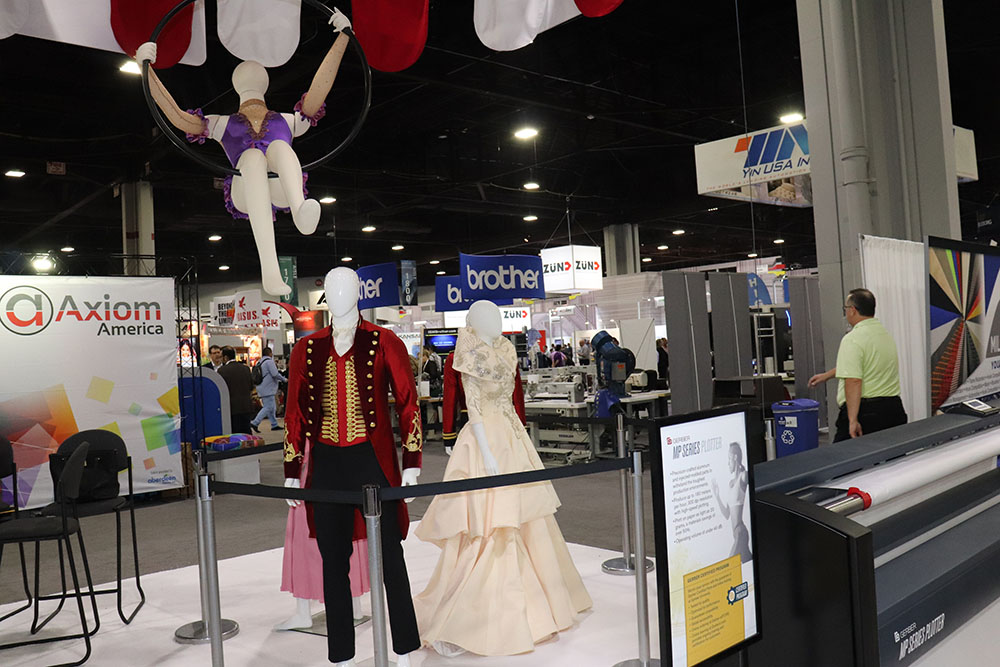
The combined Techtextil North America and Texprocess Americas shows, which took place at the Georgia World Congress Center in Atlanta from May 22-24, drew together some 536 exhibitors from 32 countries, setting new records for both exhibitors (up 26%) and square meters of space sold (up 14%).
The event was dominated by Germany’s 1,300-square meter High-Tex showcase featuring the technical textile technologies of some 66 German companies, and there were also sizeable pavilions for China, Italy and Taiwan.
High-Tex from Germany was sponsored in Atlanta for the second time by the country’s Federal Ministry of Economics and Energy in cooperation with AUMA, the Association of the German Trade Fair Industry. It made its first appearance in Atlanta in 2000, followed by highly successful presentations in Shanghai in 2002, in Mumbai in 2007, and in Moscow in 2012.
Tradition
“Bringing High-Tex from Germany back to Atlanta was a very good decision,” said Detlev Rünger, the German Consul General in Atlanta. “The southeast of the USA has a long tradition of textile manufacturing and is home to many companies which are always on the lookout for innovative textiles and machines for textile production and processing.”
“The USA is one of the most important export markets for German textile companies,” added Marc Lorch, president of the High-Tex event. “Last year German companies exported textiles worth €688 million to the USA, in addition to textile machinery worth €84 million, making it the most important market for the country outside Europe.”
