NatureWorks, Nonwovens Institute collaboration produces an innovative new filter media
As the world faces a critical shortage of personal protective equipment (PPE) for medical workers confronting the COVID-19 pandemic, a long-standing partnership between NatureWorks and the Nonwovens Institute (NWI) at North Carolina State University (NC State) has resulted in a new spunbond nonwoven technology that will enable faster production of highly breathable, reusable surgical masks and respirators.
Why the shortage?
From a supply-chain perspective, the pandemic has challenged the availability of critical nonwoven materials that are employed for end-uses related to the COVID-19 response.
According to Brad Kalil, director of market intelligence and economic insight at INDA, Association for the Nonwoven Fabrics Industry, nonwoven material, being light in weight, tends to stay where it is produced, and as the demand for nonwovens increases, capacity investments are made in the areas where they are consumed. For example, in a 4.8 million tonne U.S. market, the net trade difference is negative 67,000 tonnes. Similarly, with goods made mostly of nonwoven material. An exception to this is “Nonwoven Medical Apparel” (HTS Code 6210.10.50), as it involves the labor of sewing. It is estimated 85% of the commodity nonwoven medical apparel used in the U.S. is produced abroad.
China’s share of these imports was 80%, and Asia’s share was 92% in 2019. There is not a specific HTS code for respirators and facemasks, but the Department of Health and Human Services estimate 95% of surgical masks and 70% of tighter-fitting respirators, such as N95 masks, are made outside the U.S.
So, Kalil notes, the exception to the “nonwovens stay where produced” concept is nonwoven medical apparel and medical facemasks/respirators. And this is why the U.S. and Europe have been challenged with material shortages during the pandemic, as the pipeline of finished goods from China and Taiwan was cut off in January, essentially breaking the supply chain and triggering an immediate need for these items.
A new spunbond nonwoven structure
Typical N95 respirators and surgical masks are a multi-layer structure of one or two spunbond nonwoven layers that provide mask shape and protect the inner filtration layer. Those layers are generally combined with an electrostatically charged layer of meltblown nonwoven material which serves as the filtration layer capturing microscopic unwanted particles, such as viruses and bacteria. The charge is what boosts the meltblown’s filtering capabilities, but it also means that the masks cannot be reused since the charge can be lost during the cleaning process, and the meltblown structures are generally too fragile and can be damaged.
In response to the COVID-19 crisis, NWI was able to modify microfibrillation technology it had previously developed to form a new class of facemask filter medium with an ultra-low pressure drop. This new structure does not require electrostatic corona charging and can be reused and re-sterilized.
In response to the COVID-19 crisis, NWI was able to modify microfibrillation technology it had previously developed to form a new class of facemask filter medium with an ultra-low pressure drop. This new structure does not require electrostatic corona charging and can be reused and re-sterilized. It is also strong enough to be cut and sewn, or automatically converted into masks and respirators.
There are no spunbond filters, as filtration media with similar properties and meltblown structures do not provide the same pressure drops. The material can be fine-tuned to produce facemask media targeting N95, N99, and N100 masks, as well as MERV 13 to 16 and HEPA.
NWI’s new approach uses spunbond nonwovens made from a bicomponent PLA and polypropylene (PP) fiber to create a filtration media with the right efficiency at low pressure drop and high throughput.
The process uses novel jet strips that form a “quilted” structure. The degree of fibrillation can be controlled; partial fibrillation will result in a mix of fibers ~ (1-2 µm) and coarse fibers (15-25 µm), while full fibrillation results in a structure with fibers in the range of 1-2 µm.
The procedure employed the basic particle filtration process described in NIOSH Standard Test Protocol (STP) 0059. This STP describes the test method for the determination of particulate filter efficiency level for N95 series filters against solid particulates for non-powered, air-purifying respirators. The testing protocol meets the requirements of the United States 42 CFR part 84 standard.
