Held in late 2024, E-Textiles: International Conference on the Challenges, Opportunities, Innovations, and Applications in Electronic Textiles, was hosted by the E-Textiles Network, and brought together many of the discussion points that have come to the forefront, from commercializing innovation to environmental impact, the role of design and embedding testing within the development process. Founded in 2018, the Network aims to accelerate the development and adoption of e-textile technology.
The annual conference facilitates and highlights research activities from academia, research institutes, and industry, attracting delegates from these sectors. The event rotates around a series of European cities; Fraunhofer Forum in Berlin, Germany, was the location for E-Textiles 2024 held in November, where the Fraunhofer IZM hosted it with sponsorship from IEEE and the IEEE Electronics Packaging Society EPS.
The conference provided a packed program of six sessions over three days, with the themes of Research and Technology, Design and Fashion, Sustainability and Circularity, Reliability and Testing, and Manufacturing and Applications. While the Network is thus far primarily European, the perspective is global, attracting speakers and delegates such as AFFOA, Nautilus Defense, North Carolina State University, and Meta from North America. The addition of an exhibit area and the poster pitch sessions were well received and showcased early-stage research and more established start-ups and SMEs.
So, how has e-Textiles 2024 expanded the field? What key discussions dominated the event? How might these be seen as harbingers of near-future trends?
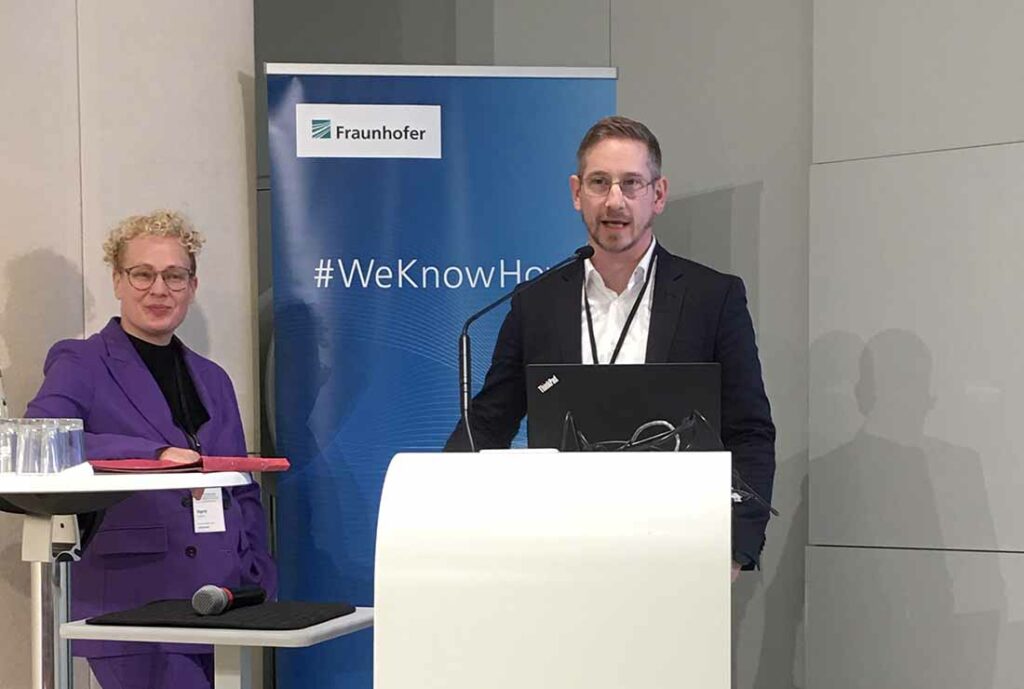
Commercializing Innovation
‘Time to market’ has been a big topic for industry and researchers in academia. In the opening address, Rolf Aschenbrenner, Deputy Head of Fraunhofer IZM, emphasized its importance. While it is not as headline-grabbing as artificial intelligence (AI), it is more of a defined entity that can be addressed within and by industry and academia. The bottom line is that research and innovation will decline without the very real possibility of achieving scale and commercialization.