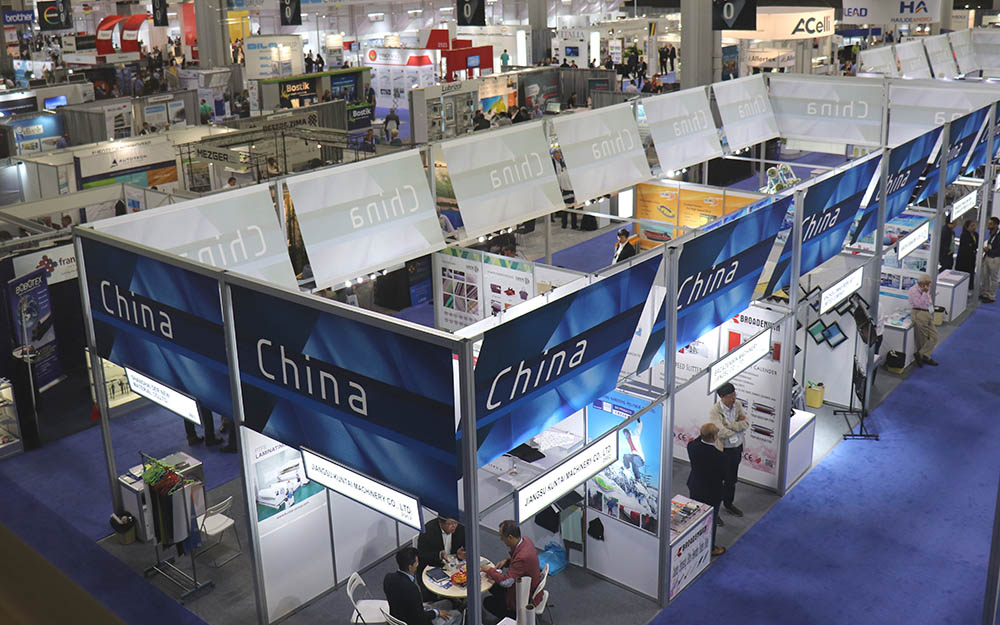
Opportunities
Dave Gardner, of organizer Messe Frankfurt’s partner SPESA – the Sewn Products and Equipment Suppliers of the Americas – said that his industry was happier than it had been for a very long time with the opportunities presented for the reshoring of manufacturing that is being enabled by new technologies.
“These new technologies are ensuring that manufacturers can achieve the quality, reproducibility and speed required to thrive and a lot of people are looking to them to bring jobs back to where the key consumer markets are,” he said. “The US textile worker is now three times more productive than in 1980 and twice as productive as in 2000. US textile shipments are up 6.7% and the fashion market is now growing at 3.5-4.5%.”
Micro-factories
Disruptive technologies on the horizon will soon become the norm, he added, referring to the automation that has led to the promotion of so-called ‘micro-factories’, involving much closer collaborations between individual companies.
Gerber Technology, for example, partnered with Kornit Digital and Henderson Sewing Machine Company to demonstrate a complete on-demand micro-factory. This encompassed 3D simulation, vision-aided cutting and direct-to-textile digital printing – along with ‘Gerbie’ the robot who transported cut pieces from Gerber’s cutting machine across the hall to Henderson’s robotic sewing center.
“This concept highlights how data management, connected systems and automation can enable purchase-activated production, redefining the concept of just-in-time manufacturing,” said Gerber’s chief marketing officer Bill Grindle. “The need for speed is imperative and automation is the key to allowing the apparel market to get products to market faster.”
