Seventy-five years have passed since the invention of acrylic fiber by DuPont scientists in 1941. Described as a “remarkable” fiber that is not damaged by sunlight, this fiber was claimed to have lasting resistance to mildew, high temperatures and even sulfuric acid.
Many other features have since been discovered that have increased the product interest and range of applications. Several innovation tools have been used to reinvent the product and increase its lifetime, ensuring its suitability for textiles and technical applications, as well as for carbon fiber production.
Fisipe SA has produced acrylic fiber in Portugal since 1976, and for the past four years it has been part of the SGL Group. Over the past 15 years, Fisipe has actively participated in the reinvention process of the fiber and currently has a portfolio of products that covers all these application areas.
The innovative profile that characterizes Fisipe was reinforced by its investment in two pilot lines dedicated to acrylic fiber (since 1998) and carbon fiber precursor development (since 2010).
These facilities, the internal laboratory support and a dedicated research and development (R&D) team working 24-hours a day on product and technology development, resulted in the evolution of products from 2000 onwards.
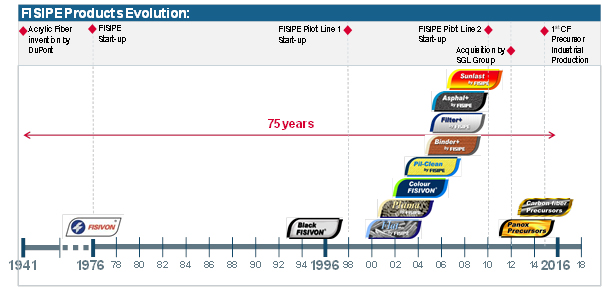
Fisipe’s innovation process involves diversified tools. These include the classical approach by introducing new physical features to the product, but also innovative marketing, applied R&D and customized production.
All these innovation tools are in line with the company’s strategy of accepting all acrylic market challenges, bridging the gap from pure commodities to complex specialties.
Partnerships with clients are a must for all R&D projects, consistent with Fisipe’s aim to be “Your Creative Partner in Acrylic Fibers.”
Innovation occurs by using the following tools alone or in combination. The resulting products thus cover different levels of complexity and innovation potential, as well as different application sectors.

Among the main ways to modify the basic acrylic fiber, Fisipe has developed expertise in the following areas:
1. Cross-section modification – rectangular, round, dog-bone and kidney-shaped. In theory, all shapes are possible as long as perfect control of coagulation conditions and spinneret design is achieved. Fisipe has reached a high level in the perfection of the fiber cross-section. This feature, combined with color, provides the best artificial fur (flat fiber) or the smoothest fiber for hand knitting (Pluma fiber).
2. Structure modification – filament compactness is a crucial feature for carbon fiber precursor. A highly porous structure can be fibrillated, producing a very high specific-area fiber adequate for friction materials. Between these extreme cases, a very low-pilling fiber (low-pill fiber) was developed, which has proved popular for uniform and work garments, as well as children’s clothing.
3. Dope injection – as DuPont announced, acrylic fiber excels in sunlight resistance. This feature, combined with the right pigment injection in the dope, provides the best fiber for outdoor fabrics (Sunlast fiber). Many materials, as long as they are finely dispersible in the right solvent system, can be incorporated in the fiber filaments to modify its properties.
4. Color by gel-dyeing – gel-dyeing along the extrusion line is the most eco-efficient way to introduce color in the fiber (Colour Fisivon). Fisipe offers a fast color-matching service to ensure clients’ exclusive colors.
5. Finishing materials – prior to the drying section, while applying the finish oil, extra smoothness, fiber chemical modification or other features such as water repellence can be achieved. This is an easy and important way to modify the fiber and is used extensively at Fisipe.
6. High-tenacity fibers – tensile properties, especially tenacity, are critical for reinforcement applications, as well as for carbon fiber precursors. As a member of the SGL Group, Fisipe has gained deeper know-how in this area following the development of carbon fiber precursors for the group. Several technical fibers used in civil construction for asphalt reinforcement (Asphalt+), as well as mortar or cement (Binder+), are promising Fisipe products that have been recently developed.
7. Heat treatment – by oxidizing the right acrylic precursors, flame retardant properties can be added to a fiber that still performs as a textile material. SGL Group offers this material (Panox) that is used for fire protection garments or aircraft brakes. A more complete heat treatment including oxidation and carbonization of a special acrylic precursor can be used to produce another acrylic-based product – carbon fiber. A wide range of carbon fibers is also available through the SGL Group (Sigrafil).
8. Marketing and customization – innovative marketing using the right brand association can be a powerful tool to innovate and create new products and business opportunities. An example is the CR7 luxury blanket produced in the USA with fibers currently sourced exclusively from Fisipe in Portugal, the home of professional footballer Cristiano Ronaldo, who plays for Spanish club Real Madrid.
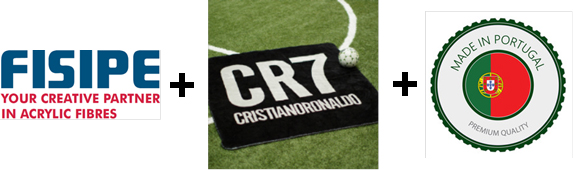
The applied R&D creates complicity and strong relationships with clients that are the basis for another important innovative tool: customized production. Acting at three product levels – commodities, specialties and customized products – Fisipe has an offer that covers the whole acrylic market (Figure 4).

Several products have resulted from this customized approach. DuPont´s scientists never imagined that acrylic fiber would be suitable for tennis balls production, but Fisipe’s clients challenged us.
Fisipe believes this is the way to reinvent the acrylic fiber and ensure a never-ending life story.
Product eco-friendliness is another challenge that also needs an innovative approach. In spite of acrylic fiber being clean to produce, respecting the environment and freeing critical natural resources, such as land and water used for growing food or biofuels, the numerous eco-friendliness challenges can only be taken with strong R&D. There is a lot still to be done.