Cellulose as a Raw Material Could Be the Answer to Future Textile Demand
Cellulose fibers are steadily making their way into a wide range of applications, including textiles, hygiene products and packaging. These fibers have a low ecological footprint, produce no micro-particles and consist of 100% renewable carbon.
Cellulose is the main component of plant cell walls and a natural polymer. It is bio-based and biodegradable, even in marine environments, where its degradation does not cause any microplastic particles.
Moreover, cellulose fibers when washed do not produce microplastics – unlike the laundering of synthetic fiber clothing, which is estimated to be the cause of 35% of the marine microplastics already in the world’s oceans.
In addition, various production technologies for extracting cellulose from plants can be used for the recycling of cellulose, which offers the possibility of circularity of the material.
Recycling Hurdles
With a compound annual growth rate of 5 to 10% in recent years, the use of cellulose fibers within the global textile market is increasing, with major investments being made in the circular bio-economy. Similar growth rates are expected in the future, which makes cellulosic fibers among the fastest growing fiber group in the textile sector.
The textile industry has identified two ways of reducing its pollution: fiber-to-fiber recycling and upcycling of textile waste. At the same time, the packaging industry is looking into alternative materials, including the use of recycled textile fibers. However, the recycling of cellulose does present some hurdles.
Fourth Event

The fourth Cellulose Fibres Conference (CFC) held in March in Cologne, Germany, and online, organized by Nova-Institut, examined how technology can overcome these obstacles, how markets can achieve circularity of the material, and how the cellulose fibers industry can contribute to the sustainability and circularity of the textile sector.
This unique two-day event, first held in 2020, focused on the increasing use of cellulose fibers in the fields of textiles, hygiene products and packaging. It attracted more than 225 participants from 30 countries, with 42 speakers and special panelists – of whom more than 40% were female, coinciding with International Women’s Day on March 8 – around 20 exhibitors and almost 20 poster presentations, both onsite and online.
The conference presented several case studies that introduced novel solutions that attempt to solve the dilemma of textile waste recycling. Other new application fields included cellulosic materials as a precursor for carbon fibers and the use of post-consumer clothing as a raw material to produce protective packaging.
Alternatives to Wood
Wood pulp is forecast to account for around 7% of global textile fiber production in 2025. However, cellulose fiber producers are now looking for alternatives to wood as a raw material – the fibers can be made from residues, by-products and side-streams of various industrial processes, explained Dr. Asta Partanen, senior expert, Nova-Institut.
But with global cotton production stagnant, the cellulose gap has been filled in recent years by the growth in synthetic fibers. Manuel Steiner, business development director of LIST Technology, Switzerland, highlighted the need to find new sources of cellulose. Recycled cotton-rich textiles as a raw material for the lyocell dissolving technology could be a solution, he said.
Dr. Alexander Deutsche, R&D director at Metsä Tissue, pointed out that raw materials from renewable resources are essential for an effective circular economy. Ensuring recyclability and efficient fiber reuse while reducing and replacing plastic as part of the shift from fossil-based raw materials to renewable biomaterials is the ultimate goal, added Anna-Stiina Jääskeläinen of Kemira, Finland.
Lost Opportunities
According to the Ellen MacArthur Foundation, used and unused textile materials valued at US$100 billion are wasted each year. Meanwhile, Textile Exchange estimates that less than 1% of textile fibers are made from textile waste owing to the lack of textile-to-textile recycling systems, adding that global textile fiber production, which has doubled in 20 years to 109 million tonnes in 2020, is expected to grow 34% to 146 million tonnes in 2030.
During a panel discussion at CFC, participants agreed that an effective textile collection system is far from reality and that this will take time to implement. It will also require close cooperation – and trust – between the whole textile value chain. In addition, designing for circularity and end-of-life solutions will be key requirements.
Circular Supply Chain
The EU-funded New Cotton Project comprises a consortium of 12 participants across the textile industry production value chain to demonstrate that creating new clothing from regenerated cotton textile waste can be commercially viable.
The project has demonstrated a cellulose carbamate technology that allows the transformation of textile waste into cost-efficient, cotton-like Infinna fibers with superior qualities, said Paula Sarsama of Finland’s Infinited Fiber Company, one of the project’s participants and the lead innovator.
