Cotton was undoubtedly the fiber of the 19th and early 20th centuries and is still by far the world’s most widely used natural fiber.
But while cotton is a biodegradable and renewable resource, the use of conventional cotton to produce clothing could decrease going forward as retailers and consumers seek more sustainable alternatives in the natural fiber category.
However, for large-scale use, textiles of the future must be both sustainable and economical to produce. There are many possible alternatives, but few are close to becoming a truly viable substitute to cotton, at least not for the foreseeable future.
King cotton
Cotton (Gossypium) has been grown for fiber and food for more than 6,000 years. Cotton is one of the most breathable and absorbent fibers around, having the ability to absorb both heat and perspiration; cotton fabrics are also easy to print and dye.
Cotton is versatile, as cotton fibers can be used for making clothing, bedding and towels, as well as paper, cooking oil, ropes, banknotes and biofuel. Moreover, products made from cotton are relatively inexpensive by today’s market standards.
There are approximately 35 million hectares of cotton currently under cultivation, with global production of cotton fiber of some 25 million tonnes, which is projected to grow by 1.5% per annum to reach almost 30 million tonnes in 2029, according to the Organisation for Economic Co-operation and Development (OECD). The largest producers are currently India, China and the U.S.
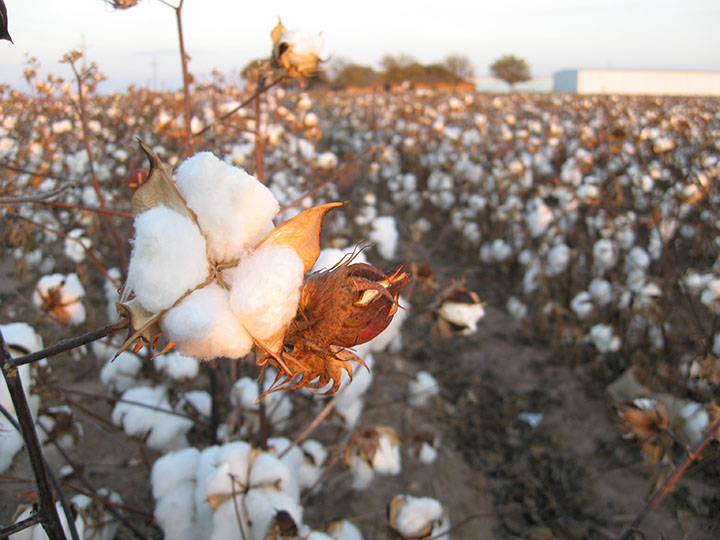
But growing conventional cotton for the textile industry has been criticized by some as harmful to the environment. Opponents say it requires a significant use of pesticides and fertilizers, with cotton consuming 16% of all the insecticides and 7% of all herbicides used worldwide.1,2
In addition, critics say cotton accounts for 2.5% of the world’s cultivated land and requires vast amounts of water – up to 10,000 liters per kilogram of cotton harvested.1,2 And studies have indicated that it takes approximately 2,700 liters of water to produce a single T-shirt.3, compared to a single person who needs on average 50–100 liters of water per day to meet basic needs.
Cotton Inc, the research and marketing organization funded by U.S. cotton growers and importers, disputes some of these figures. For example, it claims that no organization monitors the usage of pesticides, but rather data reports sales of pesticides, and that global cotton production accounted for 5% of pesticide sales in 2016. It also notes that cotton is essentially a heat- and drought-tolerant crop, with around half of the global crop relying on rainfall for watering. (NOTE: A full account of Cotton Inc.’s response to some of the critical claims against cotton production can be found at https://bit.ly/cottoninc-cottonfacts.)
While organic cotton represents a step forward in sustainability, as it avoids the use of synthetic and toxic pesticides, it still requires water and land on which to grow – although the Soil Association found that organic cotton can be grown using 91% less water than its non-organic counterpart. However, organic cotton currently makes up less than 1% of the world’s global cotton production, according to the Organic Trade Association.
But is there really a viable alternative to cotton in the natural fiber space? In recent years, several producers have started looking at other plants for sustainable fabrics – some are already widely used by the textile industry, while others will require further development to even be considered.