Cooperation enables the scaling of ideas, as illustrated by a joint paper from Tuomas Happonen, VTT Technical Research Center of Finland, and Mikko Paakkolanvaara, Screentec. Their paper, “Stretching reliability of SMD electronics integrated on elastic fabric,” discusses the manufacturing flow of integrating surface-mounted devices (SMDs) into the stretch fabric. This process is based on printing, converting, and assembly to integrate rigid SMD electronics exploiting novel material solutions such as stretchable inks and adhesive bonding technology needed to achieve the required electromechanical performance at low processing temperatures. SMD thermistors, printed wiring, multiple materials, and design configurations were integrated on both thermoplastic polyurethane (TPU) and a stretch fabric using a TPU lamination process. Tests and electromechanical characterization revealed the importance of material stack strengths and the layout design. The overall results were positive, and in maximum stretch tests, 100% stretchability without catastrophic failure was achievable.
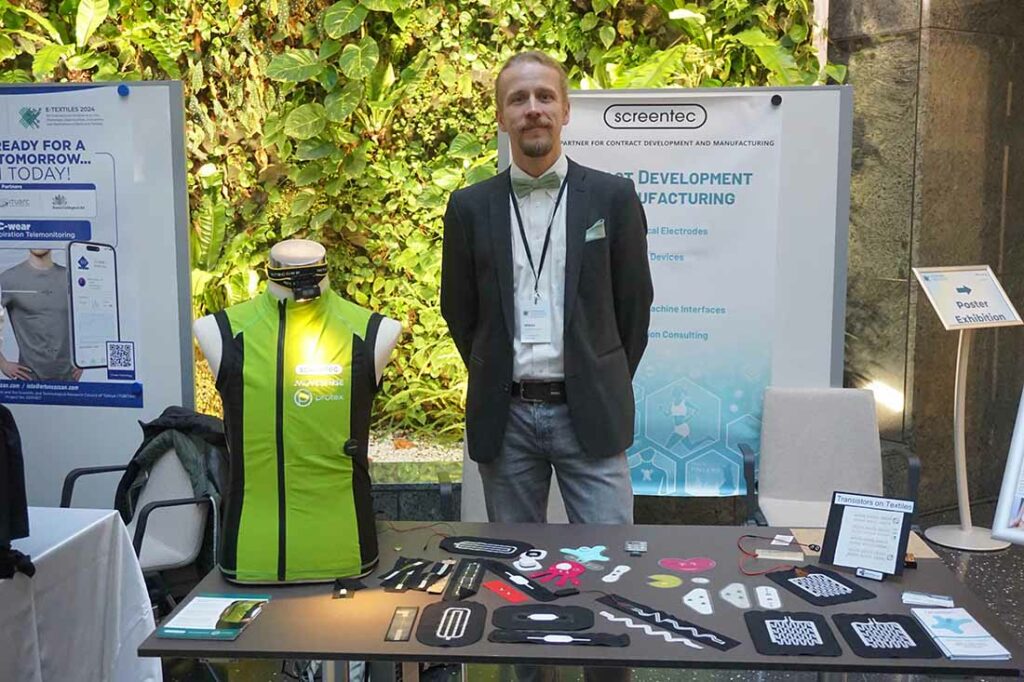
The interconnection process needed to integrate electronic modules into textiles is one of the most vexing challenges in bringing e-textiles and wearables to scale for commercialization. A research team from the Technical University of Berlin and the Fraunhofer Institute for Reliability and Microintegration IZM presented their paper titled “Towards industrialized e-textile assembly: low-temperature optimization of textile-electronic NCA bonding.” Soldering and mechanical connections such as crimping, magnets, snap fasteners, and hook and loop are commonly used, as is ultrasonic welding.
In their presentation, the researchers made the case for adhesive films as a reliable adhesion between the printed circuit board (PCB) and textile at temperatures below 130°C in addition to scale. This has the benefit of maintaining the integrity and functionality of the final product while bringing environmental benefits by reducing the energy requirement during production. This is achieved using a thermoplastic adhesive that has been pre-laminated to the base layer of the PCB and interconnected with textile-integrated circuits under the influence of heat and pressure. The follow-on process of cooling under pressure ensures that the result is a reliable interconnection.
Most presenters have a line beyond which information is withheld for reasons of IP, which is entirely sensible and acceptable at conferences. In Meta Reality Labs presentation, “Manufacturing Challenges in e-Textiles,” the speaker covered the issue in very general terms, mentioning such factors as the requirement for an extensive engineering effort from multiple disciplines to achieve manufacturing readiness; a deep understanding and knowledge of textile manufacturing; collaboration with the electronics industry; equipment and process optimization through partnerships and market acceptance. Unfortunately, the presenter did not specifically discuss Meta’s work in this area. When I asked the speaker for more details, they redirected me to the company’s website and conveyed that nothing beyond what was publically available could be discussed.