She explained that overcoming potential bottlenecks to scaling up circular textile production will require:
• finding steady and suitable post-consumer textile streams;
• developing suitable machinery for the separation and fiber identification processes;
• defining suitable textile streams from sorters to recyclers;
• ensuring financial viability of recycling post-consumer garments into new fibers; and
• understanding the post-consumer market and comparing these results to market data on feedstock availability, production flows and current disposal alternatives, such as landfill or incineration.
In collaboration with major global brands Adidas and H&M, biodegradable activewear and denim apparel were made from 100% post-consumer textile waste clothing as part of the New Cotton
Project and launched to consumers in autumn 2022.
Residual Waste Streams
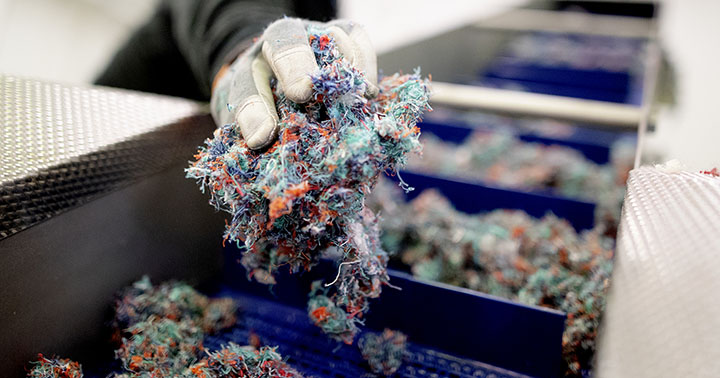
TexChain 3 is a project led by The Loop Factory and Wargön Innovation, together with 32 textile producers and stakeholders in Sweden. The project explores the possibility of generating a more circular flow of textile residuals that mainly originates from worn-out workwear and production-related waste streams.
Trials have been made within eight different prototypes with industrial waste as the raw material, with the goal of creating five products ready for commercialization. Maria Ström and Roos Mulder of The Loop Factory outlined some of the pilot projects, which include upcycling and recycling workwear, and developing a material mixture from old train seats for further processing into new products.
Reusable Diapers
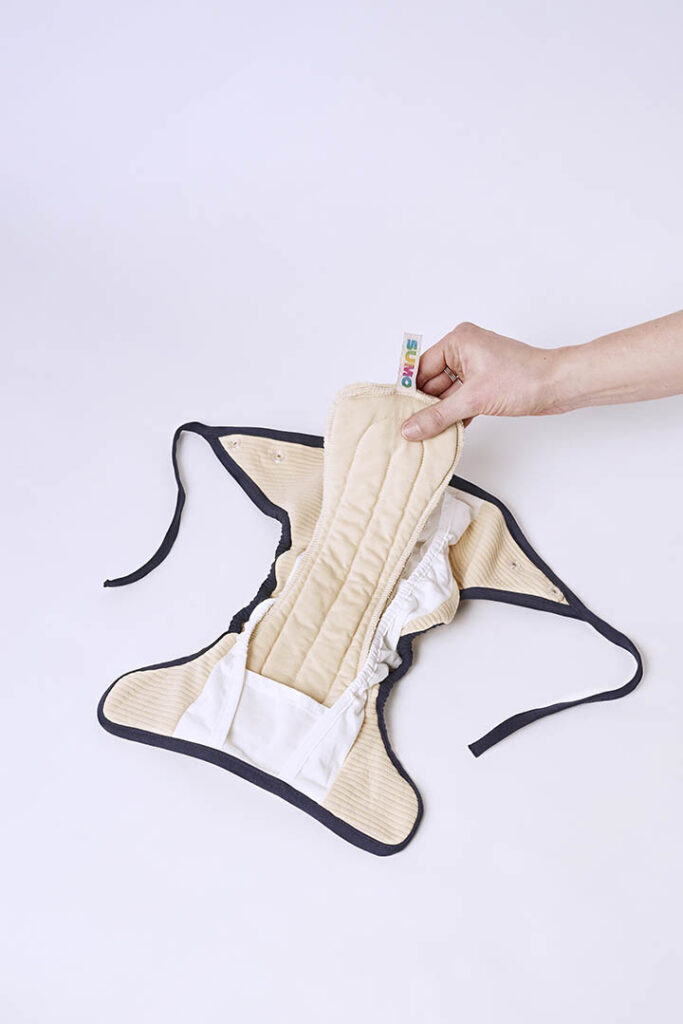
With the market for reusable diapers currently valued at US$53 billion a year with an annual growth rate of 5%, products currently on the market often lack reliability. Due to the high volumes of fluids involved, a highly absorbent construction with fast acquisition and optimized fluid distribution is required to deliver no leakage and low rewet to the skin.
