Figure 1: The structure of Conductrol
A variety of antistatic and conductive fiber products have been developed in order to provide antistatic protection and/or static dissipation. Protection from electrostatic discharge is needed for personal comfort, for safety in prevention of explosions in working environments containing explosive dusts and vapors, and for protection of sensitive electronic devices from damage during production and use.
Conductive and antistatic variants are generally made by modifying the base fiber type. Almost all fiber types have been used: nylon, polyester, polyacrylonitrile, cellulose, etc., in the manufacture of commercial products.
Variations in fiber aesthetics and conductivity are made by arranging the conductive element [particle, metal ion, metal, polymer, etc.] as surface coatings, conductive layers in the fibers, conductive components of bicomponent fibers, arranged either side-by-side or concentrically in the fibers or stripes or edges arranged longitudinally along the fiber.
These conductive fiber products generally have relatively higher manufacturing costs and higher selling prices compared to the textile fiber types they are based on. This is due to higher material costs and relatively complex and slow manufacturing processes compared to the base fibers.
Because of this, the conductive fibers generally comprise a small percentage of the total fibers used in these products, yarns, fabrics, carpets, etc.
These fibers generally are designed to have properties that meet the performance parameters required for the end product. Because of the particular technology used, there may be deficiencies in the performance of particular products. In particular, the chemical and thermal durability is very important in many end uses such as carpets, filters, upholstery, apparel, paints, coatings and laminates.
FIBER PROPERTIES
Sterling Fibers has uniquely engineered Conductrol™; an acrylic-based conductive fiber, to combine the stability of conductive carbon based materials with the enhanced conductivity that is achieved by modification with a conductive polymer. The structure of Conductrol is illustrated in Figure 1.
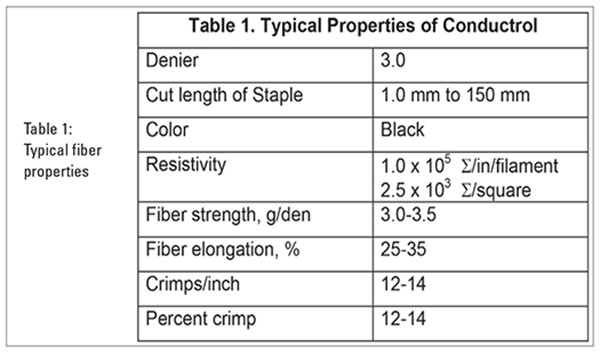
The fiber can be processed in textile systems the same as standard acrylic fibers. It can be blended into staple blends with acrylic fiber and with other types such as nylon and polyester. It can be carded, drawn, and spun into yarn using the ring spinning system as 100% Conductrol or in blends from 0.5% and up. Yarns can be knit or woven into fabrics using standard procedures. Such blends can be carded and the resulting web formed into nonwoven fabrics by hydroentangling, by needle punching, and by chemical and thermal bonding.
Short cut Conductrol can be blended with other fibers or with pulp and formed into nonwoven fabrics or papers by wet laid processes. Short cut Conductrol can be blended into resins, and paints to provide coatings with good antistatic protection and electrostatic dissipation. Short cut Conductrol can also be compounded into rubbers and plastics to provide antistatic articles.
DURABILITY OF CONDUCTROL
Conductrol is intended for use in a variety of environments: different temperatures, varying chemical contacts, wide pH range, and various cleaning agents. Therefore a number of durability tests were run over a range of conditions.
Thermal Stability Conductrol fiber was heated in an oven in an accelerated aging test at temperatures of 300 0F and 330˚F. A six inch specimen of Conductrol staple was cut. The initial resistivity was measured [AATCC Method 76-1995] and the specimen hung in a constant temperature oven with forced air recirculation. At different exposure times the specimen was removed from the oven and the resistivity was measured. This procedure was repeated for the length of the test. Results from the test at 300˚F are shown in Figure 2. The test at 330˚F was terminated after twelve days because the base acrylic fiber degraded at that time. Results from this test are shown in Figure 3.