Bast fibers, which are obtained from the outer cell layers of the stems of various plants such as flax, jute, hemp, ramie and kenaf, are among the leading contenders to make inroads on cotton’s share of the global natural fiber industry.
Hemp resurgence
Hemp (Cannabis sativa) is undergoing something of a resurgence, as it requires much less land and far less water to grow than cotton. Hemp does not require any pesticides or fertilizers, and the plant only takes about 11 weeks to mature.
Further, hemp fabrics are more resilient – cotton tends to become weaker when wet while hemp retains its strength and durability. Meanwhile, recent advances in the “cottonization” of hemp fiber could open the door to its use in high-quality clothing applications.
However, the mass adoption of hemp has been hampered by its visual and taxonomical identification with marijuana, both of which are classified as Cannabis sativa L.
But as a result of the 2018 Farm Bill in the U.S., hemp has now been removed from Schedule I of the Controlled Substances Act and is no longer considered a controlled substance, thereby legalizing industrial production of the plant and allowing for its cultivation and distribution as an agricultural product in the U.S.
Regarding potential drawbacks, hemp can be difficult to spin on its own, as the fiber itself can be irregular. As well as generally being more expensive than cotton, linen and other commonly used materials, hemp clothing may not be the most comfortable fiber to wear, and it tends to crease easily, while giving something of a “rustic” visual appearance.
Lustrous ramie
Fiber from the ramie plant (Boehmeria nivea), a linen-like flowering plant of the nettle family, has the luster of silk and is more absorbent than cotton. Ramie does not require pesticides or herbicides to grow and can be harvested up to six times in a good year.
However, ramie is difficult to process into fabric – unlike other bast fibers it requires chemical processing to de-gum the fiber. It does, however, produce a strong, breathable and comfortable material, although perhaps not as durable as other plant-based natural fibers.
While similar to flax in absorbency and density, ramie does not dye as well as cotton and, because of its high molecular crystallinity, is stiff and brittle and will break if folded repeatedly in the same place. Further, ramie lacks resiliency and is low in elasticity.
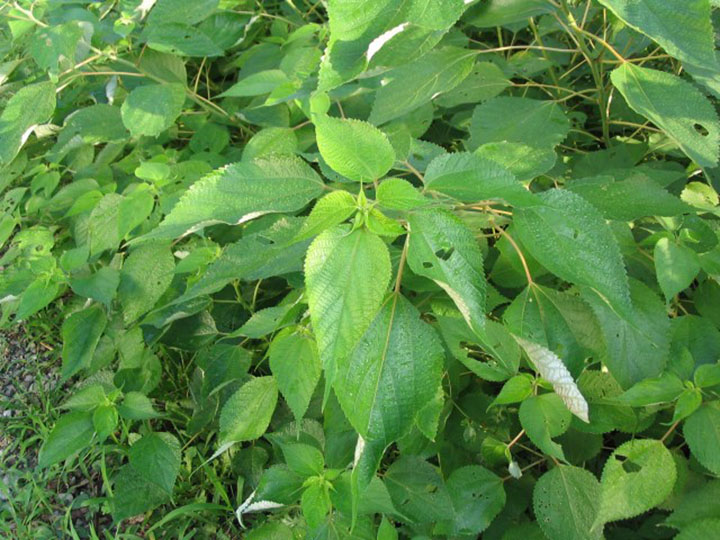
Cultivated flax
Flax, also known as common flax or linseed, is cultivated as a food and fiber crop in regions of the world with a temperate climate. It is one of the strongest plant-based natural fibers, and was one of the first to be harvested, spun and woven into textiles.
The pest-resistant flax plant (Linum usitatissimum) does not require fertilizers and needs far less water to grow than cotton; the retting process to produce the fiber also requires much less water. And unlike cotton, flax is processed using a completely mechanical method that does not involve the use of harsh chemicals.
Flax fibers have a much higher content of non-cellulosic material than cotton, generally containing a mixture of about 75% cellulose, 15% hemicellulose, 2.5% pectins and 2% lignins.
