Techtextil North America 2024 Offered Insights on Innovations, Challenges and Opportunities within the Industry
Techtextil North America 2024 (TTNA), August 20-22 in Raleigh, North Carolina included a full slate of symposium and “on-the-floor” tech talks. The nonwoven portion was led by Dr. Raoul Farer of the Nonwovens Institute at North Carolina State University. Raoul presented snapshots of the growth nonwovens have experienced in all geographies and highlighted areas in which nonwoven fabrics have and continue to displace conventional woven textiles. It has been noted that in transportation applications, parts made with nonwoven fabrics and/or nonwoven-based composites are displacing heavier injection molded plastic parts (which previously displace metal parts in many cases).
Dr. Behnam Pourdeyhimi provided an overview of sustainability solutions within nonwovens with particular focus on nonwovens produced from polylactic acid (PLA). PLA is gaining traction as a sustainable raw material as availability increases, prices decrease, and more alternatives for blending with other polymer are identified. Polylactic acid that is both bio-sourced and potentially biodegradable making it a well established leading sustainable raw material.
In addition to the talks provided by the Nonwoven Institute faculty, a number of graduate students also presented their research, including Dominic Garcia who discussed thermal bonding of polyester
fibers in nonwovens and the impact of processing aids on bond integrity. From the Wilson College of Textiles, Nur Mazumder explored the quantification of potential PFAS exposure in firefighter turnout gear by layer. A key insight was the need to consider which layers of the protective garb present an enduring risk over many uses rather than simply quantifying PFAS content “fresh out of the box.”
In some cases, such as the thermal liner nonwoven, the layer is contaminated with PFAS during manufacturing, but this is mitigated after the first washing of the garment. Feyi Adenkunle demonstrated how yarn pullout tests, normally used to quantity fiber-to-fiber drag friction can be adapted to measure and predict adhesive laminate failures. Muneeb Tahir shared work in which PLA fibers can be made even more sustainable with the inclusion of micronized soy hulls. These materials provide some level of reinforcement to the PLA fibers as they resemble “micro-soy logs” in the PLA fiber matrix. Additionally, their presence may accelerate biodegradation of the PLA fibers.
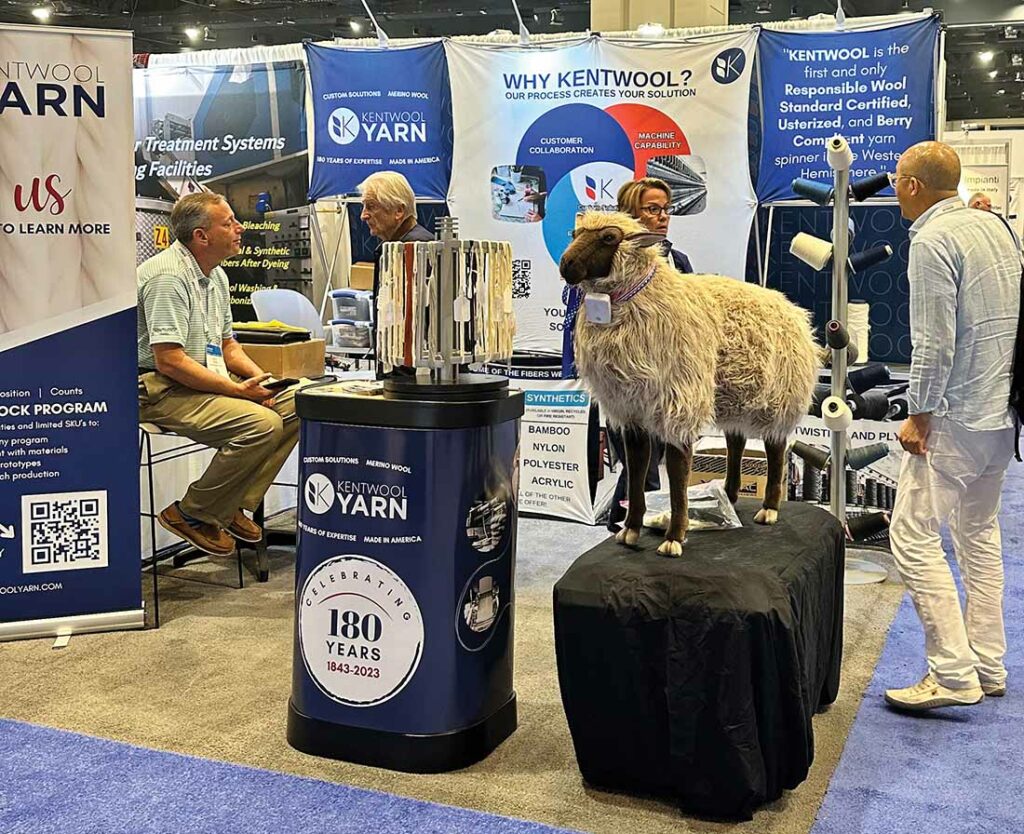
The final student presentation looked beyond raw materials and considered how processing of textile fibers and yarns could be more sustainable. Michele Schmidt presented work in which polyester was dyed using supercritical carbon dioxide rather than water-based carriers. While acknowledging that the cost of using supercritical carbon dioxide that has characteristic of both liquids and gases is higher than that of water is was seen that color-fastness of the resultant fabrics was improved. This is in addition to obviating the need for water (up to seven gallons of water per t-shirt!).