Laundering durability
Multiple laundering tests were carried out on a sample of the Conductrol tow according to AATCC Test Method 61-1984. The resistivities of the laundered tow bundles were then measured according to AATCC 76-1995. The Conductrol did not show any increase in resistivity up to 75 launderings.
Chemical stability
Durability of the conductivity of Conductrol in solutions with pH range of 3.0-11.0 was studied (Figure 4). The fibers were soaked at room temperature in solutions over this pH range. The conductivity was found to be quite durable over the pH range from 3.0-9.0 for up to 60 hours. At pH 11, the conductivity decreased and stability was fair.
Stability of Conductrol in contact with a typical industrial floor cleaner, wax composition and bleach was determined. The fiber resistivity was quite durable in detergent and wax compositions. However, in the oxidizing concentrated bleach, the resistivity increased rapidly.
APPLICATIONS
Filtration
Explosive dusts are typically removed from air streams and stack gasses by filtration. Electrostatic discharges pose a serious problem in that they can cause explosions. Use of antistatic and conductive filter media prevents these explosions. Conductrol can be used in cost effective filter media compositions and greatly decrease the chance of such explosions. The conductive elements are stable to the chemical and thermal conditions for the life of the filter bag.
In one method of application, the Conductrol fibers are blended at levels of 1-10 % with other fibers such as acrylic and polyester. These blends are formed into yarns and then woven into fabric suitable for use in filter bags.
In another method, the Conductrol fibers are blended at levels of 1-10 % with other fibers, such as acrylic and polyester. These blends are carded into webs. The webs are used in a needle punched fabric, usually with a supporting scrim fabric for strength.
Carpet backing
Conductrol can be incorporated into needle-punched primary carpet backing for ESD carpets. Typically, such carpets contain nylon filament yarns in the carpet face, with conductive nylon filament yarns arranged across the carpet. The conductive primary backing serves to interconnect the face yarns across the carpet, allowing a very effective electrostatic dissipation and prevention of electrostatic discharge in a cost effective composite carpet.
Upholstery
Conductrol is incorporated into upholstery fabrics to provide electrostatic dissipation. The level can be adjusted to provide enough protection from the level needed to prevent uncomfortable electrostatic discharge in cold, dry climates to the level needed in ESD upholstery fabrics for use in electronics manufacture, fabrication, and use.
Apparel
Clothing designed for ESD protection is required in many working environments, such as electronic equipment fabrication, manufacture, and use; explosion prone environments such as explosive manufacture, oil well work, and petroleum processing. Conductrol can be incorporated into a wide variety of comfortable, good fitting, aesthetically pleasing apparel products such as hosiery, knit shirts, lab coats, gloves, sweaters, and pullovers for use in such ESD controlled environments. Fiber blends of Conductrol with acrylic, polyester, and nylon may be made into yarns. The yarns are readily knit or woven into the appropriate fabrics. Either 100% of an intimate blend yarn, which gives a uniform appearance to the fabric, or grid-type spacing of conductive yarns may be used. The blend ratios and spacing of the grid yarns may be adjusted to provide the desired level of conductivity.
Specialty materials
Conductrol cut into very short staple lengths is incorporated into specialty materials and composites. Examples include epoxy floor coating, adhesives, paper, and rubber. The blend ratio may be adjusted to give the desired level of conductivity.
SUMMARY
Sterling Fibers has uniquely engineered Conductrol to combine the stability of carbon based fibers with the enhanced electrical performance of modified fibers. This delivers a superior conductivity/dollar ratio in most applications. With the exception of concentrated chlorine, the conductivity of Conductrol lasts in every environment tested for as long as the base acrylic fiber lasts. This fiber is easily processed by textile equipment and can be blended with virtually any other fiber at levels from 0.5% to 100% to achieve the desired conductivity in the final article. This fiber has been used in applications including bag house filtration, carpet backing, upholstery fabric, various apparel articles, and specialty materials.