Flax fibers are stronger than most other natural fibers, but are less pliable and elastic. Flax has a similar moisture regain to cotton, but absorbs moisture much more rapidly, making it suitable for towels and drying cloths.
Fine fabric woven from flax is known as linen, which is a soft, lightweight, breathable material that is naturally hypoallergenic, which makes it eminently suitable for warm-weather clothing. Meanwhile, flax, along with other plant-derived natural fibers, such as kenaf and jute, are also increasingly being used as automotive components.
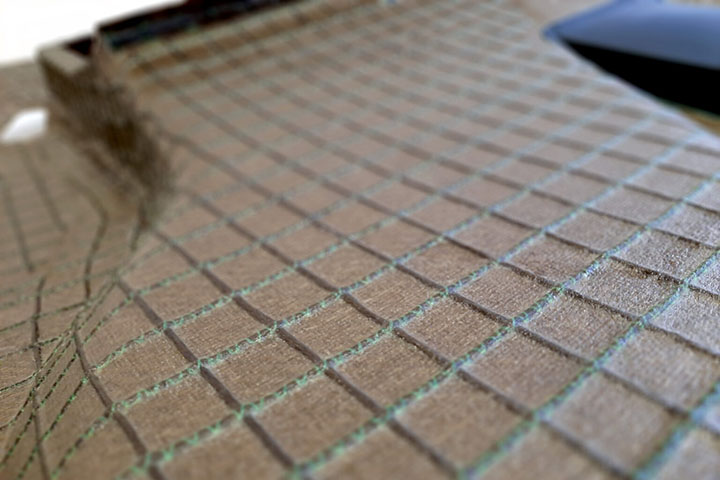
Humble jute
Jute (Corchorus), a long, soft, shiny bast fiber that can be spun into string and coarse yarns, is traditionally used to weave fabrics such as burlap sacks (hessian), rugs and carpets, as well as ropes. More diversified uses of jute include products such as espadrilles.
The processing of jute requires a retting process, either chemical or biological, to remove the pectin between the bast and core of the plant, which helps to separate the fibers.
Kenaf composites
Kenaf (Hibiscus cannabinus) is a fibrous plant that is stiff and strong with a high resistance to insects. Kenaf fibers have traditionally been used to produce paper, ropes, twine and cords. Together with other materials the fibers can also be used in composites for use in automotive, construction, packaging and furniture applications.
Bamboozled by bamboo?
Bamboo (Bambusoideae), a type of fast-growing grass, also requires significantly less water (up to four times less) to grow than traditional cotton and is self-generating, without the need to continuously replant. And like cotton, bamboo is highly absorbent and hypoallergenic, but can be cultivated without the use of pesticides or fertilizers.
In fact, clothing labeled as being made from bamboo is usually viscose rayon, made by dissolving the cellulose in the bamboo and then extruding it to form fibers. This process removes the natural characteristics of bamboo fiber, rendering it identical to viscose from other sources of cellulose.
But this does include a chemical process that involves the use of sodium hydroxide and carbon disulfide – compounds that can be hazardous to human health, although the trace amounts of these chemicals used for production can be considered negligible.
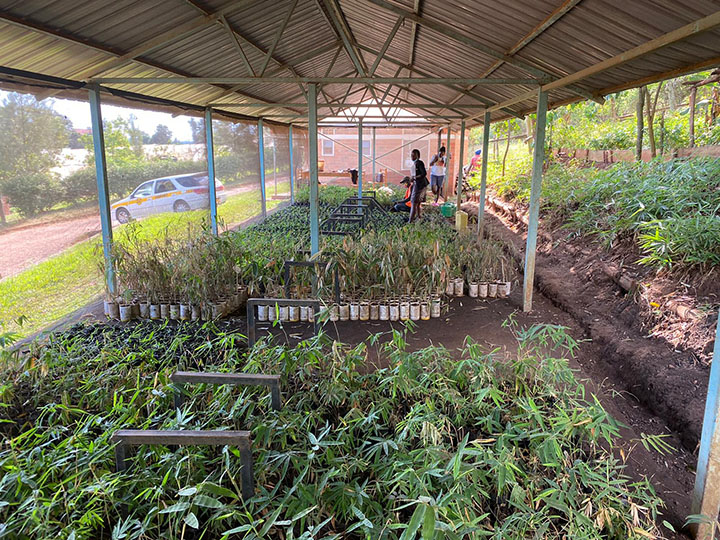
Sisal strength
Sisal (Agave sisalana) fibers have a good spread of mechanical properties, particularly strength, durability, elasticity and resistance to deterioration in saltwater, and are commonly used in the flooring, automotive, shipping (for mooring small craft and handling cargo) and construction sectors, as well as the core of the steel wire cables of elevators, and as agricultural or baler twine.
