With the coronavirus (COVID-19) spreading worldwide, International Fiber Journal is tracking stories relevant to the textile fiber industry. Facemasks, personal protective equipment, medical supplies and wipes are among the fiber-intensive technologies particularly relevant to the COVID-19 response effort. And as manufacturers of these technologies and others struggle to meet global demand in the face of the growing COVID-19 pandemic, news stories are breaking quickly. Here we will post relevant news stories on an ongoing basis. Please check back for regular updates. If you have news that you feel should be added to this summary report, please email it to Matt Migliore at mmigliore@inda.media.
Most recent update: January 19, 2022
Texas Tech researchers author study using new standardized mask filtration testing to evaluate effectiveness of alternative facial coverings
Seshadri Ramkumar, a professor of chemical countermeasures and advanced materials in Texas Tech University’s Department of Environmental Toxicology, has co-authored a study utilizing standardized methods to evaluate common household fabrics as alternative materials for barrier face coverings. Olukayode James Ayodeji, a Ph.D. candidate in the Department of Environmental Toxicology, conducted the standardized tests measuring the filtration efficiency (FE) of different facial coverings.
Using mask filtration testing standards developed by the American Society for Testing and Materials (ASTM), Ramkumar and his team compared the performance of popular ready-made facial coverings, such as bandanas and neck gaiters, to alternative household materials including denim, cotton shirts, bedding and towels. Both categories of materials were measured against R95 masks, which offer the highest level of protection against viral particles.
While a material’s ability to filter out viral particles is paramount, breathability is an equally important consideration, Ramkumar said. Unfortunately, testing revealed an inverse relationship between filtration efficiency (FE) and breathability – for instance, while denim showed the highest FE, it also had the lowest breathability of all the household fabrics, rendering it unsuitable for facemask production. Ramkumar and his team took both parameters of FE and breathability into equal account when evaluating a material’s overall performance.
According to their study, the most effective ready-made facial coverings on the market are Velcro masks with carbon filters and surgical masks, while the least effective are fashion facemasks, single-layer face coverings, neck gaiters and bandanas.
The highest-performing household materials were thick cotton shirts and towels, indicating that multi-layered cotton facial coverings with proper fit are the most effective homemade mask alternative because they offer a measure of protection against viral particles without compromising breathability.
A combinatorial approach involving both a facial covering and a surgical mask with good fit would offer the wearer better protection against particle inhalation, Ramkumar said.
Ramkumar co-authored the paper, “Particle-Size-Dependent Filtration Efficiency, Breathability, and Flow Resistance of Face Coverings and Common Household Fabrics Used for Face Masks During the COVID-19 Pandemic,” alongside Texas Tech graduate students Olukayode James Ayodeji and Terrell A. Hillard, with the support of Texas Tech graduate student Mirza Khyum. The study was published in Volume 16 of the International Journal of Environmental Research earlier this month.
Source: tiehh.ttu.edu
New research shows the interaction of water aerosol with nanofiber mesh facemask material
Facemasks made with nanofibers have drawn increasingly more attention because of their higher filtration efficiency, better comfort, and lower pressure drop. However, the interactions and consequences of the nanofibers and microwater droplets remain unclear.
New research published in the journal Physics of Fluids shows the evolution of fibers made of polymers with different contact angles, diameters, and mesh sizes under water aerosol exposure is systematically visualized. The images show that capillarity is very strong compared with the elasticity of the nanofiber. The nanofibers coalesce irreversibly during the droplet capture stage as well as the subsequent liquid evaporation stage. The fiber coalescence significantly reduces the effective fiber length for capturing aerosols. The nanofiber mesh that undergoes multiple droplet capture/evaporation cycles exhibits a fiber coalescing fraction of 40%–58%. The hydrophobic and orthogonally woven fibers can reduce the capillary forces and decrease the fiber coalescing fraction.
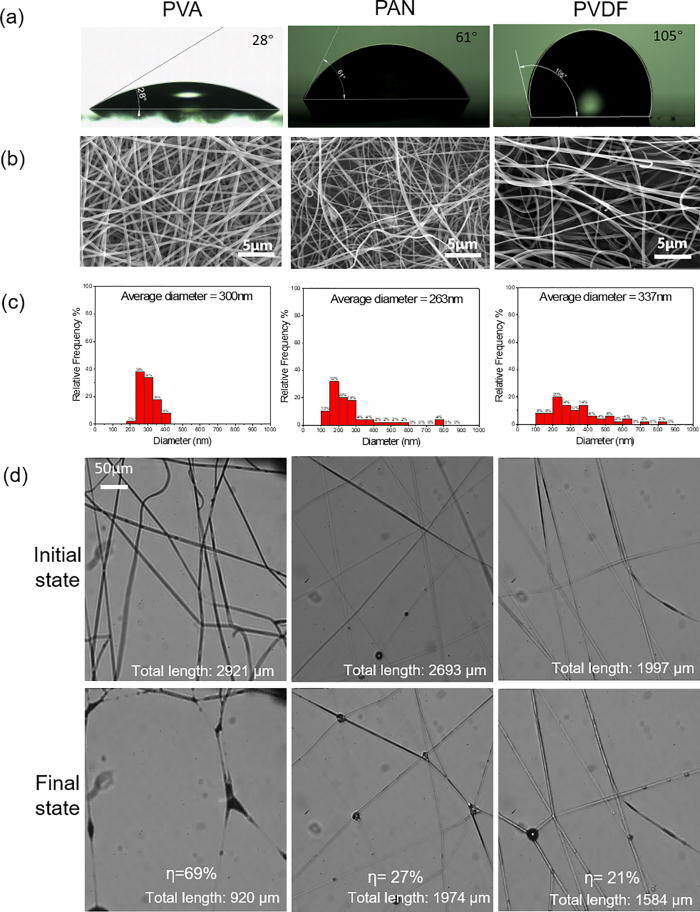
This finding is expected to assist the proper design, fabrication, and use of face masks with nanofibers. It also provides direct visual evidence on the necessity to replace face masks frequently, especially in cold environments.
Read the full story: https://aip.scitation.org/doi/full/10.1063/5.0061847 Source: https://aip.scitation.org/journal/phf
Livinguard Technology shows effectiveness against Indian Isolate of SARS COV 2 (COVID-19, wild version)
Livinguard, a developer of protective facemasks with COVID-19-deactivating properties, announced its technology has been proven effective by an independent laboratory against the Indian isolate of SARS COV 2 – Covid 19, wild version. The tests were carried out by the Indian National Institute (NII) of Immunology on Livinguard’s facemask fabric. Results indicate that each layer of the Livinguard mask has an average of > 99% effectiveness against the Indian isolate of SARS COV 2 (wild version). The principle underlying the Livinguard technology is the deactivation of microbes including bacteria and viruses*. The technology applies a positive charge at the molecular level to textile surfaces, making them more powerful than the negative charge of microbes. Therefore, microbes are deactivated when they encounter textiles treated with Livinguard Technology. Textiles treated with Livinguard Technology have also been proven to deactivate viruses, including SARS-CoV-2* (the virus that causes COVID-19) by researchers at the Free University Berlin and the University of Arizona. Furthermore, Livinguard Technology is safe for humans and the environment. Speaking about the test results, Sanjeev Swamy, Livinguard CEO, said “We are making everything possible to address the demand from the increasing number of regions that are making it mandatory to wear a mask outside and inside again. Over the past 24 months, Livinguard has been tirelessly updating its self-disinfecting technology and this is yet another example of the company rising to the challenge in a race against the clock.” The company is now focusing on pivoting its production facility to scale the delivery of its sustainable hygiene technology worldwide. Source: livinguard.com
US DoD, DHS award $6.5 M to US Cotton to boost polyester-tipped swab production
The Department of Defense (DOD), on behalf of and in coordination with the Department of Health and Human Services, awarded $6.5 million to U.S. Cotton, LLC, a subsidiary of Parkdale, Inc., to increase domestic production capacity of the polyester-tipped swabs used in COVID-19 home test kits and mass testing settings. U.S. Cotton’s COVID-19 test swab is designed for hospital and laboratory settings and, when used at home, allows for an easier self-administered test. This industrial base expansion effort will allow U.S. Cotton to increase its production capacity from 92 million polyester swab tips per month to approximately 371 million polyester swab tips per month in Cleveland, Ohio, by May 2022 to support domestic COVID-19 testing. The DOD’s Defense Assisted Acquisition Cell (DA2) led this effort in coordination with the Department of the Air Force’s Acquisition COVID-19 Task Force (DAF ACT). This effort was funded through the American Rescue Plan Act (ARPA) to enable and support domestic industrial base expansion for critical medical resources. Source: defense.gov
NCTO welcomes Senate passage of U.S. infrastructure bill, funding to bolster domestic PPE supply
The National Council of Textile Organizations (NCTO), which represents U.S. textile manufacturers from fiber through finished products, issued a statement welcoming Senate passage of a bipartisan infrastructure bill that will provide billions of dollars in new spending with the aim of revitalizing the nation’s roads, bridges and railways and help reconstitute a domestic supply chain for personal protective equipment (PPE). “We commend the Senate for passing the bipartisan infrastructure bill, which will provide critical resources for our nation’s aging infrastructure and at the same time help incentivize the reshoring of personal protective equipment (PPE) production, an important priority of the U.S. textile industry,” said NCTO president and CEO Kim Glas. NCTO worked with congressional allies to include a version of the Make PPE in America Act, legislation co-sponsored by Senator Rob Portman (R-OH) and Senator Gary Peters (D-MI), in the infrastructure legislative package. The bill ensures all PPE purchased by the Departments of Homeland Security, Health and Human Services and Veterans Affairs are Berry Amendment-compliant; guarantees long-term contracts (a minimum of two years) to U.S. manufacturers; and creates a tiered preference for PPE made in the Western Hemisphere by our free trade partners using U.S. components, after domestic manufacturing capacity has been maximized. “We sincerely thank Senator Portman and Senator Peters for working to include their Make PPE in America Act in the infrastructure bill,” Glas said. “This bill will help onshore critical production of personal protective equipment (PPE) by guaranteeing long-term contracts for domestically produced PPE and ensuring that taxpayer dollars are utilized to bolster the federal purchase of American-made PPE.” Source: ncto.org
Asahi Kasei and Nara Medical University confirm 226nm UVC LED efficacy against SARS-CoV-2
Asahi Kasei and Nara Medical University announced the results of the efficacy of 226 nm ultraviolet-C (UVC) LEDs in the inactivation of the coronavirus that caused COVID-19, and its effects on animal skin cells. The results showed that 99.9% of the virus was inactivated by both 226 nm and 270 nm UVC LEDs and there was significantly less effect on animal skin cells. In the tests, 100 of the 226 nm UVC LEDs were placed on a panel in a 10×10 array. All of the UVC LEDs were created from the proprietary aluminum nitride (AIN) substrate and pseudomorphic aluminum gallium nitric (AIGaN) technology of Crystal IS. For comparison, a similar array of 270 nm UVC LEDs were also prepared. Liquid containing viable SARS-CoV-2 was injected into a Petri dish and then dried. The panel arrays were activated at an output of 440 μW/cm² . After, the virus was collected and the amount of contagion was measured by the plaque technique. An additional experiment was conducted on mouse skin cells to estimate the damage that 226 nm UVC LED light has on animal skin compared with 270 nm light. The mouse skin cells were arranged in two layers which were then exposed to either 226 nm or 270 nm UVC LED light at a dosage of 100 mJ/cm² and 500 mJ/cm². After the exposure, the upper layer of cells was removed and the relative fraction of living cells in the bottom layer was evaluated by measuring the absorbance after applying an MTT reagent dye to the cells. The results show that the 226 nm UVC LED light had little to no effect at 100 mJ/cm² , and at 500 mJ/cm² there was less effect on the cells of the bottom layer. All experiments were conducted on the campus of Nara Medical University in Bio Safety Level 3 (BSL3) testing facilities. Airborne viruses or their effects on humans were not tested. Source: asahi-kasei.com
Everfresh from Aksa Akrilik neutralizes coronavirus by 97.48%
Aksa Akrilik announced its antimicrobial fiber product Everfresh, for products ranging from facemasks to home textiles, is capable of neutralizing coronavirus by 97.48% within 30 minutes, according to the company’s test data. Everfresh utilizes a zinc compound in the fiber with no impact on human health or skin, allowing it to be used for carpets, blankets, quilts, beddings, towels and pillows, especially in hotels, mosques and dormitories. Everfresh maintains its microbial activity and its impact against coronavirus after repeated washing.
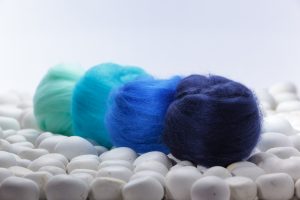
“With our new product Everfresh, we are delighted to respond to the health-sensitive needs of our society,” said Cengiz Taş, Aksa Akrilik board member and general manager. “Everfresh once again made a difference in textile products by eliminating coronavirus by 97.48 percent in half an hour. Thanks to its zinc compound, Everfresh provides antimicrobial properties to the products and reduces the need to wash the product by preventing bad odors.” Source: aska.com
Biden Administration awards contracts for up to 22.2 million US-made facemasks
The National Council of Textile Organizations (NCTO) reported that the Biden Administration has awarded two contracts to Parkdale Mills and Ferrara Manufacturing Inc., as part of President Biden’s pledge to procure millions of domestically made facemasks for community health centers, food pantries and soup kitchens across the country. North Carolina headquartered Parkdale Mills, the nation’s largest cotton yarn spinner, has partnered with Ferrara Manufacturing, a tailored clothing company based in New York City’s garment center, whose workforce is union represented by Workers United/SEIU, to manufacture over 17 million reusable masks. The government said it could purchase up to a maximum of 22.2 million masks under the two contracts. The masks will be Berry Amendment compliant, and thus 100% U.S.-made. Ferrara Manufacturing and Parkdale Mills will contract with additional U.S. companies across the manufacturing supply chain, employing nearly 5,000 American workers as a result of these awards. Parkdale will be utilizing yarn from their facilities in NC, VA, and GA and Ferrara will deploy their cut and sew operations in New York City. Source: ncto.org
HomTex receives FDA Emergency Use Authorization for Level 1 surgical masks; expects to begin production of N95 masks soon
HomTex, an Alabama-based textile manufacturer, announced it received FDA Emergency Use Authorization for its Level 1 surgical masks. HomTex manufactures three-ply disposable masks and reusable cloth masks, which it supplies to the U.S. Capitol, and it will begin production of NIOSH N95 masks in a new plant in Selma, Alabama. HomTex’s made-in-America masks are produced in facilities in Cullman and Mobile, Alabama; Tennessee; South Carolina; and North Carolina. Jerry Wooten, CEO of HomTex, said, “When I say made in America, I mean every component sourced in the US and made in the US. We believe that ramping up domestic manufacturing of PPE products is a national imperative from a safety, economic, and national security perspective, and HomTex is proud to meet that challenge.” HomTex has the capacity to produce 700 million surgical 3-ply masks and 20 million NIOSH N-95 masks annually. HomTex’s new manufacturing facility in Selma is expected to open in fall of 2021, creating 300 jobs. HomTex, Inc., a manufacturer of textile bedding products, was founded in 1987 by Jerry Wootten and is headquartered in Cullman, Alabama. Today, HomTex has a nationally recognized brand of bedding product, DreamFit and produces FDA-approved PPE masks. HomTex has over 400 employees with over a million square feet of domestic production and distribution. HomTex is a Certified Minority Business Enterprise (Certificate #SR01666 certified by the NMSDC ). Source: homtex.com
Test results show Fiber Bond VE3 chemistry inactivates 99.9% of SARS-CoV-2 in HVAC systems
Fiber Bond announced the release of its VE3 Technology, an engineered chemistry that inactivates SARS-CoV-2, according to test results. Lab testing concludes that Fiber Bond’s VE3 Technology inactivates 99.99% of the airborne SARS-CoV-2 virus within 15-minutes. The VE3 Technology is a value-added chemistry, developed in-house at Fiber Bond to help stop the spread of COVID-19 in any facility with an HVAC system. The patent-pending VE3 Technology captures and inactivates the SARS-CoV-2 virus within the nonwoven media of Fiber Bond HVAC air filters. Fiber Bonds VE3 Technology was “evaluated for its ability to inactivate SARS-coronavirus type 2” by Microbac Laboratories, Inc., and “demonstrated a 99.99% inactivation of the virus challenged.” In March 2020, shortly after the start of the COVID-19 pandemic, Fiber Bond’s team of engineers focused their expertise on the conceptualization and production of an HVAC-compatible filtration product with the ability to capture and eliminate the SARS-CoV-2 virus within an engineered binder system. In-house research and development of VE3 Technology successfully and swiftly progressed at the Fiber Bond facilities in Michigan City, IN. And, by late 2020, Microbac Laboratories, tested the VE3 Technology for capturing and inactivating the airborne SARS-CoV-2 virus. “This technology development undertaken by our Fiber Bond technical team is a testament to our ongoing efforts on providing products that enhance air quality. The VE3 technology is focused on providing an additional safeguard against airborne viral particles, specifically COVID-19, and is a great complement to our product portfolio that already includes antimicrobial products. Cleaner air helps to maintain a safer environment for all of us,” said Greg Wilkerson, president & CEO of Fiber Bond and Blocksom & Company. The VE3 Technology is designed to work in residential, commercial, and industrial HVAC systems to provide equivalent protection against SARS-CoV-2 in high-efficiency air filters. The VE3 Technology is added to the adhesive bonding agent used in the manufacturing of Fiber Bond’s nonwoven filtration media for HVAC applications. VE3 also includes Fiber Bond’s exclusive EPA-certified Spor-Ax antimicrobial agent for eliminating fungal bacteria growth on the filter media. Source: fiberbond.net
Sukano Antiviral Masterbatch shows efficacy in reducing SARS-CoV-2 on textile surfaces
Sukano’s Antiviral Masterbatch has undergone additional testing, following up a round of testing in 2020 confirming the effectiveness of its masterbatch against feline coronavirus and influenza H1N1. The company has now run extensive tests against SARS-CoV-2 in an external laboratory specialized in microbiological testing. The results confirmed the effectiveness of the Sukano Antiviral Masterbatches – within the first 30 minutes up to 99.9% reduction of SARS-CoV-2 on a fabric’s surface and a reduction up to 99.98% within 2 hours. “We extended the tests beyond PET and PA to PP and PLA, and also tested specifically against SARS-CoV-2 according to ISO standards,” said Michael Kirch, global head of R&D for Sukano. “These tests confirm the same robust and efficient results. We are delighted with the outcome of the tests and have now confirmation on the deactivation of the viruses on fabric surfaces by a certified and specialized external laboratory, giving our customers additional trust and confidence to use our high-performance additive masterbatch in their applications.” Sukano’s Antiviral Masterbatches work by directly integrating an antiviral additive into the polymer, using proprietary formulation and technology, eliminating the need for secondary processing steps. Sukano Antiviral Masterbatch allows the final product to remain fully recyclable without a loss in performance, contributing to the common goal of a circular economy. The Antiviral Masterbatch is extremely efficient and this powerful technology remains present and effective throughout the life of the product. The antibacterial efficacy was tested and remained after up to 200 washing cycles at 40 C. All this is possible without impacting the fibers’ physical properties or yellowing. The active ingredient used in Sukano’s Antiviral Masterbatches is a registered preservative in the EU, Switzerland and United States. However, to claim antiviral effect and promote this in the final product, producers using Sukano’s Antiviral Masterbatches must test the final product, have the results confirmed by a specialized external laboratory, and must comply with local legal regulations. Source: sukano.com
SGS introduces IC Mark for reuseable facemasks in U.S. and Canada
As more and more people around the world rely on the use of face masks to prevent the spread of COVID-19, SGS launched the first Independently Checked Mark (IC Mark) for reusable fabric masks, a new way for consumers in the U.S. and Canada to know if these products conform to industry and regulatory requirements. The new IC Mark tests and verifies products using key performance attributes from the recently published industry consensus standard, ASTM F3502 Standard Specification for Barrier Face Coverings. The Mark gives manufacturers and retailers a greater ability to demonstrate their focus on quality and performance, to create and supply products that meet or exceed the minimum legal requirements. In addition, its widespread use will provide consumers across North America with at-a-glance assurance that products satisfy safety and performance claims, and meet regulatory standards. “Consumers need reassurance from manufacturers and retailers that the reusable fabric masks they are using are performing as intended”, says Matthew McGarrity, Senior PPE Technical Manager for SGS North America. He adds, “They also need to know important criteria such as how many laundering cycles their masks can go through until they are no longer of use.” SGS in North America, along with other industry experts, helped draft the ASTM F3502 Standard Specification for Barrier Face Coverings. Its criteria include minimum design, performance, and care/use instructions. Working with leading experts in textiles, filtration and restricted substances, SGS drafted various domestic and mask/face covering guidelines. The IC Mark approval process tests for:
- Breathability
- Particle filtration efficiency
- Labeling
- Strap attachment strength
- Service life claims
- Restricted substances
- Flammability
Source: sgs.com
NCTO applauds Biden administration’s executive orders to solidify US supply chains for PPE and medical supplies
National Council of Textile Organizations (NCTO) president and CEO Kim Glas has issued statements supporting President Joe Biden’s recent executive orders aimed at solidifying U.S. supply chains for PPE and medical supplies, as well as actions outlined in the administration’s “National Strategy for the COVID-19 Response and Pandemic Preparedness.” “We commend President Biden for taking action in his first days in office to strengthen our domestic supply chain and manufacturing base with a ‘Made in America’ executive order directing the federal government to spend taxpayer dollars on American-made goods produced by American workers using American-made components,” said Glas. Increasing the domestic procurement threshold and the price preferences for domestic goods under the current “Buy American” law will bolster domestic production and stimulate more investment in U.S. manufacturing, said Glas. “We believe it is critical that taxpayer dollars are used to invest in American manufacturing and our workforce,” said Glas. “It is essential that we close loopholes in our Buy America laws, expand application and product coverage of domestic content rules, and close unnecessary contract waivers that undermine American manufacturing and its workforce.” Glas also thanked Senator Sherrod Brown (D-OH) and Representative Kathy Manning (D-NC) for their leadership in sending a recent letter to President Biden, requesting the president prioritize “Made in America” personal protective equipment (PPE) purchases and outlining key steps the administration can take to produce and procure quality American-made PPE for frontline workers. In addition, NCTO issued a statement welcoming President Joe Biden’s action plan and COVID-19 response, accompanied by a series of executive orders, including an order signed today to strengthen U.S. supply chains by directing federal agencies to use the Defense Production Act (DPA) to address shortages of personal protective equipment (PPE) and related vaccine supplies. “We are closely reviewing President Biden’s national strategic plan to confront the pandemic and welcome the executive order signed today to strengthen our supply chains by directing all federal agencies to use the Defense Production Act to address shortages of personal protective equipment, vaccine supplies and essential products,” said Glas. “These are important steps that will help ramp up critical manufacturing of these essential PPE products and other critically needed supplies like tests and vaccines.” American manufacturers have been at the forefront of the effort to build a domestic PPE supply chain since the onset of the COVID-19 pandemic. The U.S. textile industry retooled production and operations virtually overnight, producing millions of face masks, isolation gowns, testing swabs and other critical medical textiles. Since its inception, the DPA has been utilized by the Department of Defense to make critical investments in domestic textile manufacturing infrastructure and capacity, creating private-public partnerships through the government’s capital investments under the DPA and guaranteeing purchases through long-term contracts. “We applaud President Biden’s action today and anticipate further steps including a reported order that will seek to strengthen government procurement of U.S. products in the coming days,” said Glas. “We appreciate President Biden outlining in the ‘National Strategy for the COVID-19 Response and Pandemic Preparedness’ a series of actions and steps the administration will undertake to deploy and manufacture the vaccine and other essential products.” The NCTO has produced a video campaign that outlines steps the Biden administration and Congress must take to re-shore the production of personal protective equipment (PPE) and the entire supply chain for critical products:
To read the Biden administration’s COVID-19 action plan: whitehouse.gov/wp-content/uploads/2021/01/National-Strategy-for-the-COVID-19-Response-and-Pandemic-Preparedness.pdf To read NCTO’s critical steps that are necessary to strengthen the U.S. supply chain for essential products: ncto.org/ncto-outlines-key-priorities-for-the-incoming-biden-administration-and-congress-to-strengthen-the-u-s-supply-chain-for-essential-products/ Source: ncto.org
Porex medical device filtration materials shown to protect against spread of bacteria and viruses
Porex is one of the first in industry to initiate VFE testing for its porous polymer-based materials; results show components protect against certain aerosolized viruses To address the spread of healthcare-associated infections (HAIs) from aerosolized viral particles, Porex Corporation, a global leader in porous polymers, has pioneered the use of VFE testing methods for materials used in medical device design. Likely the first in the porous polymer material science industry to run the new analysis on filtration media, the components were able to consistently obtain a 99.9987% VFE score, showing that its materials effectively help to protect healthcare workers and patients from aerosol-based viruses potentially present in medical settings. Porex initiated VFE testing for its materials after observing the needs of its customers, which frequently fielded concerns from patients and healthcare workers seeking information that the components used in various equipment procedures would not pose risks of a HAI contraction. Nearly one in 31 hospital patients acquires a HAI—and these infections lead to an estimated 99,000 annual deaths in American hospitals alone, according to the Centers for Disease Control and Prevention (CDC). Healthcare workers face similar—if not greater—threats due to frequent exposure to viral pathogens. “The pandemic has magnified what was already a pressing issue in healthcare settings around the world, which is that inadequate filtration materials put patients and professionals at risk of contracting dangerous viruses,” said Avi Robbins, vice president, global product development and R&D at Porex. “We took the step to lead the materials industry into VFE testing to validate efficacy, and we are thrilled to confirm that our filtration and venting components are trustworthy and reliable for blocking viral particle spread.” Porex develops venting and filtration solutions by leveraging several core technology platforms such as sintered particles, bonded fiber, PTFE and Oxyphen track-etched membranes. Filtration and venting media from Porex are suitable for suction canisters, catheters, syringes and other medical equipment utilized in aerosol-generating medical procedures. Source: porex.com
Polygiene acquires Addmaster, expanding antimicrobial technology footprint
Sweden-based company Polygiene buys British Addmaster Holdings Limited, expanding its footprint for antimicrobial solutions for both soft and hard surfaces. The purchase price was SEK 374 million. “It’s great to have the backing of the EGM. We can now focus on merging the two companies and getting the organization established. The acquisition will allow us to offer the market a comprehensive solution of antimicrobial functions for both soft surfaces such as textiles and hard surfaces such as floors, handles, kitchen and bathroom fittings in public spaces. This reduces the need for washing and cleaning, therefore lessens our environmental impact,” said Ulrika Björk, CEO of Polygiene, which was established following the 2004 SARS pandemic through a spin-off from the Perstorp Group. Polygiene’s antimicrobial and odor management products include ViralOff, BioStatic and OdorCrunch. ViralOff, launched in the spring, has performed the best. According to ISO standards-based testing, it is over 99 percent effective at breaking down viruses such as SARS-CoV-2, which causes the disease COVID-19, within two hours. Addmaster Ltd is a leading supplier of high-performance, technically innovative additives to the plastics, textile, paper, paints and coatings industries. The company provides additive masterbatches, liquid or powder dispersions for any application. Biomaster Antimicrobial Technology and Biomaster Protected are Registered Trademarks of Addmaster (UK) Ltd. Biomaster Protected products are tested to ISO standards and are proven to be effective against over most common types of harmful bacteria and specific viruses including SARS-COV-2. Source: https://polygiene.com/
Standard Textile, Cleveland Clinic collaborate to develop reuseable facemask
Standard Textile, a global manufacturer of healthcare, hospitality, and consumer products, and Cleveland Clinic will collaborate to produce a non-medical grade, reusable facemask that is designed for comfort and customization. Standard Textile will sell the facemasks on its consumer website, standardtextilehome.com.