At this year’s CFC, Germany-based start-up Sumo and German specialty viscose fiber manufacturer Kelheim Fibres presented their high-performance absorbent pads for a reusable diaper, which received a Techtextil Innovation Award in 2022.
According to Natalie Wunder, project manager at Kelheim Fibres, and Luisa Kahlfeldt, founder and designer of Sumo, the washable, fitted cloth diaper consists of a waterproof cover and absorbent inserts.
Kelheim’s functionalized viscose fibers with adjusted cross-sections have been integrated, together with polylactic acid bicomponent fibers, into a needle-punched/thermally bonded nonwoven construction to produce a high-performance absorbent pad that uses no fossil-based materials.
Alternative Dissolving Pulps
Birgit Kosan, of the Thüringisches Institut für Textil- und Kunststoff-Forschung (TITK), Germany, explained that the lyocell process is a particularly environmentally friendly process with almost complete solvent recycling.
Although wood-based dissolving pulps for lyocell applications are well established, there is limited availability of wood resources. In addition, climate change, pest infestation and uninhibited forest clearances means there is a need for alternative raw material sources, such as agricultural residues and recycled cotton-based pulps from recycled textiles.
However, spinning parameters in the lyocell process will need to be adjusted depending on the properties of non-wood based dissolving pulps, she advised delegates.
Nature Meets Functionality
Professor Ellen Bendt of the Research Institute for Textiles and Clothing (FTB) at Niederrhein University of Applied Sciences, Germany, described the development of a sustainable knitted cardigan made from 100% hemp as part of the Hanfknit project.
With the participation of local partners, the project was supported by REACT-EU (Recovery Assistance for Cohesion and the Territories of Europe), a program of the European Union that was launched as a reconstruction aid to cushion the economic and social consequences of the COVID-19 pandemic in Europe.
The raw material used was an 80/20 blend of locally sourced unbleached summer hemp and Lyohemp, a regenerated fiber made from hemp straw. This underwent a rotor spinning process followed by knitting on flat-bed knitting machines.
The resulting prototype combines the positive physiological properties of hemp, such as good moisture and temperature management, with the comfort of a knitted garment, said Bendt. And being a mono-material, it also fulfills the requirement for recycling at the end of the product’s life for the circular economy.
Agricultural and seaweed residues were investigated as feedstock for the HighPerCell process, which uses ionic liquids as the direct solvent in the spinning of cellulose filaments.
Wheat Straw as Alternative Raw Material
The EU-funded HereWear project aims to enable local, circular and bio-based textiles. In particular, agricultural and seaweed residues were investigated as feedstock for the HighPerCell process, which uses ionic liquids as the direct solvent in the spinning of cellulose filaments.
Wheat straw was selected as the feedstock owing to its high availability and high cellulose content. Pulp fractionation was performed via pre-extraction, an acetone-based organosolv (Fabiola) process and alkaline treatment to maximize the recovery of the raw cellulosic material, explained Dr. Antje Ota of the German Institutes of Textile and Fiber Research (DITF), Germany, one of the project partners.
The resulting pulps were successfully processed via ionic liquids into HPC filaments made from 100% wheat straw, and the first prototypes have shown the technical feasibility of bio-based garments with good properties of the wheat straw cellulose-based textiles.
Sustainable and Traceable
Rita Valério of CeNTI – Centre for Nanotechnology and Smart Materials, Portugal, outlined the Fiber4Fiber project, which aims to develop optimized dissolving pulp from Portuguese Eucalyptus globulus trees to produce man-made cellulosic fibers, such as lyocell and viscose, which can be traced along the value chain.
As part of the project, modified lyocell fibers are being developed with properties that are appealing to the end user and meet more demanding technical and performance requirements in the market, such as antimicrobial and flame-retardant properties.
