Strong competition in the manmade fiber industry pushes all fiber producers to increase their quality level while maintaining low operating cost. Following these needs, MAE SpA of Italy along with its affiliates, has been active in providing innovative and reliable solution for the industry. MAE recently added to its portfolio the IGH brand in order to provide a complete solution for handling of fiber bobbins. Flexible, powerful and reliable automatic bobbins handling systems can be a crucial help in order to:
- Eliminate bobbins manual handling
- Link the production data to each bobbin automatically
- Track production data for each bobbin
- Improve the total quality control system
- Reduce operator time for bobbin inspection
- Reduce number of operators in production process
- Improve management of massive as well as flexible productions
IGH is the result of the merging of technical experiences and capabilities of two long time established companies, Gualchierani and Irico. The result is a team of technicians specialized to bring to customers tailor made solutions in bobbin handling, aware that each fiber production factory has unique and specific requirements.
Through MAE’s established global organization, IGH is able to grant optimized after-sales service and specialized interventions.
IGH designs and manufactures equipment and complete automatic handling lines for different fiber production areas and it is constantly involved in the research and technological updates of its own products, providing a complete range of solutions controlled by the most sophisticated and personalized computer systems. The range of products offered by MAE under its IGH brand includes:

Winder doffing system: On this system a doffer robot (IGDOFF) unloads automatically the bobbins from the winder to bring them out of the production area, recording the data relevant to the bobbin produced for its future tracking. IGH has successfully installed powerful doffing systems suitable to manage more than 9,000 bobbins per day. Picture 1 shows a doffer suitable to handle 24 bobbins loaded on 2 spindles at 1800 mm length, suitable to serve the most advanced bobbin winders available in the market. Advanced design concept allows the model HS to run at very high speed in order to work on long winder tunnels without affecting the operators safety, increasing the efficiency of the system. One HS doffer can handle the work of two standard doffers commonly available in the market.
IGH also supplies small doffing units with a capacity of just 2,000 bobbins a day with contemporary management of 20+ production lots and matching requirement of very high flexible production factories.
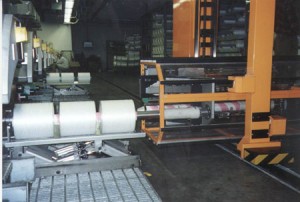
Picture 2 shows a doffer for a 900 mm spindle 3 packages BCF winder, which requires fast doffing cycle for the BCF high-count production.
The winder doffing system avoids having operators touch yarn bobbins, preserving the quality of the yarn produced. Moreover, the number of operators required in the spinning department is drastically reduced, with a clear advantage in the reduction of operation costs.
The winder doffing system can be integrated with other features including:
- Automatic paper tubes loading on winder spindle
- Automatic creel loading
- Automatic tail rotation
- Automatic labeling
The IGH doffers work for all kind of winders and for all type of yarn, like POY, FDY, BCF, HTY, Carbon fiber, Glass fibers, and others.
In-factory bobbin handling: After doffing the bobbins have to be moved to other areas of the factory to be further processed or packed, stored or moved outside the factory. IGH has several solutions for transporting the bobbins, depending on space and height available. Overhead carrier, dedicated on-floor carrier, trolley carrier, AGV are all available systems for a proper bobbin transport that IGH customizes according to customer’s request.
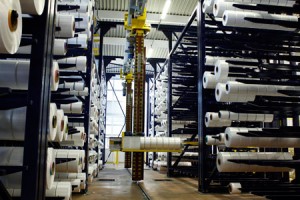
Buffer and temporary warehouses are also required, in different sizes and structures, to handle the different production lots and quality grades for a more rational handling.
Picture 3 shows an example of a compact pin temporary warehouse.
Handling also includes all operations for bobbin sorting. To improve the efficiency of sorting, IGH has implemented systems to facilitate the visual inspection by the operators. For the sorting, IGH provides:
- Automatic bobbins weighing
- Automatic bobbins labeling
- Operator interface to define the quality grade for each bobbin
- Bobbin knotting station
Packing system: IGH provides a total automatic packing system (IGPACK) to prepare pallet for storage and/or delivery to customers. The packing systems are compact to reduce the total occupied area. They are based on a mix of anthropomorphic and gantry robots to move automatically and with the maximum flexibility of the parts composing the final pallet. Main actions of the packing systems are:
- Loading from trolley or from bobbin conveying unit
- Wooden pallet support handling
- Carton box shaping
- Separator layer handling (with or without bobbin holder), in various material and different maps
- Bobbin wrapping
- Separation layer handling
- Pallet strapping
- Pallet weighing
- Pallet wrapping
- Pallet labeling
IGH has also successfully installed powerful packing systems suitable to manage multiple 30,000 bobbins per day production lots. IGH supplies packing systems for medium capacity production lots as well. For the small production units dedicated to specialty yarn, with the peculiarity to produce many small lots at the same time, IGH can supply automatic and semi-automatic packing systems using small flexible robots and in-line bobbin storages.
DTY HANDLING AND PACKING SYSTEM
IGH supplies complete handling and packing system for DTY bobbins, with the required flexibility to manage a high number of lots. The design of the handling and packing system is optimized based on customer requirements, since the number of DTY machines, available space, and number of lots are very different from case to case. All features explained on the IGPACK system are implemented for the DTY packing also.
CARBON FIBER AND GLASS FIBER

For carbon and glass fibers IGH has developed a lot of customized solutions taking into account the peculiarity of the packages to be handled. These solutions are available for IGH customers on demand. Picture 4 shows an example of a doffing system for glass fiber.
IGH can integrate all above systems with bobbin handling from different production areas for a total integrated automatic bobbin management system to get the maximum results in terms of quality and efficiency.
Maintenance interventions and costs are drastically reduced, as the number of mechanical devices is limited to the very essential, giving high efficiency performances to the IGH systems.
For more information contact:
MAE SpA
IGH – Irico Gualchierani Handling Division
Via Lizzadri N°1
29017 – Fiorenzuola D’Arda (PC), Italy
Email: info@maeliz.com lacitignola@ighandling.it