Fostering Sector-wide Collaboration to Transform Waste into Resources
The urgent need for sustainable waste management solutions in the hygiene industry is underscored by the staggering annual disposal of over 4.1 million tons of diapers in U.S. landfills alone, comprising a significant percentage of the planet’s municipal waste.
Nexus has extensive experience in recycling various streams of scrap plastic from hygiene product manufacturers. This upstream knowledge provides insights into how recyclers and the hygiene industry can work together to increase the recyclability of plastic waste. It is essential to take steps now to ensure diaper and other hygiene product matrices are inherently recyclable, laying the foundation for future innovations to address post-consumer hygiene waste. By fostering collaboration across the sector, Nexus and other advanced recyclers aim to guide the industry towards a sustainable future, transforming hygiene waste into valuable resources through advanced recycling processes.
Diaper Composition and Recycling Challenges
Diapers are complex products, typically composed of three main materials: plastics, cellulose, and superabsorbent polymers (SAP). Globally, a few companies, including North America’s Recyc PHP Inc., have the capability to effectively process rejected pre-consumer diapers and separate these components. Daniel Fortin, CEO of the company, states that his company has well-established recycling markets for both cellulose and SAP. However, reclaimed plastic, which comprise 25-40% of a diaper’s total weight, poses significant recycling challenges. These challenges stem from their mixed nature – often a blend of polyethylene (PE) and polypropylene (PP) – and from their form as flexibles and films. Traditional mechanical recycling methods struggle with these materials, as they are well-suited for rigid feedstocks composed of mono-materials.
The burgeoning advanced recycling industry presents an alternative pathway for reclaimed and scrap plastic materials from hygiene products. The plastics-to-plastics enabling technology developed by Nexus Circular, and similar advanced recycling processes, effectively transform those reclaimed plastic materials into a valuable resource for new plastics.
Revolutionizing Recycling
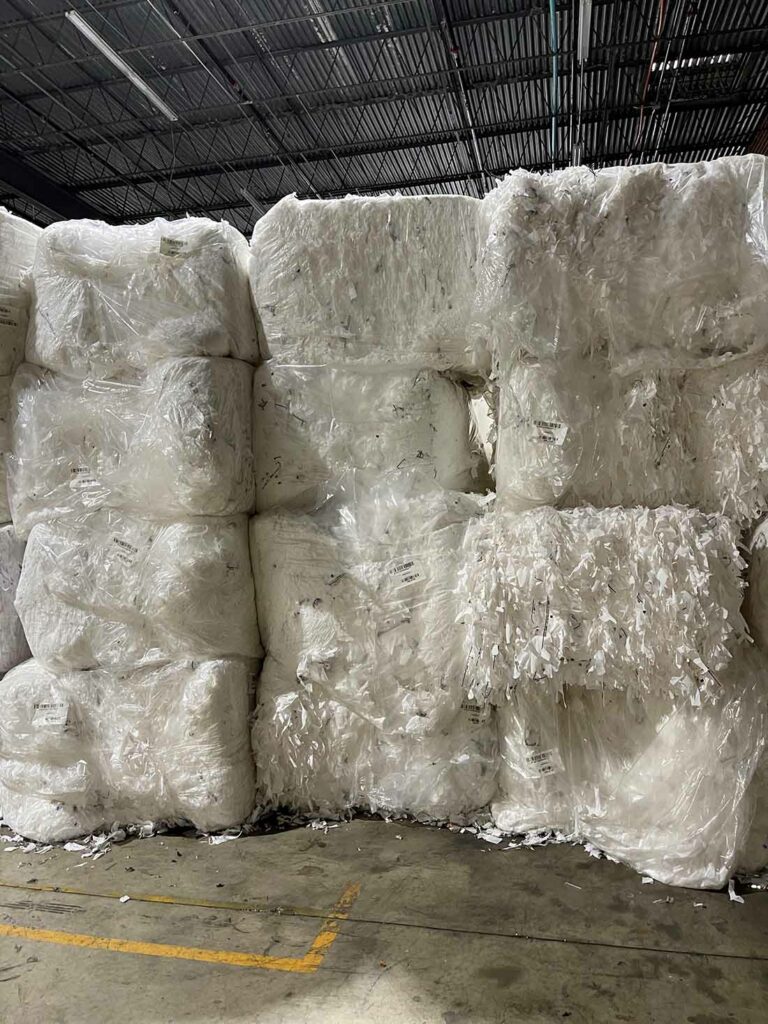
Founded in 2008, Nexus Circular has developed a pioneering advanced recycling process aimed at addressing the limitations of traditional recycling. The company employs thermal depolymerization – a conversion technology that applies heat in an oxygen-free environment at atmospheric pressure, ensuring no combustion or incineration occurs. The process transforms polyolefins back into their original molecular building blocks at a very high yield. The resulting circular feedstock is revolutionary, serving as direct substitute for fossil-based resources in the production of new, virgin-quality plastics.