GRETE Initiative

Much of the second day of the Cellulose Fibres Conference was devoted to the results from the EU-funded GRETE project, which aims to overcome the bottlenecks in the wood-to-textile value chain, explained Joan Colon of the BETA Tech Center, University of Vic–Central University of Catalonia, Spain.
The initiative aims to improve the existing textile value chain by using a new raw material based on standard paper-grade pulps, implementing novel green technologies based on ionic liquid chemicals and a recovery process for cellulose dissolution with a novel post-modification process to obtain regenerated man-made cellulosic fibers with improved technical properties.
Innovation Awards
For the third time, Nova-Institut organized the Cellulose Fibre Innovation of the Year award, sponsored by GIG Karasek, Austria, as part of the Cologne event. The conference advisory board selected six products from 20 nominations, which were put to an audience vote on the first day of the event, with the awards ceremony taking place in the evening.
In a close-run competition, the overall winner was Nullarbor high-tenacity lyocell fibers made from bacterial cellulose. Developed by Nanollose of Australia and Birla Cellulose of India, Nullarbor is significantly stronger than lyocell made from wood-based pulp – even adding small amounts of bacterial cellulose to wood pulp increases the fiber toughness, said Nanollose executive chairman Wayne Best.
The first pilot batch of 260 kg of Nullarbor (from the Latin Nulla arbor, meaning “no trees”) was produced in 2022 with a 20% bacterial pulp share, and several fabrics and garments have been produced with this fiber. The collaboration between Nanollose and Birla Cellulose is now focusing on increasing the production scale and amount of bacterial pulp in the fiber.
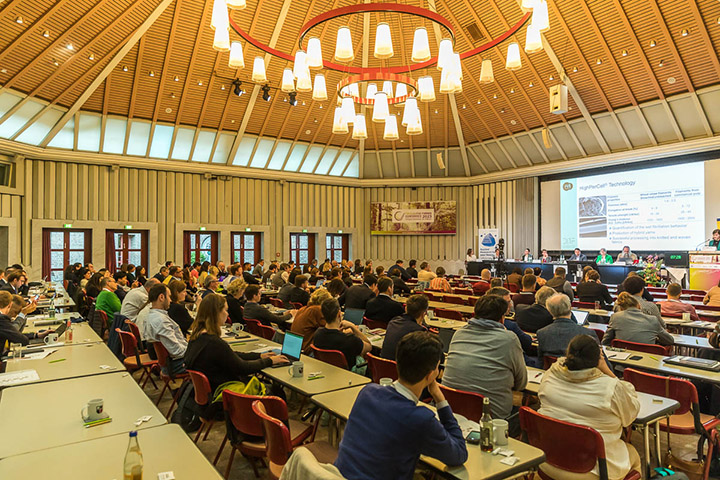
Second place in the innovation award went to Renewcell of Sweden for Circulose, a branded dissolving pulp made from 100% textile waste, such as used clothing and production scraps, which provides a material for fashion that is fully recycled, recyclable, biodegradable and of virgin-equivalent quality. Circulose can be used by fiber producers to make staple fibers or filaments such as viscose, lyocell, modal, acetate or other types of man-made cellulosic fibers.
Third place was awarded to Vybrana, a new-generation banana fiber upcycled from agricultural waste from Gencrest Bio Products, India. Raw fibers are extracted from the banana pseudo-stem at the end of the plant’s lifecycle and the biomass waste is treated by Gencrest’s Fiberzyme technology, which removes the high lignin content and other impurities and helps fiber fibrillation. The company’s proprietary cottonization process provides fine, spinnable cellulose staple fibers suitable for blending with other staple fibers and can be spun on any conventional spinning systems, explained Sandesh Saxena, head of marketing.
The other innovation award nominees were HeiQ AeoniQ, a climate-positive continuous cellulose filament yarn that reproduces the properties of polyester and polyamide yarns in a cellulosic, biodegradable and endlessly recyclable fiber; Lenzing’s Tencel Luxe lyocell yarn that offers an alternative to silk, long-staple cotton and petroleum-based synthetic filament yarns; and sustainable, plastic-free, biodegradable and compostable sanitary pads from Sparkle Innovations, USA.
Next Event
Next year’s Cellulose Fibres Conference will be held from March 13-14, 2024, again in Cologne. For further information, visit www.cellulose-fibres.eu