Development of Electrically Conductive Polyester Yarn by Surface Modification for Smart and Technical Textiles
Until textiles take their place in our lives, it involves many complex and long processes such as fiber and fabric production, finishing processes, sales and marketing (Figure 1). Textile structures, which were first developed to meet the dressing needs of people, are now designed to serve many current needs with flexible and functional product design of materials science.
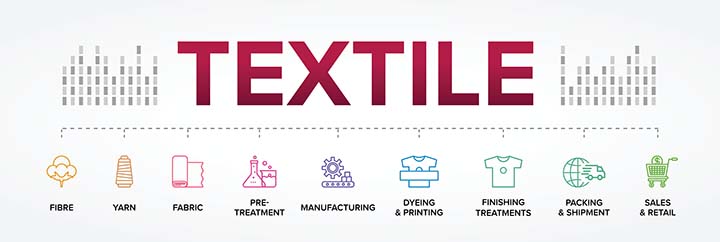
Growing Niche
In the recent years, electronic textiles (e-textiles) as a class of soft or flexible electronics have generated a growing interest due to their many potential applications in healthcare, security, entertainment, and others (Figure 2). Electronic textiles (e-textiles) combine electronic capabilities of devices such as sensors, actuators, energy harvesting and storage devices, and communication devices with the comfort and conformability of conventional textiles. At this point, conductive textiles are designed to serve the niche products of smart textiles.
When developing these materials, conductive yarns will play a key role. Of course, they have to be softer than metals, but durable and elastic as conventional yarns. There are some applications of smart textiles in the market. For instance, some woven apparels produced with conductive yarn, senses the movement and touch of the body. These interactions are activated in the sensitive area of the garment. The other examples enable wearers to answer calls, play music and take photos directly off devices on their arms.
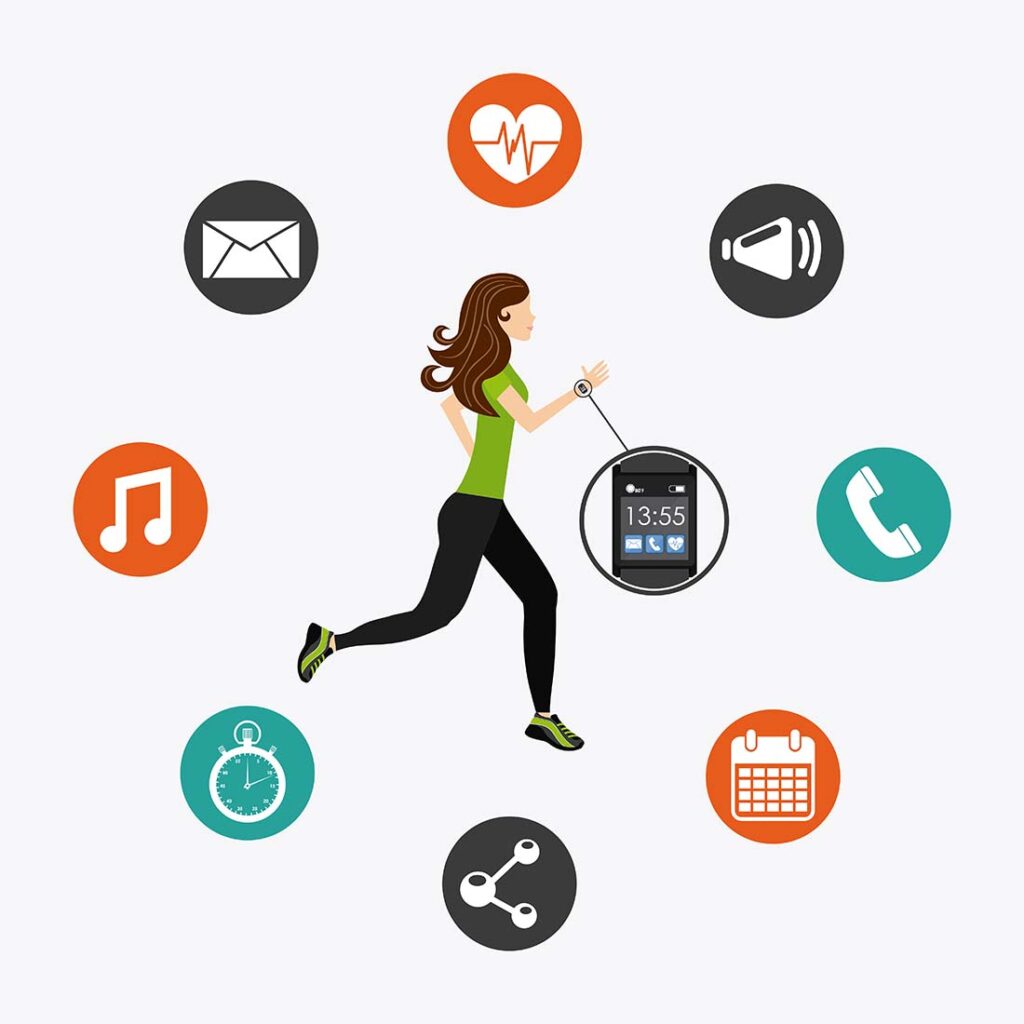