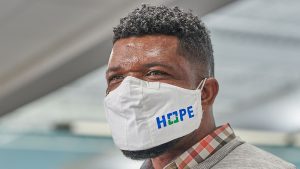
Standard Textile’s and Cleveland Clinic’s respective innovation teams collaborated to design the non-medical facemask, which will bear the inspirational message “HOPE” after Hope Hospital, a temporary hospital in the Sheila and Eric Samson Pavilion on the Health Education Campus of Case Western Reserve University and Cleveland Clinic. In April, Cleveland Clinic transitioned the Samson Pavilion to a temporary hospital to meet the potential needs of patients and the community in the event of a surge of patients with COVID-19. The building was converted back to the Health Education Campus for the fall semester. The reusable facemask offers enhanced comfort with its 100% cotton construction and breathability with its mesh lining. Adjustable ear loops and a neck strap add convenience of use, while its filter pocket and removable nose clip offer customization options. Standard Textile and Cleveland Clinic plan to produce custom-branded versions of the facemask for key partners looking to outfit their employees and customers with an enhanced, non-medical facemask. Source: standardtextile.com
ITMF survey shows COVID-19 has had negative impact on textile turnover, but expectations are improving
The International Textile Manufacturers Federation (ITMF) conducted its 6th ITMF Corona-Survey among ITMF members and affiliated companies and associations about the impact the COVID-19 pandemic has had on the global textile value chain. In total, 159 companies from around the world participated. In comparison to the 5th ITMF Corona-Survey (September 5th – 25th, 2020), the turnover expectations have improved by 4 percentage points from -16% to now -12% compared to 2019 (Graph 1).
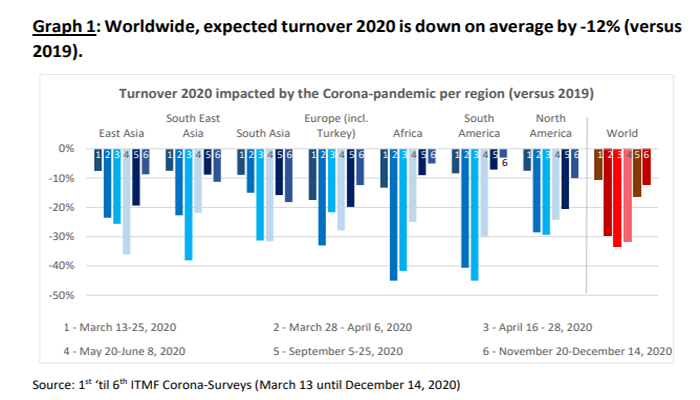
For 2021 and the following years, turnover expectations have overall improved slightly . On average, companies are expecting a small improvement from -1% (5th survey) to +3% (6th survey) compared to 2019. Also, for 2022 and 2023 the outlook has improved slightly from +9% (5th survey) to +11% (6th survey) and from +14% (5th survey) to +15% (6th survey), respectively. The turnover expectations for 2024 – compared to the 2019 levels – have not changed (+18% in the 5th and 6th survey). Source: itmf.org
Mask-Alliance Bavaria certifies FFP2 facemask; production to begin at Zettl Group plant in Weng
Founded in May 2020, in response to the COVID-19 pandemic, the Mask-Alliance Bavaria established a complete value chain for the manufacture of facemasks in Germany. In its latest development, the Futurus facemask has been certified as an FFP2 protective mask. In December, production will start at alliance member Zettl Group’s plant in Weng, Bavaria. Since the beginning of this initiative to produce mouth-nose protective facemasks, the founding members of the Mask-Alliance Bavaria – PIA Automation (automation specialist from Amberg), Sandler Group (manufacturer of high-tech nonwovens from Schwarzenbach/Saale) and Zettl Group (leading supplier in the field of automotive interiors) – had been working to produce certified FFP2 masks in Bavaria.
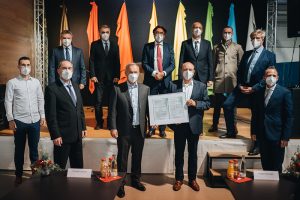
On December 3rd, Jörg-Timm Kilisch, Managing Director of DEKRA Testing and Certification GmbH, officially presented the certificate at the Zettl Group company site in Weng, Landshut district. FFP2 or FFP3 masks are particularly recommended as personal protective equipment for healthcare workers who are exposed to an increased risk of infection in their work. The quality of the filter medium, the mask design, the fit and the available filter area are decisive for the classification of the product. In joint development work and close cooperation with the new association member DEKRA, the certification process was successfully completed at the end of October. The fully automated production lines in Weng will now produce up to 6 million Futurus masks per month. An expansion of the production capacity to up to 10 million masks per month is already being planned. The Mask-Alliance Bavaria is thus expanding its contribution to securing the supply of these important medical products. Source: masken-verbund-bayern.de
WHO issues COVID-19 mask guidance; references AATCC standards
The World Health Organization (WHO) now advises manufacturers wishing to produce product with consistent performance to follow guidance from AATCC or other standards organizations. WHO issued interim guidance for “Mask use in the context of COVID-19,” and the annex provides information on fabric face coverings, including reference to AATCC M14, Guidance and Considerations for General Purpose Textile Face Coverings: Adult. This WHO guidance, which is an update of the guidance published on 5 June 2020, includes new scientific evidence relevant to the use of masks for reducing the spread of SARS-CoV-2, the virus that causes COVID-19, and practical considerations. It contains updated evidence and guidance on the following:
- mask management;
- SARS-CoV-2 transmission;
- masking in health facilities in areas with community, cluster and sporadic transmission;
- mask use by the public in areas with community and cluster transmission;
- alternatives to non-medical masks for the public;
- exhalation valves on respirators and non-medical masks;
- mask use during vigorous intensity physical activity;
- essential parameters to be considered when manufacturing non-medical masks (Annex).
AATCC staff participated in a series of weekly meetings of the WHO group that compiled the latest guidance. The language and thresholds for several essential face covering parameters are consistent with the recommendations in AATCC M14. While various national and regional bodies have issued similar guidance, AATCC M14 was the first global standard to address general use face coverings. The AATCC recommendations for filtration and breathability are similar to those cited in other standards. Further alignment of standards was discussed and encouraged by the WHO advisory group. In addition to testing parameters, AATCC M14 includes practical consideration for fabric and design selection. This is particularly valuable for manufacturers pivoting from unrelated products with minimal background in textiles or public wellness. WHO also references AATCC TM100, Test Method for Antibacterial Finishes on Textile Materials: Assessment of, for antibacterial testing, though the organization advises caution in making antimicrobial claims for non-medical face coverings. AATCC M14 is under the jurisdiction of committee RA113, Emerging Technologies Test Methods. The committee met in November and plans to develop a new standard to address the specific needs of face coverings for children. Participation in AATCC research committees is open to all. WHO Guidance: https://apps.who.int/iris/rest/bitstreams/1319378/retrieve AATCC M14: https://members.aatcc.org/store/m014/3085/ AATCC COVID Resources and Information: www.aatcc.org/covid/ Source: aatcc.org
Polygiene ViralOff promises antiviral capability with ‘lifetime of garment washability’
Polygiene is launching its newly developed formula of ViralOff with lifetime of garment washability (equivalent of 30 washes), proving performance against SARS-CoV-2 with over 99% reduction of microbes in the material within two hours. This also results in longer lasting products, which means a reduced impact on the environment. The new formula is being applied by a number of partners as we speak and is ready for high volume deliveries in January 2021. “There has been some confusion in the market as claims to washability wrongly rely on tests that are not antiviral, but rather antibacterial. We have therefore developed a treatment that provides an antiviral effect according to global test standard ISO18184:2019 (Determination of antiviral activity of textile products) and really meets the antimicrobial and antiviral claims that we make”, says Daniel Röme, Chief Technology Innovation Officer at Polygiene.
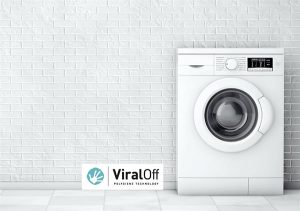
“Demand has been high from the fashion and lifestyle segments for an improved formula of Polygiene ViralOff that will have lifetime washability with a maintained high level of viral reduction. As the pandemic has evolved, there seems to be a consensus on the fact that antimicrobial materials will be the ‘new normal’ in products such as garments, bags, often-touched items, cleaning and home products and more, going forward. This regardless of the number of vaccines that are being developed, which we hope will put a stop to or slow down this global pandemic. I believe that when the world is re-opening, this feature will be highly valued by many people”, concludes Ulrika Björk, CEO Polygiene. We still believe that fewer washes are always a good thing. However, we also want to make sure that products that need to be washed, keep their effectiveness, get an extended lifetime and are not thrown away too early. Source: polygiene.com
HeiQ Viroblock wins First Place in prestigious Swiss Technology Award program
HeiQ Viroblock won the coveted Swiss Technology Award 2020 for its breakthrough antiviral textile technology, HeiQ Viroblock. This is the most notable recognition for the young company’s innovative spirit and technologies as well as its contribution to stemming the spread of the global pandemic COVID-19. The leading technology prize in Switzerland, Swiss Technology Award, yesterday announced the 2020 prizes, and among all the notable finalist innovations of the year, HeiQ was bestowed the highest honor as First Prize Winner.
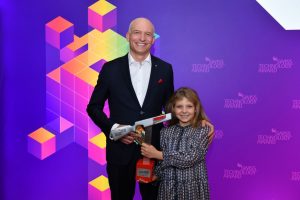
Developed in record time and launched after the Swiss authorities announced the lockdown in March 2020, HeiQ Viroblock has had a major impact on the global textile industry and is being unprecedently adopted by mills around the world. HeiQ Viroblock is one of the world’s most efficient and effective antiviral/antimicrobial technologies and has been applied by more than 150 brands worldwide to over 1 billion products from face masks to apparel to home textiles to date. What exemplifies HeiQ Viroblock is its ability to turn any fabric antiviral. It’s among the first textile technologies in the world to be proven effective against the SARS-CoV-2 virus. HeiQ Viroblock consists of a combination of HeiQ’s patent-pending vesicle and silver technologies. The two mechanisms of attack result in an over 99.9% destruction of viruses in 5 minutes. HeiQ Viroblock is a unique patent-pending formulation of 72% bio-based ingredients, made with 100% cosmetic-grade materials from the International Nomenclature of Cosmetic Ingredients list. Source: heiq.com
Polygiene partners with Silvertek to incorporate antimicrobial textile treatment with FDA-approved facemask technology
Polygiene has partnered with Silvertek to provide FDA-approved facemasks with the antimicrobial textile treatment ViralOff, which is a tested and certified technology per the global standard of ISO18184:2019 against SARS-CoV-2, H3N2 and H1N1. Months prior to the pandemic, SilverTek was already developing an advanced facemask with its FDA-registered manufacturer. Unlike most masks on the market, which are being manufactured under Emergency Use Authorizations and with little thought to design, SilverTek had the benefit of time and experience to craft their proprietary FDA-listed mask for optimal comfort and breathability. For example, SilverTek discovered early in their mask development that exhalation valves were an unsafe component of mask wear due to their release of the wearer’s unfiltered exhale. For this reason, airlines, many public school districts, and entire regions such as the California Bay Area are now banning masks with valves. ”We wanted to find the best antimicrobial treatment for our NanoFit mask and evaluated numerous companies in the process”, states Silvertek President Ji-mei Ma. Further noting: “We were looking for a partner we could trust – who was environmentally friendly, wellness-conscious, and an established player in the field of antimicrobial technologies. We are glad to have selected Polygiene and have ViralOff protect our NanoFit Masks.” ”We are excited that ViralOff adds value to a FDA-listed textile mask. In addition to the high antimicrobial performance, these masks will also need less washing* and will therefore last longer, which is good for the user and the environment,: says Ulrika Björk, CEO of Polygiene. *For more information on washing habits and Covid-19, read “Survey on viruses, washing and ViralOff”. Source: polygiene.com
Data suggests cotton batting can increase the filtration efficiency of cloth facemasks
Recent FDA chief Scott Gottlieb, Ph.D., argued that he’d “rather try to get everyone in masks” and “try to get them in high-quality masks because we know it’s going to slow down the transmission.” Against this backdrop, a new study published in Risk Analysis, “Reinventing cloth masks in the face of pandemics,” by Stephen Salter, P.Eng., describes how Effective Fiber Mask Programs (EFMPs) can help communities find a balance between the economy and curbing community spread. A separate study by Stadnytskyi, et al. estimates that one minute of loud speaking generates at least 1,000 virion-containing droplets that remain airborne for more than eight minutes. If everyone uses effective masks, the benefit is compounded because each person’s mask reduces the number of particles they transmit, and also the number of particles they inhale. The new study in Risk Analysis suggests that the effectiveness of cloth masks can be improved by using a non-woven material such as cotton batting. Increasing the surface area of fibers exposed to moving air improves filtering efficiency because the smaller particles are absorbed onto the fibers. In May and June of 2020, 17 handmade cotton batting masks underwent 35 tests using commercial quantitative fit testing equipment to determine their filtering effectiveness. The results showed average filtering effectiveness of 76 to 90 percent against aerosol particles. Read the full story: https://www.sra.org/2020/10/23/new-data-on-increasing-cloth-mask-effectiveness/ Source: https://www.sra.org/
PureAir Filtration, Nobel Biomaterials partner to develop antimicrobial fiber for filtration
PureAir Filtration, a company specializing in removing corrosive gases, toxic vapors and odors, announced it has launched a strategic partnership with Noble Biomaterials, a leader in antimicrobial and conductivity solutions for soft-surface applications. The companies have developed an antimicrobial fiber called FiberShield that can be used as an added fabric layer in particulate filters to help fight microbes amid the COVID-19 pandemic. FiberShield is made of a proprietary blend of nonwoven nanofibers that are impregnated with antimicrobial Ionic+™ silver technology. The antimicrobial fabric can be used in any particulate filter and is the only one on the market to offer such flexibility to filter manufacturers. FiberShield with Ionic+ technology has been tested and proven effective by independent testing laboratories to inactivate over 99% of specific pathogens. PureAir also debuted a second product in its antimicrobial line called Microbe-sorb, an adsorbent media that utilizes a proprietary blend of compounds to activate, enhance and deliver the strong antimicrobial properties of permanganate, a material commonly used in medical practices since the early 1800s. Independent laboratory tests show Microbe-sorb inactivates over 99% of microbes on contact. Source: pureairfiltration.com
Zinc fiber technology proves 99.7% effective in combatting respiratory viruses, including influenza and human coronavirus
ION Manufacturing announced its ZnTech technology – a proprietary and patented zinc fiber matrix capable of generating microcurrent that is lethal to coronavirus and other virulent pathogens. According to ION, ZnTech has significant potential for various applications, including its use in Personal Protective Equipment (PPE) and both medical and consumer-grade electroceutical fabrics. ION Manufacturing is among the first U.S.-based companies to come to market with scientifically verified zinc-based antiviral technology. ZnTech fully destroys viral pathogens, while most currently available antiviral technology employs chemicals that only retard or repel viral particles. Market competitors often employ coatings of other metals, such as Copper and Silver, neither of which are capable of generating the microcurrent essential to kill Coronavirus. Further, Zinc is a proven safe and non-toxic element, making it most suitable for application in materials that are placed directly on the skin and over the mouth. The zinc fiber matrix interacts with exhaled moisture and oxygen, or oxygen from the skin’s surface, to generate the microcurrent. The sustainable electric field is created without wires or an external battery source and maintains its current, despite repeated washings. The antiviral properties of ZnTech facemask technology greatly decrease transmission of exhaled infectious droplets to the surrounding environment while offering protection to those who are wearing the fiber. In addition to its antiviral applications, microcurrents have many positive and well documented health benefits including increased blood flow, enhanced ATP production in the mitochondria, pain relief, collagen production and nerve stimulation. ZnTech fabric was lab tested by Integrated Pharma Services, a leading pre-clinical and clinical research organization. ZnTech™ consistently demonstrated antiviral properties against various respiratory viruses including influenza and human coronavirus with a 99.7% success rate. The antiviral efficacy testing was conducted based on ISO Standard 18184:2019. Source: ionsportswear.com
Fallon, Shawmut invest in West Bridgewater, Mass., manufacturing site, adding capacity for 180 M N95 respirators per year
The Fallon Company and Shawmut Corporation announced the creation of a new domestic manufacturing operation to produce N95 respirators. Manufacturing equipment installed in an expanded facility based in West Bridgewater, Mass. will enable end-to-end production of up to 180 million masks per year. Additionally, the operation is expected to create as many as 300 new jobs in Massachusetts. The new effort will also be supported with a $2.7M grant from the Commonwealth’s Manufacturing Emergency Response Team (MERT), a state-led initiative that has facilitated the production of more than 11 million pieces of personal protective equipment (PPE) and other critical items by manufacturers that pivoted operations to address COVID-19 at the onset of the public health crisis. This is one of 13 grants totaling $6.5 million being distributed to multiple organizations during October, or “Manufacturing Month,” to support the production of PPE in Massachusetts. “The MERT program continues to identify and support successful ‘Made in Massachusetts’ manufacturers like the Fallon Company and Shawmut Corporation, that will produce N95 masks and other PPE equipment locally, for Massachusetts front-line responders, business owners, and residents,” said Governor Charlie Baker. “We are pleased to welcome the expansion of this manufacturing facility in Massachusetts and appreciate the role these companies are playing in the Commonwealth’s fight against COVID-19.”