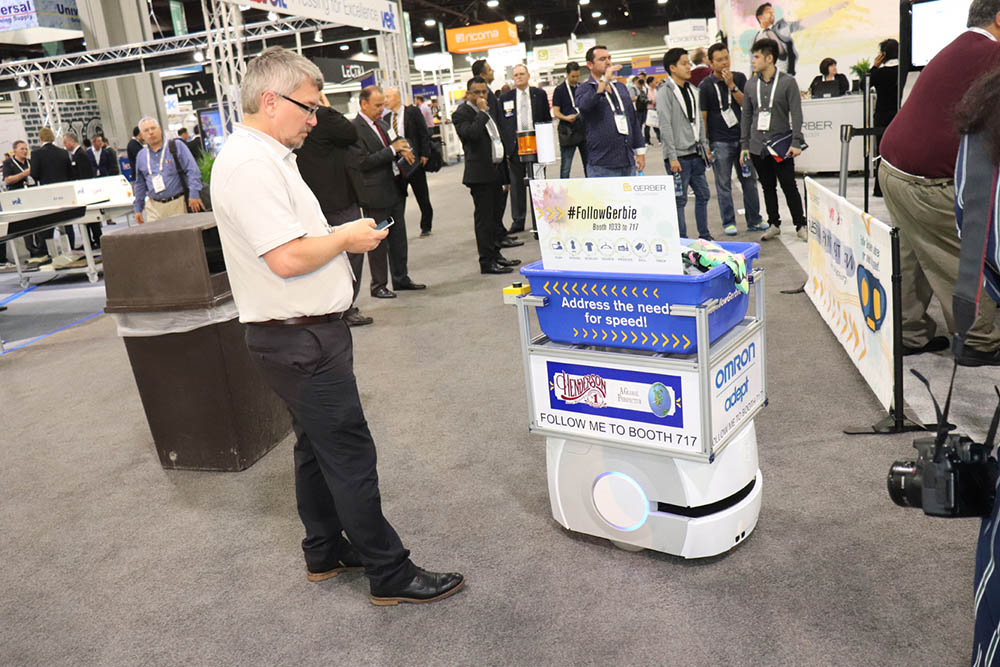
Gerber and Kornit executives spoke of the complete revenue conversion such set-ups are enabling, with the eight months traditionally needed in traditional garment manufacturing from design to delivery being reduced to just eight hours from design to fully-validated prototype, and thousands of items being shipped to customers within just eight days.
It was pointed out that H&M – as a leading fast fashion retailer, if by no means the biggest – recently reported it has some $4.3 billion worth of unsold inventory on its racks, and the just-in-time systems now being developed have the ability to make such problematic scenarios disappear.
“There’s the potential here to make all of that waste – and the associated costs of materials and resources – vanish, by enabling a completely new supply chain economic model,” said Grindle. “And this is not pie in the sky – it’s happening now.”
A similar concept was detailed by the Swiss cutting systems developer Zünd, again working with Henderson, and also EFF Reggiani and Klieverik. In addition, Qondac, the new automation arm of German sewing technology leader Dürkopp Adler, demonstrated new networked infrastructures and a robotic sewing system, while Lectra introduced its new Cutting Room 4.0 system and the Virga single-ply cutting solution.
Lectra’s system digitally transfers information between IT systems and the cutting room and automates non-value-added tasks. Virga offers a complete cutting line for simultaneous loading, scanning, cutting and offloading.
An addition to cutting intelligence was introduced by Italy’s Caron, with new software that identifies whether or not a fabric fault falls within or without a cutting pattern on a fully nested fabric, for further optimization.
Innovation Tour
Stops at Caron, Gerber, Qondac and Lectra were all included in two special tours for journalists arranged by Messe Frankfurt, taking in the latest innovations of a wide range of companies operating all along the textile manufacturing supply chain, from fiber to finished product.
They included 3dMD, a leader in the development of anatomically-precise 3D and “temporal-3D” (4D) surface imaging systems and the sophisticated software required to support serious applications in healthcare, biometrics, ergonomics, research, size and fit, and already has more than 1,500 3dMD units in use by customers across the globe.
“We are now seeing big opportunities in the textiles field due to online shopping and there are also so many new technologies coming along that will be wearable, such as VR headsets, where precise sizing will be essential,” said Chris Lane with 3dMD. “We have come out of the medical sphere where precision images are the norm, so why shouldn’t that apply to what people wear on a daily basis too?”
