Harshal Chokhawala, Co-Founder & CEO, Shares the Vision for BAYSE™ – the World’s
First Scalable, Bio-Based, Microplastic-Free, Biodegradable Super Absorbent Polymer
Super Absorbent Polymer (SAP) is the key ingredient for any hygiene product in the marketplace that is meant to absorb fluids and provide protection for baby and adult diapers, and sanitary napkins, among others. SAP is traditionally a petroleum-based product that is not biodegradable and contains plastics and chemicals that when released disrupts soil moisture balance. Products made with SAPs are taking the heat when it comes to these end-of-life environmental implications. The industry is taking this seriously and is rising to the challenge to explore bio-based solutions.
The biggest hurdle to most bio-based solutions in development now is industrial scalability. Laboratory-proven bio-SAP is under development across the supply chain; the challenge is being able to produce it in mass and be able to easily adapt to current production and manufacturing processes in place.
At the recent Hygienix 2024 in Nashville, TN in November, ZymoChem revealed their historic achievement in bio-SAP production. The San Leandro, CA, company announced the launch of BAYSE™, the world’s first scalable, bio-based, microplastic-free, and biodegradable Super Absorbent Polymer, set to revolutionize the $145 billion global hygiene industry and pave the way for a more sustainable future.
“We’re upending the materials industry. Our technology delivers sustainability without compromising performance, scale, and importantly, economics.”
— Harshal Chokhawala, Co-Founder & Chief Executive Officer
BAYSE™ is a drop-in replacement for traditional, fossil fuel-based SAPs, which are a key component in disposable, absorbent hygiene products such as infant diapers. Unlike petroleum-derived, polyacrylate counterparts, BAYSE™ is made from renewable resources, maintains a lower carbon footprint, and is readily biodegradable, addressing the environmental concerns associated with the 300,000 diapers that enter landfills or are incinerated every minute.
What is even more important, the company shared that ZymoChem’s proprietary technology platform enables the production of BAYSE™ at a cost which is competitive with traditional SAPs, ensuring that sustainability can be achieved without the need for a “green premium.” This emphasis on delivering novel materials to the market that meet the performance expectations of consumers and do so at a cost that is approachable is central to ZymoChem’s product design approach and how it is posed to make an outsized impact on the industry.
ZymoChem is breakthrough science for a fossil-free future. ZymoChem envisions a world in which the goods consumers depend on everyday are bio-manufactured from 100% renewable materials and designed for a sustainable economy. Through their multi-generational and multi-product patents, ZymoChem’s proprietary Carbon Conserving (C2) microbes convert renewable feedstocks into bio-based materials without compromising price, performance, scale, or sustainability, while radically minimizing CO2 loss during the production phase.
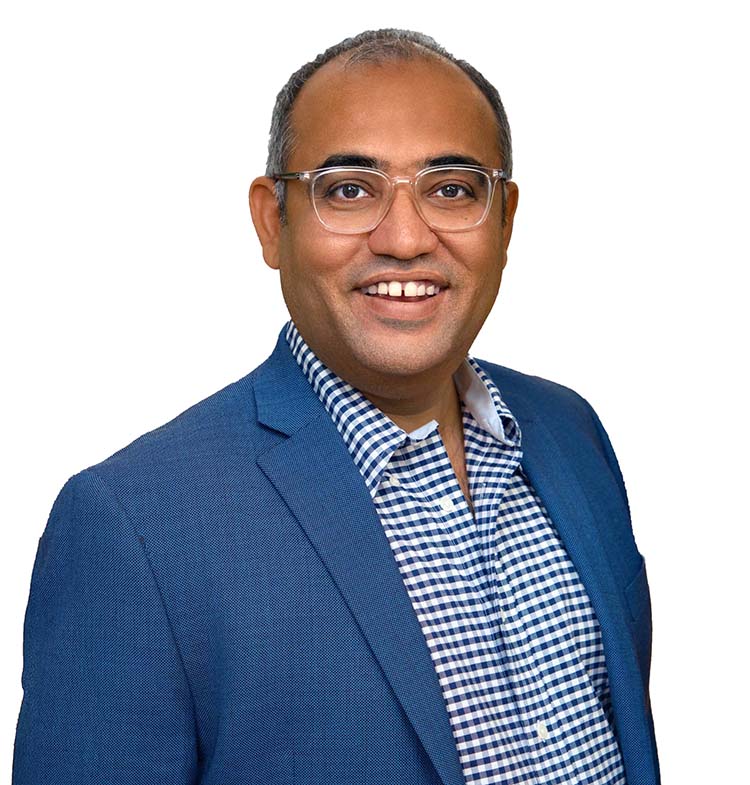
The company is led by Dr. Harshal Chokhawala, PhD, Co-Founder & CEO. Chokhawala is a dynamic leader in the field of biotechnology, renowned for his groundbreaking work in decarbonization and sustainable manufacturing practices. Given his deep expertise, Chokhawala offers invaluable insights into the future of clean energy, green technology, and the role of innovation in combating climate change. He navigated ZymoChem’s evolution from an idea on paper to a well-funded entity, securing backing from venture capital, government grants, and collaborations with Fortune 500 companies.