Industrial Takes on Sustainability
Switching from academic to industrial innovations in sustainability, there was a particularly exciting presentation from Beth Esponnette of Un-Spun and Julie Rader of Walmart. They discussed a joint project to 3D spin apparel items in an approach that, while not quite “on-demand,” could enable local manufacture and greatly shorten the supply chain and inventory loads. It was noted that in addition to significant trim scrap in apparel manufacture, nearly 30% of apparel produced was not sold via primary markets and/or was scrapped.
The 3D spun apparel would nearly eliminate the trim waste in garment production. Enabling localized production would collapse long logistic channels, eliminating cost and environmental impacts.
Finally, by collapsing logistics and enhancing response time to market demand, apparel waste can be reduced as what’s produced will better reflect current consumer desires. While fashionable prototypes were worn throughout the week at TTNA by Beth Esponnette, it is acknowledged that there are still challenges in scale-up of the technology, ensuring yarn supply, and unlocking finishing steps.
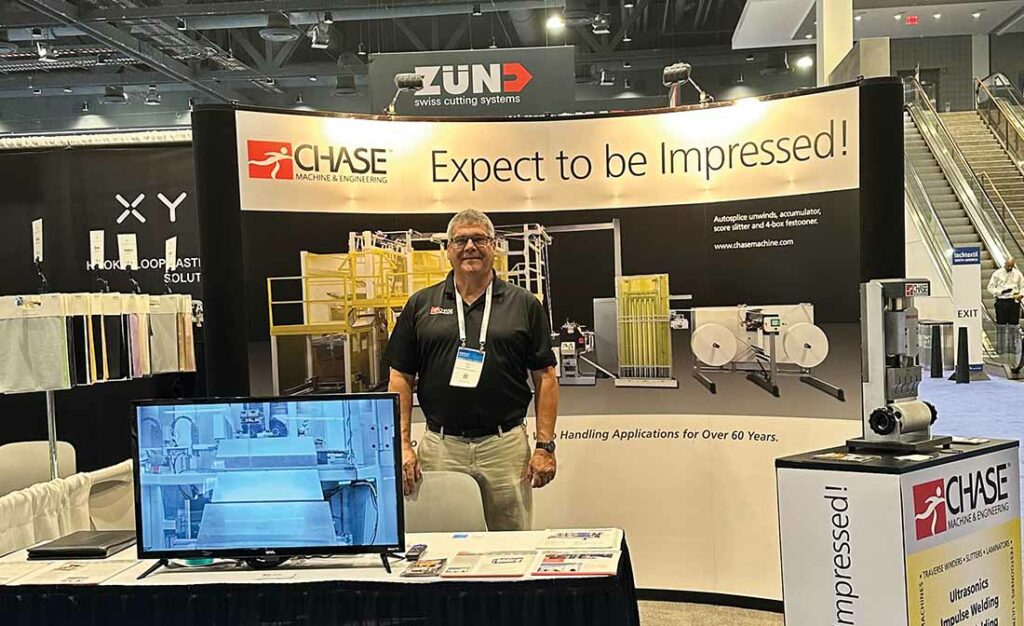
In addition to considering how to reduce apparel textile waste on the front-end, Professor Karen Leonas discussed the case and challenges of driving circularity in post-consumer textile recycling. Amongst the challenges she noted were consumer education about apparel recycling, apparel textile fiber mix, unknown composition of minor fiber components, inconsistencies in “waste” apparel supply, variable market pull, and an overall lack of infrastructure. Noting that this remains a classic chicken-or-the-egg debate of whether infrastructure is needed before full-scale recycle can begin, she provided examples of apparel textile EPR legislation from California, Massachusetts, New York and the European Union that will begin to force the issue by requiring that apparel textiles are not landfilled. For greater insight into the EU efforts, she provided excerpts from one her student’s (Caitlin Jones) research that categorized each EU nation’s readiness to meet the 2025 target dates of the 2022 EU Strategy for Sustainable and Circular Textiles. Professor Leonas also discussed technology improvements in artificial intelligence, near infrared fiber classification, and digital ID/product passports that are making the sorting of apparel waste easier and more reliable.
