Over the past century, man has truly harnessed the power of artificial polymer materials; polymeric fiber materials have allowed for applications not possible with the use of natural fibers.
Driven by cost, ease of processing and variety of applications, the use of synthetic polymer fibers has expanded to all corners of life. However, these polymers are primarily derived from petroleum feedstocks – a finite resource. Additionally, while these polymers are incredibly robust, they present a problem at end-of-life.
Japanese biotechnology company Spiber is now seeking to harness the power of modern biotechnology to create industrial materials that can fit into a modern circular economy.
Protein polymers
Nature has been using protein polymers as functional and structural material for eons. Natural protein fibers like keratin (i.e. wool) and silk have been used by humans for millennia.
However, natural proteins only represent a subset of potential polymeric materials that can be made from the amino acid building blocks of proteins. Spiber is taking inspiration from nature and developing new protein polymers to meet market needs.
Founded in 2007, Spiber has been developing a “full-stack” protein design-and-production platform that enables us to start with an idea and make polymeric protein materials.
We take inspiration from natural protein materials, such as spider silk, and design the polymer from the genetic level. Then, we use microbes to ferment, or brew, our raw polymeric material. We refine and process the raw polymer into materials such as fibers or plastics (Figure 1).

Brewed Protein* materials, a proprietary product developed by Spiber, are made from structural proteins produced by microbial fermentation. Spiber’s Brewed Protein polymer composition can be changed at the molecular level. We tune the properties at the chemical and processing level to make materials for the designed use.
To make fibers, we have developed and adapted industrial solution-spinning techniques for Brewed Protein (Figure 2, left). We are able to tune fiber and yarn properties by changing the process parameters, as well as the chemical composition of the polymer itself. Our filament yarns can then be processed using standard textile machinery into staple fibers, spun yarns, knit and woven fabrics.
Focus on apparel & automotive
Spiber is currently focusing on using Brewed Protein within the automotive and apparel sectors.
Working with partners such as Kojima Press, a Tier 1 supplier for Toyota, we have demonstrated high-performance materials, such as sheet molding composite (SMC) fiber composites for automotive applications (Figure 2, right). We have also worked closely with Goldwin to develop fibers and yarns that can be used in the apparel sector.
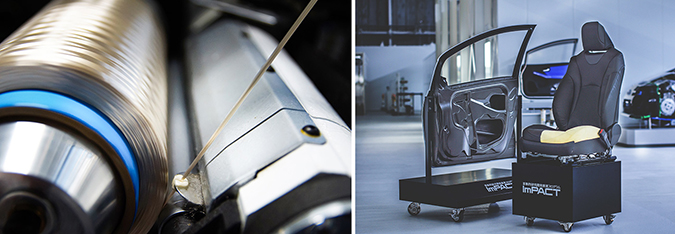
In the automotive sector, lighter components allow for higher efficiency of the vehicle; the material performance must be retained. For apparel, replacing synthetic polymers with natural polymers, while retaining properties, can address end-of-life concerns of textiles, especially in the fast-fashion market.
Brewed Protein materials can be adapted to meet the different material requirements of both automotive and apparel.
In collaboration with Goldwin, Spiber has released two items containing Brewed Protein under The North Face brand in Japan. The Planetary Equilibrium t-shirt (Figure 3, left) is made from cotton/Brewed Protein blended spun yarn that seeks to represent the balance of the biodiversity found on earth.

The Moon Parka (Figure 3, right) is an outdoor apparel jacket. The shell is a 100% Brewed Protein woven fabric, which is paired with a waterproof laminate and Clean Down, a special down product manufactured by Kawada Feather.
To address the divergent demands of different applications, Spiber uses fibers with two different Brewed Protein compositions. The fabric of a t-shirt comes into contact with your skin and should provide a soft comfortable feeling, whereas an outdoor jacket should be weather-resistant and protective to the user.
For the t-shirt, we chose a Brewed Protein fiber to complement the high-quality cotton with which it is blended. This yields a yarn that allows for a heavy fabric construction with a smooth, soft feeling.
For the Moon Parka, we designed a hydrophobic protein polymer that, after spinning and weaving, has met Goldwin’s strict quality standards for shell material. As a result, the Moon Parka is suitable for outdoor activities during winter, as well as on the streets of Tokyo.
In addition to our work with Goldwin, we also collaborate with Japanese couture fashion designer Yuima Nakazato. Natural spider silk undergoes a process called “super-contraction” (shrinkage of up to 50%) in water.
While we design this property out of most of our protein fibers, Nakazato saw an opportunity: he harnessed super-contraction to create three-dimensional garment designs from a Brewed Protein yarn by a process he dubbed “biosmocking”.
Nakazato has refined the biosmocking technique through the course of two couture shows at Paris Fashion Week (see featured image), where the versatility in fabric construction and dye color can be observed. Many of the accessories here are also made from Brewed Protein materials.
Brewed Protein materials are bio-derived, bio-based protein polymers with the potential for biodegradability. By utilizing renewable sources for our primary feedstock we can address some of the sustainability issues surrounding traditional polymeric material.
Addressing end-of-life concerns
Our Brewed Protein materials can also address end-of-life concerns. Preliminary biodegradation testing has shown positive results for our raw material in multiple environments. As the properties of Brewed Protein materials can be customized to suit specific applications, there is potential for the biodegradability of our materials to be modified in the future.
Spiber is now tackling the two largest challenges for industrial adoption of protein polymer materials – cost and scale. Currently, we are limited by the scale of raw material production.
In mid-2019, Spiber broke ground on its first Brewed Protein production plant in Thailand. When this plant comes online, we will be able to produce hundreds of tonnes annually.
At Spiber, we have now shown that designed protein polymer materials are an industrially viable materials solution. We continue to iterate on our process, taking inspiration from nature and designing in functionality to deliver industrially relevant protein polymer materials for use across industries.
* Brewed Protein is a trademark of Spiber Inc.