To support the scale up of BAYSE™ and the rest of ZymoChem’s product portfolio, this early stage company relies on a syndicate of progressive thinking venture investors. In 2024, ZymoChem raised a $21 million Series A round of funding with investments led by Breakout Ventures. Participation came from well recognized, new investors including lululemon athletica, inc. and Toyota Ventures, and existing investors including GS Futures, KdT Ventures, and Cavallo Ventures.
International Fiber Journal sat down to talk with Chokhawala at the Hygienix Show to discuss how all this came about, and how they were able to engineer the first to scale bio-SAP.
International Fiber Journal: Tell us about your company and its evolution.
Harshal Chokhawala: We’ve been operating since 2015 as a growing company. In the beginning, coming out of University of California Berkley, my co-founder Jon Kuchenreuther and I were heavily into the research side of how to engineer microbes and build the technology for the microbes.
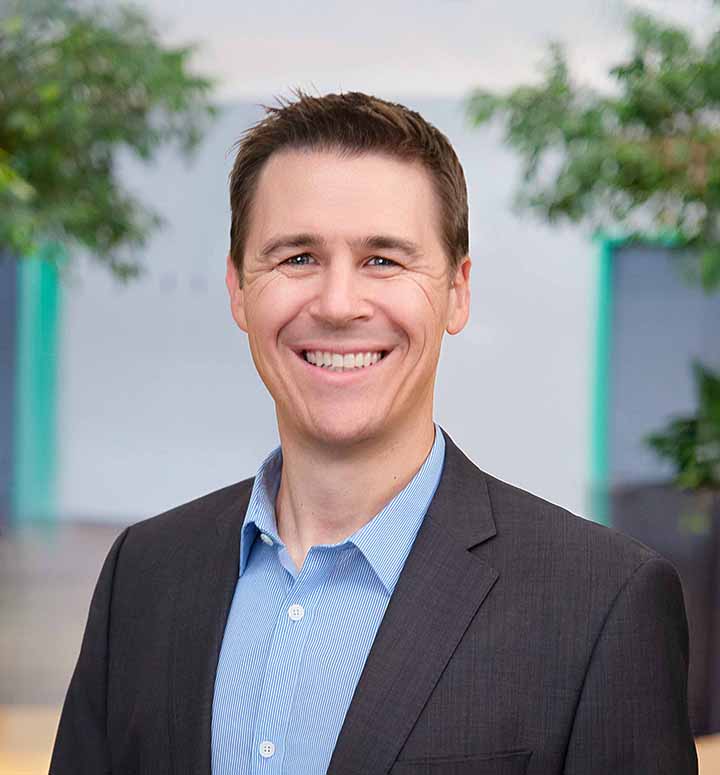
When we formally incorporated in 2015, we were accepted into the National Institute of Biomedical Imaging and Bioengineering (NIBIB) program that support biomedical engineering and research.
We received multiple Department of Energy grants, joined Breakout Labs and were backed by the Thiel Foundation and partnered with Agile BioFoundry, which is funded by U.S. Department of Energy BETO.
With all this activity to support our platform development, it was in 2019 that we started transitioning from a research organization to a more commercial organization. ZymoChem underwent its first growth surge, when the applications for our polymers business expanded.
We were very focused on replacing materials that existed today. Rather then sourcing from petroleum, our ingredients are made from sugar or other renewable carbon sources via fermentation. It is from here that we are have found incredible applications for our specialty chemicals, like a super absorbent in hygiene articles.
IFJ: What is your marketplace for BAYSE™? What makes it different?