The sales in the global conductive fiber market have exceeded 1.8 billion USD in 2022. The forecast of the market share will reach 4.9 billion USD by 2031, as seen in Figure 3[1]. The main reasons for this change in growth rate are the growing demand of conductive fibers with high growth potential for their high flexibility, durability and lightness. It is thought that it can replace copper cables in the aerospace industries in next years. Conductive yarns on the market today have a very high price up to of $800 kg. Textiles made with conductive yarns serves a niche of high value-added products in the market.
Production Varies
Conductive textiles can be produced in many ways. Some of them are: using metallic yarns, conductive polymers, carbon nanotubes, grafen and applying functional coatings. Functional coatings don’t look like traditional coating methods such as protection and decoration. Textiles are soft, comfortable, washable, and lightweight.
Any coating technique or method that is used for conductivity, must impart electrical conductivity and good sensing performance without loosing these properties. Ideal material and application for functional coating should offer a balance in terms of process-ability, sensing performance, environmental stability.
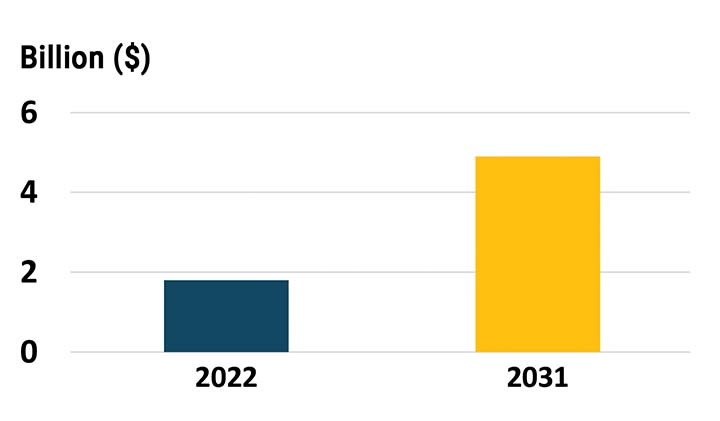
Oxidative Chemical Vapor Deposition (oCVD) is a recently developed innovative technique, an efficient, solvent-free technique used to obtain uniform, thin and highly conductive polymer layers on a variety of flexible and rigid substrates. In addition, oCVD method is an environmentally friendly surface modification method that has been developed in recent years, and it allows the materials to be provided with a wide variety of permanent functional properties with very little chemical use.