Nexus has been operating at commercial scale since 2018 and is one of a handful of commercial advanced recycling companies in North America, including Eastman, Purecycle, and ExxonMobil. Nexus is aligned and partnered with global polyolefin resin producers including Braskem, Chevron-Phillips Chemical Company, LyondellBasell, and Shell, supporting their plastic circularity commitments. Nexus’s circular feedstock allows those companies to produce virgin-grade plastics that meet stringent quality standards.
Each tanker or rail car of circular feedstock can directly displace an equivalent volume of fossil-based feedstocks, offering a significant opportunity to reduce reliance on non-renewable resources and decouple plastic manufacturing from extraction.
Feedstock Suitability for Advanced Recycling
Advanced recycling technologies are designed to handle a broader range of used plastics and more challenging formats than traditional recycling processes. Examples from the absorbent hygiene product (AHP) value chain include rejected bicomponent nonwoven materials from converters and product trimmings from diaper and feminine care manufacturers.
Nexus also partners with innovative companies like diaper reclaimer Recyc PHP, Inc. (Montreal, Canada) to ensure that complex diaper materials are recycled. A key study by Nexus and Recyc PHP, presented at Hygienix 2023, showcased the suitability of reclaimed plastics from various rejected diaper brands and products. The results are presented in Table 1.
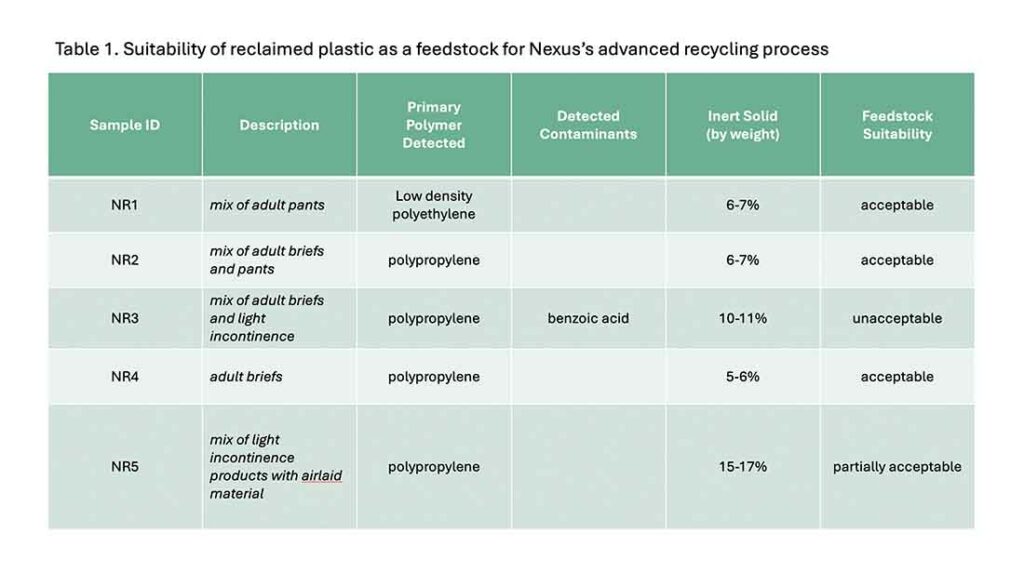
The results were compelling: Four of five samples had acceptable polymer compositions for Nexus’ recycling process, including polypropylene (PP) and polyethylene (PE). However, the presence of airlaid materials in one sample (NR5) illustrated the challenges posed by such materials, which complicate the separation process for diaper reclaimers and reduce the yield of circular feedstock for plastic recyclers. Reclaimed plastics from formulations that contain airlaid material must be controlled and metered in carefully to minimize yield, operational, and financial impacts to the recycler.