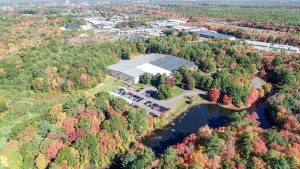
The operation brings together two well-established, successful family businesses to serve as one of only a handful of high-quality mask manufacturers in the U.S. The West Bridgewater facility will extend existing Shawmut manufacturing capabilities, which include medical gowns, to add polypropylene meltblown extrusion and mask conversion capabilities to create respirators, shoring up the U.S. healthcare supply chain with domestic production. The 60 tons of machinery was fast-tracked from Reifenhauser REICOFIL GmbH & Co of Germany on an expedited timeline and, last week, landed in the Port of Boston. In addition to a financial investment by Joseph Fallon, CEO of the Fallon Company, the effort will be supported by President Michael Fallon and the company’s development, legal, and construction teams. Funds will support infrastructure upgrades, utility improvements, and capital investment to Shawmut Corporation’s manufacturing facility in West Bridgewater. Widely recognized as the leader in melt-blown polypropylene production equipment, the Reifenhauser production line will enable the conversion of non-woven materials into N95 respirators in Massachusetts. Source: shawmutcorporation.com
Suominen partners with fellow Finnish companies to ensure supply and authenticity of facemasks in Finland
Finland, with no domestic facemask production at the time, had difficulties sourcing high-quality masks at the beginning of the COVID-19 pandemic. Suominen, a globally leading nonwovens producer, was one of the companies that promptly reacted to the difficult situation. In an ultra fast-tracked innovation process Suominen and its partners developed a novel nonwoven, FIBRELLA Shield, suitable for use in the manufacturing of respirators. The innovative nonwoven, developed in only a few months, has passed the European Standard EN 14683:2019 Type II requirements in terms of filtration efficiency and pressure drop.
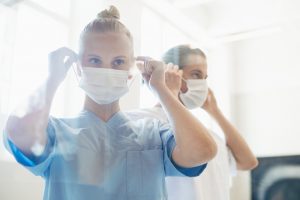
“FIBRELLA Shield not only provides excellent protection, it is also comfortable and easy to breathe through,” said Suominen’s Category Manager Johanna Sirén. At the same time that Suominen was developing the new material, Screentec Oy – a renowned producer of medical electrodes and human-machine interfaces for demanding environments – decided to start production of high-quality face masks at its Oulu works. After an exceptionally fast installation phase, the new production line was ready by late summer. “The common aim, a fully domestic supply chain for high-quality face mask production, was a natural starting point for our cooperation with Suominen. The plan is that in the future we will mainly use Suominen’s FIBRELLA Shield in our face masks,” said Screentec’s CEO Antti Tauriainen. Suominen has been working with TrueMed Oy, an innovative Finnish start-up, already earlier. TrueMed has developed an AI and machine vision-based non-additive solution that is used to detect original and counterfeit medicines and medical products. The aim of the cooperation between the three companies is to be able to confirm the authenticity of the masks and the nonwoven used in them – in this case, FIBRELLA Shield – and thus to guarantee end-user safety. The cooperation also aims to produce important inventory information for the customer, for example, information about expiration days or how many masks that have been used. “Determining if the product is genuine or a counterfeit is done through our mobile phone app, TrueMed Scanner. We provide Suominen an identification process and mechanism that can detect the product authenticity on the fiber level of the nonwoven material. Suominen Intelligent Nonwovens utilizes TrueMed’s proprietary AI and machine vision platform. At the same time, we can read all the necessary codes and markings on the product and it’s packaging,” explained TrueMed’s CEO Jyrki Berg. “By combining the deep know-how of the three companies, we are able to offer our customers high-quality face masks with verifiable authenticity as well as the ability to follow the inventory data. In the future many of these kind of technical innovations, for example related to the end-users safety, smart supply chain data, carbon footprint information and so on, can be taken into use with Suominen Intelligent Nonwovens TM. This very fast joint development project was also funded by Business Finland research and development funding,” said Suominen’s CTO, Markku Koivisto. Source: suominen.fi
Freudenberg to add meltblown capacity in Europe
Freudenberg Performance Materials (Freudenberg) is expanding its production capacity for nonwoven media used exclusively to manufacture certified facemasks of the mouth-nose protection type pursuant to the EN14683 standard, as well as FFP1, 2 and 3 masks pursuant to the EN149 standard. The media are specially developed for and sold to the medical technology processing industry. To that end, Freudenberg is investing in the construction of a new state-of-the-art meltblown production line at the Kaiserslautern site. Commissioning of the new plant is slated for the first quarter of 2021. “As a world-leading manufacturer of technical textiles and filtration media, Freudenberg Performance Materials has deep expertise in materials for certified face masks. By expanding our production capacity in Kaiserslautern, we are making a contribution to mastering the challenges presented by COVID-19 and supplying certified type face masks as well as FFP1, FFP2 and FFP3 masks in Germany and Europe”, said the CEO of Freudenberg Performance Materials, Dr. Frank Heislitz. With the new line, Freudenberg is significantly expanding production capacity for meltblown nonwovens in Kaiserslautern. The world-leading technical textiles manufacturer produces these materials from extremely fine meltspun polypropylene microfibers that are several times thinner than a human hair. Masks made of these nonwovens can filter very small particles such as viruses thanks to the superfine structure of the material and its electrostatic charge. Source: freudenberg.com
NWI’s spunbond high-efficiency filter media wins RISE Innovation Award
More than 150 professionals in product development, materials science, and new technologies convened for the 10th conference edition of RISE—Research, Innovation & Science for Engineered Fabrics, held virtually, Sept. 29-Oct. 1. The event was co-organized by INDA, the Association of the Nonwoven Fabrics Industry, and The Nonwovens Institute, and North Carolina State University. Among the program highlights was the presentation of the RISE Innovation Award, which was presented to The Nonwovens Institute at North Carolina State University for its Spunbond High-Efficiency Filter Media. The product is a completely new approach to creating filtration media with the right efficiency at low pressure drop at a throughput of 350 kg per meter per hour. The pressure drop with The Nonwovens Institute’s new filter is unmatched by any meltblown structure and doesn’t require electrostatic charging, which has been an obstacle to facemask manufacturing during the COVID-19 pandemic. The materials is also much stronger than traditional meltblown filter media, thus providing the potential for reuse after appropriate cleaning and disinfection.
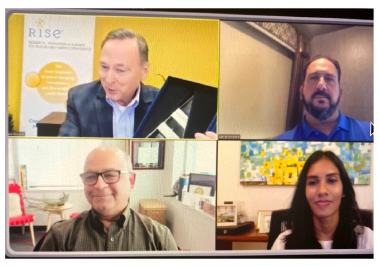
NWI said it has produced 4.5 million meters of the material so far, enough to produce 100 million masks. Other nominees for the award included FemTech at MAS Holdings Pvt. Ltd. for its leakproof absorbent nursing pads and Sustainable Solutions Incorporated for its BlueCON Nonwovens initiative that produces recycled resin from hospital waste. Source: riseconf.net * International Fiber Journal is owned by INDA, Association of the Nonwoven Fabrics Industry (inda.org).
Shemesh invests $4M to develop 200PPM canister wipes technology platform
Building on decades of perfecting existing technologies pertinent to wipes production, Shemesh announced a $4 million investment in a new wipes manufacturing technology, responding to increased demand and market trends, partially set by the COVID-19 pandemic. The investment includes a new U.S. showroom and spares inventory. The all-new total solution canister wipes platform, dubbed TKS-200, is an extension of the empirically proven TKS-60 and TKS-120 models. The TKS-200 is designed to run at a consistent speed of 200ppm and a maximum speed of 220-240ppm. Prior to being available for purchase, the TKS-200 will be demonstrated to a select group of key industry players at the all-new U.S.-based Shemesh headquarters in Green Bay, Wisconsin, in the second half of 2021.

Canister wipes lines are much more sophisticated compared with lines built for other traditional market sectors, such as food & beverage or cosmetics, which Shemesh also operates. That is partially because such pharma-grade lines involve high-speed liquid filling in containers with elastic solids in them (the round nonwovens) combined with other complex technologies unique for canister wipes lines as automatically stuffing rolls (the round nonwovens) into cans in high speeds. This often happens while simultaneously dealing with alcohol-based solutions as well as in a potentially corrosive environment. Shai Shemesh, Shemesh Automation’s CEO commented, “We have been working tirelessly over the last few decades to optimize our machinery and truly perfect our total turnkey solution for the canister wipes industry. I am so proud of what we have managed to achieve with the ground-breaking TKS-200 total turnkey solution. Indeed, we know of no other company on a global scale with such deep, vertical know-how in such different technologies as Liquid Filling, Round Wipes Rolls Stuffing, Conduction Sealing, Capping, Labelling, and Case Packing – the core technologies underlying the Shemesh great value proposition catered to our customer base. As the only company in the world capable of offering a true canister wipes outfit from product feed all the way to a packed case with equipment built under just one umbrella – the edge we provide at Shemesh to our customers is immense.” Source: shemeshautomation.com
Sukano announces masterbatches for PET and PA fibers have antiviral effect
Many viruses have been shown to survive on surfaces including metal, cardboard and plastic. However, plastic items can be treated to trap and inhibit the replication of viruses. Sukano has developed Antiviral Masterbatches for PET and PA fibers that have a strong antiviral effect on the plastic parts, while also potentially helping to reduce waste and improve the sustainability credentials of the final articles produced. Sukano’s Antiviral Masterbatches work by directly integrating an antiviral additive into the polymer, using proprietary technologies. The power of this technology is that the antiviral effect not only remains stable during the usage of the product, but that it is maintained after washing. This is because the additive is consistently present on the surface of the product, without being released into the environment. Sukano conducted tests at an external laboratory specialized in microbiological testing and in accordance with ISO 18184:2019 (fabrics) and ISO 21702:2019 (plastics inject molded parts and films) to independently confirm the effectiveness of its antiviral effect on the plastic parts. The result showed that over 98 % of the Feline Coronavirus was eliminated within the first two hours. The tests were performed using the Influenza H1N1 virus and a Feline Coronavirus, which has structures and mechanisms similar to SARS-Cov-2. SUKANO Antiviral Masterbatches offer not only high performance, but also durability, as the antiviral efficacy of the fibers remains after multiple washing cycles at 40 C. This is possible without impacting the fibers’ physical properties or yellowing. Read the full announcement on SUKANO Antiviral Masterbatches: https://www.sukano.com/en/company/news/sukano-masterbatches-demonstrate-long-term-antiviral-effect Source: sukano.com
Lydall to add fine fiber meltblown line in France with capacity for 600 M respirators and 2.2 B surgical masks
Lydall, Inc., a manufacturer of value-added engineered materials and specialty filtration solutions, today announced its investment in a new production line to create fine fiber meltblown filtration media for facemasks and high-efficiency air filtration systems. This new line will be installed at Lydall’s facility in Saint-Rivalain, France, in the second quarter of 2021, substantially increasing the company’s capacity to supply this critically needed material to the European market. The investment solidifies Lydall’s position as one of the largest global suppliers of fine fiber meltblown filtration media, the crucial component of N95 respirators and the European equivalent, FFP2/FFP3, as well as surgical masks and MERV-, HEPA- and ULPA-grade air filters. Lydall will receive up to 30 percent of funding for the investment through the support of France’s Ministry of the Economy and Finance. “COVID-19 has created unprecedented global demand for face masks, upgraded air filtration systems and other products that are essential to preventing the spread of the virus. In response, governments around the world are now focused on establishing secure, reliable and sustainable domestic supply chains so they can guarantee they have access to high-quality products that are pivotal to national security and public health,” said Sara A. Greenstein, President & CEO of Lydall. “Our global footprint and 100-year heritage in creating specialty filtration solutions position Lydall to serve as a local manufacturing partner to governments around the world, now more than ever. We take our role in creating products that protect people and places from viruses such as COVID-19 incredibly seriously, and we are grateful for the support of the French government, which will allow us to ramp up production even further.” Once this additional line is operational, Lydall expects to produce enough fine fiber meltblown filtration media for 600 million FFP2/FFP3 respirators or 2.2 billion surgical masks per year. The company plans to hire additional staff to support the increase in production. Source: lydall.com
Revolution Fibres publishes paper touting electrospun nanofiber vs. meltblown
Filtration plays an important role in purifying and decontaminating two life necessities — water and air. As awareness of the related health issues has increased, the demand for protection from airborne pollution and disease has also increased. From this perspective, Revolution Fibres of Auckland, New Zealand has issued a new white paper explaining the unique and enhanced capabilities that electrospun nanofibers provide when used as an active layer in facemasks. When compared to common meltblown filters, Revolution Fibres makes the case that electrospun nanofibres provide better protection against air particles, bacteria, and viruses such COVID-19. Read the white paper: https://www.revolutionfibres.com/wp-content/uploads/2020/08/MB-vs.-NF-White-Paper.pdf Source: https://www.revolutionfibres.com/
Rockline disinfecting wipes formula receives EPA coronavirus kill claim approval
Rockline Industries announced the formula used in its hard surface disinfectant wipes (EPA registration number 6836-336) has been approved by the U.S. Environmental Protection Agency to add claim language that the formula has been proven to kill SARS-CoV-2, the coronavirus that causes COVID-19, when used according to directions. “Disinfecting wipes that kill the coronavirus that causes COVID-19 are essential to the health and safety of our communities,” said Ron Kerscher, senior vice president of sales and marketing for Rockline. Rockline is among the first private brand suppliers to receive the EPA’s approval for a coronavirus kill claim for the chemistry it uses in its disinfecting wipes products. “With this claim, retailers and consumers can have confidence that our disinfecting wipes products when used as directed will protect their homes and families,” Kerscher added. Source: http://www.rocklineind.com/
PyroTex fiber certified 99% effective against SARS-CoV-2 virus
Specialty fiber PyroTex by Hamburg, Germany-based company PyroTex Industries is reported to provide 99.57% (99% after 14 seconds) against the SARS-CoV-2 virus. This result has been confirmed by an independent, ISO-certified laboratory according to ISO 18184: 2019. The PyroTex fiber is an engineered Acrylic, which can be employed for protective masks, general protective and medical clothing as well as products for the hospitality and the private sector. The company is cooperating already several large brands to incorporate the PyroTex fiber for PPE used to support the COVID-19 response. Besides its activity against SARS-CoV-2, the flame and heat resistant PyroTex fiber also has an activity of over 99% against bacteria such as Staphylococcus Aureus, Escherichia Coli and Klebsiella Pneumoniae. All properties are permanent and non-toxic, certified according to OekoTex Standard 100, class 1. Source: http://pyro-tex.de/
Driven by wipes demand, Suominen reports record quarterly sales
Suominen achieved record high quarterly net sales and operating profit in the second quarter of 2020, increasing net sales by 18% to EUR 122.2 million. Sales volumes increased considerably, but sales prices decreased following lower raw material prices. The main driver for the volume increase was higher demand of wipes due to the COVID-19 pandemic. “We were able to respond to the increased demand by running our production efficiently despite the challenges caused by the pandemic,” said Petri Helsky, Suominen President & CEO. “Our operating profit increased significantly to EUR 12.4 million (2.7) in the second quarter mainly due to higher production and sales volumes. Also margins increased as the lower sales prices were compensated by lower raw material and other direct product costs, while fixed costs were kept well under control.” The pandemic increased sales volumes in all markets also in the second quarter. In the longer term, Suominen expects the COVID-19 pandemic may lead to a continued increase in demand for nonwovens for cleaning and disinfection products. “In June we upgraded our outlook for the year due to stronger than anticipated development in all our markets. The outlook for 2020 states that we expect that our comparable operating profit will improve significantly from 2019,” said Helsky. Source: https://www.suominen.fi/
Nonwovens Ibérica launches meltblown line
Nonwovens Ibérica announced the launch of a high-performance line for the production of meltblown, the only nonwoven suitable for the manufacture of EPI facemasks and sanitary material up to 99% bacterial filtration efficiency. The meltblown material, which has been in short supply as the global COVID-19 crisis has taken hold, is low cost and will be manufactured in large supply from the last quarter of 2020 to help support the production of facemasks and PPE needed in response to the COVID-19 pandemic. Source: https://www.encarnonwovens.com/
Two-layer polyester mask design shows 91.8% efficiency in Viral Filtration Efficacy test
Ed Goodwin, the founder and product development manager of HipSaver Inc., has always obtained scientific validation for all of his medical textile products. As such, he engaged Nelson Laboratories, to test his company’s DermaSaver Sci-Tex Mask construction. “We believed our product would be effective based on the known textile science, and now these results from Nelson Labs have proven that to be true,” says Goodwin. “Virus transmission experts agree that exposure duration and dose volume of virus particles are two key factors in overwhelming the immune system. This test result shows a dramatic reduction in the dose volume exposure.” Viral Filtration Efficacy (VFE) test showed the DermaSaver Sci-Tex Mask material construction to be an average of 91.8% effective in preventing aerosolized virus particles from penetrating through the mask. The virus particles tested are five times smaller than COVID-19 virus particles, implying that the efficacy against preventing COVID-19 virus particles from penetration could be even greater. The mask, which retails for less than $20, consists of two layers of water resistant (hydrophobic) microfiber polyester that repels airborne droplets. The brushed inside surfaces of the layers mesh together to create an additional barrier. For additional information and to view the full test report, visit: dermasaver.com
INDA publishes Meltblown Nonwoven Markets: COVID-19 Impact Analysis
With respirators and medical facemasks at the forefront of efforts to fight COVID-19, a new report from INDA, the Association of the Nonwoven Fabrics Industry, examines the market and outlook for the stand-alone meltblown process used to produce those products. The report, Meltblown Nonwoven Markets: COVID-19 Impact Analysis, presents an outlook on the meltblown required for medical facemasks and respirators in the U.S., providing insights for companies to make informed decisions during these times. The report also provides a global view of meltblown capacity. Based on extensive research, producer surveys and interviews with industry leaders, the report is authored by Brad Kalil, INDA’s Director of Market Intelligence & Economic Insights, an industry leader on providing important information on this sector of the nonwoven industry. This report is focused on the overall market and provides an introduction to meltblown techniques, the fibers’ unique properties and end-use applications, historical capacity, and estimated U.S. and global volumes. For more information on this report: https://imisw.inda.org/store/detail.aspx?id=MELT20 Source: inda.org * International Fiber Journal is owned by INDA, Association of the Nonwoven Fabrics Industry (inda.org).
Nonwovens Institute, Freudenberg PM partner to add capacity for up to 1M facemasks per month
Together with The Nonwovens Institute at NC State University, Freudenberg Performance Materials will begin production of ear loop procedure and N95 masks. The two organizations are aligning their expertise and supply chains to bring PPE to universities and healthcare workers as quickly as possible. Through this partnership, NC State is supplying Freudenberg Performance Materials with the necessary roll goods needed for production while Freudenberg provides the textile manufacturing expertise and work force needed to install, operate and maintain the four new production lines. “As the leader in the development of the next generation of nonwovens, we knew we could step in and help fill this critical need. By partnering with Freudenberg, we will ensure the reliable completion of millions of protective face coverings to battle the coronavirus using NWI’s novel filter media”, says Behnam Pourdeyhimi, Executive Director of The Nonwovens Institute. Once fully operational, the site will be able to produce more than one million masks a month. In addition to the facemask lines provided by NC State, Freudenberg is also in the process of installing six additional production lines to manufacture surgical and N95 masks. Not only will the lines help provide essential face coverings, but the addition of the lines has enabled Freudenberg to add 50 new positions within the company to operate the lines. Source: freudenberg-pm.com & thenonwovensinstitute.com
IFAI Expo to be all-virtual in 2020
Given the continuing uncertainty with the spread of the COVID-19 pandemic and the importance of the health and safety of the entire textile community, IFAI has made the difficult, yet unavoidable decision to transition IFAI Expo 2020, set for November 3-6, 2020, in Indianapolis, Ind., to an online only virtual event. IFAI Virtual Expo will take place over several days in early November 2020 in a robust platform designed to provide many exciting opportunities for attendees, exhibitors and sponsors to discover, network and help grow their businesses. Going virtual allows attendees — both domestic and international — to experience IFAI Expo in a new way. Attendees will explore the knowledge-packed educational sessions from the comfort of their home or office. Textile professionals from anywhere in the world can discover new products, chat, network and meet with exhibitors, communicate with colleagues and learn from world-class educators and presenters. The decision to cancel the live event was not easy. IFAI considered the impending potential cost exposure of exhibitors and attendees, and concerns for safety, as well as travel difficulties inhibiting attendance, and determined this was our best option. Source: ifai.com
Bolger & O’Hearn donates hand sanitizer to support COVID-19 response
Bolger & O’Hearn has donated 22 quarts of hand sanitizer to Community Connections, Inc., a Massachusetts nonprofit that provides life-enriching services and training for developmentally disabled adults, ages 22 and above. The programs at Community Connections are designed to help their clients live as independently as possible. The organization has been closed since March 16 due to the COVID-19 pandemic and the donation will help support its reopening later this summer. Tanya Madeira, the Life Skills Program Manager at Community Connections, stated that the organization is currently planning the reopening of the Fall River locations in August with very strict restrictions and guidelines to ensure the safety of her clients and staff. Community Connections serves 58 developmentally disabled adults with a staff of 17, and donations of hand sanitizer and disinfectants are needed and greatly appreciated. In April, Bolger & O’Hearn donated over 700 pounds of hand sanitizer to Brigham and Women’s Hospital in Boston. BWH is a teaching affiliate of Harvard Medical School. That donation of hand sanitizer was distributed in 4.6 ounce bottles to residents of underserved Boston communities, where hand sanitizer was either not available or affordable, to help fight the COVID-19 pandemic in New England. Source: bolgerohearn.com
VDMA highlights how textile machinery is being employed in COVID-19 response
As the coronavirus continues to have an impact worldwide, the VDMA textile machinery association serving Germany and Europe has launched a new series of web events called “Textile Machinery Webtalk.” The series features experts from up to four VDMA member companies presenting their innovative technologies on a specific topic with particular emphasis on how textile machinery is being employed in the COVID-19 response. Topics of the first two webtalks were:
- “Technologies for the production of melt-blown nonwovens for respiratory protection masks (FFP masks and surgical masks)”
- “Technologies for the production of respiratory protection masks (FFP masks and surgical masks)”
The next webtalk will take place on July 23 2020 from 14.00 to 16.00 (CEST) on the topic of “Technology solutions to produce fully-fashioned community face masks.” Experts from KARL MAYER, STOLL by KARL MAYER and Jakob Müller will be presenting their technologies for producing everyday textile masks. Registration is available at https://register.gotowebinar.com/register/2607744021751510284 VDMA is also offering a website, http://www.machines-for-textiles.com, with detailed information on process steps and the range of services offered by the members of VDMA Textile Machinery. The overview is continuously updated, with a manufacturers’ directory featuring a broad range of textile machinery companies. Source: vdma.org
Industry coalition calls on U.S. govt. to aid in reshoring of PPE manufacturing
An industry coalition representing the U.S. personal protective equipment (PPE) production released a statement outlining policy principles and objectives needed for reshoring and safeguarding domestic PPE manufacturing. The joint statement noted: The COVID-19 pandemic, which exposed severe shortages in U.S. PPE supply and an over-reliance on foreign-sourced products, underscores how important it is for the U.S. government to incentivize, support and maintain domestic manufacturing capacity for PPE. Our association members, encompassing every segment of the U.S. textile, apparel and PPE supply chain, as well as unions representing workers, acted swiftly to convert manufacturing facilities and build supply chains virtually overnight to produce desperately needed PPE. We are united in our support of important principles that must be adopted in order to address our current public health needs and guarantee our nation is better prepared to respond to future emergencies. The statement was signed by the following organizations: AFL-CIO Alliance for American Manufacturing American Iron and Steel Institute American Sheep Institute Coalition for a Prosperous America Georgia Association of Manufacturers Hand Tools Institute INDA: Association of the Nonwoven Fabrics Industry Narrow Fabrics Institute National Cotton Council National Council of Textile Organizations Parachute Industry Association Rhode Island Textile Innovation Network SEAMS: Association of the U.S. Sewn Products Industry SEIU South Carolina Textile Council U.S. Industrial Fabrics Institute United States Footwear Manufacturers Association United Steelworkers Warrior Protection and Readiness Coalition Workers United/SEIU Read the full joint statement and principles: http://www.ncto.org/wp-content/uploads/2020/07/2020-07-20-Joint-Industry-Statement-on-PPE-Principles-Final.pdf Source: ncto.org * International Fiber Journal is owned by INDA, Association of the Nonwoven Fabrics Industry (inda.org).