A TSI model 8130 automated filter tester was used to determine the results. The instrument was calibrated per the STP and the procedures for loading per the requirements of the United States 42 CFR part 84 standard. The loading test involves subjecting the mask to up to 200 mg of salt particles at a flow rate of 85 L/min. The loading behavior of the first 3 samples determines how the remaining 17 samples are tested (Figure 1).

In the case of Type 1 and Type 2, the remaining 17 samples only are measured for their initial efficiency (since the efficiency never drops), while for the Type 3 and 4, the full loading is performed and the maximum penetration of minimum efficiency is determined.
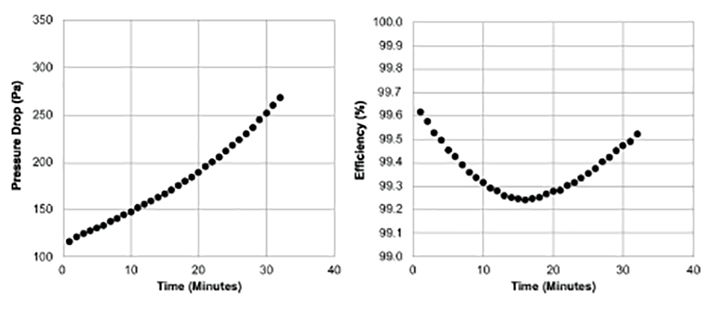
For the sample of 20 filters or filter cartridges to demonstrate acceptable performance, each filter must meet or exceed the specific collection efficiency limit (≥95% for N95, ≥99% for N99, and ≥99.97% for N100).
The loading behavior of a leading commercial N95 respirator is shown in Figure 2. This respirator is Type 3 and the minimum efficiency is 99.25%.
In a two layer duckbill design mask (sample masks were produced at Spoolex, France), testing shows that the pressure drop in the new masks that reach N95 efficiency rates is lower than a leading commercial N95 respirator. This is mainly due to the structure of the spunbond medium used while the larger size of the duckbill design leads to a lower face velocity and therefore a lower pressure drop. Figure 3 is a typical medium sized duckbill design.
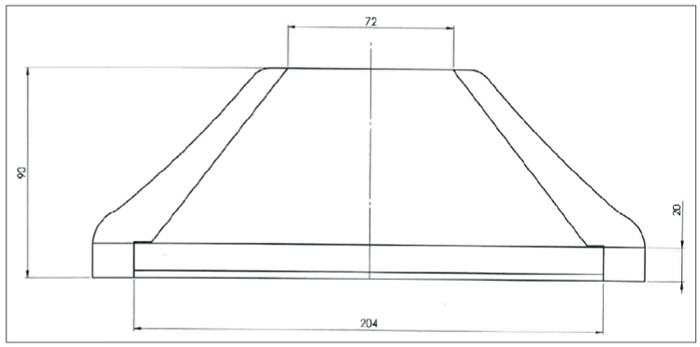
A two layer duckbill made from two layers (each 125 GSM) of the new spunbond structure behaves similarly but demonstrates a much lower pressure drop.
The spunbond combined with NWI’s meltblown (25 gsm) results in even more impressive results. The SMS (100 gsm spunbond + 25 gsm meltblown + 100 gsm spunbond) yields an amazingly superior product (Figure 5).


The role of spunbond, bicomponent fiber
The partnership between NatureWorks and the Nonwovens Institute started over 15 years ago. At the time, many companies were interested in NatureWorks’ relatively new PLA biopolymer branded Ingeo, but many struggled to process it efficiently into nonwoven materials. To overcome this hurdle, NatureWorks began a collaboration with NWI focused on basic process development for spunbond fabrics. Applications range from high-performance microfiber wipes, durable products, synthetic leather substrates, filtration and more.
Before long, the partnership was successful in defining an efficient spunbond process that provided the industry with much needed guidance for the successful processing of PLA. Over the years, the collaboration has continued with NatureWorks and NWI has continued developing fabrics based on new Ingeo biopolymer products, and NWI has leveraged its processing knowhow to develop new nonwoven solutions across a broader range of fiber and fabric configurations. As an example, the Winged fiber technology (Sanctuary Systems) uses Ingeo for the production of filters, facial masks, and specialty wipes.