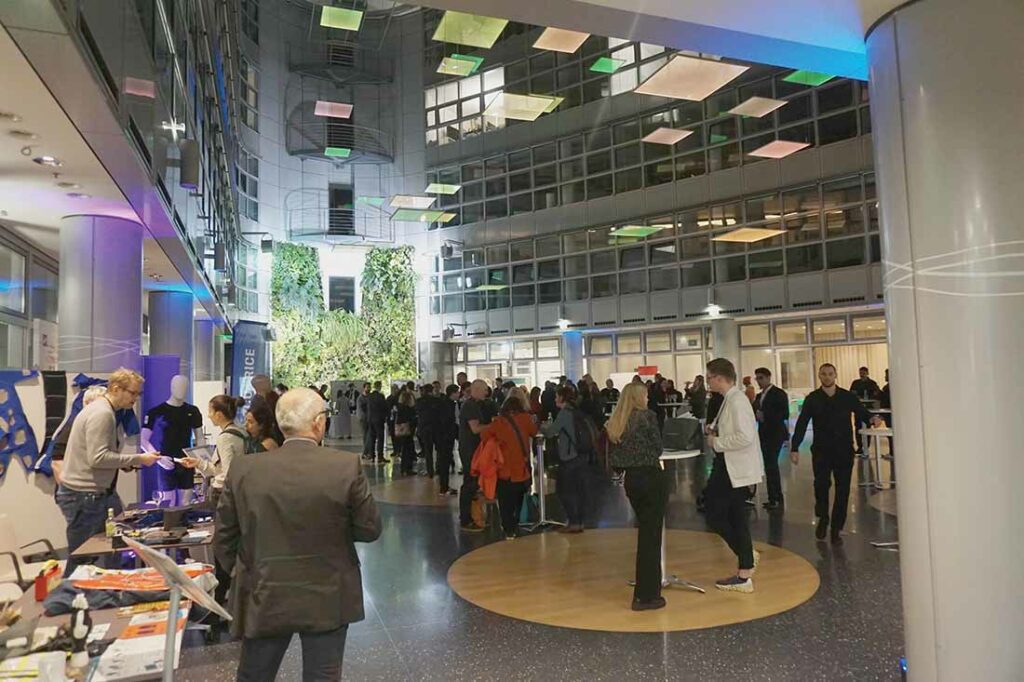
Meta has patents registered in the U.S. and EU patent offices relating to their work on a future smartwatch and next-generation risk device intended to work with upcoming XR meta headsets. One of their more interesting patent applications from an e-textile point of view is US 2023/0376112 A1, relating to knitted textile structures formed by altering knit patterns to accommodate external mediums and manufacturing processes associated with these. In this example, a level of detail has been publicly available for some time.
Environmental Impact
There has been a shift in the language around sustainability and e-textiles over the past year. While full circularity is still an avowed goal, in the short- to medium-term, researchers are looking to see what aspects of this they might address now to achieve a degree of progress. Presenting an Aalto University group-authored paper titled “Sense and Degrade: Fully Bio-Based and Biodegradable E-Textile Capacitive Sensor,” Sofía Guridi spoke about the need to prioritize more sustainable materials, specifically replacing non-renewable and toxic plastics and metals with renewable and biodegradable materials. The intention is to facilitate disassembly using novel cellulose-based conductive and dielectric materials combined with a wool and carboxymethyl cellulose (CMC) woven substrate. In an iterative process, a series of prototypes is developed and tested. In the first prototype, water droplets were applied to the sensor core back CMC layer to attach it to a woven wool textile.
A second prototype introduced the sensor’s core into a woven wool pocket. In the final prototype, a combination of wool yarns and CMC films was woven to create a textile pocket where the sensor’s core was introduced. The researchers have developed the work to the proof-of-concept stage, demonstrating disassembly through the water at the end of life. The intention is to help open a research path for mono-material developments in e-textiles.