Techtextil North America and Texprocess Americas 2020 postponed until next editions
Due to COVID-19, the organizers of Techtextil North America and Texprocess Americas have announced that the co-located events have been postponed until 2021 & 2022 respectively. “While we firmly believe that our health and safety plan exceeded all recommended guidelines to provide a safe trade show environment, several outside factors including travel restrictions, quarantine mandates and other governmental regulations across the globe have made moving forward with an in-person event impossible at this time,” Kristy Meade, Group Show Director, said in a letter to exhibitors. The next edition of Techtextil North America will take place August 15-17, 2021 in Raleigh, North Carolina. The next edition of Texprocess America will take place May 17-19, 2022 in Atlanta, Georgia and will be co-located with the 2022 edition of Techtextil North America. Source: techtextilna.com and texprocessamericas.com
European producers set for 20-fold increase in nonwoven facemask output by November
EU production of facemasks, essential for tackling the coronavirus crisis, is set to increase 20-fold by November this year compared to pre-crisis times. This means that EU-based producers will be able to make the equivalent of 1.5 billion three-layer masks a month, according to figures released by EDANA, the global association serving the nonwovens and related industries. Over the last three months, EDANA has been liaising with partner associations including MedTech Europe, ESF, and EURATEX to ensure sufficient supplies of essential public health equipment. EDANA convened a new sector group representing face mask converters, nonwoven suppliers, testing laboratories and equipment manufacturers to work together to develop an independent and self-sufficient supply chain for medical face masks and personal protective masks in the EU. The group will work to ensure adherence to applicable European Standards and to encourage responsible product stewardship throughout the life-cycle of face-masks from raw material sourcing to end-of-life solutions. Source: edana.org
HanesBrands has supplied more than 450M face coverings & 20M medical gowns to U.S. govt.
HanesBrands has completed production and distribution of more than 450 million all-cotton cloth face coverings and more than 20 million medical gowns supplied to the U.S. government for use during the COVID-19 pandemic. The company also has introduced various all-cotton, nylon, and polyester blend facemasks for consumers under its Hanes and Champion brands that are available online, in leading retail stores, and in company outlet stores. The company’s business-to-business operations are also supplying large quantity orders to organizations.
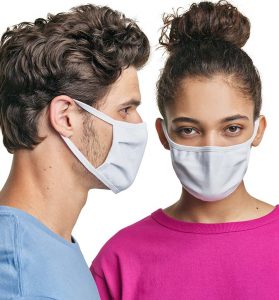
“We are proud of the commitment of our employees and our ability to quickly pivot to large-scale production of face coverings and facemasks to meet important needs during the COVID-19 pandemic,” said Michael E. Faircloth, group president, global operations, American casualwear and e-commerce. “In just three months, we were able to go from never having produced facemasks to making more than 450 million government face coverings, designing and developing branded programs of high-quality comfortable nonmedical facemasks for consumers, and safely and responsibly reopening operations to support our core innerwear and activewear businesses. We have been able to keep tens of thousands of employees in the United States and across our global supply chain gainfully employed, productive and safe during a crippling pandemic.” Hanes has introduced 3-ply all-cotton face masks for consumers in 5-count and 10-count packages available at leading mass merchandise, dollar store, grocery, drug, and home improvement retailers. Champion has introduced a lightweight 1-ply polyester-spandex blend face mask in three vibrant graphic-design patterns and colors. In mid-July, Champion will introduce a 2-ply all-cotton face mask featuring X-Temp cooling and wicking fabric. In August, Champion will introduce a 2-ply cotton-polyester blend face mask featuring adjustable nose piece and X-Temp cooling and wicking fabric. In addition to the more than 450 million cloth face coverings, the company designed, developed and produced more than 20 million washable and reusable long-sleeve medical gowns distributed to hospitals and healthcare facilities in need during the COVID-19 pandemic. Source: hanes.com
Nice-Pak wipes show efficacy against SARS-CoV-2
Nice-Pak, a producer of wet wipes, including disinfectant wipes for consumer markets, announced that it has generated data showing its products (EPA Reg. No. 9480-5) demonstrated efficacy against SARS-CoV-2, the virus that causes COVID-19. Nice-Pak’s wipes are sold under the Grime Boss brand, as well as many popular private labels. The testing was conducted in early May by Microbac, a testing laboratory that offers antimicrobial/antiviral testing for disinfectants, antiseptics, sanitizers and medical devices, and was completed in line with U.S. Environmental Protection Agency (EPA) test methods and guidelines. The data will be sent to the EPA for review and approval. If approved, Nice-Pak will update its products’ labels, providing consumers with a proven effective solution to kill the SARS-CoV-2 virus, when used according to label instructions. “As the world continues to face the COVID-19 crisis – and as Americans start to reopen businesses and public spaces – effective cleaning and hygiene solutions will remain essential,” said Jim Dalton, Vice President and Head of Research & Development, Nice-Pak. “These positive test results support Nice-Pak’s mission and commitment to protect consumers from harmful pathogens and help keep them clean and healthy.” Source: nicepak.com
OZ Health Plus inks deal with Oerlikon Nonwoven, brings first spunbond/meltblown line to Australia
Queensland Australia company OZ Health Plus will establish Australia’s first manufacturing plant to make the critical fine plastic material used in most protective facemasks. OZ Health Plus has purchased a plant of the Swiss-based technology company Oerlikon to establish a Queensland-based production plant for spunbond and meltblown nonwovens. These fabrics are essential for Australia’s facemask manufacturers, who currently produce about 500 million medical and industrial masks per year. However, the fabrics have to be imported from overseas and access to these materials has been severely disrupted during the COVID-19 pandemic. Oerlikon’s German-based business unit Oerlikon Nonwoven has now executed legal and commercial arrangements to supply the specialized machinery which can manufacture the nonwoven material locally. The plant will commence operations in April next year, with a second stage planned for late 2021. The plant will be capable of producing meltblown fabrics for 500 million masks per year, along with other medical and non-medical grade products, filtration products, sanitary items, antiseptic wipes and more. Rainer Straub, Head of Oerlikon Nonwoven said: “We are very proud that we can now for the first time supply our Oerlikon Nonwoven meltblown technology to Australia. Due to the short delivery time, we hope to make our contribution to the Australian population and their safe supply of high-quality protective masks as soon as possible.” Source: oerlikon.com/manmade-fibers
Julius Group, Noble Biomaterials partner to develop antimicrobial gloves & masks
Julius Group, a manufacturer of gloves and fashion accessories, and Noble Biomaterials, a provider of aantimicrobial and conductivity solutions for soft-surface applications, announced a strategic partnership to produce reusable antiviral/antibacterial gloves and masks for consumer use. Amid the global pandemic, the companies are partnering to allow Julius Group to manufacture PPE using Noble Biomaterials’ powerful Ionic+ antimicrobial technology. The reusable antimicrobial gloves and masks will be made with fabric that incorporates 99.9% pure silver, which provides a dramatic reduction in virus infectivity on soft surfaces. These consumer products will be released through InnoTier, a company recently launched by Julius Group. “We believe that a truly innovative approach to technology can have a big impact on the world,” said Juliana Lam, Chairman of Julius Group and Founder and President of InnoTier. “It can impact people and the planet and ensure a sustainable future for all. We also believe that we can only do this with a truly global mindset.” Noble Biomaterials’ infection-prevention textile technology has been used globally for decades in healthcare environments to reduce the growth of microbes and protect soft surfaces such as privacy curtains, bedding, scrubs and lab coats. Source: juliusgroup.com & noblebiomaterials.com
AATCC offers blotting paper for use with PPE testing
With the rise in production and testing of medical personal protective equipment (PPE), access to correct testing apparatus and materials is critical. AATCC now offers a one-stop shop for impact penetration testing needs, including blotting paper suitable for AAMI PB70 classification testing. AAMI PB70 Level 1-3 certification and testing requires using AATCC TM42, Test Method for Water Resistance: Impact Penetration along with a blotting paper that matches the paper specifications included in the AAMI PB70 standard. Blotting paper can be ordered at: https://members.aatcc.org/store/blotting15x225/3074/ Source: aatcc.org
Berry partners with Medicom to support facemask production in Britain
Berry Global announced its partnership with The Medicom Group to support a commitment to the British government in producing facemasks. Berry Global is undertaking efforts to enhance the production capacity of protective material with investment in a new meltblown nonwoven line at one of its manufacturing facilities located in the United Kingdom. The company will work on incorporating its proprietary charging technology into this production line for delivering optimal filtration efficiency. This will help it cater to growing demand for protective material, suitable for the manufacturing of Type IIR and N99-identical FFP3 masks, conforming to European standards. Medicom’s European Kolmi brand will make these masks and sell the finished products in the market. This latest strategic move highlights Berry Global’s increased participation in the fight against the coronavirus outbreak. Notably, in May 2020, the company made efforts to drive its global Meltex meltblown capacity with the inclusion of an additional meltblown asset in Berlin for the production of high-efficiency filtration media. This production line will aid in catering to growing customer demand for the material conducive to premium applications including FFP2 (N95) and FFP3 (N99) for the facemask markets. Source: berryglobal.com
AATCC warns against claims of COVID-19 protection in textiles or related materials
The uncertainties surrounding COVID-19 and the best response for safety and Personal Productive Equipment (PPE), has many understandably concerned. However, AATCC issued a statement warning against misleading, false or ill-informed product claims concerning protection against the novel coronavirus SARS-CoV-2 or COVID-19 in textiles or related materials. AATCC said using TM100 or TM147 to demonstrate efficacy against viral activity is not the correct application for the methods, as they evaluate bacterial activity. Any claims that AATCC endorses or certifies a product to protect against COVID-19 is a false statement, noted the association. Successfully passing AATCC TM100 or AATCC TM147 has no bearing on whether a product will prevent or protect against the COVID-19 virus. While a predictor of functionality, if someone promises or alludes that their textile-related product will defend against COVID-19 solely because it passed one or both of these methods, caution is advised. At this time, there are no AATCC textile testing methods or approved modifications of AATCC testing methods that are available for measuring antiviral activity of textiles against SARS-CoV-2. Source: aatcc.org
Suominen introduces new material for EN Type II facemasks
Suominen has developed a nonwoven material for the manufacturing of facemask applications. The new nonwoven has passed European Standard EN 14683:2019 Type II requirements in terms of filtration efficiency and pressure drop. “Our FIBRELLA Shield nonwoven has excellent filtration efficiency and pressure drop values meaning that the material provides protection while being comfortable and easy to breathe through. Measured with an applied method by VTT* results indicate that FIBRELLA Shield nonwoven’s filtration efficiency is higher than 99% reaching type II requirements but of course the material can also be used for lighter model Type I masks or uncertified masks,” said Category Manager, Johanna Sirén. The standard EN14683:2019 for medical masks is for end products and the converter has to repeat the tests to confirm the standard compliancy for the end product. The end product needs to comply also with the regional regulations, if any. Developed in cooperation with VTT, this new material is the latest addition to the FIBRELLA family. FIBRELLA Shield is already in production at Suominen’s Nakkila plant. Currently the plant is capable of producing material for approximately 15 million masks per month. Source: suominen.fi/en/
Hollingsworth & Vose introduces new material for nonsurgical medical gowns
Looking to help meet the critical need for Personal Protective Equipment for healthcare workers during the COVID-19 pandemic, global manufacturer Hollingsworth & Vose has, on a rapidly accelerated timeline, developed a new material for non-surgical medical gowns. Using standard construction methods, this new material can be converted into medical gowns for healthcare workers in hospitals, nursing homes and other medical facilities. The material meets stringent testing including the AATCC 42 impact penetration and AATCC 127 hydrostatic pressure tests. Its origin stems from a COVID-19 related task force that H&V convened at the start of the pandemic to see how the company could expand production and help meet the shortage of medical grade PPE. H&V works across industries, including in medical, automotive, energy, power generation, and air quality. Source: hollingsworth-vose.com
Study shows layered system of commonly available fabrics outperforms N95 respirator in filtration efficiency
A new study by Northeastern University found that a facemask constructed using fabrics manufactured by AKAS Textiles, a Pennsylvania-based textile manufacturer, outperformed an N95 respirator in an aqueous media under positive pressure of 20 Kilo Pascal, simulating a sneeze/cough. The study tested more than 70 different common fabric combinations and masks, including the N95 respirator, for their ability to block the transmission of virus-like nanoparticles. The mask with the best filtration was made of layers of ProCool Performance Fabrics combined with Zorb 3D Stay Dry Dimple fabric. The combination of these fabrics tested 72% more effective than the N95 respirator. The study was published in ACS Nano, a monthly, peer-reviewed scientific journal published by the American Chemical Society. The authors wrote, “Layered systems of commonly available fabric materials can be used by the public and healthcare providers in face masks to reduce the risk of inhaling viruses with protection that is about equivalent to or better than the filtration and adsorption offered by 5-layer N95 respirators. The mask swere evaluated with steady-state, forced convection air flux with pulsed aerosols that simulate forceful respiration”.

The study was done at 14 Liters per minute air flow, which is more than twice the human ventilation, at rest. ProCool Performance Fabrics are two-sided fabrics which are inter-knitted to provide filtration. The special wicking fibers in it help in managing the moisture. Zorb 3D Stay Dry Dimple is made with surface layers of wicking Stay Dry fibers with an innermost core of dense cellulosic fibers, which work as the filter. The three-dimensional engineered pattern provides great filtration and keeps the mouth area dry and fresh, according to AKAS Textiles. Read the research report published in ACS Nano: http://www.stevelustig.com/CV/COVID-Nano-preprint.pdf Source: akastex.com
Textile treatment proves effective against SARS-CoV-2 in lab tests
HeiQ’s Viroblock NPJ03 is among the first textile technologies in the world to be proven effective against SARS-CoV-2 in the laboratory. Tests conducted by Swiss textile company, HeiQ, with the Peter Doherty Institute for Infection and Immunity in Melbourne, Australia (Doherty Institute), showed that treated fabric achieved 99.99% reduction of the virus. HeiQ Viroblock NPJ03 is a textile treatment for industrial use, designed to provide textiles with antiviral and antibacterial properties. The combination of silver antimicrobial technology and vesicle technology rapidly destroy enveloped viruses including coronaviruses. It has previously been tested against coronavirus 229E, another strain of virus in the Coronavirus family.
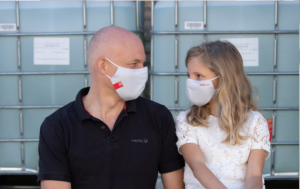
The latest testing with SARS-CoV-2 virus was conducted by researchers at the Doherty Institute, a joint venture between the University of Melbourne and The Royal Melbourne Hospital, an internationally renowned institution combining research, teaching, public health and reference laboratory services, diagnostic services and clinical care into infectious diseases and immunity. The research project involved a disinfection test protocol that simulated the real-life interaction of small aerosol droplets contaminating clothing. A known concentration of SARS-CoV-2 virus was contacted with the sample fabric for 30 minutes followed by measurement of remaining infectious SARS-CoV-2 viruses. The fabric sample treated with HeiQ Viroblock NPJ03 had no infective viruses left after 30 minutes. The result indicated a SARS-CoV-2 virus reduction of 99.99% relative to the inoculum control. Source: heiq.com & doherty.edu.au
Research shows facemask textiles directly inactivate SARS-CoV-2
Researchers from Freie Universität Berlin at the Institute for Animal and Environmental Hygiene and the Institut für Textiltechnik (ITA) of RWTH Aachen University are collaborating on the topic of alternative personal protection equipment. The testing was conducted in the context of the EIT Health Project ViruShield, supported by the European Union, with the objective to discover alternative filter materials for facemasks in light of tight supply and globally imbalanced supply chains for personal protective equipment.
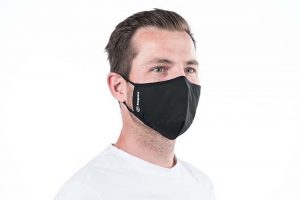
The Swiss company Livinguard has developed a treatment for textile facial masks that can directly inactivate bacteria and viruses, according to the researchers. While researchers at the Institut für Textiltechnik (ITA) of RWTH Aachen University conducted experiments on the chemical and physical properties of various textiles for face masks, researchers at Freie Universität Berlin were able to demonstrate that these new textiles can reduce high amounts of SARS-CoV-2 virus particles by up to 99.9% within a few hours. The principle underlying the Livinguard Technology is that the textile surface has a strong positive charge. When microbes come into contact with the technology, the microbial cell, which is negatively charged, is destroyed, leading to permanent destruction of the microorganism. Unlike alternative metal-based solutions, the novel technology has been found to be safe for both skin and lungs. Moreover, Livinguard Technology is very sustainable, allowing users to reuse the mask up to 200 times with no reduced impact on safety or efficacy. Source: ita.rwth-aachen.de & livinguard.com
Germany marks launch of meltblown funding program with Innovatec, Oerlikon in support of facemask production
Germany’s Federal Minister of Economics Peter Altmaier today handed over the first notice of funding to Innovatec GmbH in Troisdorf as part of the recently launched “Nonwoven Production” funding program. The North Rhine-Westphalian company intends to produce an additional 1 500 tons of nonwoven per year in the future with the two newly installed subsidized meltblown lines of which one is from Oerlikon Nonwoven. The additional volume will enable the production of more than 1.5 billion protective masks.
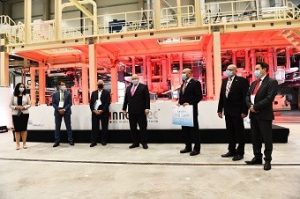
Photo: Matthias Hoffman
Innovatec GmbH, the self-proclaimed largest nonwoven manufacturer in Europe, has invested a two-digit million Euro amount in two new production lines for meltblown nonwovens. Both lines are “made in Germany” – and one line comes from Oerlikon Nonwoven in Neumünster. “We are very proud to have been involved in this project from the very beginning and to be able to actively support such an important nonwoven producer as Innovatec with our meltblown technology”, explained Rainer Straub, Head of Oerlikon Nonwoven. Source: oerlikon.com
Facemask line capable of producing up to 1M disposable surgical masks per day with a lower-cost design
The W+D/BICMA hygiene group of Winkler+Dünnebier has developed a fully automatic, high-speed facemask converting line for the production of high-quality disposable face masks. This new converting line will be able to produce masks for surgical-grade applications. It is capable of producing 800 facemasks per minute, but with a lower cost mask ear loop design.
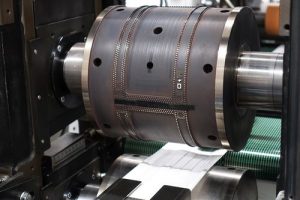
The new AUXILIUM FM has a speed of up to 150 m/min (492 ft/min) and is able to produce up to 1 million high quality face masks per day. Adding to the manufacturing throughput efficiency is a unique lower-cost mask design capability for an expensive component of the mask, which maximizes the capabilities of lowest cost per piece mass production. There are also different options available for mask stacking and automation, which make this mask machine best suited for Industry 4.0 manufacturing. The new mask line produces and laminates three fabrics (spunbond, meltblown, thermo-bonded nonwovens and others). It utilizes W+D/BICMA’s technology in automatic unwinding and splicing for nonwoven webs, cutting and positioning devices for the metal nose bar, and heat and ultrasonic edge welding. Source: bicma.com
Lydall adds fine fiber meltblown line for filtration media for N95, surgical and medical facemasks
Lydall, a manufacturer of value-added engineered materials and specialty filtration solutions, announced an investment in an additional fine fiber meltblown asset in response to the exponential increase in domestic and global demand of specialty filtration media for facemasks. This new production line will enable Lydall – one of the few American manufacturers capable of producing high-quality fine fiber meltblown filtration media for N95, surgical and medical facemasks – to significantly increase its supply and help alleviate the shortage of meltblown materials, both in the U.S. and internationally. “In the wake of COVID-19, the need for the filtration media that makes facemasks effective has increased dramatically, so much so that it is now being called the ‘golden fleece,’” Sara A. Greenstein, President and CEO of Lydall, said. “As one of the only companies in North America and Europe with the technical expertise, supplier relationships and access to the right machines to produce this filtration media, we feel great responsibility to do everything within our power to increase our output, support domestic supply chains and contribute to the global fight against COVID-19. This investment is one example of Lydall’s commitment to do just that.” The new asset will complement Lydall’s existing global meltblown capacity and is estimated to supply the filtration media for one billion face masks per year, almost a third of the 3.5 billion that the U.S. Department of Health and Human Services has projected as necessary to protect healthcare workers. Lydall expects commercial production to begin in its Rochester, New Hampshire facility in the fourth quarter of 2020 and plans to hire up to 15 additional employees to support the increase in production. Source: lydall.com For more on Lydall’s COVID-19 relief effort: https://lydall.com/covid-19-relief-effort
FET conducting trials, aims to provide more meltblown material options for medical and PPE applications
Fibre Extrusion Technology (FET), a Leeds, UK-based specialist in process solutions and equipment for the manmade yarns and fiber extrusion industry, has received unprecedented enquiries about its nonwoven meltblowing systems since the onset of the COVID-19 pandemic, according to the company. “We’re currently running trials, preparing samples and defining specifications for companies in Germany and Italy, as well as the UK, and we could already have sold the lab line we have here many times over,” says managing director Richard Slack. “It’s primarily designed for R&D and pilot scale applications, but trials have proven it to be suitable for the low volume production of critical meltblown face mask materials. Some of the customers to whom we’ve supplied similar lines have already pivoted their production to this, which has generated further interest.” The company is positioning itself as a service provider to nonwoven companies who may be exploring alternatives to polypropylene in meltblown, leveraging its expertise with a wide range of fiber types for medical applications and sustainable alternatives for facemasks and PPE. Source: fetuk.com
Rieter reports low demand due to COVID-19 pandemic
Rieter, a leading supplier of systems for short staple fiber spinning, issued a statement indicating that since the end of March 2020 there as been low demand for spare parts and wear & tear parts and delays in testing programs during the development of new machines, as a result of the COVID-19 pandemic. According to the company, customers are postponing investment projects or unable to implement them due to restrictions imposed by national governments. This has resulted in low demand for new machines, and Rieter is implementing crisis management, including short-time working at its facilities in Switzerland and Germany, and is predicting mid double-digit million losses in the first half of 2020. Source: reiter.com
Huntsman, Bao Minh partner to produce high-grade isolation gowns in support of COVID-19 response
Huntsman Textile Effects and Bao Minh Textile, one of the largest woven fabric producers in Vietnam, are collaborating to produce fabric that meets the stringent performance standards required of isolation gowns. High-quality medical gowns are essential protective wear for healthcare workers combatting the global COVID-19 pandemic, but they are in short supply worldwide. Bao Minh Textile will initially treat 760,000 meters of woven fabric with a carefully curated combination of Huntsman Textile Effects barrier effect solutions and auxiliaries. This fabric is sufficient to produce 345,000 high-grade isolation gowns. Bao Minh Textile’s isolation gown fabric relies on a range of Huntsman pretreatment, dyeing and finishing solutions. These include CLARITE ONE, an all-in-one pretreatment for peroxide bleaching; NOVACRON and TERASIL dyes; PHOBOL CP-C, an excellent oil-, water- and stain-repellent finish; and PHOBOTEX RSY, a non-fluorinated durable water repellent with extremely high washing resistance. PHOBOL EXTENDER XAN is also applied to further increase wash durability. Source: huntsman.com
Berry announces capital investment in meltblown capacity in South America
Berry Global Group announced the capital investment in its global meltblown nonwoven fabric capacity for South America. This investment further strengthens the Company’s global reach and position as the leading nonwovens manufacturer. This line is Berry’s first meltblown asset, based on its Meltex technology, to be located in South America and continues to support the demand for health and wellness products. With continued demand for face masks globally, Berry has been working closely with customers to help ensure production and supply. The investment will bring more than 400 metric tons of Meltex™ meltblown nonwoven material to the region, which will enable production of more than 500 million surgical-grade masks per year. The new asset will be operational in the March 2021 quarter, will be placed at an existing Berry production facility in South America, and will focus on the production of materials for ASTM L2, L3, and N95 masks. The new line will be upgraded with Berry’s patented charging technology post installation. Source: berryglobal.com
Johns Manville begins producing nonwoven material for Level 3 medical gowns
The Johns Manville plant in Spartanburg, South Carolina, has started production to make nonwoven fabric that will be used for manufacturing of urgently needed disposable medical gowns used in the fight against the spread of COVID-19. This is the second move by Johns Manville to quickly develop and launch a product to support the response COVID-19 virus. In April, production started in Richland, Mississippi, of nonwoven media for the manufacturing of face masks. “Given the urgent need for action,” Vasuta said, “we quickly decided to build on our own capabilities and develop a coated product to supply the domestic medical gown manufacturing industry.” The new polyester spunbond nonwoven is designed for the production of Level 3 medical gowns. “The fabric offers superior liquid barrier performance compared to materials used for Level 1 and Level 2 medical gowns, while also providing comfort and stitch-strength,” said Souvik Nandi, Director Nonwovens Technology at Johns Manville Engineered Products. The new fabric is formally known as Evalith® 017/120H3 and is a coated continuous filament, calendared polyester nonwoven. It meets the requirements for a Level 3 medical gown as established by ANSI/AAMI PB70:2012 Liquid barrier performance and classification of protective apparel and drapes intended for use in health care facilities. Per this standard, the material was tested to AATCC 42-2017 Water Resistance: Impact Penetration Test and AATCC 127-2017 Water Resistance: Hydrostatic Pressure Test. Additionally, Evalith 017/120H3 has been tested to and meets the flammability standard per 16 CFR Part 1610 Class 1, according to the U.S. Food and Drug Administration policy and guidance. Source: jm.com
Pitt researchers create durable, washable textile coating that can repel viruses
Masks, gowns, and other personal protective equipment (PPE) are essential for protecting healthcare workers. However, the textiles and materials used in such items can absorb and carry viruses and bacteria, inadvertently spreading the disease the wearer sought to contain.