During the initial development of the recommended spunbond process, it was observed that PLA in fiber melt spinning processes could be successfully spun into a fiber across a relatively broad range of conditions. Additionally, the melt processing temperatures required to process the biopolymer offered the perfect temperature range for production of bicomponent fibers with other polymers like polyolefins, polyamides, polyesters (especially polytrimethylene terephthalate – PTT and polybutylene terephthalate – PBT), TPE and TPU elastomers, PVDF and beyond.
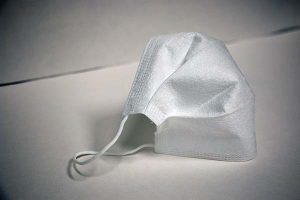
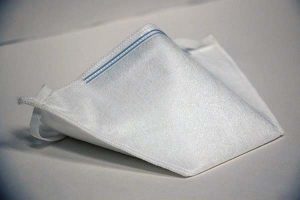
These combinations of materials proved not only to be technically feasible, but were also commercially interesting for a variety of applications – from durable apparel to battery separators, liquid filters, air filters, wipes and more – in many cases leveraging the unique properties and performance of each individual polymer.
In addition to the product possibilities offered when combining different polymers, it has been discovered that certain unique processing characteristics of these materials can be leveraged to provide specific advantages.
When polyolefins are meltspun, the production rates are generally limited by increased shear rates as more molten polymer is forced through the spinneret capillaries to form the individual fibers. As the shear rate increases, melt fracture and fiber breaks can occur forming fabric defects and effectively limiting the production rates to less than 250 kg/m/hr in modern spunbond lines. Polymers like PLA are much less sensitive to these shear rate effects and as a result can be produced at higher rates. This remains true even in combination with other polymers like polyolefins in bicomponent fibers. Production rates on spunbond lines can be increased to greater than 400 kg/m/hr when using a bicomponent structure with PLA. With over a 60% increase in productivity from a single spunbond line and given the costs of modern spunbond equipment, fabric producers can take advantage of both the economic and competitive advantages.
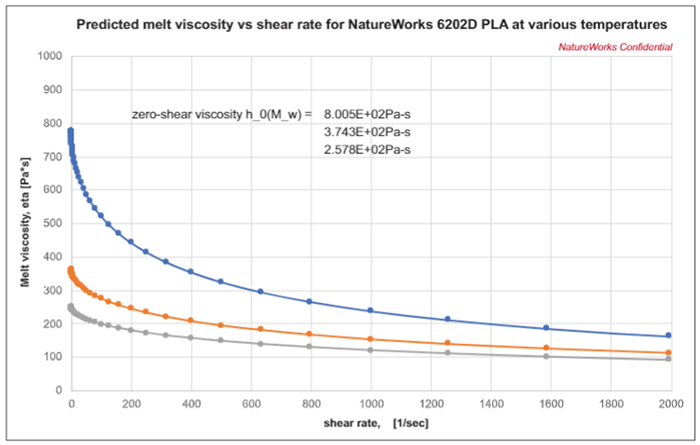
Beyond manufacturing efficiencies, the presence of both polymers in this biocomponent fiber is often necessary for creating improved performance in the final nonwoven fabrics.
Early uses of PLA in bicomponent fibers focused on dissolving PLA. The typical configuration with these initial developments was an island in the sea structure with PLA being the sacrificial sea and the islands being some other conventional polymer that would remain intact after sea polymer dissolution. This process created small fibers with high surface area useful for filtration or softness in specialty fabric applications like synthetic leathers. More recent bicomponent applications have focused on retaining both polymers and leveraging the properties of each for functional benefits.