Conductive yarns can be developed by oCVD method in a very sustainable and efficient way. In oCVD method, the surface of the polyester yarn is treated with a liquid oxidant and then the surface is subjected to monomer vapor. The monomer polymerizes on the surface under suitable ambient conditions and forms a polymeric layer. Conductive EDOT monomer can be easily used in the oCVD method due to its volatile nature and turns into PEDOT by polymerizing on the surface.
Coated Polyester Yarn Project
In the KORTEKS Conductive Polyester Yarn Development Project, untreated polyester yarn is treated with oxidant chemical then fed into the OCVD reactor. Iron chloride was used as oxidant and the conductive EDOT monomer vapour was fed into the reactor. The yarn passes through the modified yarn guides in the reactor. Vacuum and heating is applied during coating. After coating, a washing process is applied to remove the unreacted oxidant remaining. Finally the yarn is wounded on a spool (Figure 4).
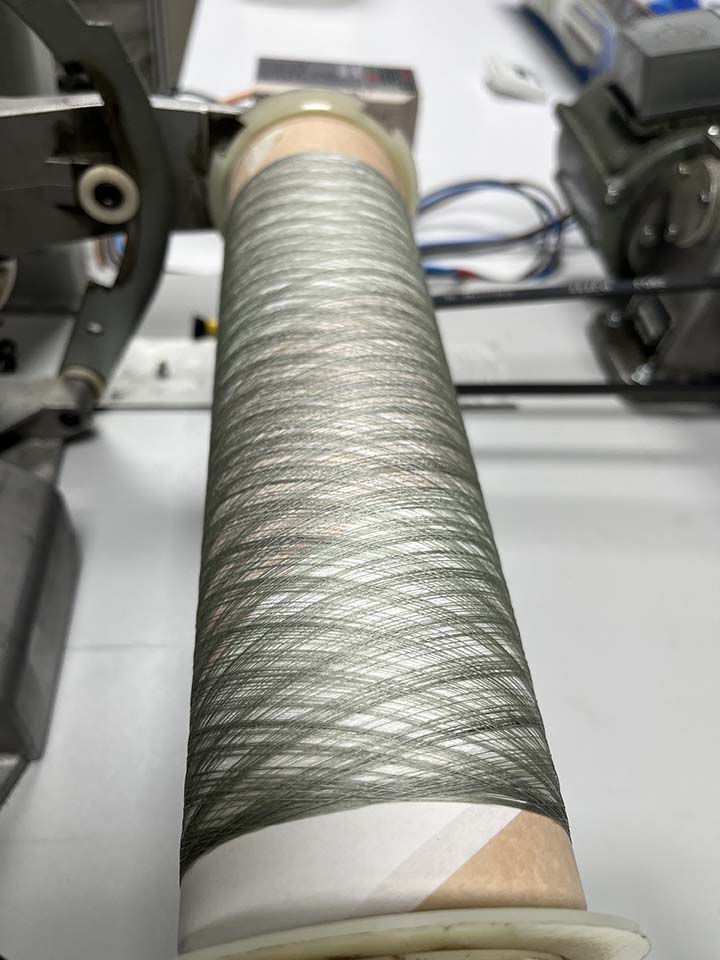
The PEDOT coated polyester yarns have electrical conductivity to light led lamps. However, for scale up (reel to reel) coating processes, devices/processes are required for commercial products. In addition,
durability is an important criteria for industrial products. So, durability of the coating will be also studied with future weaving/knitting/dyeing/finishing trials.
Raw Material of the Future
A conductive yarn can be used in many ways in many applications. For now, the most interesting applications of wearables are around fashion, music, entertainment and healthcare. In the next several years, we are likely to witness the emergence of new strategies to design and manufacture complete e-textile systems including power supply, communication, activation and data processing.
It’s thought that conductive polyester yarns are promising candidates of raw materials intended for various wearable and smart fabric applications as a new platform for future textile electronics.
- https://www.futuremarketinsights.com/reports/conductive-fibers-market