A greater emphasis is needed on including circularity considerations into the initial product designs to avoid unnecessary complications as fibers are reclaimed and reused. Both policy and educational efforts are needed to drive public awareness of circularity.
Also, on the topic of circularity, Xochil Herrera Scheer of The Chicago Pattern Maker led a lively panel discussion on Real World Circularity with Sean Su Circ Inc., Shane O’Toole of Origin Materials, and Bob Carswell of Material Return. Starting with the sometimes-loaded question of what does sustainability mean, each panelist gave their take and noted that circularity rarely equates with “zero waste” or “zero carbon emissions.” In the best-case scenario, there is still working loss that will occur.
Furthermore, when considering use of recycled fibers, occasionally there will be a need to augment with virgin materials. Some parties may use these arguments to imply that circularity is impractical or a failed recycling approach, while more pragmatic environmentalists will recognize the need for progress over perfection. Each participant noted two important considerations for companies entering the “circular economy” space – first, new entrants need to find some quick wins to establish credibility, even if those wins are not the endgame goal of the technology, and second, it’s important to be cognizant to avoid taking sustainable materials and making an unsustainable end-product.
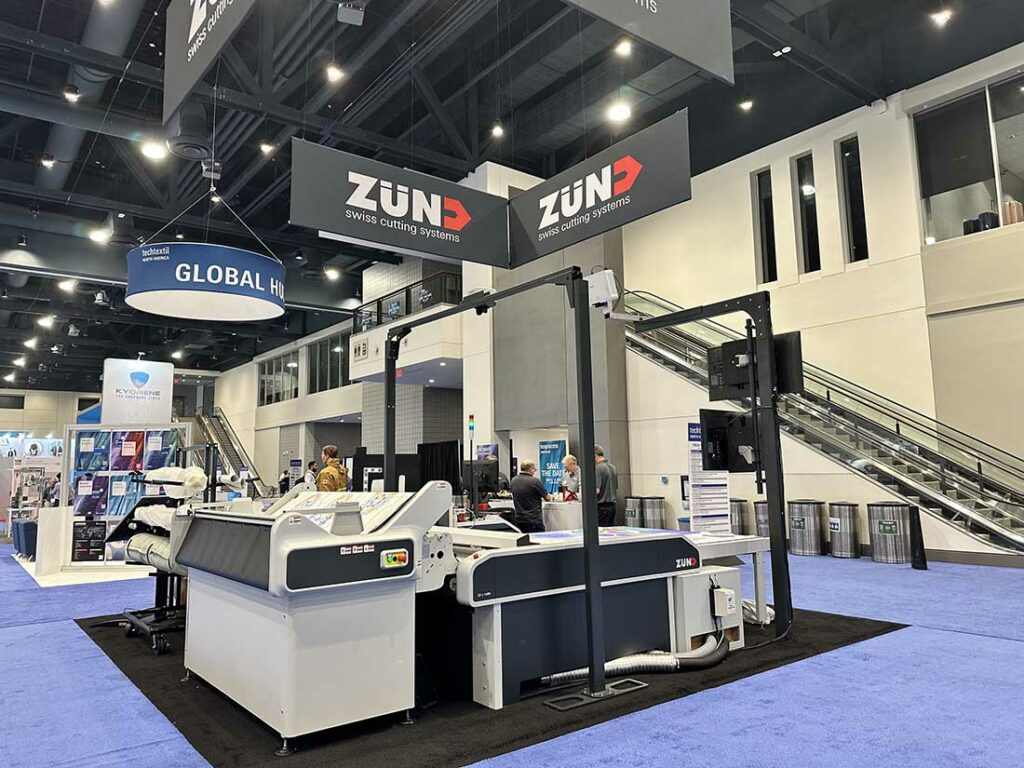
While the primary focus of their efforts is around the fibers, it’s critical to not lose sight of treatments, colorants, sizings, and other additives that may be included with recycled fibers. A greater emphasis is needed on including circularity considerations into the initial product designs to avoid unnecessary complications as fibers are reclaimed and reused. Both policy and educational efforts are needed to drive public awareness of circularity.