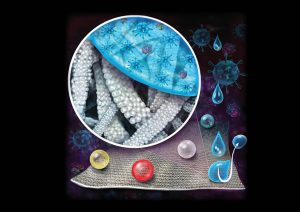
When the coronavirus spread amongst healthcare professionals and left PPE in short supply, finding a way to provide better protection while allowing for the safe reuse of these items became paramount. Research from the LAMP Lab at the University of Pittsburgh Swanson School of Engineering may have a solution. The lab has created a textile coating that can not only repel liquids like blood and saliva but can also prevent viruses from adhering to the surface. The work was recently published in the journal ACS Applied Materials and Interfaces. Read the full story: https://www.engineering.pitt.edu/News/2020/Virus-Repelling-Textile-Coating/ Source: engineering.pitt.edu Related article: https://fiberjournal.com/wipes-in-the-age-of-covid-19/
Oerlikon to supply meltblown nonwoven systems to support manufacture of 50M respiratory masks per month for European market
FleeceforEurope, a newly established partnership between Lindenpartner, Düsseldorf-based Kloepfel Group and Berlin-based industrial consultancy, Bechinger & Heymann, is set to make 50 million class FFP1 through FFP3 respiratory masks a month using Oerlikon Nonwoven’s high-end meltblown technology. The initiative aims to manufacture and distribute masks exclusively for the European market from the beginning of fall. Meltblow nonwoven material is in high demand to provide the protection required of class FFP1 through FFP3 respiratory masks. Source: oerlikon.com/en/brands/nonwoven/
Cotton and textile sectors call for collaborative action as they aim to recover from COVID-19 pandemic
The Better Cotton Initiative (BCI), The Committee For International Co-Operation Between Cotton Associations (CICCA), The International Cotton Association (ICA), The International Cotton Advisory Committee (ICAC) and the International Textile Manufacturing Federation have announced an initiative to establish “a common set of values and shared commitment to safe trading and contract sanctity across the global cotton community.” The collaboration is a response to the challenge of ensuring that fair and equitable trade practices govern the commercial relationships throughout the cotton and textile supply chains. “We believe that these principles have never been more important than they are now,” noted the organizations in a statement. “The loss of demand resulting from COVID-19 and the preventative measures that are being applied throughout the world affects the cotton and textile sectors from end to end. It is essential for each trading partner to be mindful of each other’s position. We must strive to find mutual agreements which keep in mind our shared commitment to the long-term health of the international cotton and textile trade, and to the principles of fair and equitable trading practices on which it is built.” The organizations are calling for those engaged in the cotton and textile value chains to commit to: • Take actions that are considered and designed to contribute to the recovery of the cotton and textile sectors in 2021 and beyond • Communicate, collaborate and be responsive to the needs of their counterparties • Continue to respect the trade rules that govern the sectors • Recognize and publicize positive behaviors. Identify and call out negative, counterproductive commercial behaviors. Source: itmf.org
Jumpstart ramps up production for personal protective apparel
Jumpstart Consultants, Inc., has increased capacity at its U.S.-based manufacturing center to include personal protective apparel fabric production to their current capabilities mix which normally supplies the building envelope, roofing, floor protection, and industrial packaging markets. Jumpstart manufactures a variety of converted rollstock goods which meet the stringent ANSI PB70, Level 3 standards for protective apparel used in healthcare facilities. Jumpstart rollstock can be used by converters to produce typical PPE articles such as surgical gowns, isolation gowns, other protective apparel, surgical drapes, and drape accessories. Multiple grades are available, including both polypropylene and polyester spunbond nonwoven fabric structures in various customer-specified product widths. “The variety of Jumpstart products which comply with the ANSI PB70 standard provides PPE converters with unique choices for breathable, water resistant rollstock,” said Chris Shepherd, Executive Vice President of Jumpstart Consultants, Inc. “We are pleased to leverage a uniquely diversified raw material supply chain and a flexible manufacturing platform in the US to support the present critical need for PPE materials for our health care system.” Source: jumpstartinc.net
Fitesa inks deal with Reicofil to expand its PPE capacity worldwide
Fitesa signed four new projects with technology supplier Reicofil. The package includes state-of-the-art equipment that will significantly increase capacity to serve the healthcare and hygiene markets, making nonwovens for medical gowns, drapes, surgical and N95 facemasks, diapers and sanitary products. According to Fitesa, the exact locations of these projects will be disclosed in due time, but the intent is to strengthen the company’s global footprint without focus on any one region. Source: fitesa.com
INDA launches portal highlighting nonwovens industry’s efforts in responding to COVID-19
INDA, the Association of the Nonwoven Fabrics Industry, launched a new portal on its website highlighting its member companies who are working to support the COVID-19 response worldwide. The portal, called “Allies Against COVID-19” is designed to connect suppliers with buyers and increases awareness of actions by nonwoven & engineered fabric producers in the fight against COVID-19. The website details such actions from 71 INDA member companies that span the entire supply chain. The actions range from advancement in cutting edge viricidal and antimicrobial treatments to increased capacity and through-put to manufacture facemasks, gowns, disinfectant wipes, and community outreach. Companies are listed alphabetically and include contacts and website links. “INDA is a resource connector in this effort to provide the necessary PPE materials and disinfectant wipes to combat the COVID-19 pandemic. We’re witnessing fast and strong contributions by the nonwoven & engineered fabrics community in this effort. INDA is proud to support our members by giving notice to their efforts to contribute to this noble cause,” said Dave Rousse, INDA President. View the portal: https://www.inda.org/indamembers/covid.html Source: inda.org * International Fiber Journal is owned by INDA, Association of the Nonwoven Fabrics Industry
Scramble for masks sees demand soar for Germany’s ‘golden fleece’
Forget gold, copper, silver and steel. The hottest commodity of the coronavirus crisis is a little-known synthetic fabric called meltblown. Used to make the medical masks that protect front-line hospital staff the world over from Covid-19, it is now so valuable that it has been nicknamed the “golden fleece”. European producers can barely believe the amounts Asian buyers are prepared to pay for the stuff. “One Hong Kong trader was recently offering €100 per kilogram — ten times the pre-crisis price,” said Pierre Wiertz, head of Edana, the global trade association for manufacturers of nonwovens. Read the full story: https://www.ft.com/content/b26e82b8-97ab-495b-a0ab-203708868f9b (subscription required) Source: ft.com
The Nonwovens Institute announces COVID-19 webinar series
The Nonwovens Institute will be presenting a series of six webinars providing critical technical information and insight on the value and importance nonwovens technology for infection prevention. The first webinar, “The Anatomy of N95 and Surgical Masks,” will take place May 20, 2020, 11:00am – 12:00pm EDT. Registration is free for NWI Members and $50.00 for nonmembers. Dr. Behnam Pourdeyhimi, the executive director of the The Nonwovens Institute, will examine the specific materials, construction, and performance of various facemasks in light of the current Covid-19 pandemic. He will discuss the key attributes of nonwovens technology and their effect on filtration efficiency and user protection. Registration Link: https://reporter.ncsu.edu/link/courseview?courseID=NWI-WBR-01&deptName=NWI Other webinar topics include:
- Webinar #2: Air and Aerosol Filtration Basics
- Webinar #3: Meltblown Fabrics and Process in PPE
- Webinar #4: Spunbond Fabrics and Process in PPE
- Webinar #5: Gowns
- Webinar #6 Wipes and Other Products for PPE.
Source: thenonwovensinstitute.com
Techmer PM develops technology to help meltblown fabrics maintain electrical charge
As demand surges for facemasks during the COVID-19 pandemic, Techmer PM, LLC, has developed a technology to improve the efficacy of the fabrics used in the production of such masks. The technology, called the Charge Enhancer, is used during the production of meltblown nonwoven fabrics to help the resulting masks meet the filtration performance requirements set forth by ASTM F2100. Techmer PM provides its Charge Enhancer in pellet form to producers of meltblown nonwovens, who then add it to polypropylene in a concentration of 4- 5%. As the extruded nonwoven comes off the production line in roll form, the material is subjected to an electrical charge via an air plasma treatment, also known as “corona” charging (no relation to the coronavirus). The Charge Enhancer technology helps the meltblown fabric enhance and retain the electrical charge imparted by corona charging. “Without the Charge Enhancer, the mask media would struggle to retain a filtration efficiency of ≥95%,” said Bhushan Deshpande, Techmer PM’s vice president of technology. Techmer PM is also testing new technology designed to provide more permanent charge-enhancing effects compared to what is currently available. “This newer technology will be well suited for mask manufacturers looking to develop reusable masks,” according to Deshpande. Source: techmerpm.com
Midwest Textiles, Hollingsworth & Vose partner to develop homemade facemask kit
Midwest Textiles and Hollingsworth & Vose (H&V) are collaborating on a new ready-to-sew face mask kit for the general public. The new collaboration between Midwest and H&V offers an improvement to the everyday consumer by adding a layer of Nanoweb FM to the mask. Nanoweb FM is new filtration media made by H&V, designed for use in homemade face masks. “H&V is one of the world’s leading producers of filtration media for face masks and many other filtration applications. By partnering with Midwest, and through the development of Nanoweb® FM media, we are able to help support individuals and communities across the country that are struggling to obtain basic levels of protection,” said Mike Clark, Division President at H&V. “Our new Nanoweb® FM media was designed specifically for general use in homemade face masks, and can be inserted in a face mask pocket or stitched into a disposable pleated mask.” Consumers can purchase ready-to-sew face mask kits and Nanoweb® FM media for homemade masks at www.sitnsewfabrics.com. One kit containing 4 masks will cost $24.95, and it is estimated to take 15 minutes to sew and assemble each mask. Source: hollingsworth-vose.com & midwest-textiles.com
Bondex ramps up production of material for PPE & N95 facemasks
To support the industry demand for PPE materials, Bondex, a producer of carded thermalbond, hydroentangled and needlepunch nonwovens, is dedicating a portion of its capacity to produce materials designed for use in N95 mask construction and materials for use in isolation gowns and other PPE applications. Bondex develops a polypropyelene nonwoven that is used in both mask and isolation gown applications, as well as hydroentangled polyester that is also used in the construction of mask materials. “We have implemented plans as necessary to continue our supply to our customers though the pandemic crisis,” says Bondex president Brian Little. “We have also recognized the needs in society to help battle this COVID-19 pandemic so we are adding staff in order to supply technical nonwovens for selected PPE applications in order to support these key initiatives.” Source: bondexinc.com
ITMF study shows impact of coronavirus pandemic on the global textile industry
The International Textile Manufacturing Federation (ITMF) has conducted a survey among ITMF Members about the impact the Corona pandemic had on the global textile value chain, especially on current orders and expected turnover in 2020. In total 34 companies from around the world participated in addition to two national textile associations with several hundred participants. The results show that on average companies in all regions of the world suffered significant numbers of cancellations and/or postponements. On world average, current orders dropped by -8.0%. The decrease in orders ranges from – 4.0% in South America to -13.3% in Africa. Part I results: https://itmf.org/images/dl/press-releases/2020/Corona-Survey-1st-2020.04.01-Press%20Release-FINAL.pdf Part II results: https://itmf.org/images/dl/press-releases/2020/Corona-Survey-2nd-2020.04.06-Press%20Release-FINAL.pdf Part III results: https://itmf.org/images/dl/press-releases/2020/Corona-Survey-3nd-2020.04.29-Press%20Release.pdf Source: itmf.org
NCTO calls for Executive Order instituting ‘Buy American’ policy for PPE materials
National Council of Textile Organizations (NCTO) President and CEO, Kim Glas, issued a statement urging the government to institute “Buy American” policy changes to help bolster U.S. manufacturers producing personal protective equipment (PPE) for frontline workers battling the COVID-19 pandemic. “If the government is sincere about reconstituting a U.S. production chain for medical personal protective equipment (PPE) to resolve the drastic shortages we are experiencing during the current pandemic, it is going to have to make key policy changes to help incentivize domestic production,” said Glas. “A strong Buy American mandate for these vital healthcare materials needs to be instituted for all federal agencies, coupled with other reasonable production incentives, to help ensure a strong U.S. manufacturing base for these essential products.” Citing the U.S. Department of Defense’s fiber-to-finished product Buy American rule for military textiles, Glas said the model for such a program is already in place for the military and would just need to be replicated to ensure the supply of PPE during emergencies like the COVID-19 pandemic. “Expanding domestic purchase requirements through Executive Order and other legislative initiatives will ensure that PPE production through U.S. supply chains that have been created overnight don’t evaporate as soon as this crisis is over,” said Glas. Read the full NCTO statement: http://www.ncto.org/ncto-urges-government-to-institute-buy-american-policy-to-boost-manufacturing-of-personal-protective-equipment/ Source: ncto.org
Oerlikon to produce 1M facemasks per month; takes significant orders for meltblown technology
Oerlikon Nonwoven converted its R&D laboratory systems in Neumünster, Germany, in early March to manufacture nonwovens to provide oronasal facemasks to small local businesses and local companies. The laboratory system at the R&D Center is normally used solely for research and customer trials. It was never conceived for continuous operation in its original form. Now Oerlikon Nonwoven has made further investments in order to enable continuous operation in the laboratory. With this, material for more than one million protective masks a month can be manufactured. Since the beginning of the coronavirus crisis, the company has received more than 500 inquiries that we are progressively dealing with. The laboratory has run out of raw materials and new orders for replacement materials had to be placed before Easter – with current delivery times of approx. three weeks. Once raw materials arrive, production will be resumed and considerably expanded in May. Oerlikon has partnered with companies to convert the raw materials into masks for end use. Oerlikon Nonwoven has also fired up the production of the machines and systems used for its meltblown technology. The demand from Germany, Europe and the rest of the world has quickly secured the company a boom in orders, reaching in the mid-range double-digit millions. The company will be commissioning the first meltblown system at the site of a leading Western European nonwovens producers in the second quarter of 2020. This system will be deployed exclusively in the manufacture of nonwovens for respiratory masks. Source: oerlikon.com/manmade-fibers
A mathematical approach to meltblown production efficiency
Nonwovens production is currently attracting more attention than ever before from the general public, because in times of the corona pandemic, nonwovens are vital for infection protection in the medical sector and also for the protection of the entire population. Disposable bed linen in hospitals, surgical gowns, mouthguards, wound protection pads and compresses are some examples of nonwoven products. Especially in intensive care and geriatric care, disposable products made of nonwovens are used due to the special hygiene requirements. At the moment there are clear bottlenecks in the production of these materials. For the meltblown nonwovens class, however, it is difficult to increase production efficiency because meltblown processes are highly sensitive to process fluctuations and material impurities. Although nonwovens are not all the same, the rough principle of their production is relatively similar to all industrially manufactured nonwovens: molten polymer is pressed through many fine nozzles, stretched and cooled down in an air stream and thus deposited into the typical white webs. “Meltblown” stands for the submicron fiber process whose nonwovens are responsible for the decisive filter function in face masks.
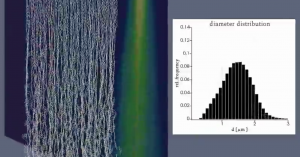
With meltblown technology, nonwoven fabrics are produced directly from granules. A special spinning process in combination with high-speed hot air is used to produce fine-fibered nonwovens with different structures. The fibers are highly stretched by the turbulent air flow. During this process they swirl in the air, become entangled and fall more or less randomly onto a conveyor belt where they are further consolidated – a very complex process. Nonwovens manufacturers around the world are striving to massively increase their production capacities. This is where Fraunhofer ITWM’s software comes into play. “Our Fiber Dynamics Simulation Tool FIDYST is used to predict the movement of the fibers, their falling and the orientation with which they are laid down on the conveyor belt. Depending on the process settings, turbulence characteristics are generated and thus nonwoven qualities are created that differ in structure, fiber density and strength,” explains Dr. Walter Arne from the Fraunhofer ITWM. He has been working at the institute for years on the simulation of various processes involving fibers and filaments. The methodology is well transferable to meltblown processes. In these processes, one of the specific features is the simulation of filament stretching in a turbulent air flow – how the stretching takes place, the dynamics of the filaments and the diameter distribution. These are all complex aspects that have to be taken into account, but also the flow field or the temperature distribution. The simulations of the scientists at the Fraunhofer ITWM then provide a qualitative and quantitative insight into the fiber formation in such meltblown processes – unique in the world in this form when it comes to simulate a turbulent spinning process (meltblown). Read the full story: https://www.itwm.fraunhofer.de/en/press-publications/press-releases/2020_04_22_meltblown-nonwoven-infection-protection.html Source: itwm.fraunhofer.de
Lenzing, Palmers form new company, Hygiene Austria, with a focus on protective mask production
Lenzing AG and Palmers Textil AG found “Hygiene Austria LP GmbH”, in which Lenzing AG holds 50.1% and Palmers Textil AG 49.9%. The newly founded company will start producing and selling protective masks for the domestic and European markets from May 2020. Over the past few weeks, Lenzing AG and Palmers Textil AG have invested several million euros in a modern production infrastructure at the Wiener Neudorf location and secured the corresponding raw materials for protective masks production. In a first step, the company produces so-called mouth-nose protective masks (MNS) and surgical protective masks of class EN14683. Hygiene Austria LP GmbH plans to increase its capacities to over 25 million masks per month over the next few weeks and to expand this business geographically as well. The demand for high-quality MNS and respiratory masks for medical personnel is increasing rapidly, and there is real competition on the international market for these products. In order to sustainably secure domestic supply now and in the future and to strengthen the business location, the two companies Lenzing AG and Palmers Textil AG have now set a milestone with their own competence center for hygiene based in Austria. Hygiene Austria LP GmbH thus makes a significant contribution to combating the Covid-19 pandemic and ensures the long-term supply of these critical goods in Austria in high quality. “We decided to pool our knowledge, network and experience in a competence center for hygiene together with our partner Palmers. The aim of this joint venture is to provide the citizens of Austria and Europe with the best possible protection through locally manufactured, high-quality products,” says Stefan Doboczky, CEO of Lenzing AG. „Masks will continue to play an important role in our daily lives and we are proud that we were able to achieve our goal of an industrial production so quickly together with our partner Palmers.” Read the full story: https://www.lenzing.com/newsroom/press-releases/press-release/lenzing-and-palmers-join-forces-to-fight-coronavirus Source: lenzing.com
KARL MAYER proving machines to manufacture up to 250k facemasks per month
KARL MAYER is working with industry partners to ramp up facemask production, leveraging its double needle bar raschel machine to enable the production of roughly a quarter of a million masks per month. The masks are produced entirely without the need of any sewing work. Two models are available for the various demands. Type 1 is produced at short notice and is suitable for everyday life. Due to their 3D shape, these masks have a tight fit and good wearing properties. They offer a convenient air exchange, a soft skin feeling, and prevent friction points on the ears, even after long-term use. The masks can be reused after their utilization. Simply wash and dry them, and the next application can start immediately. Type 2 provides all the advantages of type 1, but it can be equipped with a replaceable nonwoven lining via a pocket. This increases the filtration capacity, at the same time ensuring minimum waste after use. Regarding the filtering effect, the certification process is currently underway for a medical standard for both mask types. To ensure a fast use of the face masks in Germany, KARL MAYER equipped a customer with the required machine technology and the instructions for the production of the masks. The mask manufacture will start by the end of April. Once the installed KARL MAYER machine is running at full speed, it is possible to produce up to 400 masks per hour or 240,000 pieces per month. At the same time, KARL MAYER is working on reducing the production time for additional machines, so that capacity can be increased as quickly as possible. By mid-May we can achieve a production of up to half a million masks per month. Source: karlmayer.com
Essity ramps up facemask production
Essity, a Stockholm-based provider of health and hygiene products, has acquired three new machines for large-scale production of facemasks to support COVID-19 response efforts. With this investment, the Essity will be producing facemasks in factories in Mexico, Sweden and the United States. “The demand for facemasks in the fight against COVID-19 is substantial and with this investment we hope to meet some of this demand. Contributing to society is one of our key priorities under the current circumstances,” said Donato Giorgio, president of Global Manufacturing at Essity. The machines are expected to begin operation by Q4 2020, and Essity will be able to provide facemasks to health and elderly care and for internal use. Essity previously announced a redirected production in Sweden and the development of surgical masks for health and elderly care use. The development has been in close dialogue with the Swedish government and the National Board of Health and Welfare. Employees at Essity’s production facilities outside Gothenburg have, over the course of just a few weeks, redirected production and developed a surgical mask for healthcare use. The masks are undergoing quality tests in partnership with Research Institutes of Sweden (RISE) to ensure that they meet the requirements and needs for healthcare use. Source: essity.com
Monforts provides industrial-scale testing for companies developing PPE finishes to assist in COVID-19 response
In the current fight against COVID-19, a number of formulators of textile finishing chemicals have rushed out new antiviral and antimicrobial treatments intended for PPE (personal protective equipment) such as face masks and medical gowns and drapes. These finishing chemicals have naturally already been thoroughly tested in laboratories and their effectiveness verified at laboratory or pilot scale. However, they are new to many manufacturers of textiles and nonwovens now preparing to use them on an industrial level. “We know that in this current, unprecedented situation, many of our customers are rapidly preparing to transition from their usual manufacturing programmes to the production of PPE items,” says Klaus Heinrichs, vice president at Monforts. “Some, such as Trident and Welspun in India, which both operate a number of our machinery ranges, have already embarked on new PPE production programmes. The three lines at the ATC situated at the Monforts HQ in Mönchengladbach, are industrial scale and trialing new products on them goes beyond lab or pilot plant testing to rapidly identify any problems that might occur once full production is underway. The Monforts teleservice team is also fully available as normal to help customers via remote service on trouble shooting issues. Source: monforts.de
Taiwan forms surgical mask supply chain, donates 15M units to countries battling COVID-19
The Taiwan Textile Federation (TTF) is working with a range of industry organizations to form a complete surgical mask supply chain by integrating upstream, midstream, and downstream textile industries. With the help of textile manufacturers such as Formosa Plastic Group, Formosa Chemicals & Fibre Corporation, Far Eastern New Century Corporation, KNH Enterprise Co., Ltd., China Surgical Dressings Center Co., Ltd. and Chang Hong Machinery Co., Ltd. etc., the organization said Taiwan has transformed from an importing country for surgical masks to the second-largest surgical mask producer worldwide with daily production capacity of 15 million units in response to the COVID-19 pandemic. Taiwan has donated 15 million surgical masks to support medical staffs in countries with severe coronavirus outbreak, and will continue to provide support to the international community, according to the Taiwan Textile Federation. Under the Taiwan-U.S. epidemic prevention cooperation framework and in the spirit of “Taiwan can help!”, Taiwan has donated 2 million surgical masks to the U.S. and will continue to help strengthening protection for frontline medical personnel by providing 100,000 urgently needed surgical masks every week. Read the full story: https://finance.yahoo.com/news/taiwan-textile-industry-actively-helping-110000040.html Source: https://www.textiles.org.tw/TTF/english/home/English.aspx
NatureWorks, NWI partner to produce spunbond-based nonwoven material for N95 facemasks
As the world faces a critical shortage of personal protective equipment (PPE) for medical workers confronting the COVID-19 crisis, a long-standing partnership between NatureWorks and the Nonwovens Institute (NWI) at North Carolina State University (NC State) has resulted in a new spunbond nonwoven technology enabling the production of at least 10 million additional N95 surgical masks. NWI has converted the use of its research and training pilot production line to produce the face mask materials, and NatureWorks has donated the Ingeo resin needed to produce the spunbond material.