Sample NR3 revealed the presence of benzoic acid, a depolymerization product of polyethylene terephthalate (PET), indicating the use of polyester in that specific diaper product. Deeper analysis and characterization revealed that PET was used in the top sheet, whereas the other four diapers utilized a polyolefin-based top sheet.
The study underscores the complexity of diapers and the challenges that mixed polymer systems pose for reclaimers and recyclers. Diapers utilizing single polymers or combinations of PE and PP polyolefins significantly improve the matrix’s recyclability. This highlights the importance for manufacturers to consider recyclability in the design phase, aiming to use plastics from the same polymer family to enable compatibility with recycling technologies.
Why Discrete Plastic Families Are Desired
Designing end products with plastics from discrete plastic families is crucial for recycling due to the inherent chemical differences between these families. This is particularly true for the major plastic families in hygiene products – polyesters and polyolefins. Polyesters, such as PET, require different processing conditions due to their higher melting points. Additionally, PET tends to degrade into undesirable by-products under conditions suitable for the advanced recycling of polyolefins. This degradation not only diminishes the quality and yield of the recycled material, but also increases maintenance and operational costs due to the by-products that can damage recycling equipment.
This same concept extends to materials that intertwine non-wovens with cotton as well as PLA and other non-polyolefin bioplastics. When non-polyolefin plastic materials are included in the diaper matrix, the value of the resulting reclaimed plastic is greatly reduced.
While advanced recycling technologies can process polyester (through methanolysis) and polyolefins (through pyrolysis) separately, producing high-quality circular feedstocks, they struggle with efficiently processing mixtures of polyester and polyolefin materials. This critical distinction underlines that mixing these materials can severely restrict recycling options. Therefore, it is vital for manufacturers to consider these recycling implications when designing hygiene products.
Integrating Sustainability into Design
Hygiene product manufacturers are continually innovating to meet consumer demands for comfort, performance, convenience, and affordability. Concurrently, there is a growing imperative to address environmental sustainability, driven by stringent government regulations and evolving consumer expectations. Many companies have responded by dedicating entire teams to minimize waste generation,
ensure effective landfill diversion, and achieve significant reductions in Scope 1, 2, and 3 emissions.
The aspects of design and sustainability are intertwined, as the selection of materials during the design phase directly impacts the recyclability of the final product. If sustainability considerations are not integrated with cost and consumer expectations during design, formulators may inadvertently select materials from different polymer families, complicating or even precluding recycling opportunities.
This issue was highlighted in the study presented at the 2023 Hygienix conference, demonstrating that plastics reclaimed from diapers containing both polyester and polyolefin components are unsuitable for commercial advanced recycling processes. Although the differences when incorporating polyester are subtle and often indistinguishable to consumers, they result in a plastic matrix that lacks a viable recycling pathway.