Pineapple leaves
London, U.K.-based Ananas Anam has developed Piñatex, a natural textile that utilizes the fiber by-products of the pineapple (Ananas comosus) harvest. The resultant material is lightweight, soft, flexible, breathable and durable, and can be used as a natural leather alternative in footwear, clothing, fashion accessories, interior furnishings and automotive upholstery applications.
Piñatex is produced partially from a waste product that requires no additional land, water, pesticides or fertilizers. It takes around 480 pineapple leaves (the waste from 16 pineapple plants) to produce one square meter of Piñatex fabrics.
However, the use of pineapple leaves as a fabric is a technological alternative that is still in its infancy. And Piñatex is not 100% biodegradable – the nonwoven substrate made from 80% pineapple leaf fiber and 20% polylactic acid is biodegradable only under controlled industrial composting conditions.
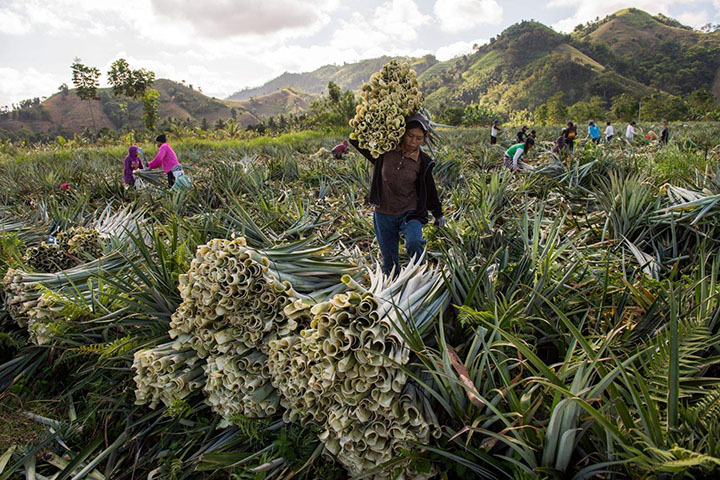
Coconut coir
Coir is one of the thickest and most resistant natural fibers, derived from the outer husk of the coconut husks – it is the fibrous material found between the hard, internal shell and the outer coat of a coconut (Cocos nucifera).
Coir fiber is relatively waterproof and one of the few natural fibers resistant to damage by saltwater. It is typically used in such products as floormats, doormats, brushes, mattresses, floor tiles and ropes, as well as in upholstery padding, sacking, fishing nets and horticulture.
Coir derived from 100 coconuts can produce 1 kg of fabric. As the fabric is derived from a by-product that would otherwise be disposed of, there is no need for additional water or land. Coir is also a highly renewable fiber – coconut harvests occur every 30–45 days.
A few years ago, a type of “coconut fabric” was being acclaimed as the future of sportswear. Cocona uses activated carbon from coconut shells and volcanic sands – waste from the food and water filter industries, respectively. The particles are produced using dynamic thermoregulation technology called “37.5” (the body’s ideal core temperature in degrees Celsius), developed by Cocona, based in Boulder, Colorado, which can then be impregnated into more standard synthetic fibers, such as polyester and polyamide.
Cocona fabric is said to dry quickly, about 92% faster than cotton, produce less odor and can be laundered more frequently. It is also highly durable, providing protection against ultraviolet radiation and is wrinkle resistant.