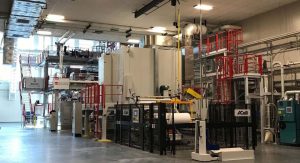
“Because of the COVID-19 crisis, we took the spunbond technology and created a new generation of unique filters that have excellent filtering capability without needing to be charged, meaning they can potentially be reused after cleaning with peroxide, or an alcohol solution,” says Behnam Pourdeyhimi, executive director of NWI, Wilson College of Textiles associate dean for industry research. and extension, and William A. Klopman distinguished professor. “Because these materials are also strong they can be cut and sewn by traditional techniques.” The new nonwoven fabric is a bicomponent fiber made of Ingeo biopolymer (PLA) and polypropylene (PP), providing significant strength and bulk with equal effectiveness in filtration. Additionally, Ingeo improves the productivity of the spunbond process by at least 30%. Leveraging these benefits, NWI’s pilot line can produce enough material to make 2 million masks per week. Read the full story: https://www.natureworksllc.com/News-and-Events/Press-Releases/2020/2020-4-22-NWI-N95-masks-release Source: natureworksllc.com & thenonwovensinstitute.com
Berry outlines COVID-19 actions, launches new media for facemask materials
Berry Global announced strategic initiatives to increase production of face mask materials. The initiatives include the company designating additional capacity for the production of facemask materials in North America and introducing a new material for facemasks in Europe. With demand outpacing current supply for facemask filter media, the product development team at Berry has responded to deliver innovative solutions in a matter of weeks to support the demand. These solutions include pivoting existing manufacturing assets and creating alternative materials for facemasks. To address the ever increasing demand for facemask material in the United States, Berry has expanded its proprietary Meltex platform to add meltblown capacity in Waynesboro, Virginia. This capacity was converted from a pilot line into one which provides full commercial output. The line will make meltblown materials, which will ultimately be used in surgical-grade face masks along with N95 and N99 respirators. This added capacity will support the manufacturing of approximately 200 million facemasks annually, according to the company. In addition to its Waynesboro facility, Berry has a number of North American nonwovens manufacturing facilities which are rapidly producing materials that help protect against the spread of COVID-19. The added capacity in Waynesboro is complementary to the company’s existing portfolio, producing incremental output surgical-grade materials serving the North American market. Berry also launched an extension to its Synergex range of products, Synergex ONE, a new media for facemask applications. Developed to initially meet the new facemask categories for general population, the aim is to quickly bring the media up to EN 14683:2019 standards for surgical masks. The newly introduced Synergex ONE provides a multilayer nonwoven composite product in a single sheet, as an alternative to traditional facemask layer structures. This new material will be manufactured in Europe and serve the European market and is available immediately. Source: berryglobal.com
Don & Low producing medical-grade fabric to help meet PPE needs in the UK
UK-based Don & Low produced is producing clinical-grade fabric and is working with the government and health authorities to co-ordinate some of Britain’s biggest manufacturers to turn the fabric into hospital gowns. Burberry, which is involved in the project, has retooled its factory in Castleford, West Yorkshire, from making trench coats to produce protective masks and clothing. Will Campbell, sales manager at Don & Low, said that its factory had dedicated 100 per cent of capacity to the NHS. “Once in full-scale production, we will be producing the material 24 hours a day, seven days a week for the next three months,” he said. The factory has received an order from the government to make 7.4 million metres by May, which will be sewn and welded into 3.5 million gowns at other sites. The government has issued a call to arms for garment manufacturers to switch their factory lines to PPE. However, most British retailers have shifted clothing production overseas, meaning that there are few remaining textile factories in the UK to produce the number of gowns required. Read the full story: https://www.donlow.co.uk/gb/en/news/New%20medical-grade%20fabric%20to%20support%20NHS%20needs/ Source: thetimes.co.uk & donlow.co.uk
NCTO calls 90-day tariff deferral on U.S. textile imports ‘counterproductive’
The National Council of Textile Organizations (NCTO), representing the full spectrum of U.S. textiles from fiber through finished products, issued a statement from NCTO President and CEO Kim Glas today, voicing concern over the administration’s executive order instituting a non-reciprocal 90-day deferral on certain tariffs. The temporary postponement of duties does not apply to products with antidumping or countervailing duties or those products subject to penalty duties under Section 232, 201 and 301. As further details of the order emerge, we are closely reviewing the implications for the U.S. textile industry. “At a time when domestic textile producers and its workforce have mobilized to transform their production lines to manufacture the personal protective equipment (PPE) supplies for frontline healthcare and medical workers fighting the COVID-19 pandemic, the administration’s decision to defer duties for 90 days on the vast majority of products imported into the United States is counterproductive. “This move contradicts the administration’s top stated priority of rebuilding American manufacturing and buying American and could have severe negative implications for the entire U.S. textile industry, whose companies and workforce already are facing enormous economic hardship. “We support the need to temporarily eliminate barriers to the entry of emergency medical supplies and certain PPE inputs tied directly to the COVID-19 response. But make no mistake, the key drivers behind efforts to defer tariffs have nothing to do with facilitating access to PPE products or stopping the spread of COVID-19.” Read the full NCTO statement: http://www.ncto.org/ncto-statement-on-administrations-90-day-tariff-deferral/ Source: ncto.org Related article: https://fiberjournal.com/achieving-us-self-sufficiency-on-meltblown-fabric-for-facemasks/
U.S. Cotton partners with FDA, Gates Foundation, UnitedHealth Group & Quantigen to supply cotton swabs for coronavirus testing
Parkdale Mills subsidiary U.S. Cotton, the nation’s largest manufacturer of cotton swabs, has joined in an effort with the Food & Drug Administration (FDA), the Gates Foundation, UnitedHealth Group and Quantigen to ramp up production of spun synthetic swabs to help the country’s frontline health care workers administering tests for the COVID-19 disease. U.S. Cotton has developed a fully synthetic, polyester-based Q-tip-type swab that can be used in coronavirus diagnostic testing. The U.S. Food and Drug Administration just announced that these synthetic swabs – with a design similar to Q-tips – could be used to test patients for the coronavirus. U.S. Cotton, based in Cleveland, Ohio, plans to leverage its large-scale manufacturing capacity to rapidly increase production of large quantities of the polyester swabs, which are in short supply for testing kits across the country. The FDA has determined that spun synthetic swabs can be used in COVID-19 testing based on the results from a clinical investigation stemming from its collaboration with UnitedHealth Group, the Gates Foundation and Quantigen. Source: uscotton.com
Lubrizol joins NIKE COVID-19 initiative, donates TPU polymers for PPE face shields and respirator lenses
Lubrizol, together with NIKE, Inc., is helping protect frontline medical workers fighting against COVID-19. To support Nike’s efforts to develop and donate full-face shields and powered, air-purifying respirator (PAPR) lenses to hospitals across several U.S. cities, Lubrizol donated ESTANE® thermoplastic polyurethane (TPU) polymers, an important element in both pieces of personal protective equipment (PPE). Nike’s version of the full-face shield transforms elements of the brand’s footwear and apparel, including TPU. Lubrizol’s innovation team quickly evaluated materials, provided insights to optimize performance and re-orchestrated its production and supply chain to produce and donate the necessary material to Nike as part of this effort. In addition to the full-face shields, the ESTANE TPU donation will be used in lenses for powered, air-purifying respirator (PAPR) helmets, used in situations where medical professionals face the greatest airborne pathogen exposure as they provide critical care to infected patients. Source: lubrizol.com
Ahlstrom-Munksjö materials validated by French Government for facemask production
In accordance to the newly implemented guidelines issued by the French National Agency for the Safety of Medicines and Health Products (ANSM) aimed at providing policies that help expand the availability of face masks for non-sanitary use, Ahlstrom-Munksjö has received necessary certification for the use of its Reliance SMS 200, Reliance SMS 300, Reliance® Dextex 200 and Reliance Dextex 300 materials for facemask production. Typically used for the manufacturing of sterilization wraps for surgical instruments, these materials have been deemed to meet the requirements of a category 1 mask type for use by professionals in contact with the public. In addition, Reliance SMS 200 and Reliance SMS 300 have been shown to be compatible to the performance criteria of surgical masks. The validation was acknowledged following a series of tests conducted by the Direction Générale de l’Armement (DGA), the French Government Defense procurement and technology agency. Testing confirmed the performance compatibility of the Reliance SMS material with surgical facemask types thanks to its breathability and bacterial filtration efficiency, whereas Reliance Dextex proved to ensure permeability to air and to perform in protection barrier efficiency at a level compatible to the category 1 face masks currently in use. Reliance SMS 200, Reliance SMS 300, Reliance Dextex 200 and Reliance Dextex 300 manufactured at the Medical business plants in Windsor Locks, United States and Mundra, India and converted at the site in Pont Audemer, France, have already been supplied to hospitals across France, to the French Government and distributors. Source: ahlstrom-munksjo.com
Johns Manville starts production of filtration media for facemasks at Richland, Mississippi plant
The Johns Manville plant in Richland, Mississippi, has started production to make nonwoven filtration media that will be used to create needed facemasks to help stop the spread of COVID-19. Most nonwoven production of face masks was abandoned in the U.S. many years ago and moved to Asia. Given the shortage of face masks in the U.S. and Europe, JM’s Engineered Products business decided to build on its existing capabilities and help fill the market demand. JM media meets or exceeds Level 1 BFE 95% (Bacterial Filtration Efficiency) and VFE (Viral Filtration Efficiency) requirements. These results were verified by an FDA-registered national laboratory. The JM plant in Richland employs about 50 people and produces a variety of filtration products for various air and liquid applications using polypropylene and polyester meltblown technology. Richland’s meltblown filtration media can be found in numerous industrial, automotive, consumer products and FDA-approved food and healthcare applications. Source: jm.com
RKW joins coalition of manufacturers to produce FFP-2 protective facemasks
In response to the COVID-19 pandemic, RKW Group, Sporlastic, the Gherzi Consulting Group and others have formed the “FIGHT” consortium to jointly produce FFP-2 type protective masks. RKW is participating in the production of FFP-2 protective masks by producing a laminate made of spunbonded nonwoven fabric at its Gronau, Germany facility. Production has been running at full speed for a few days now, with the aim of achieving a weekly capacity of around 750,000 masks. The RKW spunbonded nonwoven is processed in Gronau into a laminate with meltblown material that meets the high demands on the filter material for FFP-2 masks. It must capture at least 94 percent of the particles in the air down to a size of 0.6 micrometers. The COVID-19 coronavirus is bound in water droplets averaging around 1 micrometer in size. The first production batch will be delivered to the first client, the Ministry of Social Affairs and Integration of Germany’s federal state of Baden-Württemberg. Further public sector clients are currently in negotiation with the consortium. Source: rkw-group.com
NC State’s Nonwovens Institute calls for collaborators in making facemask materials and masks for COVID-19 response
The Nonwovens Institute (NWI) at North Carolina State University is responding to the shortage in capacity for making filtration media and converting it to make facemasks by opening up its meltblown and spunbond nonwoven-making facilities. NWI is utilizing its expertise to produce specially designed fabrics that can be delivered to manufacturers in the U.S. to assemble facemasks, and it is also investing in new converting equipment to locally assemble ready-to-use facemasks for healthcare workers, as well as for public use. NWI is also seeking collaborators, partners, suppliers, and customers to engage in the response by contributing money, equipment and materials.
Need area:
- Cash Donation (online, check, wire transfer)
- Equipment & Materials Donation
What’s needed:
- Investment support to scale-up nonwoven production, invest in new converting equipment, and increase capacity.
- Equipment for production and maintenance, e.g., Reicofil Spare Parts for Production, nonwoven belts, SB and MB resins (polypropylene & PLA), forklifts, and product handling and storage equipment.
Impact:
- Accelerate time to full production of affordable facemasks that make a difference.
- Ensures production reliability and resin supply for production.
Questions about this initiative can be directed to nonwovens@ncsu.edu. To learn more about facemask technology types and applications, Behnam Pourdeyhimi, Ph.D. NWI Executive Director has posted a detailed description here. Source: thenonwovensinstitute.com
Britain’s textile industry boosted by coronavirus pandemic
The coronavirus outbreak is a human tragedy and an economic disaster, but some businesses could in the long term do quite well out of it. Take Britain’s textile industry. Throughout the 1990s, British textile companies lost a lot of business to China as clothing retailers and brands in the United Kingdom turned en masse to the Far East for cheaper production. But now the disruption in trade with China has made some of those retailers reconsider the wisdom of having long supply chains, and they’ve been turning back to British manufacturers. Read the full story: https://www.marketplace.org/2020/04/13/covid-19-britain-textile-industry/ Source: marketplace.org
Bally Ribbon Mills providing structural tapes and elastics for COVID-19 response
Bally Ribbon Mills (BRM) is manufacturing narrow-woven structural tapes and elastics for use in a range of medical items required for the current COVID-19 emergency. The tapes and elastics are used by manufacturers of facemasks, face shields, gowns, other personal protective equipment (PPE), and medical patient soft goods, as well as patient slings, wheelchair harnesses, braces, and respiratory equipment.
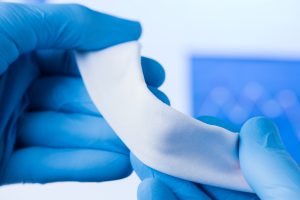
BRM offers ¼- to ½-inch woven tapes and webbing in natural polyester and elastic. Latex-free options are available, as well as material with 100 percent elastic stretch. Also available are ¼-inch to ¾-inch nylon grosgrain binding tapes used in medical tie applications and special designs where Velcro is utilized for closure. Source: ballyribbon.com
Eastman donates materials to Purdue University to support production of PPE for COVID-19 response
As part of the world’s collective effort to respond to the coronavirus pandemic, Eastman is donating materials to produce protective lenses and face shields for medical personnel. Eastman donated 600 square feet of material to Purdue University. More than 40 volunteer faculty and staff members are using the school’s laser cutting system to produce up to 3,000 lenses and 4,000 face shields. The protective equipment will be distributed to hospitals across Indiana. “I’m proud of the speed at which the Eastman team was able to get material to the teams at Purdue,” said Brendan Boyd, Vice President, Specialty Plastics & Fibers Technology said. “The need for more protective equipment is urgent. We value these innovative partnerships that can meet a significant community need quickly and effectively.” Purdue’s Bechtel Innovation Design Center is using a pilot-scale manufacturing facility to make protective glasses and face shields. “Under guidance from medical professionals, we have redesigned and manufactured complex fittings for ventilators and are actively producing laser cut, waterjet cut, and 3D-printed parts for face shields and safety glasses,” said David McMillan, assistant director of the center. Source: eastman.com
DuPont, HHS, FedEx partner to expedite shipping of Tyvek garments to aid COVID-19 response in US
DuPont has partnered with the U.S. Department of Health and Human Services (HHS) and FedEx to provide expedited shipping of Tyvek garments critical to COVID-19 relief efforts.Bolger & O’Hearn reports spike in demand for durable water repellents amid COVID-19 response
Bolger & O’Hearn, known for developing innovative specialty chemicals for the global textile industry, is seeing brisk demand for the company’s high-powered durable water repellents (DWRs) in connection with COVID-19 and the growing call for Personal Protective Equipment (PPE) and other medical textiles. This includes DWR’s used in the production of medical masks, gowns, bed coverings, hospital room drapes, etc. “In particular, we are seeing a high demand for Stormproof/Breathable OmniBloq™, a DWR we developed for high-end performance apparel brands that surpasses industry standards for water and soil repellence,” said Kelly Murphy, co-president of Bolger & O’Hearn. Bolger & O’Hearn has been designated an Essential Service by the state of Massachusetts, the US department of Defense and Homeland Security. Their offices, R&D labs and manufacturing operations are remaining open as the company provides brands and textile manufacturers with the chemistries they need to make PPE and other textile end products essential to fighting COVID-19. Source: bolgerohearn.com
Webinar Series: Nonwoven market, products and supply in the world of COVID-19
INDA, Association of the Nonwoven Fabrics Industry, will present the first in a three-part webinar series focused on the role nonwoven materials are playing in the COVID-19 response, Tuesday, April 14, 2020, 2:00 pm–2:50 pm EST. Part I in the series, titled “Structure, Effectiveness and Differentiation of COVID-19 Wipes & Masks,” will be presented by Chris Plotz, Director of Education & Technical Affairs, for INDA. The webinar will cover physical and chemical characteristics of disinfecting nonwoven hand wipes, hard surface wipes, and facemask technology for COVID-19 response in work, home, and personal care applications. Highlighted topics will include:
- Face mask: Differentiation and filtration efficacies
- Wipes: Dry and wet
- Chemistries: Types and effectiveness for hand, skin, and hard surface sanitizers
- Nonwovens best protection practices and new developments
Plotz is a business leader with 19 years of technical nonwovens related experience in global product management and product development. At INDA, Plotz directs, oversees, and expands education and training programs for all levels of industry members, manages the international harmonized standards activities, Product Stewardship activities, Technical Advisory Board, and key services areas that INDA operates for its members. Subsequent webinars in the series include:
- “Absorbent Hygiene Marketplace During COVID-19: Disruption, Risks, & Opportunities,” Svetlana Uduslivaia, Head of Research, Euromonitor International
- “Increasing Nonwovens Materials to Respond to COVID-19 Crisis,” Brad Kalil, Director of Market Intelligence and Economic Insights, INDA
Register for the webinar series at: https://imisw.inda.org/store/SearchResults.aspx?searchterm=webinar&searchoption=ALL Source: https://www.inda.org/ * INDA owns International Filtration News.
European Man-Made Fibres Association publishes position paper on critical role man-made fibers are playing in coronavirus response
CIRFS, the European Man-made Fibres (MMF) Association, published a position paper calling on the European authorities to recognize the MMF industry as a supplier of critical goods in the battle against both the SARS-CoV-2 virus and the Covid-19 lung disease. Frédéric van Houte, Director General of CIRFS says: “The world is being confronted with an unprecedented crisis. CIRFS is shocked by the dramatic impact of the Covid-19 pandemic. Our industry has taken all safety measures needed in this crisis. The main priority should now be a wide access to all necessary protective equipment. MMF are indispensable in the production of masks and other protective equipment. CIRFS therefore calls on the European Commission to recognize the MMF sector is an essential supplier in the production of health and hygiene-related products to fight COVID-19 and to deploy all possible measures possible to support it. The European MMF industry is committed to continuing to invest and to create jobs in Europe.” Read the paper at: https://www.cirfs.org/file_access/application/files/2715/8624/6516/2020_04_06_-_CIRFS_PRESS_RELEASE.pdf Source: cirfs.org
NCTO highlights what U.S. textile industry organizations are doing to aid the COVID-19 response
The National Council of Textile Organizations (NCTO), an association that represents U.S. textiles from fiber through finished products, issued a statement from textile executives leading the nation’s unified effort to produce critical personal protective equipment (PPE) to help hospitals and healthcare workers fighting the COVID-19 pandemic. In factories across the country, textile companies are retooling production virtually overnight to produce PPE products ranging from hospital gowns, face masks and shoe covers to scrubs. The industry is playing a critical role in the nation’s manufacturing strategy and solution to help contribute to the high demand for these products. “Coordinating with local hospitals, healthcare organizations, the entire U.S. production chain and federal agencies, the textile industry has been at the forefront of the incredible manufacturing effort, contributing to the country’s rapid response to the rising needs of frontline workers,” said NCTO President and CEO Kim Glas. “This industry has taken the lead in this effort, utilizing American manufacturing facilities and workers, despite facing many challenges in this environment. Our industry will continue to do all they can to serve the American people, frontline hospital workers and patients at this time.” Read the full story: http://www.ncto.org/textile-industry-unites-to-play-critical-role-for-the-nations-production-of-ppe-products/ Source: ncto.org
Sinopec Yizheng Chemical Fibre Co. launches first of 12 planned meltblown lines
Sinopec Yizheng Chemical Fibre Co (YCFC) successfully launched its first melt-blown non-woven production line on March 29 in Yizheng, Jiangsu province, which was manufactured by Shaoyang Textile Machinery Co, affiliated to Sinomach’s subsidiary China Hi-Tech Group Corporation (CHTC). Shaoyang Textile Machinery succeeded in reducing the lead time to a month and delivered the production line 13 days earlier than the date required by the State-owned Assets Supervision and Administration Commission of the State Council (SASAC).