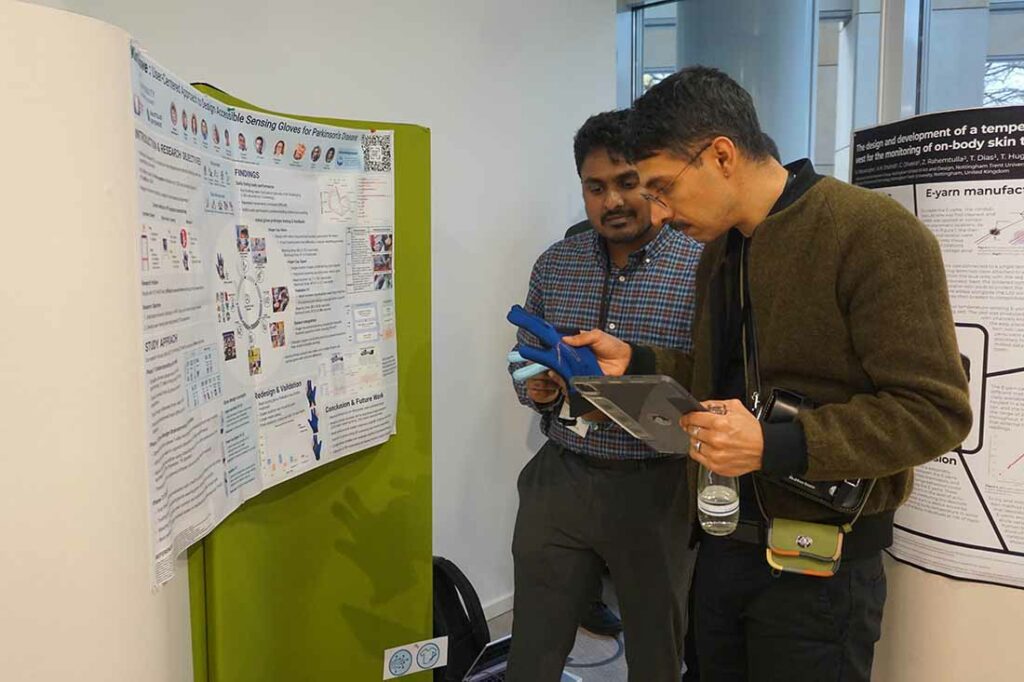
Health and Medical Applications
One of the dominant themes of the conference, health and medical applications, included papers from a multidisciplinary team from Austria and Switzerland addressing the need to monitor elderly patients for respiratory problems in their homes. In a paper titled “Wearable Health Monitoring Textile Band with Direct Inkjet Printed Electronic Island,” inkjet printing was brought together with e-embroidery as part of the FFG-funded TEXhype project. The aim is to integrate multiple sensor islands into a stretchable textile-based belt seamlessly. This is done using a combination of direct-to-garment inkjet printing of multi-material electronic islands along with conductive yarn embroidery. The researchers believe that the versatility offered by bringing these two processes together will pave the way for a scalable process and commercialization that addresses the need for the optical heart rate sensor to directly contact the skin. This will detect changes in the reflection of emitted light that varies with blood volume fluctuations occurring beneath surface of the skin. To do this, the electronic island for heart rate detection is located on the inner side of the belt ensuring a consistent contact with the wearer’s skin during use. The work is currently at proof-of-concept stage with the next step to conduct a clinical validation study.
Gillian Lake-Thompson presented “Design and development of a knitted e-textile sensing environment for fetal heart monitoring”, work undertaken by the speaker and colleagues at WSA, University of Southampton and the Beijing Institute of Fashion Technology. The intention here is to offer an alternative to rigid devices such as cardiotocography (CTG) in the form of a flexible, wearable garment that is visually discreet and can be used for long-term monitoring in clinical environments as well as in the patient’s home. Researchers at ETH Zurich and Donghua University, Shanghai, addressed the need to make sensing during motion monitoring visible to the eye for applications in personal healthcare, disease detection and diagnosis. Their paper titled “Mechanoluminescent Fibers for Visualizing Motion Sensing” proposed a novel luminous fiber based on the mechanoluminescent (ML) effect. A core layer of (ZnS:Cu2+) was surrounded by a rubber elastomer sleeve with the fiber shown to emit a visible green light at 520 nm within a tensile strain range of 30%, with the light positively correlated to tensile acceleration. This is achieved without needing to be plugged in or relying on additional electronic components such as batteries or chips making it well-suited for integration to clothing.
E-Textiles 2025 will be held November 12-14, 2025 at ENSAIT, University of Lille, Roubaix, France.