korea 10%, and the rest of the world purchasing the remaining 31%.
For many years China completely dominated the supply of denim to major export markets, with around 3,000 companies based around the Guangzhou town of Xintang alone supplying some 800,000 pairs of jeans every day.
Vibrant hub
Xintang became the most vibrant denim market in the world with initial investment from Hong Kong and an accommodating local government policy framework. The region became a magnet for cheap migrant labor from China’s inland provinces, and buyers from the international brands flocked to the region.
But then things changed. On the back of its international success, China’s labor costs climbed five-fold and the government started to withdraw its backing for companies solely concerned with commodity manufacturing for lower margin exports. On top of this was a severe pollution problem that attracted unfavorable headlines around the world.
As a result, buyers from the international brands started to look elsewhere, resulting in China’s denim exports contracting significantly.
Manufacturers in Bangladesh, India and Pakistan – as well as Brazil, Mexico, Turkey and Vietnam – have all benefited from this situation and US President Donald Trump’s tariff system maneuvers have not yet impacted the denim industry.
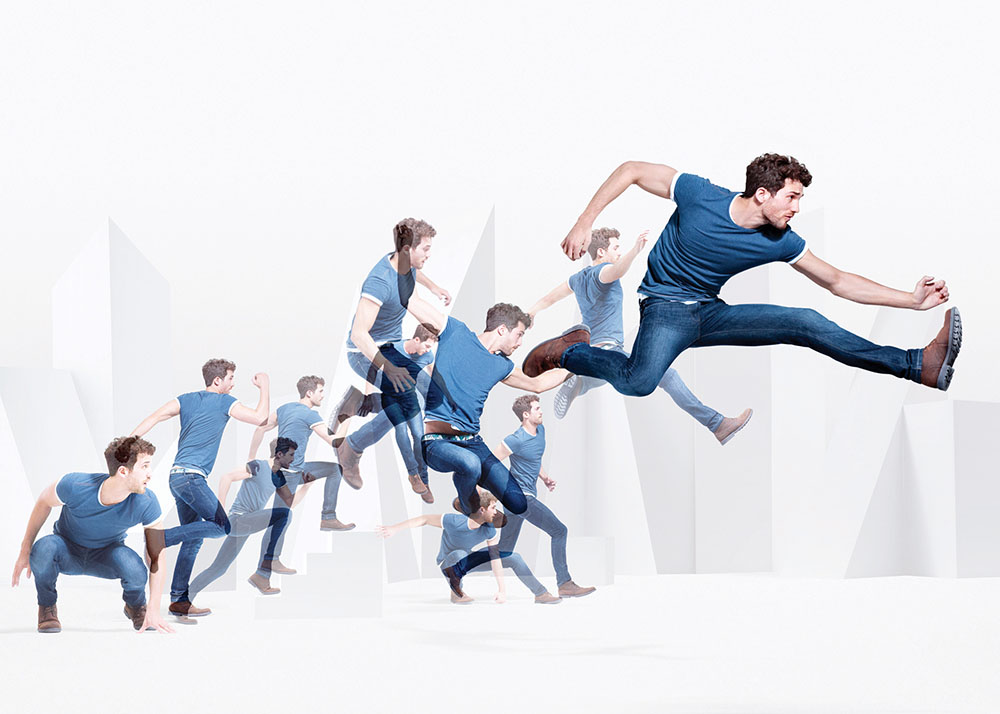
Twin demands
In an increasingly competitive market denim mills are now facing demands for both accelerated performance and guarantees of sustainable manufacturing from the brands they supply – two requirements that frequently make uneasy bedfellows.
Stretch, for example, is now expected as a given in denim jeans, through elastane fibers – as spearheaded in the industry by Invista’s Lycra, among others – to ensure comfort, fit and freedom of movement, without loss of shape.
Lycra dualFX technology, which provides soft and even stretch while maintaining shape recovery, is now licensed to 61 denim mills and is based on a triple-core technology in yarns, with two strands of Lycra fiber and a third of Lycra T400, a multi-polymer filament, wrapped with cotton.