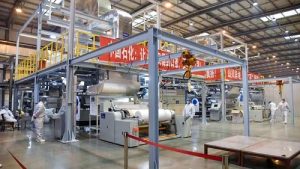
As the filter layer of a surgical mask, the meltblown nonwoven material is an essential raw component in mask production. Mask production lines are expanding rapidly across the country as an urgent part of pandemic prevention and control, and a large number of manufacturers are facing a shortage of raw materials. Shaoyang Textile Machinery will supply 12 meltblown nonwoven production lines in total to YCFC. When all 12 lines are operational, YCFC will have a daily output of 12 tons of N95 melt-blown non-woven or 18 tons of surgical mask materials, and be able to increase production of disposable surgical masks by 18 million pieces a day. Source: sinopec.com
P&G CEO issues open letter, outlining company’s plans for COVID-19 response
In an open letter, Procter & Gamble president & CEO David Taylor outlined the company’s commitment to supporting the COVID-19 response worldwide. In the letter, Taylor said, “We’re stepping up to provide much needed product donations and financial support. Our contributions of product and in-kind support now exceed $15 million and will continue to increase as we work with communities around the world to understand how we can best serve them.” Many P&G products are being employed to prevent the spread of COVID-19, particularly those that are used daily for cleaning and sanitizing homes, businesses and places like healthcare and assisted-living facilities. Other P&G products are critical for helping consumers maintain proper hygiene, personal health and healthy home environments. Taylor said, “Millions of P&G products are being donated from 30 brands in more than 20 countries, with more on the way. These donations ensure that families who do not have basic access to the everyday essentials many of us take for granted, can have the cleaning, health and hygiene benefits P&G brands can provide. “Our contributions are broad-based with cash support to ensure disaster relief organizations can meet immediate needs, including hygiene education and medical equipment and supplies.” Taylor said P&G has installed new lines to start production of hand sanitizer in five manufacturing sites around the world, using it to ensure the company can continue operating safely and sharing it with hospitals, health authorities and relief organizations. The company also plans to expand manufacturing capacity further in additional facilities in the coming weeks and will have a capacity of at least 45,000 liters per week when fully operational. Work is also under way to produce critically needed face masks at P&G manufacturing sites around the world. “We’re up and running already in China. We have teams working to install capacity in North America, Europe, and Asia Pacific, Middle East and Africa, and will quickly begin production in the coming weeks,” said Taylor. He said this is important for several reasons:
- It will increase the supply of masks for hospitals, first responders and other organizations by reducing market demand for production and industrial use;
- It helps us create a safe working environment for P&G people;
- Long term, it will allow us to directly help many communities across the globe where there is unprecedented need for protective supplies.
Read the full letter at: us.pg.com/covid19/
ANDRITZ introduces high-speed face mask converting line
In the first configuration, this new converting line will be able to produce masks for surgical/medical applications; other mask types – like N95/FFP2 – are currently being evaluated.
India exempts customs duty, cess on ventilators, surgical masks, PPE & Covid-19 test kits
“In the context of Covid-19 situation, considering the immediate requirement of ventilators and other items, the Central Government has granted exemption from Basic Customs Duty and Health cess, on the import of these goods, with immediate effect,” the government said in a statement late Thursday evening.
Read the full story at: https://economictimes.indiatimes.com/news/politics-and-nation/govt-exempts-customs-duty-cess-on-ventilators-surgical-masks-ppe-covid-19-test-kits/articleshow/75072273.cms Source: economictimes.indiatimes.com
Web Industries subsidiary, Omega Systèmes, shipping 900K French Directorate-approved facemasks
Omega Systèmes, a Web Industries company, is shipping 900,000 personal facemasks approved by the French General Directorate of Armament to the Ministère des Armées for distribution to food manufacturers, supermarkets and nursing homes conducting business in France. Obtaining the French General Directorate of Armament approval for mask production called for Omega to pass a series of tests carried out in accordance with stringent Armament specifications, including those for wearer protection. The announcement comes at a time when demand for the facemasks is high throughout France. Prime Minister Édouard Philippe has extended COVID-19 containment measures until April 15th, as the number of infections in France exceeds 81,000 with more than 10,800 deaths in hospitals. The masks are being supplied by the Ministèred Armées to businesses whose personnel are at a high risk of contamination, such as those working in the food sector and facilities housing the elderly. These single-use masks can be worn for up to four hours before being changed and offer a 96% protection rate. Source: webindustries.com
Ahlstrom-Munksjö ramps up medical fabrics production to provide up to 30 million face masks per month
Responding to the COVID-19 pandemic, Ahlstrom-Munksjö has increased capacity across its entire protective medical fabrics product portfolio. The exponential spread of the COVID-19 virus around the world has caused an exceptional situation, creating strong demand for healthcare goods in general, and specifically for protective medical products that are made from the company’s fabrics. Ahlstrom-Munksjö is also expanding manufacturing of fabrics production lines normally used for producing other fiber-based materials. In the beginning of March, the company expanded the production of face mask materials to a fine fiber line normally used for industrial filtration materials at the Turin plant, Italy. The technology is unique, generating good protection and breathability for medical use, and approved as a surgical mask. The advantage of this technology compared to the commonly available electrostatically charged material is its durability. Protection efficiency of electrostatically charged materials is lost overtime when humidity gets in contact with the filter media, whereas protection efficiency of a mechanical filter media remains intact over time. First orders were received in the middle of March, and Ahlstrom-Munksjö is now targeting to ramp up fabrics production for more than 20 million face masks per month. In April, Ahlstrom-Munksjö is expanding the production of face mask materials to a line normally used for industrial filtration materials at the Tampere plant in Finland. Currently the material is well suited for lighter fabric face masks in civil activities. Droplets test shows that the media has efficiency above 90% at 3 microns and above 85% at 1 micron, which is close to a surgical face mask requirement. Development continues to meet the requirements of material for surgical masks for medical use. Considering the ongoing production, the Tampere plant can deliver fabrics for around 10 million face masks per month on a short notice. Source: ahlstrom-munksjo.com
Gerber forms task force to help companies convert manufacturing to PPE
To support the COVID-19 response, Gerber Technologies has created the Gerber PPE Task Force to support its customers as they need to increase their production and/or transition to manufacturing personal protective equipment (PPE). By joining, companies receive access to a number of resources and services including:
- Production-ready patterns, cut files, markers, tech packs and more.
- Help with the setup of cutter parameters specific to the selected fabrics.
- Training, software, equipment and service technicians to ramp up production.
- Support for changing over current production lines to the production of PPE.
- Contact information for fellow suppliers and manufacturers through our PPE Manufacturing Matchmaking Program.
- Introducing existing PPE manufacturers to those converting to PPE production.
- Production-ready files and recommended materials for applications related to labels, placards and signage.
For more information about this program, visit gerbertechnology.com/covid19. Source: gerbertechnology.com
Ramina running meltblown pilot line 24/7 to manufacture medical face mask material
Source: ramina.it
Reifenhäuser calls for creation of industrial supply chains for face masks and medical protective clothing in Europe
Reifenhäuser Reicofil recently opened its R&D facility to the manufacture of nonwoven fabrics for face masks and medical protective apparel to support the COVID-19 response. However, the company says the utilization of this material is under-performing, with only small-scale, manual conversion of the material into face masks for end use. “Within the last two weeks, many initiatives have been founded that sew masks by hand. Thus, at least small production capacities have been established in Germany within a very short time, which now want to be supplied,” said Bernd Kunze, Ph.D., managing director of Reifenhäuser Reicofil. “From the many inquiries we have very consciously selected those initiatives that work efficiently and deliver masks quickly and reliably first to where they are most urgently needed.” For Reifenhäuser, however, manually operating converters remains only a partial success, as the quantities produced in this way are only a small amount of the overall demand for medical protective clothing. Likewise, the company notes that if the general population is to be supplied with masks, the demand would rise into the billions. To actually solve the problem, the company said Germany and Europe need to establish their own industrial production sites with closed European supply chains and decisive political action. The aim must be to supply Europe with protective material independently and competitively, both now and in the long term. “We need a strategic production reserve for medical protective clothing in Europe,” said Bernd Reifenhäuser, CEO of the Reifenhäuser Group. “We have to quickly build up the machine capacity for the industrial production of masks in high volumes, but at the same time, the corresponding capacities for the production of the necessary high-quality nonwovens in Europe must be created.” Source: reifenhauser.com
Cummins, DuPont working on alternative material for N95 respirator masks
As the COVID-19 pandemic spreads across the globe, Cummins Inc. and DuPont are helping address the nation’s shortage of N95 respirator masks. Cummins’ NanoNet® and NanoForce® Media technology, which uses DuPont’s Hybrid Membrane Technology (HMT), can typically be found in air, fuel and lube filtration products used in heavy-duty diesel engines to prevent long-term engine wear, but also can be used in the N95 respirator masks worn by healthcare professionals to filter harmful airborne particles that can spread COVID-19. The need for N95 masks has skyrocketed in recent weeks in response to the COVID-19 pandemic. Many of the world’s leading mask manufacturers are in need of the critical materials to assemble the mask and are struggling to meet demand. “Cummins is re-evaluating our supply base and manufacturing capabilities to identify how we can support our healthcare professionals who rely on critical personal protective equipment to do their jobs,” said Amy Davis, Vice President of Cummins Filtration. “Our NanoNet® Media can fill a key supply void and help address the mask shortage facing the United States and other countries around the world.” The first mask prototypes using Cummins’ donated media were assembled by University of Minnesota teams in March as part of an initiative to provide masks to M Health Fairview and other Minneapolis-based healthcare systems. As the COVID-19 outbreak escalated, the University of Minnesota realized their supply of N95 masks to protect healthcare workers would potentially run out in a matter of weeks. To address this challenge, a team of designers, engineers, chemists, surgeons, anesthesiologist and apparel and clothing experts from the University of Minnesota’s Institute for Engineering in Medicine; Medical School; College of Design; College of Science and Engineering; and Center for Filtration Research Consortium (CFR) came together to address this projected shortage of critical personal protective equipment. “The first thing we recognized from our experts in the Center for Filtration Research, who work directly with Cummins, is that not all filtration materials are created equal and that the Cummins material is an excellent alternative,” said Jakub Tolar, Campus Health Officer and Medical School Dean at the University of Minnesota. “We are tremendously grateful for the generous donation from Cummins of their filtration materials toward our mask effort. Since the arrival of the filtration media, we have been able to make rapid progress, and we now believe we have several viable mask options, including both a disposable and re-usable option. These designs show real promise in keeping our healthcare workers safe should standard medical supplies of N95 masks no longer be available,” continued Tolar. DuPont’s Hybrid Membrane Technology goes beyond the limits of traditional semi-porous or nonwoven membranes for air and liquid filtration. Made using a proprietary spinning process, the hybrid technology materials are comprised of continuous sub-micron fibers. The end result is a “membrane-like” sheet structure that balances breathability and high filtration efficiency of particulates. While products featuring Cummins’ media will need to be vetted and approved by the National Institute for Occupational Safety and Health (NIOSH), the company is preparing to do its part to help relieve the burden facing the healthcare industry. “We’re working as quickly as possible with healthcare regulators and other partners to help certify products with our materials, and prepare our manufacturing facilities to meet demand,” said Davis. Mask manufacturers interested in learning more about Cummins’ media technology can visit cumminsfiltration.com/respiratormedia. Source: cumminsfiltration.com
Curt G. Joa manufactures 80,000 headstraps for medical faceshields needed for COVID-19 response
Wisconsin-based manufacturer Curt G. Joa received a call from a vendor around 1 p.m. asking the same question many manufacturers across the country have been asked:
“Can you make protective equipment for health care workers?”
After that call, a team of about eight design engineers and employees immediately started designing different options for producing head straps for face shields. Within two days, a design was chosen and almost 80,000 head straps were made.
Read the full story: https://www.sheboyganpress.com/story/news/2020/04/03/ppe-sheboygan-curt-g-joa-make-head-straps-face-shields/5103604002/ Source: sheboyganpress.com
Alchemie launches new coating technology to support COVID-19 response
Alchemie Technology accelerated the launch of its Novara precision coating technology for technical textiles in support of global efforts to combat COVID-19. Alchemie is actively partnering with manufacturers worldwide to build production lines to address acute personal protective equipment needs and medical textile shortages.
Alchemie’s Novara technology delivers high-precision, 2D-patterned one or two-sided functional coatings to technical textiles. Novara combines the throughput of conventional coating technologies with the precision of digital to unlock new product design opportunities and radically reduce the cost of technical textiles. The technology enables functional coatings to be applied with precision, all controlled with real-time digital data.
According to Alchemie, the benefits of Novara include:
- Precise 2D digital placement of coatings, including one or two-sided application using different materials
- Production with reduced material consumption: only delivering coating where it’s needed
- Reduced inventory and digital productivity benefits, including rapid changeovers in less than five minutes and economic short runs
Source: alchemie.com
ISAIC partners with area organizations to produce millions of medical- & surgical-grade masks in Michigan
The Industrial Sewing and Innovation Center (ISAIC) is working with the City of Detroit, the Michigan Economic Development Corp., Carhartt, Rock Family of Companies to mobilize local apparel manufacturers to produce standardized, centralized PPE and automate mass production of pleated surgical masks. The initiative is expected to produce millions of pleated medical grade masks and thousands of sewn surgical masks and isolation gowns. Under this regional initiative, the organizations are making mask and gown kits with standardized product specifications, created in consultation with area hospitals, to be dispersed to local manufacturing partners for production. ISAIC will administer orders, control inventory and handle distribution to hospitals and other medical facilities. If you are a hospital or medical facility in need of PPE, click here. If you are a local sewing specialist or manufacturer and want to get invovled, click here. Source: isaic.org
Berry contracts with Reifenhäuser Reicofil for new meltblown line in France to produce respirator materials
Reifenhäuser Reicofil and Berry Global Group have signed a contract for a meltblown line to produce filter material for FFP2 (N95) and FFP3 (N99) respirators. The plant is scheduled to be delivered in June. In order to support the fight against the coronavirus, Reifenhäuser Reicofil has reduced the delivery time of the line by one third, to 3.5 months. The 1.6 m wide Reicofil meltblown line is equipped with a technology for electrostatic charging for filter materials, a key component of face mask filtration. The plant will bring an additional annual capacity of 550 tonnes of N95 material and 365 tonnes of N99 material, respectively. serving the EMEA market. The plant will be installed in France. “We are pleased that the Berry Group, the world’s largest producer of nonwovens, is investing in new capacities for urgently needed, high-quality filter material,” said Bernd Kunze, Ph.D., CEO of Reifenhäuser Reicofil. “The demand for these materials is currently enormous and will, in our opinion, remain so in the future. We will provide all producers, who want to get involved in the fight against COVID-19, with the best possible support for rapid project realization.” Source: reifenhauser.com & berryglobal.com
NC State’s Nonwovens Institute to employ novel material for production of masks and mask filters
NC State’s Nonwovens Institute (NWI) is using its two research and training pilot production lines to produce face mask materials that will be used to protect medical workers supporting the COVID-19 response. N95 respirators and surgical masks are generally a sandwich of one or two common nonwoven layers – so-called spunbond layers that provide mask shape and protect the inner filtration layer – combined with a layer of nonwoven meltblown material that serves as the filtration layer and captures microscopic unwanted particles like viruses and bacteria. But because of the current critical need for masks caused by COVID-19, the NWI team created a new spunbond material that can serve as an effective filter without the need for a meltblown filtration layer. The unique fabric is composed of two different polymer materials that are combined to make a single fiber with significant strength and bulk – and that shows effectiveness in filtration similar to current materials used. “Because of the COVID-19 crisis, we took the spunbond technology and created a new generation of unique filters that have excellent filtering capability and can potentially be reused after cleaning with peroxide, or potentially alcohol solution,” said Behnam Pourdeyhimi, executive director of NWI, Wilson College of Textiles associate dean for industry research and extension and William A. Klopman Distinguished Professor. “Because these materials are strong, unlike classical meltblown filters, they can also be cut and sewn by traditional techniques.” Typically, one meter of spunbond material provides enough material for about 20 to 25 masks when using the current designs, Pourdeyhimi said. One of the NWI’s production lines started producing 2,000 meters of spunbond material per hour, with the potential to create some 20,000 meters of spunbond material in a day. NC State is currently in discussion with industrial partners to make masks with the material. NWI’s other production line is a meltblowing pilot line that will make the classical meltblown material for N95 masks and surgical masks. “We created a recipe for the production of classical N95 respirator materials and will ship those materials out for industrial partners to convert these into respirators,” Pourdeyhimi said. The meltblown material takes a bit more time to produce; Pourdeyhimi estimates that his production line can make about 12,000 meters of material in one work shift. Thanks to support from across the university, Pourdeyhimi says that NC State has ordered machines that will allow the NWI to make surgical masks in its Centennial Campus facilities. Those machines should arrive in the next month. “We will set these machines up and take our own materials and convert them into masks and provide them to local communities,” Pourdeyhimi said. Source: thenonwovensinstitute.com
Milliken shifts manufacturing to focus on advance medical PPE
Milliken & Company is manufacturing barrier protection fabrics to be used in gowns and headcovers for healthcare professionals supporting the response to the . Milliken is also researching and developing materials for incorporation into N95-grade masks.
The company says it is leveraging its materials science expertise to manufacture much-needed personal protective equipment (PPE) for the healthcare industry amid the current COVID-19 global pandemic. Milliken’s new advanced medical fabrics and barriers are currently available and complement Milliken’s breakthrough BioSmart antimicrobial technology used in scrubs, lab coats and hospital privacy curtains, harnessing the power of bleach to kill up to 99.9% of common bacteria on contact. Milliken is manufacturing barrier protection fabrics to be used in gowns and headcovers for healthcare professionals. Milliken is also researching and developing materials for incorporation into N95-grade masks. These new innovations complement our existing range of products that can be used for temporary shelters in situations where it’s deemed necessary to set up transitory field hospitals. Source: milliken.com
NCTO calls on U.S. to abandon 90-day tariff deferral on textile imports
The National Council of Textile Organizations (NCTO), an association representing U.S. textiles from fiber through finished products, issued a statement from NCTO President and CEO Kim Glas today in response to the U.S. administration’s plan to institute a 90-day deferral on MFN tariffs, as reported by numerous press outlets. The reported plan being pushed by the importing and retailing industries would defer certain tariffs, including those on finished apparel products. It is an ill-advised policy that will hurt the U.S. textile industry at the very time it is answering the call of the nation to produce medical supplies to battle the coronavirus pandemic. NCTO has been at the forefront of the efforts to deploy resources, converting production lines to manufacture urgently needed medical supplies like face masks and their textile components, to address the critical need for personal protective equipment and other medical and sanitation supplies in the fight against the coronavirus. These unnecessary tariff concessions would benefit importers and retailers at the direct expense of manufacturers on the front lines of the COVID-19 response and send a demoralizing message. Tariff deferrals would severely exacerbate ramifications for the U.S. economy, manufacturers and workers and open the floodgates for imports. If the U.S. government makes tariff concessions during this crisis, it will be inviting a virtual tsunami of imports further devastating domestic manufacturing as it attempts to regain its footing. We urge the administration to abandon any moves to defer tariffs on finished products. It would only serve to allow importers to exploit the current crisis, while dealing a severe blow to U.S. manufacturing and its workers. Source: ncto.org
How the coronavirus travels through the air
How the coronavirus travels through the air has become one of the most divisive debates in this pandemic.
As the coronavirus pandemic continues, many people are now overthinking things they never used to think about at all. Can you go outside? What if you’re walking downwind of another person? What if you’re stuck waiting at a crosswalk and someone is there? What if you’re going for a run, and another runner is heading toward you, and the sidewalk is narrow? Suddenly, daily mundanities seem to demand strategy. Read the full story: https://www.theatlantic.com/health/archive/2020/04/coronavirus-pandemic-airborne-go-outside-masks/609235/ Source: https://www.theatlantic.com/ Follow the Atlantic’s COVID-19 coverage: https://www.theatlantic.com/category/what-you-need-know-coronavirus/
Oerlikon to supply 2-beam meltblown system to Asian manufacturer; opens its testing lab for production of face mask materials
A leading Asian large-scale manufacturer of manmade fibers and polymers has invested in a new Oerlikon Nonwoven meltblown system. The recently signed contract includes a 2-beam system for manufacturing filtration nonwovens – predominantly for medical products such as face masks – with a nominal capacity of up to 1,200 tons of nonwovens a year. The commercial production launch has been scheduled for the fourth quarter of 2020. The 2-beam system has an operating width of 1.6 meters and is equipped with the new patented Oerlikon Nonwoven electro-charging unit. Electro-charging the filter nonwovens allows the manufacture of sophisticated EPA- and HEPA-class filter media as well as media that comply with the requirements of N95-, FFP2- and FFP3-class respiratory masks. The demand for filtration nonwovens for medical applications has risen tremendously across the globe since the outbreak of the coronavirus epidemic, presenting all manufacturers with huge challenges. “We are currently receiving inquiries from all over the world for our system concepts,” said Ingo Mählmann, Ph.D., vice president of sales & marketing for Oerlikon Nonwoven. “To improve the supply situation, we have changed our prioritization in favor of considerably shorter delivery times for meltblown systems, so that customers can now be supplied even faster and also with very short lead times.” A meltblown system will be commissioning at the site of a leading Western European nonwovens producers as early as the second quarter of 2020. This system will be deployed exclusively in the manufacture of nonwovens for respiratory masks. Due to the current state of emergency with regards to the local supply of face masks, Oerlikon Nonwoven is currently using its own laboratory system to produce electrostatically charged filter media, which are being sent to local small businesses and companies for the manufacture of face masks. “We are thrilled to be making a contribution towards fighting the pandemic, particularly in the local vicinity of our production site in Neumünster”, adds Rainer Straub, head of Oerlikon Nonwoven. Source: oerlikon.com/en/brands/nonwoven/
Berry expedites roll out of meltblown capacity in EMEIA market
Berry Global Group, Inc. has advanced its investment in an additional specialty meltblown asset to produce high-efficiency filtration media serving the EMEIA markets. Current projections are for commercial production to start in June 2020. This investment is targeted to meet increased demand and customer growth and will be focused on premium applications, such as FFP2 (N95) and FFP3 (N99) for industrial face mask and cabin air filtration markets. The new line will be equipped with Berry’s proprietary charging technology to deliver optimal filtration efficiency and pressure drop at lower basis weights. As the largest manufacturer of nonwoven fabrics and one of the world’s leading plastic packaging suppliers, Berry makes materials for face masks and protective healthcare apparel to packaging for food preservation and disinfecting products, many of which have seen a demand surge in the fight against COVID-19. “As a market leader in that space, we had been planning to add more capacity shortly after our latest investment in Asia came on line. The opportunity to support the fight against COVID-19 accelerated our decision,” said Cedric Ballay executive vice president and general manager for Europe in Health, Hygiene, and Specialties for Berry. “Our ability to be agile will benefit our customers and our communities.” Source: berryglobal.com
WPT Nonwovens acquires two lines, readies facility to begin production of surgical & N95 masks
WPT Nonwovens (Beaver Dam, KY) announced it will begin production of surgical masks and N-95 respirator masks, responding to requests from state and local officials looking for Kentucky manufacturers willing to assist with the production of supplies needed for the COVID 19 response. According to Travis Robbins, WPT Nonwovens Vice President and General Manager, the company has moved forward with the purchase of two fully-automated machines, one for producing surgical masks and one for producing N-95 respirators. It has dedicated 5,000 square feet of its Beaver Dam facility to set up these two new production lines. However, the company said the raw materials needed to produce the masks has been challenging with price gouging on raw materials required to make the N-95 respirators. Through the supply chain relationships developed by WPT Nonwovens, the company was able to source the necessary materials from a reliable and reputable supplier at an affordable cost. Robbins says that he is confident WPT Nonwovens will be able to supply needs at a price well below what the current market can offer, and that the company will be positioned to run 24/7 production to meet volume demands. WPT Nonwovens expects to produce 100,000 surgical masks per day, and 35,000 N-95 mask per day. It expects the surgical masks will be ready to ship by May 1, and the N-95 masks will be ready by June 1. Source: wptnonwovens.com
FEMA issues call for medical supplies, PPE to support COVID-19 response
- To sell medical supplies or equipment to the federal government, please submit a price quote under the COVID-19 PPE and Medical Supplies Request for Quotation. Full details can be found in the solicitation (Notice ID 70FA2020R00000011).