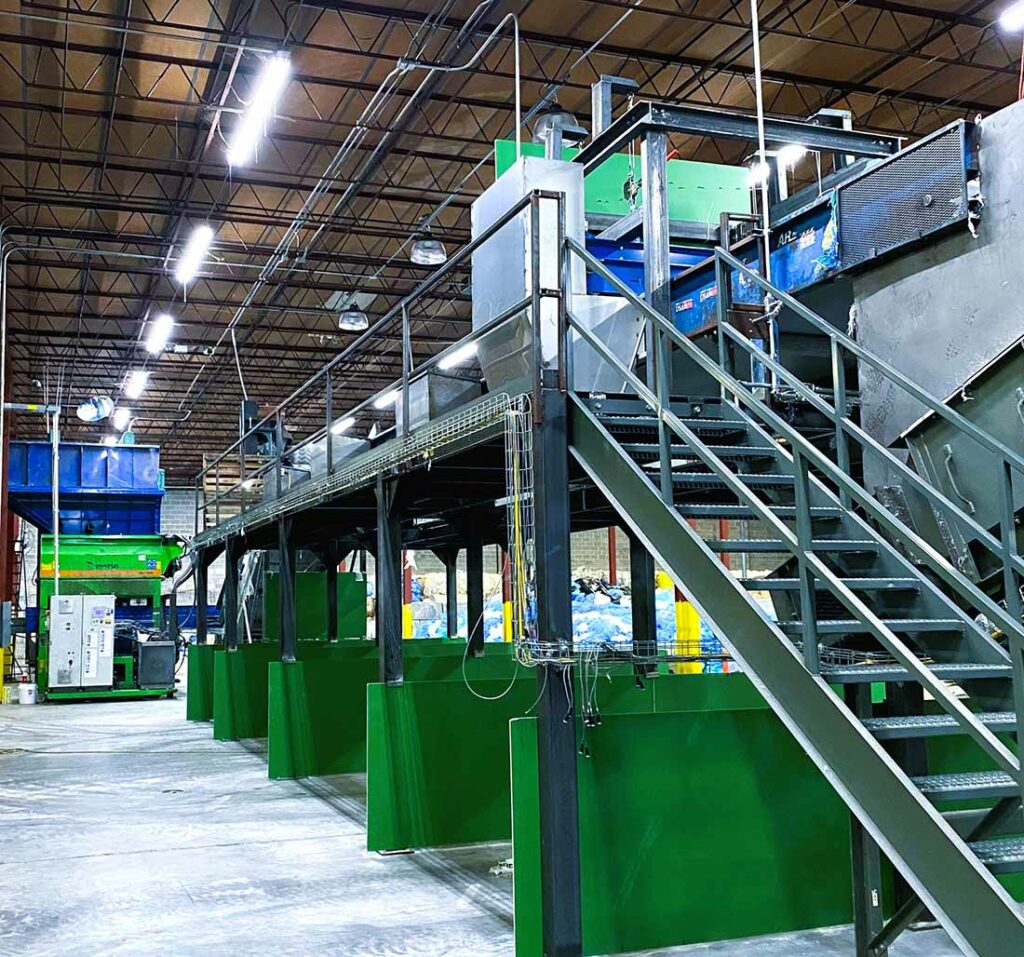
Encouragingly, many reclaimed plastic streams from diapers have already proven to be excellent feedstocks for advanced recycling, indicating that many products are already designed with solely polyolefin materials. Despite this progress, polyester-based plastics are still used in diaper components such as the top sheet and acquisition distribution layer (ADL), as indicated on ingredient lists of major brands.
Addressing these challenges requires a paradigm shift towards designing products using single polymer family systems. This shift is critical not only in the hygiene sector but across all industries reliant on polymer-based products. By standardizing materials, especially in the initial design phase, manufacturers can gain immediate benefits in waste diversion and carbon footprint reduction.
This strategic shift also lays the groundwork for long-term benefits from future recycling innovations. The recycling of post-consumer diapers will require consumer support alongside substantial infrastructural and engineering investments. A robust and dependable recycling market for all reclaimed materials is essential to justify these investments. A collaborative effort between producers and recyclers is crucial to establish a sustainable framework that supports the long-term viability of recycling initiatives for complex post-consumer plastic feedstocks and material circularity.