Functional Fabrics
Another panel session, Smart Threads and Healing Fibers, explored the topic of functional fibers, textiles, and fabrics. Jordan Schindler of Clothing 2.0, Jeff Margules of Norton Rose Fulbright US LLP, and Samantha Shintay of Hohenstein Institute explored the opportunities and challenges of using fibers and fabrics to deliver therapeutic solutions to the user. Selling of textiles with drug claims will generally require FDA approval, even if the drug is already FDA approved. This is due to the concept that “old drugs” with new carriers, e.g., fibers, become “new drugs” in the eyes of the FDA. Such materials will also require drug facts labelling. On the other hand dietary supplements that do not claim disease treating attributes are not FDA regulated. However, the FTC monitors advertising of health products to avoid claim that are untrue, misleading, or unsubstantiated.
Samantha Shintay detailed many of the claim verification testing protocols that Hohenstein is involved with including but not limited to biocompatibility, cytotoxicity, skin irritation, chemical irritation, total digestion of fabrics to determine presence of various substances (e.g. heavy metals). It was suggested that for companies exploring the functional fabric space, that socks are often a good starting point since they are not likely to be in contact with membranes that may require more rigorous verifications. Finally, it was noted that when designing such materials, that end-of-life considerations become more important. For instance, how efficacious is the product after 25 washings and will the product require a regulated disposal channel or can it be disposed of in a manner typical to conventional apparel textiles?
A final panel session explored the challenges of providing textile PPE solutions for women in the workplace. Melissa Dixon of National Safety Apparel, Professor Cassandra Kwon of the Wilson College of Textiles at NCSU, and Kelly Franko of Seraphina Safety Apparel participated.
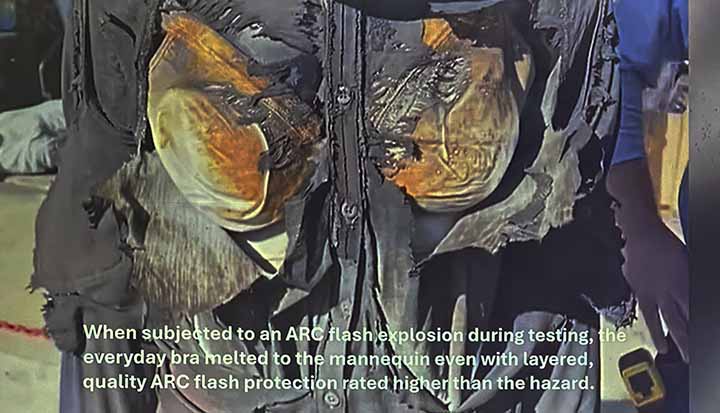
While sizing and availability are perhaps more commonly known challenges, it was revealing to learn that in some cases of high visibility PPE apparel, that there are minimum requirements for the area of reflective or otherwise highly visible fabric in the garment. This may result in PPE for persons of smaller frame being larger and/or more cumbersome than necessary, to the point of potentially impeding the person from performing their task safely.
Similarly, diversity in shape and more complex body shapes may require more sophisticated seaming to ensure the fit necessary for proper PPE performance. It was alarming to hear that less than 30% of female firefighters believed that their turnout gear fit well. Due to smaller order volumes, overseas producers are less willing to produce properly fitting PPE for women which has cost implications but also creates opportunities for domestic semi-custom production.
Overall, the various areas of innovation were exciting to learn about. A common theme throughout was the need for regulators and legislators to keep pace with changing market needs and the technical advances addressing those new needs. It was also clearly stated by many of the speakers and panelists that to meet the challenges, whether related to sustainability, trade, or ESG issues, a collaborative approach, entailing all elements of the value chain, was needed to ensure success in a timely manner.