Abrasion resistance is another key requirement, provided by performance fibers such as Cordura nylon, as highlighted in denim ranges by both Artistic Milliners and Cone Mills at the London show.
And since price is always paramount in this market, fiber blends of cotton and polyester are used wherever possible.
Closed loop
Yet when it comes to recycling, blended fabrics – as well as accessories, such as zips, buttons and stitching threads – can prove highly problematic, which is why most recycling programs for cotton generally concentrate on pre-consumer waste and those for polyester prefer to recycle polyethylene terephthalate (PET) bottles rather than post-consumer clothing.
Most denim mills are keen to highlight the use of recycled PET in their ranges, yet these are inevitably in blended fabrics, putting limitations on further recycling in the move towards achieving truly closed-loop manufacturing systems.
This is one of the issues leading to calls for a greater concentration on garments being designed for recycling from the very start, but it is yet to take hold.
PCR cotton
As members of the Alliance for Responsible Denim (ARD), Turkey’s Kilimdenim and Pakistan’s AFGI are now also including a percentage of post-consumer recycled (PCR) cotton in their collections.
Spanish company Hilaturas Ferre is producing special recycled cotton yarns for denim by collecting and sorting textile waste from around the world and upcycling it via cutting/shredding and spinning into new Recover yarns.
The company ensures the quality and color of its Recover yarns is consistent, replicable and free of harmful substances through optimized waste management systems, strict testing and certification policies, and its proprietary ColorBlend process.
“There is around 92 million tons of textile waste generated each year and a real need to try and introduce more recycled fibers,” said Hélène Smits of ARD.
“Recover recycled cotton is the lowest impact cotton option available today and there are immense impact savings to be achieved with it, not only because we limit the use of virgin cotton and the associated impacts, but also because we do not add water or chemicals to the cotton to get the color.
“Together this means you can save up to 15,000 liters of water when you use 1 kg of Recover recycled fiber instead of 1 kg of conventional dyed cotton.”
Refibra
Also proving popular with many denim mills is the new Refibra fiber from Austria’s Lenzing.
Lenzing’s Tencel cellulosic fiber already provides denim fabrics with enhanced richness, softness and drape and is also receptive to special denim finishing techniques that add to their sumptuous look and feel.
Tencel has excellent sustainable credentials too, being based on renewable cellulose and manufactured in a closed-loop process, with the wood and pulp harvested from certified and controlled sources.
Going a stage further, Refibra is based on post-industrial cotton waste, which is turned into pulp and combined with virgin wood pulp, again using closed-loop manufacturing, to make new fiber.
“Currently, it is only possible to recycle 100% cotton textiles based on the waste from garment makers’ cutting rooms for Refibra, but eventually the goal is to move to post-consumer waste, where naturally there are many more challenges in ensuring uniform quality,” said Tricia Carey, Lenzing’s director of global business development for denim.

Cradle to cradle
C&A meanwhile looked to Asahi Kasei to provide the stretch in its latest Cradle to Cradle (C2C) Gold-certified Wear the Change women’s denim jeans, which are now available in Europe, where they retail at just €29 a pair.
The C2C Certified Product Standard guides designers and manufacturers through a continual improvement process, aiming to achieve a circular economy approach.
It examines a product through five quality categories – material health, material reutilization, renewable energy and carbon management, water stewardship and social fairness.
A product receives an achievement level in each category – Basic, Bronze, Silver, Gold or Platinum. The criteria at each level aims to eliminate all toxic and unidentified chemicals.
For the Wear the Change jeans, more than 100 separate components across the entire supply chain had to be assessed during the extremely stringent C2C certification process, with the lowest achievement level for a single component representing a finished product’s overall rating.
Only Asahi Kasei’s Roica V550 elastane was suitable for providing the 1–2% stretch required, being the only elastane that is registered C2C Gold to date.