Sustainable Nylon Alternative Bylon™ Progressed by FET and Sci-Lume Labs
Every year, millions of tonnes of apparel fibers are made into billions of garments, the vast majority of which are landfilled or incinerated. Both synthetic and natural apparel fibers cause significant environmental damage, whether through the extraction of non-renewable resources like fossil fuels; the consumption of huge amounts of water, fertilizers and pesticides; the sheer quantity of discarded garments; or the release of pollutive microfibers into our ecosystems and food chains.
The problems posed by apparel fibers are growing. Global fiber production nearly doubled between 2010-2022, from 58 million to 116 million tonnes.[1] Well over half of the apparel industry’s carbon emissions – approximately 600 MT CO2– is attributed to conventional fiber production, ~95% of which is polyester, cotton, man-made cellulosics, and nylon.[2] Responding to mounting urgency by consumers, regulators, policymakers, governments, nonprofits, and other organizations, apparel brands have set ambitious targets to embrace a circular transition in fashion. However, it will be impossible for brands to do so while using conventional synthetic and natural materials.
The challenge of accomplishing a circular fiber transition ultimately comes down to three factors: scale, performance and cost. Circular fibers must scale to meet growing demand; deliver the same performance as best-in-class incumbents; and be cheap enough to be considered viable alternatives by manufacturers and brands. Achieving this industry-wide transformation requires cross-industry, pre-competitive collaboration in order to scale new technologies and accelerate impact.
For example, BASF and Inditex recently announced loopamid, a nylon 6 entirely derived from textile waste. Geno – a biotech company using sugar and microbes to produce industrial chemicals through fermentation – has partnered with Aquafil to develop a biobased nylon 6 that has been brought to market by lululemon. Similarly, Fiber Extrusion Technology Limited (FET) and Sci-Lume Labs have recently collaborated on leveraging FET’s melt spinning expertise to develop a new biobased and biodegradable fiber called Bylon™.
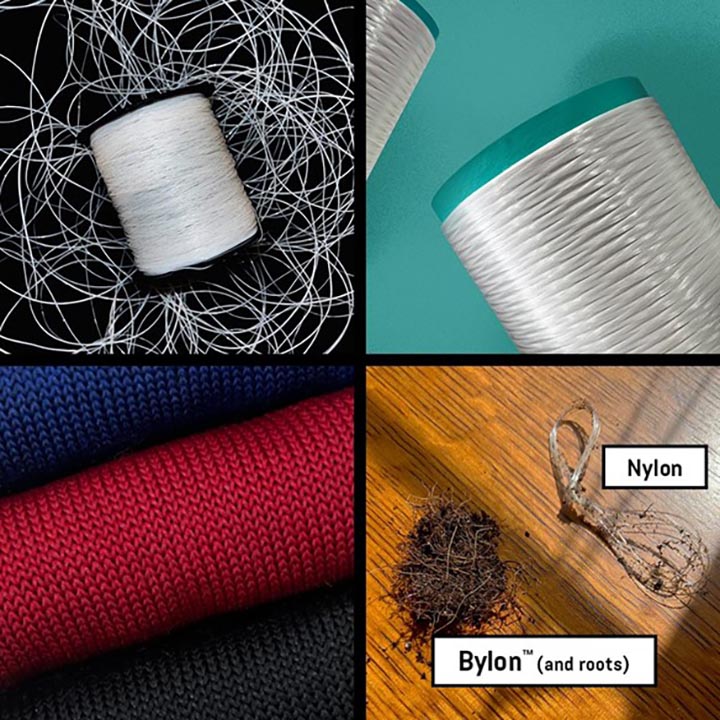
Fiber Extrusion Technology
Established in 1998, FET designs, develops, and manufactures extrusion equipment for a range of high-value textile material applications worldwide. FET’s major strength has always been their ability
to collaborate with customers in testing, evaluating, and developing high-value materials with diverse, functional properties – and making sure their machine solutions are suitable to the task at hand.
The FET Fiber Development Centre is a vital part of this work, enabling access to equipment for customers to test and trial sustainable raw materials and processes. In recent years, a high proportion of FET’s laboratory development time has been related to the sustainability sector, with many of these projects involving clients testing and developing sustainable ways of manufacturing yarns which were previously non-sustainable. In other cases, FET have worked with polymer developers and innovators who wished to further evaluate their technology and push their manufacturing capability to the next level. FET continues to extend their breadth of experience in the sustainability field: they have successfully processed over 30, sustainably sourced, different polymers in multifilament, monofilament, and nonwoven formats.
Bylon uses agricultural waste as its renewable biobased feedstock, is 100% recyclable by both chemical and mechanical recycling technologies.