Enabling Circularity
The EPA defines a circular economy as “an economy that uses a systems-focused approach and involves industrial processes and economic activities that are restorative or regenerative by design, enable resources used in such processes and activities to maintain their highest value for as long as possible, and aim for the elimination of waste through the superior design of materials, products, and systems (including business models).”
A key advantage of advanced recycling is its ability to return plastics to the value chain at their highest value – as virgin-grade plastic. Nexus actively works within the hygiene industry to convert waste from the manufacture and distribution of hygiene products into circular feedstocks through its plastic-to-plastic recycling process.
An essential aspect of circular recycling is a transparent and verifiable system that tracks the journey of recyclable materials within the supply chain, enhancing accountability and sustainability. Nexus holds the International Sustainability and Carbon Certification (ISCC+) certification, indicating that its supply chain uses materials that are fully traceable and sustainably sourced. Since its initial certification in 2020, Nexus has been recertified annually, reflecting its ongoing commitment to sustainability.
These ISCC+ certified liquid feedstocks from advanced recycling set the foundation for resins that meet strict specifications and purity standards, essential for food-contact and hygiene products. Such resins represent a transformative development for industries that traditionally struggle to use recycled materials due to stringent purity and regulatory requirements. Advanced recyclers are creating a mechanism for plastic waste to return to the value chain at its highest potential value, making true circularity a tangible reality for the hygiene sector.
Reduction of GHG Emissions
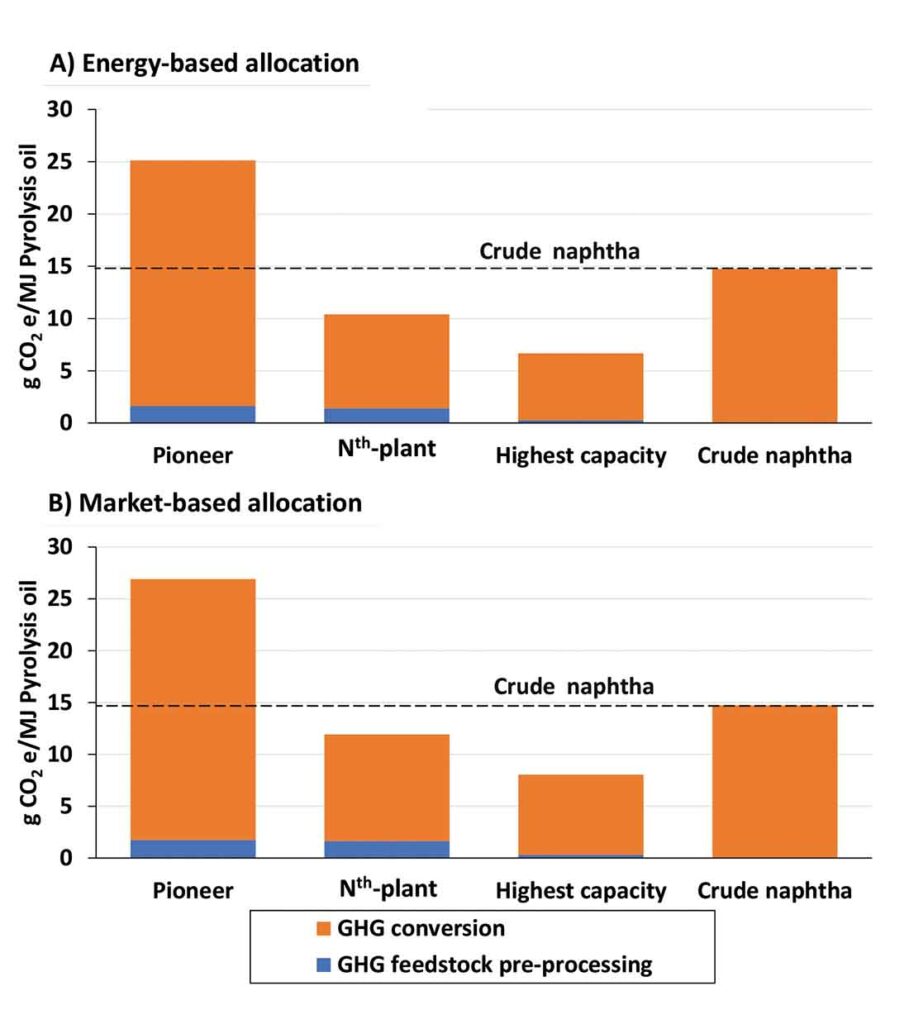
Chart courtesy of Argonne National Laboratory Life-cycle Analysis of Conversion of Post-Use Plastic via Pyrolysis with the GREET Model
In considering the role of the circular economy in enhancing resource efficiency, addressing the environmental impacts of circular systems and materials, especially in terms of reducing greenhouse gas emissions (GHGs), is crucial. Advanced recycling technologies support both recycling and landfill diversion and play a key role in mitigating climate change via their potential to reduce GHG emissions. This aligns with the global initiatives by plastic converters and absorbent hygiene product (AHP) manufacturers to lower their carbon footprints.