Chokhawala: We are very excited that in 2024, we announced the launch of our first commercial product, which is the low-carbon footprint bio-based super absorbent polymer, called BAYSE™. That has been exceptionally exciting for ZymoChem from a product perspective. We also announced the close of Series A round of funding, raising $21 million with iconic companies investing and partnering with us. So, 2024 was a fantastic year. We grew the team to 60, from under 20 just two and a half years ago. And that expansion has been in support of this initial product.
In terms of the market, we are a North American company, so we will start here, but we want the sustainability and this product to be global. We’re upending the materials industry. Our technology delivers sustainability without compromising performance, scale, and importantly,
economics.
What makes us different is the technology. The molecule is different. We’re bringing a different molecule to the table that shows great promise, and the approach is different. We have leveraged a biotech fermentation-based process, and that’s relatively new in the industry. The SAP market is built off of polyacrylic acid. Similar to how PLA has made an impression on the plastics industry with a novel take, we’re doing this with a different material called PGA – polyglutamic acid.
We’ve been developing this technology for almost a decade now, and we have been incredibly fortunate to have the support, the investment, and the commercialization expertise of some of the largest companies on the planet, including brands such as lululemon, large petrochemical companies, and some of the world’s largest auto manufacturers.
Why are all of these companies so excited and invested in this success? Well, one of the big reasons is the technology of bio-manufacturing that we have developed is fundamentally reinventing how polymers and materials are made for everyday goods that these large companies produce, all the way to hygiene products. We have the potential to touch a lot of these different types of industries.
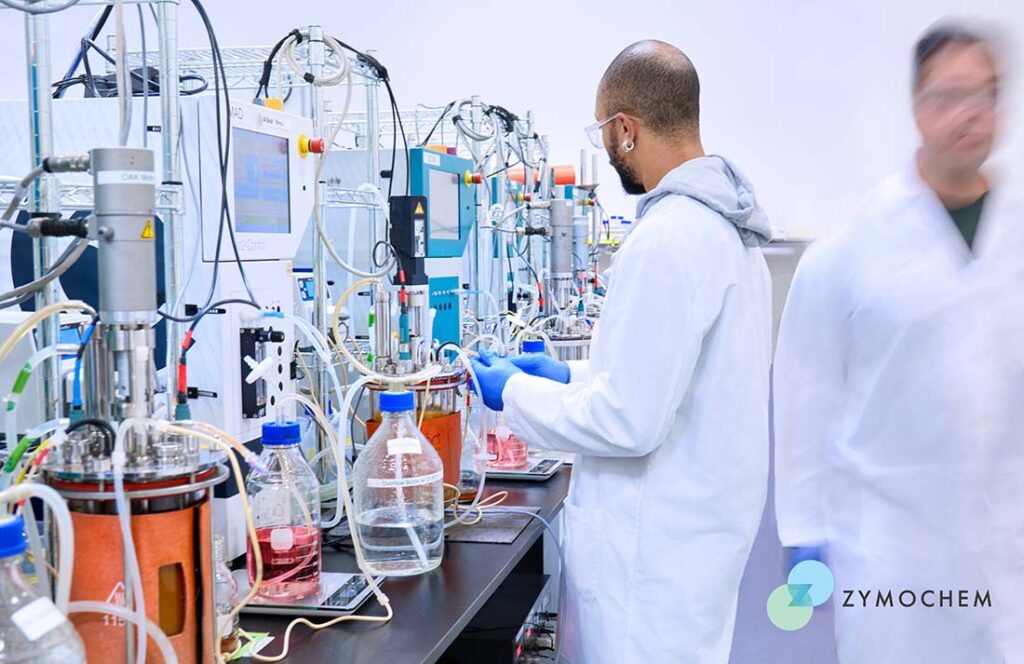
IFJ: What was the inspiration behind the research for BAYSE™?
Chokhawala: Please indulge me on a personal back story of how we came here. In 2019, my wife became pregnant with twins, a boy and a girl. I started reading a lot about how the development of a baby in the womb. One of the things that sort of blew my mind was how micro-plastics could pass through the human placenta into the baby. As a scientist with a PhD, I know it takes a special amount of work to design drugs that do that, and micro plastics just went in and out.
This was the real genesis of this idea. We recognized that the products around us, how they are made, how they persist, all have an impact on our health. We knew with our experience in biochemistry that we could develop a better way.
As a company, we recognized that sustainability was a key pillar to our product design, and so that focus went to the end of life of the product. When you design plastics, they need to have end of life that is in tune with the life of what is used for.