However, Cocona fabrics have yet to take the world by storm. And while Cocona clothing is suitable for vegans, its production may involve monkeys to harvest the coconuts.4
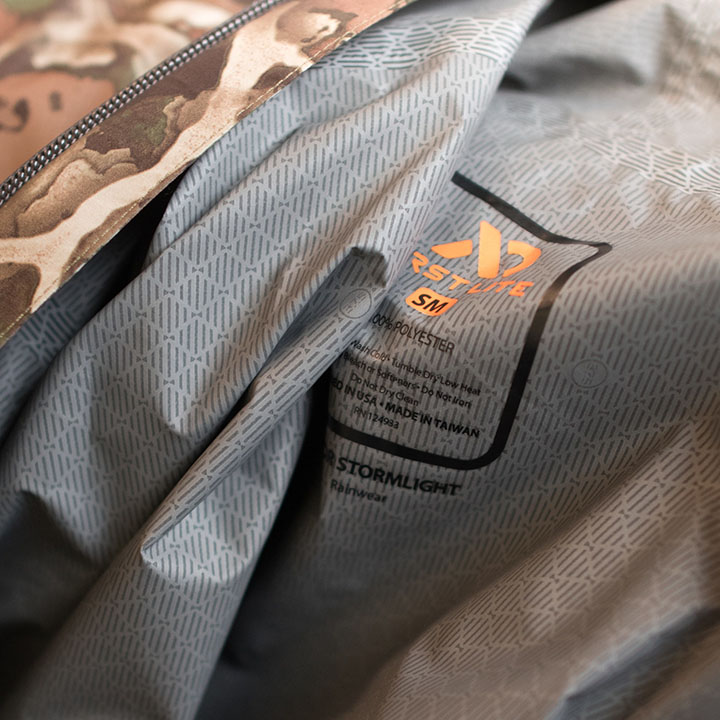
Sour milk
In pushing the boundary of what is an alternative fiber, several developments have used sour milk to make a sustainable fabric.
German company Qnature has developed QMilk, a 100% natural, non-allergenic biopolymer that is manufactured through a resource-efficient, zero-waste process using no chemical additives, it is claimed by the company.
The QMilk process uses casein, a protein that makes up about 80% of milk protein content, produced from the raw milk from dairies that is no longer tradable and cannot legally be used as food.
QMilk yarns are said to be ideal to spin with other natural or synthetic fibers to produce a silky-smooth yarn with moisture absorption and antibacterial properties. Potential end uses include fashion, home textiles, automotive, and medical and hygiene applications, such as nonwoven wipes.
But considering both fiber production and textile processing, there is no such thing as a 100% sustainable fabric, although some may be better than others. Meanwhile, “sustainable fashion” has become such an overused phrase that few consumers know what this really means; misinformation abounds in an era of over-consumption.
Meanwhile, Duedilatte, a Tuscany, Italy-based fashion label, has also developed a process to convert milk protein into fiber, creating T-shirts and baby clothing with potential expansion into bedding, medical and automotive.
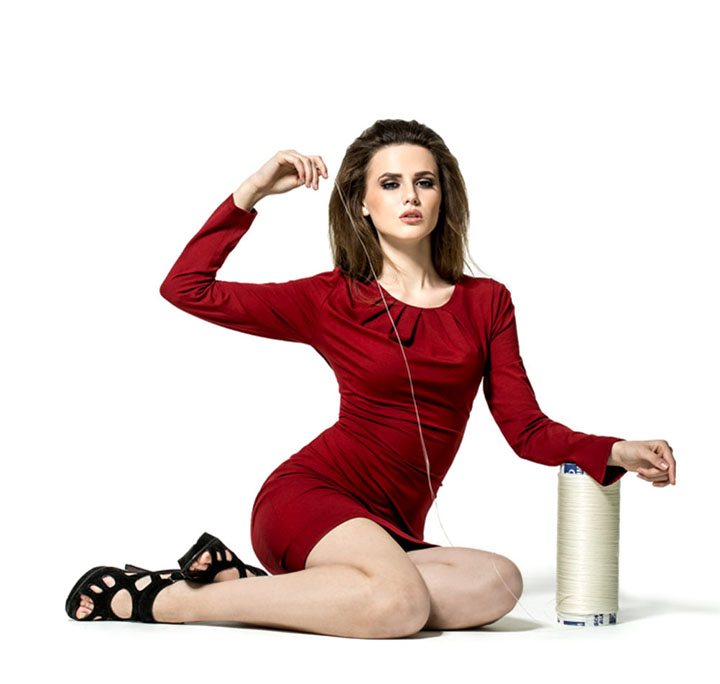
Turning milk by-products into a silk substitute is not exactly a new idea. In the 1930s, Italian engineer Antonio Ferretti managed to produce fabric from milk, and Italian company SNIA Viscosa began producing milk-based fabric on a large scale, even selling patents to other countries, including Germany, Belgium, Japan and the U.K.