For example, the new spunbond filter media is able to leverage the inherent stiffness of PLA so that even in small sub-micron fibers, a more three-dimensional structure can be produced. This results in significantly lower pressure drops due to improved fabric structure formation. PLA also allows pleatability of the filter media – a self-pleating filter media eliminates the need for a scrim layer resulting in lower costs. Early studies with single-component meltblown fabrics in sub-micron fibers also identified this lower pressure drop and pleatability. For filtration applications, this improved structure formation is key to providing depth filtration and the reduced pressure drop across the media.
Work carried out by Professor Gajanan Bhat (formerly University of Tennessee, now University of Georgia) demonstrates that in structures composed of similar size filaments made from PLA and PP, the PLA structure exhibits permeabilities that are much greater than those of the PP structures. This is partly due to the stiffness of PLA and also partly because of its higher density leading to a lower solid volume fraction (higher porosity) at the same weight, thickness and fiber size.
In addition to structural benefits, leveraging significant polymer property differences between combinations of materials like PLA and polyolefins can be leveraged to improve filtration. With combinations like PLA and PP, polar and non-polar polymers can be combined and advantages such as ease of separation can be used to fragment the multicomponent fibers into multiple smaller fibers. This process increases the available surface area and raises the level of filtration.
This also allows the use of a broader array of bicomponent fiber structures utilizing PP and PLA for ease of splittability in the case of segmented pie and segmented ribbon structure.
Breathability & comfort
With the COVID-19 crisis lingering on, there is a need for a better “cloth” mask. There are many examples of masks on the market made from knitted and/or woven fabrics. Such masks are not regulated, and the data reported are often misleading. Some report efficiencies without reporting pressure drop and some claim being the most breathable and capitalize on the bacteria filtration efficiency, which is ~3.0 microns. These cloth masks do not behave as respirators and have poor mechanical filtration and no electrostatic filtration. Cloth masks, when characterized by using the NIOSH testing protocol, demonstrate little or no efficiency.
For the consumer, the breathability and comfort is a critical feature. This is where the new spunbond structure can offer significant opportunities in terms of offering a much higher level of respiratory protection while offering low pressure drop.
An example is shown in Figure 7 for two layers of 100 gsm spunbond in a duckbill design measure, as per the NIOSH test procedures.

This type of structure offers significant protection at very low pressure drop, and is far superior to existing cloth masks. The initial efficiency is 95% but drops when using the loading test required by NIOSH. This loading test is a very severe test and many masks may not be loaded to the same extent during their normal use. The minimum efficiency is ~ 90%.
A similar structure with two layers of 125 gsm spunbond was shown above meeting the N95 requirement at a slightly higher pressure drop.
Additionally, these pressure drops are low enough that such masks can be worn by children – many schools are reopening and offering three-layer cotton masks that offer very little protection. Below is one example of a three-layer cotton mask tested on a TSI 8130, at 32 L/min.
Flow rate (L/min) |
Pressure Drop (Pa) |
Efficiency (%) |
|
3-layer Mask |
32 |
22.7 |
21.1 |
3-layer Mask |
85 |
75.5 |
16.5 |
The road ahead
Leveraging the new spunbond material’s production efficiencies, LINC (Leaders in Innovation and Nonwovens Commercialization), a manufacturing incubator within the NWI pilot facilities, has provided over 4.5 million square meters of media to partners across North Carolina and the U.S. This translates to over 100 million masks produced since March 2020 for front-line healthcare works and beyond.
Currently, NWI has significant background IP and two new patents are pending on this new technology. In the future, NWI plans to license this technology to global nowovens manufacturers to further scale up the industry’s ability to meet the demand for PPE and beyond. The current structure has many other uses, such as durable microfiber wipes, HVAC filters, etc.
From a sustainability perspective, using a biobased component like PLA reduces the carbon impact of these masks, but there is rightfully concern around the waste that is generated from the increase in single-use masks.
There has been interest in developing and even some prototypes of compostable masks. However, industrial composter systems have no desire to accept a product that doesn’t help divert more yard and food waste, the primary contributors to quality compost, into their systems. By creating a mask that can be reused safely, this new biocomponent spunbond structure has the potential to reduce the number of single-use surgical masks in use.