With twins, as you can imagine, we had a mountain of trash coming out of my home. Being a materials company focused on everyday growth using sustainability, I could visually see how this was contributing to the larger problem. As we started digging deeper into this industry, we realized you could literally have a diaper designed to be fully circular in natural, made with bio-based ingredients, except for one thing: the SAP. And that also happens to be the primary component responsible for the performance.
This was the genesis of sorts, where we identified an opportunity that needs to be solved. Given our company background, the question was: How do you engineer microbes to make chemicals in a more stable way? What is nature’s portfolio of chemicals you can make? We found this really beautiful thing called polyglutamic acid.
IFJ: Explain polyglutamic acid (PGA) and how you discovered it is a drop-in substitute for fossil fuel based SAP?
Chokhawala: There is a Japanese delicacy called natto which is fermented beans. When eaten, it’s very stringy. And that’s PGA formed by bacterial fermentation.
Structurally, it is a polymer which has very similar characteristics of the polyacrylic acid that is used today to manufacture SAPs. We endeavored to design something based on this polymer that would be super absorbent.
Now, it took us four years to go from concept to a product that matches toe-to-toe with the fossil-based SAPs and to build our IP protection. It is a fermentation-based technology, so inherently, it is substantially lower carbon footprint than fossil-based manufacturing, and you can design materials that have much better end of life properties versus what is available today.
IFJ: What other areas is your company exploring?
Chokhawala: Super absorbents are one target. We also work on other very large materials, like nylons as an example, which also have a huge environmental problem. Nylon production carries with it a tremendous carbon footprint and is used in millions of metric tons globally each year.
Overall, our vision from day one has been, how do we disrupt these very, very large industries which have systemic problems because of the way materials are manufactured or disposed of. The goal is to use breakthrough science to help the world transition to a fossil free future.
We are blazing a new path forward for how products we use every day – from the items we touch, feel, and wear — are sourced, manufactured, consumed, and disposed of.
IFJ: Explain the science behind BAYSE™.
Chokhawala: In some respects, creating BAYSE™ is somewhat straight forward since we use a fermentation process which is like brewing beer. In other respects, it can be quite complex, relying on our team’s years of expertise in biochemistry.
In simple terms, we use a source of sugar to feed our microbes and brew a broth. That material is then purified and, using our proprietary process, cross-linked to provide the qualities – in the case of the SAP, hyper absorbency – that we are seeking.
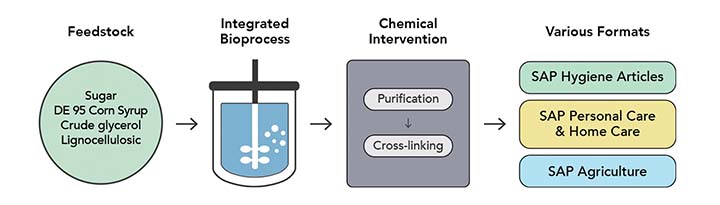
IFJ: How did you prove the ability to deliver BAYSE™ to industrial scale levels? How was it tested?
Chokhawala: Yes, making this material in small quantities in the lab setting is one thing. Translating this to industrial scale is another. We are happy to share a recent announcement that last Fall we were able to deliver the same output we’ve seen in the lab scale in 45,000 L fermentation tanks. That means that we scaled 180,000 times the lab setting and moved from producing hundreds of kilograms of our material to metric tons of it. We are excited to continue this scale up in 2025 and begin satisfying commercial interest, which requires hundreds and thousands of metric tons, beginning in 2026.
IFJ: What are the plans for 2025 and beyond? What new things are you working on?
Chokhawala: 2025 is all about scale. We recognize the immense pent-up demand that exists in the hygiene industry for a technology like BAYSE™ that checks all the boxes and that is what we are excited to deliver. We are prioritizing our available material with those wanting to invest in our mutual success and be a first mover in this space. We continue to hear from stakeholders in non-hygiene categories of how this technology can impact their industries so prioritization of interest and intent will be key.
Beyond the products themselves, we also were thrilled to share recently that we became both a public benefit corporation and achieved B Corporation certification. These are important achievements for our organization and serve as a great message to customers that we can build game changing technology and deliver them in a way that has a positive impact on society and the environment.
In a nutshell, 2025 is about building for scale and impact.
Learn more at www.zymochem.com.