However, the new fabric had its problems – it was not as soft or durable as wool and yarns tended to fall out of the material when ironed. Italy’s milk-based products quickly went out of fashion at the time, unable to compete with the arrival of synthetics that were both more resistant and considerably cheaper.
As well as using milk casein, Duedilatte chief executive officer and founder Antonella Bellina has developed fibers derived from other natural raw materials from the agricultural food chain, such as rice and coffee.
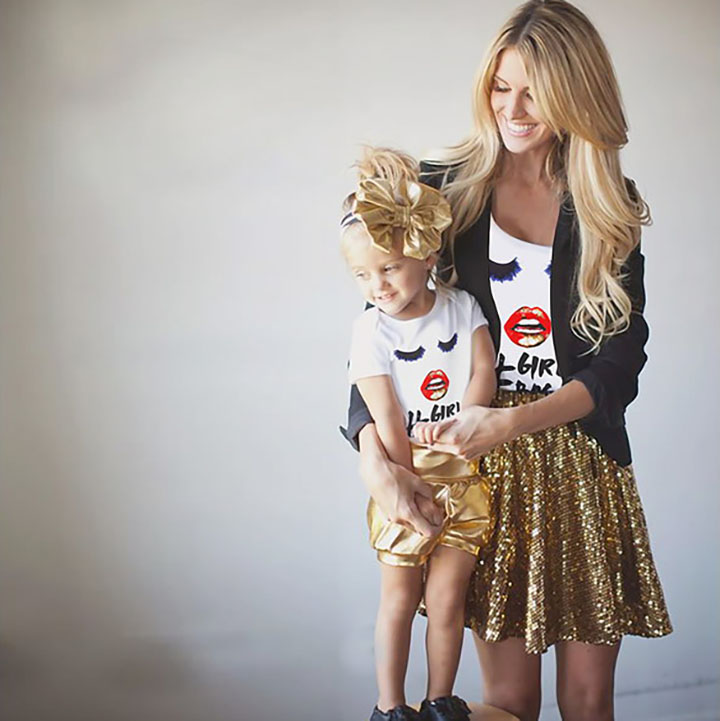
Sustainable fashion?
Consumers are often told that natural fibers are good for their health and well-being and good for the environment. They are comfortable to wear, they are a sustainable resource and can be used without depleting or damaging the natural environment.
But considering both fiber production and textile processing, there is no such thing as a 100% sustainable fabric, although some may be better than others. Meanwhile, “sustainable fashion” has become such an overused phrase that few consumers know what this really means; misinformation abounds in an era of over-consumption.
While both animal and plant fibers are generally biodegradable and renewable resources, the rate at which we produce and consume them, often resulting in overgrazing and extensive land use, may not be so sustainable in the long run.
References
1. “Thirsty for fashion?,” The Soil Association, https://www.soilassociation.org/media/19674/thirsty-for-fashion-soil-association-report.pdf.
2. “Tons of cotton produced,” The World Counts, https://www.theworldcounts.com/challenges/consumption/cloth ing/world-cotton-production-statis tics/story.
3. “The Impact of a Cotton T-Shirt,” World Wildlife Fund, https://www.worldwildlife.org/stories/the-impact-of-a-cotton-t-shirt.
4. “Is cocona good or bad,” HEALabel, https://healabel.com/c-fabrics-materials-textiles/cocona.