Sci-Lume Labs and Bylon
Sci-Lume Labs is developing Bylon™ as an apparel fiber that can deliver circularity without compromising on performance, scalability, or cost. Bylon uses agricultural waste as its renewable biobased feedstock, is 100% recyclable by both chemical and mechanical recycling technologies, and biodegrades in the natural environment, resulting in fewer persistent plastics in our ecosystems and food chains.
From the start, Sci-Lume Labs founder Oliver Shafaat knew that to realistically compete at global scale, Bylon needed to be a thermoplastic, ensuring that it could be produced by the same manufacturing equipment used to make incumbent synthetics like nylon and polyester. In need of a partner to prove out his vision for scaled Bylon production, Shafaat contacted FET due to their reputation as a fiber machine manufacturer that could support melt spinning of a diverse range of polymers.
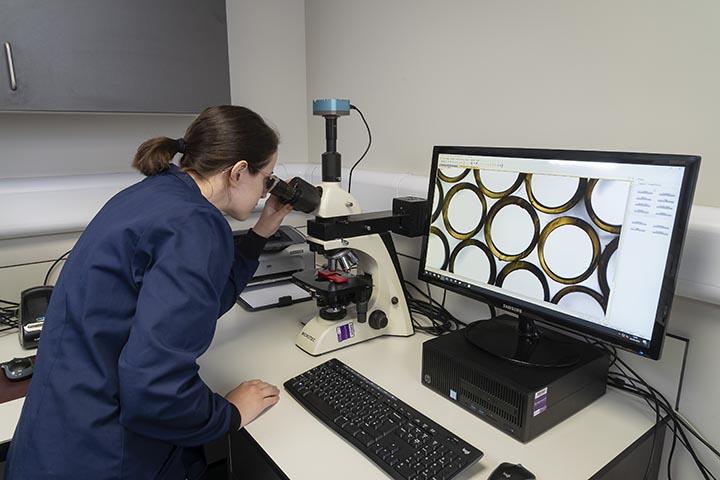
Collaboration Journey
Early discussions between FET and Sci-Lume Labs established FET’s ability to conduct spinning trials at a variety of different scales. While it is possible to conduct lab trials to evaluate spinnability with 100 g of material, these tests cannot produce usable yarns. 1-2 kgs of material is needed to run a trial on a FET pilot line, with larger quantities of 5 kgs or more providing the opportunity to generate substantially more insight into the manufacturability of the new material, while also producing sample yarns.
In 2023, joined by Sci-Lume Labs’ Shafaat, the first multifilament melt spinning trial was conducted at FET’s Fiber Development Centre in Leeds. “I greatly appreciated being able to participate in the trial, as seeing melt spinning first-hand enabled me to better understand the process and anticipate the problems Sci-Lume Labs might encounter as we scaled Bylon production,” Shafaat said. Owing to FET’s preparation, expertise and facilities, the first-ever spinning trials successfully produced viable Bylon yarn for apparel. Sci-Lume Labs subsequently conducted further studies on the new yarn to better understand how it would respond to downstream processing such as biodegradation, knitting, dyeing, and wash/dry cycles. It did so without issue.
A further trial was undertaken at FET with the aim to generate more yarn, and to refine the Bylon spinning process. While this trial was not successful, further offline discussion between FET and Sci-Lume Labs quickly identified the root cause of these problems, which Sci-Lume Labs is working to address prior to future engagements with FET. For those at FET who worked on the Bylon trials, it was exciting to engage with a start-up business driven by such an impactful purpose. Ultimately, the trial work conducted
at FET showed that Bylon is readily spinnable; and the results of downstream work show great promise for the technology.
Furthering the Mission
FET’s work on Bylon has enabled Sci-Lume Labs to better understand their technology and to showcase physical products to apparel industry brands, manufacturers, and potential investors. The progress of this body of work has accelerated Sci-Lume Labs’ technological readiness level (TRL) from TRL 3 to TRL 6, bringing them significantly closer to their commercialization goal. The continuing partnership between Sci-Lume Labs and FET exemplifies the kind of collaboration the fiber industry needs as it works toward a circular transformation. Combining the visionary talents of innovators like Sci-Lume Labs with the deep expertise and flexibility of manufacturing partners like FET brings us closer to realizing a more sustainable future.
References
- Textile Exchange. (2023). Materials Market Report
- https://textileexchange.org/app/uploads/
2023/11/Materials-Market-Report-2023.pdf - Ellen MacArthur Foundation. (2017). A new textiles economy: Redesigning fashion’s future. https://www.ellenmacarthurfoundation.org/a-new-textiles-economy