The Argonne National Laboratory, part of the U.S. Department of Energy, recently completed a comprehensive Life Cycle Analysis for pyrolysis-based advanced recycling. The Argonne study confirms that, at commercial scale, pyrolysis can reduce GHGs by 35% compared to fossil-based resources.
The analysis accounts only for Scope 1 emissions, which are directly emitted by sources under company control. It does not account for additional potential benefits such as reducing fossil fuel reliance, enhancing landfill diversion, and avoiding the environmental and energy impacts of incineration.
With its capacity to enable landfill diversion and reduce GHG emissions, advanced recycling technologies like those developed by Nexus are ideally positioned to partner with the hygiene industry in its transition towards circularity.
The Path Forward
Nexus Circular and its peers in the advanced recycling industry are pioneering a path forward in the recycling of polyolefin flexible materials, offering a viable solution to help address a global waste challenge. Nexus’s technology is complemented by a suite of other advanced recycling technologies and innovative companies that are scaling rapidly to offer solutions for challenging plastic waste streams across polymer families and industries. These companies offer an opportunity to divert waste from landfills and incineration while simultaneously reducing GHG emissions.
Partnerships between hygiene companies and advanced recyclers are essential to support the transition towards a circular economy and set a new standard for sustainability in the hygiene industry. It is imperative that manufacturers, consumers, and recyclers collaborate to foster designs that prioritize both functionality and recyclability. By acting now to design recyclable hygiene product matrixes, the industry sets a foundation for future recycling innovations. Our collective commitment to these design principles will ensure that environmental benefits and circularity are realized alongside consumer satisfaction.
References:
Norihiro Itsubo, et al. “Life Cycle Assessment of the Closed-Loop Recycling of Used Disposable Diapers.” Resources 2020 9 (34). DOI: 10.3390/resources9030034.
U.S. Environmental Protection Agency. “Facts and Figures about Materials, Waste and Recycling: Nondurable Goods: Product-Specific Data.” https://www.epa.gov/facts-and-figures-about-materials-waste-and-recycling/nondurable-goods-product-specific-data#DisposableDiapers (Accessed April 11, 2024).
Joan Manuel F. Mendoza, et al. “Improving Resource Efficiency and Environmental Impacts through Novel Design and Manufacturing of Disposable Baby Diapers.” Journal of Cleaner Production 2019 (210), 916-928. DOI: 10.1016/j.jclepro.2018.11.046.
Ulises R. Gracida-Alvarez, et al. “Life-cycle analysis of recycling of post-use plastic to plastic via pyrolysis.” Journal of Cleaner Production, Volume 425 (2023). DOI: 10.1016/j.jclepro.2023.138867.
U.S. Environmental Protection Agency. (2021). “National recycling strategy: Part one of a series on building a circular economy for all.” Retrieved from http://www.epa.gov/recyclingstrategy (Accessed April 12, 2024).