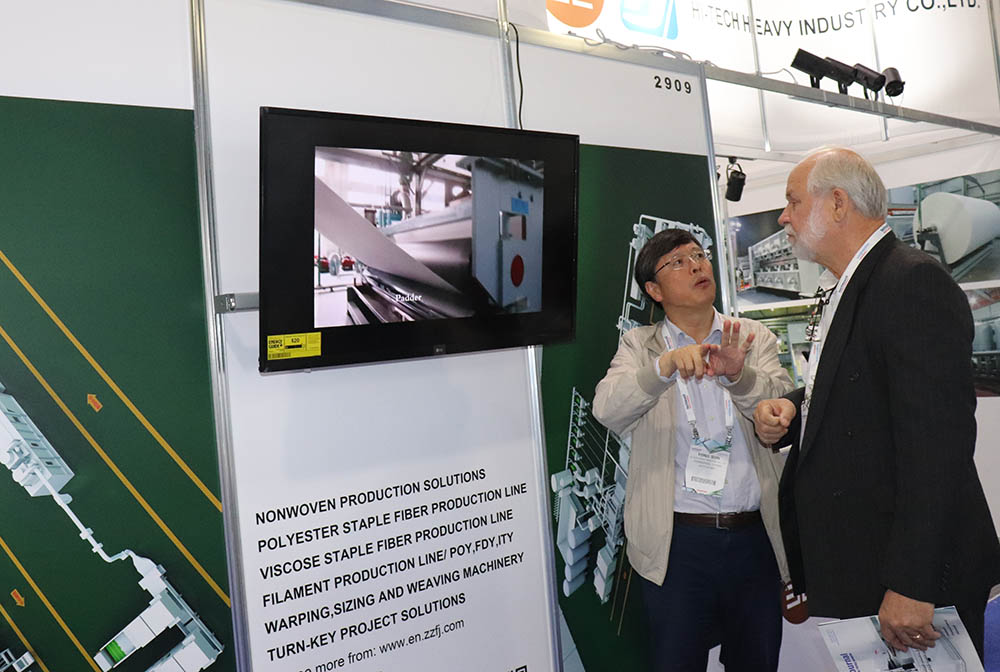
Flame resistance
In yarn developments, Canada’s Filspec displayed welder coveralls made from its latest Firefil which is based on a fiberglass filament core and provides extreme fire resistance. Fabrics for workwear woven from the yarn do not melt or drip when confronted with flames and the yarns will not shrink in extreme heat. They also have a tear strength that is 200% higher than NFPA requirements.
CTF2000 of Belgium meanwhile introduced its Flamaway as a patented process for making cotton and cotton blends flame retardant.
Flamaway is locked into place at the fiber level and does not compromise on the softness, moisture regulation or safety of a garment, remaining invisible until a flame turns the fabric into a strong char.
Sewing threads
A range of new sewing threads were showcased by American & Efird (A&E), including Anefil Poly, a 100% recycled, twisted multifilament based on Unifi’s Repreve polyester. Anefil Poly is said to provide excellent color fastness with good chemical resistance and has been engineered to provide excellent performance on both manual and automatic sewing machines. Benefits include seam integrity and excellent strength and abrasion resistance.
Repel is a new A&E PFC-free water-repelling thread engineered to meet the needs of retailers and brands in eliminating PFCs in their products, while Anefil Reflector adds luminescence to garments – an area also being explored by Germany’s Lunative.
This start-up company was a 2017 winner of the German Design Award for its LUNAlight smart light wear technology, which adds a homogeneous and pleasant light to fabrics. The company supplies customers with special kits for the seamless integration of its proprietary decorative piping into textiles. LUNAlight is flexible and lightweight, adjustable and highly customizable. Garments containing the technology can be washed at 30ºC and are completely safe.
Lunative has made limited edition garments for car manufacturer Audi and also air hostess uniforms containing its technology for Lufthansa.
Embroidered electronics
Germany’s ZSK demonstrated its embroidery technologies for adding tailored sensors and heating elements to fabrics, and also a machine for freely placing and fixing reinforcement materials.