- This solicitation requires registration with the System for Award Management (SAM) in order to be considered for award, pursuant to applicable regulations and guidelines. Registration information can be found at www.sam.gov. Registration must be “ACTIVE” at the time of award.
- If you have medical supplies or equipment to donate, please provide us details on what you are offering.
-
If you are a private company that wants to produce a product related to the COVID response – email nbeoc@max.gov.
- If you are interested in doing business with FEMA and supporting the response to COVID- 19 with your company’s non-medical goods and/or services, please submit your inquiry to the Department of Homeland Security (DHS) Procurement Action Innovative Response Team (PAIR) team at DHSIndustryLiaison@hq.dhs.gov.
Source: fema.gov
Milliken ramps up production of anti-microbial fabric
Milliken & Company has increased domestic production of its BioSmart anti-microbial fabric.
Considering alternatives to minimize the impact of the face mask shortage
An editorial published March 20 in JAMA requested creative ideas on how to reuse the N95 face masks, as well as how to make alternatives to commercial masks. The innovation on display convinced surgeon Ed Livingston, a coauthor of the editorial and an editor at JAMA, that “this is the biomedical engineering community’s Apollo 13 moment.” In this fast-moving emergency, it’s unclear which homespun efforts will help the most. The following article considers how to best conserve the PPE that we have and how to make more. Read the full story: https://www.sciencenews.org/article/coronavirus-covid-19-ppe-face-mask-shortages-creative-solutions Source: sciencenews.org
How 3M Plans to Make More Than a Billion Masks By End of Year
Andrew Rehder, manager of 3M Co.’s respirator mask factory in Aberdeen, S.D., got the call from headquarters on Tuesday, Jan. 21. He gathered about 20 managers and supervisors into a conference room, where they sat, unworried, less than 6 feet apart. Rehder told them that a new virus was spreading rapidly in China and that 3M was expecting demand for protective gear to jump.
The Aberdeen plant had already ramped up production of respirator masks in response to demand from first responders battling wildfires in Australia and contending with a volcano in the Philippines. Now, Rehder told his charges, Aberdeen would shift to “surge capacity.” Idle machinery installed for precisely this purpose would be activated, and many of the plant’s 650 employees would immediately start working overtime. “We knew it wouldn’t be a two-week blip, it would be longer,” Rehder says. “But I had no idea.”
This is 3M’s moment, one for which the staid, 118-year-old Minnesota manufacturing giant—the maker of Post-its, Scotch tape, touchscreen displays, and scores of other products—has been preparing for almost two decades. Read the full story: https://www.bloomberg.com/news/features/2020-03-25/3m-doubled-production-of-n95-face-masks-to-fight-coronavirus Source: bloomberg.com
Honeywell increases production of N95 face masks to support COVID-19 response
Honeywell is ramping up production of N95 masks in the United States to support the COVID-19 response. The production boost will come from the Honeywell factory in Smithfield, Rhode Island, which also produces UVEX safety glasses. The N95 face masks will be delivered to the U.S. Department of Health and Human Services for use to support health, safety and emergency response workers. Honeywell expects the new mask production line in Smithfield will create at least 500 jobs. Recruiting, hiring and training manufacturing workers will begin immediately. Source: honeywell.com
Klopman commits to produce 700k face masks per month
Klopman, a European manufacturer of protective fabrics, has committed to produce up to 700,000 protective masks per month, which are sterilizable and reusable up to 50 times, according to the company. Due to its capability in the production of fabrics for the medical and health sectors, the company has been included in Italy’s list of “essential” organizations. The masks will be made from a double layer of fabric to ensure maximum protection and comfort while in contact with the nose and mouth. A first batch of 10,000 masks will be donated to the health authority of Frosinone and to the hospital “Fabrizio Spaziani,” with a rapid response supply chain in place to serve the needs of public and private operators. In order to ensure a barrier effect with low particle release, Klopman said its masks will be based on the Vectron 8200 fabric, which is usually used in electronics, cleanrooms and in hospitals due to its characteristics, including a hydro/oil repellent finish to enable domestic and industrial washing at 75°C. Source: klopman.com
US FDA loosens restrictions on PPE and medical devices to bolster supplies for COVID-19 response
The U.S. Food and Drug Administration took action to increase U.S. supplies to support the U.S. response to COVID-19 by providing instructions to manufacturers importing personal protective equipment and other devices. One of FDA’s priorities in combating the COVID-19 pandemic is facilitating access to critical personal protective equipment (PPE) and devices. The agency is engaging with importers and others involved in the import trade community during this pandemic to facilitate the entry of needed products, including PPE, into the U.S. These instructions to importers clarify the types of PPE that can be imported without engaging with FDA. They also include information about the type of information importers can submit to facilitate their entries. The FDA has adjusted import screening to further expedite imports of legitimate products and are continually monitoring import systems to prevent and mitigate any potential issues. For more details on the FDA guidance on masks and respirators, see https://www.fda.gov/media/136449/download. Full guidance on medical gowns is still being drafted. The FDA also established a special email inbox, COVID19FDAIMPORTINQUIRIES@fda.hhs.gov, for industry representatives to quickly communicate with the agency and address questions or concerns. Source: www.fda.gov
EURATEX calls for clarity on facemask types and appropriate uses
As the impact of the corona crisis is growing, EURATEX, the European Textile and Apparel Confederation, is calling for a stronger coordination and cooperation among the EU and its member states, and clear communication on the required safety measures. Specifically, the global COVID-19 emergency has created an unprecedent global demand for protective masks to be used by healthcare, law enforcement, population and key business value chains. According to its modelling, the WHO estimates that each month there will be a request for 89 million medical masks. In the most affected regions, as Lombardy in Italy, the monthly demand for certified masks – only for healthcare workers – exceed 10 million. EURATEX is identifying options to increase the availability of protective masks in the EU, both by enhancing the existing capacity and creating new manufacturing capacity, including support to textile value-chain companies reconverting their production Under normal circumstances two main type of face protecting masks are put on the market:
- PPE masks protect persons from outside agents. Products must be certified by laboratories as per requirements of the PPE Regulation (typically harmonised standard EN 149) with level minimum FFP2 or better FFP3.
- Medical masks primarily protect patients from the wearer. Products shall meet requirements of the Medical Device Directive/Regulation (typically standard EN14683) by auto-certification and upon testing
In the present circumstances, masks offering a general protection are used as well. These masks offer different degrees of protection, depending on which materials are used and how they are made. These are usually intended for use by the population and are not meant to be used by healthcare workers. Public authorities should communicate clearly on the difference between these masks, and their level of protection. Source: euratex.eu
Reifenhäuser Reicofil converts its own meltblown test lines to facemask production
The German machinery and plant manufacturer Reifenhäuser Reicofil has temporarily converted two of its test plants to full production in response to the coronavirus pandemic. The lines installed in the company’s nonwovens technology center, which are otherwise exclusively used for research and development as well as customer trials, have been producing meltblown material for the production of urgently needed facemasks. Until further notice, the meltblown lines will be operated in 4-shift operation 24/7. The daily output is sufficient for up to one million facemasks. Reifenhäuser said trial operations will be almost completely suspended during this period. The meltblown material from the nonwoven technology center is already sold out for the next five weeks. However, Reifenhäuser continues to look for opportunities to strengthen the local supply during this crisis. The company is in close contact with associations, authorities and other companies. Material for other medical protective clothing could also be produced at short notice, according to Reifenhäuser. In related news, Reifenhäuser Reicofil is shortening the delivery time for meltblown lines to 3.5 months, with the aim of supporting the production of the crucial middle material layer for face masks. Supplies of face masks have been severely stressed in the face of the COVID-19 response. Dr. Bernd Kunze, CEO of Reifenhäuser Reicofil, said, “In situations like the current one, we gladly depart from customary procedures. Sticking to standards in a non-standard situation is out of place. It goes without saying that we will do everything in our power to serve the needs quickly and in the accustomed high quality.” The first contract with the new delivery time has already been concluded. The 1.6 meter wide Reicofil Meltblown line is scheduled to start operation in August 2020. With an annual output of 550 metric tons, the plant will produce H99 filter material for up to 1.8 million face masks a day. Source: reifenhauser.com
Ford joins 3M, GE in speeding up ventilator, respirator production
Ford Motor Co said it was working with General Electric’s healthcare unit and 3M Co to speed up production of ventilators for patients and respirators for healthcare workers as the coronavirus pandemic escalates. Source: https://www.reuters.com/article/us-health-coronavirus-ford-motor/ford-joins-3m-ge-in-speeding-up-ventilator-respirator-production-idUSKBN21B1PD
USTR requests input on lifting ‘Section 301’ duties on Chinese imports of medical-care products
In order to facilitate the U.S. response to COVID-19, the Office of the U.S. Trade Representative (USTR) has announced that it is now accepting comments from interested parties on the possibility of removing some of the additional “Section 301” duties that have been applied on various Chinese imported medical-care products. According to USTR, each submission must specifically identify the particular product of concern and explain precisely how the product relates to the response to the COVID-19 outbreak. For example, the comment may address whether a product is directly used to treat COVID-19 or to limit the outbreak, and/or whether the product is used in the production of needed medical-care products. Comments may be submitted regarding any product covered by the action in the investigation, regardless of whether the product is subject to a pending or denied exclusion request. However, submissions are limited to comments on products subject to the tariff actions and relevant to the medical response to the coronavirus. Source: inda.org For more information, click here.
BYD opens face mask and bottled disinfectant plant
BYD created what it describes as the world’s largest mass-produced face masks plant, which is running at full capacity and is able to produce 5 million masks and 300,000 bottles of disinfectants per day. This allows the firm to help alleviate severe shortages that have affected hospitals and agencies across China in the face of the global COVID-19 outbreak. On February 8, the newly-built production lines in one of BYD’s industrial parks in Shenzhen started to produce these critical supplies, with hundreds of staff working both day and night shifts along with machines working around the clock. In late January, BYD began to assist in the production of masks and disinfection gels to tackle the growing COVID-19 outbreak. A special task force was appointed by BYD chairman and president Wang Chuanfu, consisting of leaders from different business divisions and more than 3,000 engineers involved in research and development, design, processing and other roles. The task force moved in less than two weeks to finish work that normally takes two months, completing both the R&D and manufacturing process of mask production equipment within seven days, with the completion of R&D for medical-grade hand sanitizers in six days. Supplies were shipped to medical staff dealing with the COVID-19 response in China. Source: byd.com
EU takes action to procure ventilators, masks and medical equipment
European Parliament is working with member states to ensure that the EU can buy ventilators, masks and other medical equipment to be put at the disposal of hospitals across the EU.Last week, the Commission set up a scheme to gather medical equipment (through rescEU) so that the necessary supplies to combat COVID-19 can quickly get to member states facing shortages of equipment. This equipment is needed to treat infected patients, protect health care workers and help slow down the spread of the virus.
Parliament is working with member states to swiftly approve 40 out of 50 million EUR for intensive care medical equipment such as ventilators and personal protective equipment, such as reusable masks. Member states are also joining forces under the Joint Procurement Agreement to buy personal protective equipment, respiratory ventilators and items necessary for coronavirus testing. Working together in this way will give them a stronger position on the world market. Source: https://www.europarl.europa.eu/news/en/press-room/20200323IPR75622/covid-19-eu-institutions-take-action-to-procure-life-saving-medical-equipmentTextile and apparel brands to build supply chain for emergency manufacturing of medical facemasks
American apparel brands and textile companies are responding to a White House request for medical supplies, building a supply chain to fast-track the manufacturing of medical face masks. Parkdale Inc.– the largest yarn spinner in the U.S. headquartered in North Carolina—helped lead the effort to build the coalition with Hanesbrands, Fruit of the Loom and six other companies to set up a manufacturing supply chain and begin ramping up production of the masks. The coalition consists of Hanesbrands and Fruit of the Loom, often competitors in the marketplace, who are banding together for the greater good of a nation facing one if its most monumental challenges. American Giant, Los Angeles Apparel, AST Sportswear, Sanmar, America Knits, Beverly Knits and Riegel Linen are also part of the coalition working tirelessly to respond to a national emergency in the nation’s time of need. Dr. Peter Navarro, assistant to the President and director of the White House Office of Trade and Manufacturing Policy, worked with the coalition and helped expedite the production of these masks. The first face masks have been approved by the U.S. Department of Health and Human Services. The companies expect to begin production on Monday and will make the first deliveries by mid-week. If companies are interested in dedicating resources to help the cause, please reach out to the National Council of Textile Organizations at kellis@ncto.org NCTO is a Washington, DC-based trade association that represents domestic textile manufacturers, including artificial and synthetic filament and fiber producers. Source: ncto.org Related Story: “NC textile mill ‘heeds call of nation,’ gears up to make 10 million face masks per week” Related article: https://www.filtnews.com/as-coronavirus-surges-filtration-questions-arise/
U.S. Textile and Nonwoven Associations Urge Government to Deem Manufacturing Facilities “Essential”
U.S. textile and nonwoven associations issued a joint statement today urging federal, state and local governments to deem textile and nonwoven manufacturing facilities as “essential” when drafting “Shelter in Place” orders in response to the COVID-19 crisis. The statement was sponsored by the National Council of Textile Organizations (NCTO), INDA (Association of the Nonwoven Fabrics Industry) and Industrial Fabrics Association International (IFAI). Our associations recognize the serious challenges our elected officials, health administrators and others are facing when issuing orders to protect communities across the country and we understand the necessity for leaders to enforce a ‘Shelter in Place” order or quarantine orders. Our members make a broad range of inputs and finished products used in an array of personal protective equipment (PPE) and medical nonwoven/textile supplies, including surgical gowns, face masks, antibacterial wipes, lab coats, blood pressure cuffs, cotton swabs and hazmat suits. These items are vital to the government’s effort to ramp up emergency production of these critical supplies. If workers who produce these goods are not granted an “essential” exemption from “Shelter in Place” and other quarantine orders to go to their manufacturing and distribution facilities, it will cause major disruptions in the availability of these goods. This will create significant hardship to healthcare providers and consumers across the country who depend on steady and stable supplies of these critical items. We are asking the administration and state and local authorities to provide greater certainty and clarity for our companies and employees and ask for a clear exclusion of our manufacturing operations from “Shelter in Place” orders as the textile and nonwoven products that we make in the U.S. play an essential role in mitigating the shortages of critical supplies. Such a designation will help us avoid disruptions of vital goods and services during this challenging time. Source: inda.org, ifai.com, ncto.org
EDANA, European Safety Foundation, EURATEX collaborate to address COVID-19 supply chain issues
While the European Commission is currently looking at mapping the need for masks in the Member States, first estimates show that no less than 250 million medical masks and 30 to 40 million personal protective equipment (PPE) masks will be needed on a monthly basis in the EU for the battle against the COVID pandemic. In this context EDANA, the European Disposables and Nonwovens Association, is working closer than ever with the European Safety Foundation and EURATEX, the European Apparel and Textile Confederation, to support supply chain efforts for PPE and medical supplies. Actions include:
- Providing the European Commission with the necessary information to accelerate the procurement of medical facemasks and protective masks in the EU
- Matchmaking suppliers of materials needed to create medical facemasks and personal protective masks with existing or prospective manufacturers of these
In its efforts to reach out and share information EDANA is also working together with MedTech, the European trade association for the medical technology industry including diagnostics, medical devices and digital health. The organization also issued a message to the European Commission, noting that any export ban or restriction would be potentially counter-productive, since in the short and medium term, whether one likes it or not, the supply of medical face masks and personal protective equipment in the EU heavily depends on third countries, in particular from Asia. Source: edana.org
COVID-19 Has Caused A Shortage Of Face Masks. But They’re Surprisingly Hard To Make
Both the masks made for medical personnel and for consumer purchase require a once-obscure material called melt-blown fabric. It’s an extremely fine mesh of synthetic polymer fibers that forms the critical inner filtration layer of a mask, allowing the wearer to breath while reducing the inflow of possible infectious particles. “We’re talking about fibers where one filament has a diameter of less than one micron, so we are in the nano area,” said Markus Müller, the sales director at German company Reicofil, a major provider of melt-blown machine lines. And there’s now a global shortage of melt-blown fabric due to the increased demand for masks — and the difficulty in producing this material. Source: https://www.npr.org/sections/goatsandsoda/2020/03/16/814929294/covid-19-has-caused-a-shortage-of-face-masks-but-theyre-surprisingly-hard-to-mak Related article: https://www.filtnews.com/when-the-unexpected-happens-are-todays-filtration-sytems-ready-for-the-challenge/
Sionopec puts meltblown assembly line into operation
Sinopec Corp, China’s leading energy and chemical company, put its first meltblown nonwoven fabric assembly line into operation at its Yanshan factory in Beijing on March 6. The Yanshan factory is a converted 3,600 square meter old warehouse that has found new life as a global production base following the challenges brought by the coronavirus outbreak.
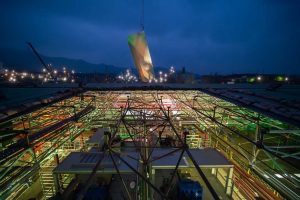
The 14,400-ton capacity Yanshan facility is one of Sinopec’s two meltblown nonwoven fabric assembly bases and is co-managed with China National Machinery Industry Corporation. The base has two nonwoven production lines and three spunbond production lines and can produce up to 4 tons of melt-blown fabric for 1.2 million N95 disposable masks or 6 tons for 6 million disposable masks per day. The new facility also takes advantage of Sinopec’s integrated upstream supply-chain by sourcing local materials from Yanshan and support from the on-site synthetic resin production line. Source: sinopecgroup.com
Across Asia, countries race to boost face mask supplies
At a face mask factory just outside the South Korean capital of Seoul, workers are churning out 300,000 masks a day – and it’s still not enough. Source: https://www.reuters.com/article/us-health-coronavirus-masks/across-asia-countries-race-to-boost-face-mask-supplies-idUSKBN20T16A
3M taps regional suppliers to meet soaring demand for masks
The U.S. Department of Health and Human Services intends to buy 500 million N95 respirators over the next 18 months for the Strategic National Stockpile (SNS), the nation’s supply of pharmaceuticals and medical supplies. Source: https://www.reuters.com/article/us-health-coronavirus-3m-idUSKBN20S214
Squabble over mask shortage erupts as coronavirus spreads
At a visit to 3M in Minnesota, Vice President Mike Pence noted the company can currently only produce 4 million FDA-blessed surgical masks per month. Source: https://www.politico.com/news/2020/03/05/coronavirus-mask-shortage-122152
U.S. to Ramp Up Mask Production, But China Is Bottleneck for Raw Materials
Honeywell International Inc is the other major U.S. mask producer, which is aiming to ramp up production. Source: https://globalbiodefense.com/headlines/u-s-to-ramp-up-mask-production-but-china-is-bottleneck-for-raw-materials/
3M can’t confirm Pence comments about making more masks
Jennifer Ehrlich, a 3M communications manager said in an e-mail late Saturday that any information about government contracts for respirators would have to come from the Office of the Vice President. However, Ehrlich added, “Just to clarify, we are not yet under contract for the volume mentioned today. However, we are preparing to respond to the U.S. administration’s request for a proposal for respirators. 3M continues to maximize production at its manufacturing facilities in the U.S. and around the world for all types of N95 respirators.” Source: http://www.startribune.com/3m-can-t-confirm-pence-comments-about-making-more-masks/568354132/
US mulls using sweeping powers to ramp up production of coronavirus protective gear
The Trump administration is considering invoking special powers to rapidly expand domestic manufacturing of protective masks and clothing to combat the coronavirus in the U.S., two officials told Reuters. The biggest producers of face masks in the United States include 3M Corp and Honeywell International Inc. Health and Human Services (HHS) Secretary Alex Azar said at a congressional hearing on Wednesday that China controls “a lot of the raw materials as well as the manufacturing capacity” related to face masks. Very little of this stuff is apparently made in the (United) States, so if we’re down to domestic capability to produce, it could get tough,” the DHS official told Reuters. Source: https://www.cnbc.com/2020/02/28/us-mulls-using-sweeping-powers-to-ramp-up-production-of-coronavirus-protective-gear.html
3M ramps up N95 respirator production as demand surges from global coronavirus outbreak
From the streets of Beijing to Milan Fashion Week, people around the world are turning to protective masks and respirators to try and reduce the risk of infection amid the global outbreak of coronavirus. Demand is so high that it’s increasingly difficult to order respirators on e-commerce platforms like Amazon. “We’re seeing outbreaks develop in new countries every day. But even the countries where there isn’t a widespread outbreak are working really hard to prepare right now, in case they do have that situation,” Dr. Nikki McCullough, 3M’s global head of safety, told CNBC. Source: https://www.cnbc.com/2020/02/28/3m-ramps-up-n95-respirator-production-amid-global-coronavirus-outbreak.html