While the spunlace machine is the key piece of equipment in spunlace nonwoven production, jet strip washing machines are one of the crucial auxiliary items to safeguard the outstanding performance of the spunlace machine. The jet strip, inserted inside the water jet head, produces a high-pressure water needle, which has a significant impact on the quality of spunlaced fabric.
The water needle comes out from the tiny holes evenly arranged on the jet strip, with diameters ranging from 0.12-0.3mm. Impurities and minerals in the water can block the holes and lead to defected fabric. Thus, there is a need for a jet strip washing machine, which is efficient and convenient in doing the routine work of cleaning the jet strip.
1. Requirement for jet strip cleaning machine and its principles
Traditionally the jet strip washing machine is based on the ultrasonic technique. Ultrasonics produce a cavitation and acceleration effect, which generates vibration and impact to remove impurities.
Considering practical production, the jet strip would be cleaned in every 6- 8 hours via the ultrasonic method. Frequent cleaning will cause the jet strip to be repeatedly subjected to the instantaneous high pressure generated by the ultrasonic wave, causing damage to the fine holes of the jet strip, and small cracks in the hole wall, which affects the quality of the water needle and makes the cleaning process more difficult. When the jet strip is clogged, there will be dense stripes and fluff on the fabric surface, which has a negative impact on the quality of the fabric surface. Therefore, the market calls for a new type of jet strip cleaning device, which is simple to operate and does not damage the jet strip substrate.
When the jet strip is clogged, there will be dense stripes and fluff on the fabric surface, which seriously affects the quality of the fabric surface. Therefore, the market calls for a new type of jet strip cleaning device, which is simple to operate and does not damage the jet strip substrate.
2. Principle of the new jet strip cleaning machine
The functional principle of the new jet strip cleaning machine includes two parts: One is the chemical cleaning effect – the jet strip is chemically immersed in the immersion tank. The immersion liquid can remove various substances that block the jet strip, including fiber debris, microorganisms and their slime, oil, and scale, sediment, dust and other substances in the water system. At the same time, the immersion liquid of a specific formula will not cause corrosion to the water needle board itself and damage the water needle board. The second is the physical cleaning effect – the hard dirt on the surface of the jet strip is cleaned by a high-pressure water jet. The impact and shear force generated by the high-pressure water jet crushes and separates the dirt. The changes of physical nature of the water jet itself during the working process will also enhance the cleaning effect. Working pressure in the process of cleaning is very important. It is necessary to be able to clean the dirt on the surface of the jet strip without damaging the substrate, but also to consider the effect of the cleaning pressure on the jet characteristics. Therefore, this type of jet strip cleaning machine chooses a stable water flow of 20MPa as the working water flow in the physical cleaning process.
3. Structure and operation of new type jet strip cleaning machine
3.1. Structure and operation of chemical immersion tank
The chemical immersion tank is of long-slot structure (Figure 1), which includes a tank body for containing the immersion liquid, a control box located at one end of the tank, a temperature controller installed in the control box, and an electric heating tube in the tank. The tank is used to store the immersion liquid containing the chemical agent. The control box, thermostat and heating tube are used to heat the immersion liquid so that the immersion liquid maintains a constant temperature during application, so as to achieve a better immersion effect.
The operation procedure is: prepare the chemical immersion liquid in the chemical immersion tank; switch on the heating tube in the control box and adjust the temperature of the immersion liquid with a thermostat (60 C ~ 80 C); put the jet strip in the solution for about one hour; and then initiate the next physical cleaning.
In the process of chemical immersion, the immersion liquid is very important, which directly affects the cleaning effect. The formulas for preparing chemical immersion liquid are relatively diverse. For the purposes of this article, we will employ a simple and easy-to-use formula: 10% -15% solution of ammonium chloride, ammonia and EDTA (ethylenediamine tetraacetic acid) as a cleaning solution. In order to maintain a good cleaning effect, the cleaning fluid needs to be changed once a week.
3.2. Structure and operation of high-pressure water cleaning platform
The high-pressure water cleaning platform is shown in Figure 2 and Figure 3. The working platform of the cleaning platform is fitted with a drive guide wheel at the inlet that controls the linear movement of the jet strip. Inside the platform, there is cleaning chamber with a high-pressure water nozzle. Then there is the first blowing port, guide wheel at the outlet, the second blowing port and the light inspection hole. The high-pressure water nozzle inside the cleaning chamber is connected to the high-pressure pump positioned below. The air compressor is connected to the first blowing port and the second blowing port through the pipeline.
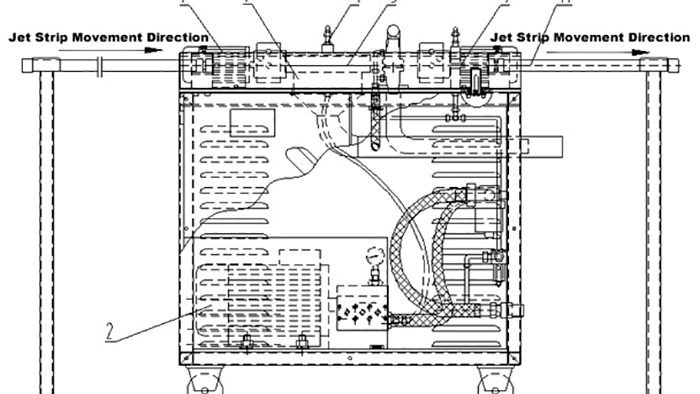
The operation procedure of the jet strip cleaning machine is: put the immersed jet strip into the inlet bracket of the high-pressure water cleaning platform, and then start the high-pressure pump and the motor. After the normal operation, the guide wheel takes the strip to the cleaning chamber. It is dispersed into a fine high-pressure water needle, which works on the clogged jet strip. At the same time, the impurities are carried away by the water flow. The sewage is recovered by the recovery pipeline and discharged out of the machine.
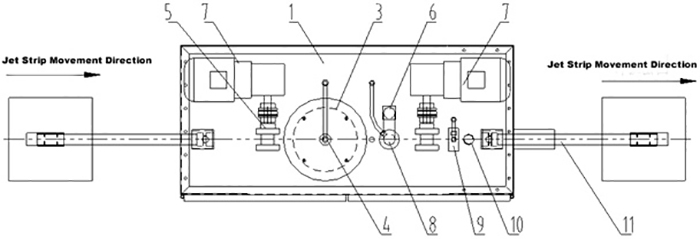
9-Second blow port 10-Light inspection hole 11-Storage tube
After the high-pressure water cleaning, the jet strip enters the first blow port for preliminary drying, and the residual water on the surface of the jet strip will be taken away by compressed air and then comes to the second blow port for further drying. Then the strip enters into the light inspection where the operator can use the light to observe whether the pinhole is cleaned and whether it needs to be cleaned again. The entire physical cleaning process avoids the operator’s direct contact with the cleaning process of the jet strip, prevents the jet strip from being contaminated by operators, and achieves the best cleaning effect. The entire process can be maintained at a speed of 1.5m/min. Take the 3.5m jet strip as an example, the cleaning process takes only three minutes, achieving the purpose of rapid cleaning.
Hi-tech Heavy Industry Co., Ltd.’s new type jet strip cleaning machine is simpler to operate without damaging the substrate. At the same time, it can achieve a good cleaning effect through the dual functions of chemical cleaning and physical cleaning, thus ensuring the quality of the spunlaced products. In addition, the new jet strip cleaning machine has a simple manufacturing structure, convenient to use, with spare parts easily accessible on the market. According to market feedback, customers are generally satisfied with the effect of this cleaning machine.
For more information, please contact dongl@zzfj.com.