The latter can be used in applications where the production of components or textile structures requires the stitching of variable geometry ply stacks, or where composite reinforcement fabrics need to be reinforced locally.
The system is suitable for various materials, including carbon, glass and aramid fibers, as well as wires etc. In the process, the single layered rovings are fixed to the base material by stitching and the base material is moved by the pantograph, enabling it to lay rovings in any direction and quantity.
E-textiles
Japan’s Mitsufuji Corporation has worked with seamless knitting leader Shima Seiki to develop a range of new e-textile applications for its Hamon-branded seamless fabrics, based on its AGposs silver-metalized conductive filaments, fibers and yarns.
“The 99.9% silver surface of our fibers makes them perfect in systems for the collection of biometric data,” explained the company’s sales manager Kota Yamazaki. “A very clear signal can be obtained with no noise. Our Hamon systems are gaining traction in the USA and we’ve now established an office in New York.”
Another development showcased by Mitsufuji was a seamless undergarment system equipped with active water cooling for workers in hot environments.
Nano pigments
Organic Dyes and Pigments is the exclusive Americas-wide distributor of Peracto nano pigment dispersions and inkjet inks which exploit a colorant nanotechnology offering extremely energy-efficient and environmentally friendly textile padding and inkjet printing, requiring no pre-treatment or post-treatment.
The drawbacks with current systems, explained business development manager Randy Yorston, are that each type of fiber requires different dye or ink classes and blends of different fibers must be treated twice.
“Pre-treatment of the textile is typically required before printing or pad-dyeing and large amounts of water are needed for pre and post-treatment, dramatically increasing energy costs,” he said. “For digital printing, different processes, printers and print heads are needed and for pad-dyeing, different process equipment is required.”
Peracto can enable a 50% reduction of process costs compared to traditional continuous dyeing processes, he added, and processes are simplified, with the possible elimination of pre-treatment or fabric differentiated post-treatments and reduced water consumption.
“It is compatible with current dyeing and printing equipment and leads to much higher efficiency, using a single colorant system to dye all synthetic and natural fibers and no change of ink or dye chemistry for different fibers. 4A wash-fastness ratings can be achieved.
Interior designs
Some very attractive home furnishing products, including a flexible partition and elegant seating cubes were displayed by Germany’s nonwovens leader Sandler, from the company’s 100% polyester fibercomfort range for sound dampening and technical insulation.
These nonwovens are designed for use as components of wall and ceiling systems, partitions, furniture or wall decorations, to create a quiet environment in the home or workplace.
“Fibercomfort nonwovens are available in different thicknesses and densities and can be soft and voluminous or compacted and self-supporting, as well as with a specially smoothed or open-pore surface,” explained the company’s project manager Christian Szwarc. “Through further processing, the nonwovens can be enhanced with print motifs, laminated, flocked to create a roughcast look or coated with natural materials to create individual design elements and add original looks to every room.”
Techtextil NA 2019
The developments mentioned in this article represent just the tip of the iceberg of what was to be discovered at Techtextil and Texprocess North America 2018. The 2019 Techtextil North America will fittingly be held in Raleigh, North Carolina, February 26-28, 2019.
North Carolina’s rich history in textile production dates back to the 1800s and today serves as the location of several of the most important global textile companies, industry associations and educational resources. North Carolina leads the US in the textile mill industry with over 700 textile manufacturing establishments and over 42,000 industry workers.
In addition, North Carolina State University’s College of Textiles, located in Raleigh, serves as a hub for textile research and development and as a primary supplier to the industry talent pipeline nationwide.
“We are thrilled to announce Raleigh as the destination city for Techtextil North America 2019,” said Dennis Smith, president of Messe Frankfurt North America. “Not only is North Carolina an international hub for industry and innovation in textiles, but the city of Raleigh has become one of the fastest growing, more forward-thinking in the nation.”