When Longevity is a Necessity for Nonwovens
Durability is critical to the high performance of many nonwovens, and two of the most extremely demanding uses they are put to where a long life must be guaranteed is firstly as the filter media employed in industrial baghouses, and secondly, as geotextiles which are widely used in civil engineering projects.
King Coal
Despite the rapid expansion of renewable energy, surging electricity demand in major economies saw the world’s use of coal increase by 2.6% in 2023 to reach an all-time high, according to the International Energy Agency (IEA). A turning point, however, may now be on the horizon.
In China – which accounts for more than half of all global coal consumption – electricity generation from hydropower has been recovering in 2024 from exceptionally low levels in 2023. This, alongside the continued rapid deployment of solar and wind, is significantly slowing down the growth in coal use in 2024.
Another major annual increase in China’s electricity demand, however, forecast at 6.5% in 2024, makes a decline in the country’s coal consumption unlikely. In the first half 2024, India’s coal consumption also climbed sharply.
Coal demand in Europe meanwhile continues on a downward trend, largely due to emissions reduction efforts in power generation and coal use has also been contracting significantly in the United States in recent years, although stronger electricity demand and less switching from coal to natural gas threaten to slow this trend in 2024.
Boilers
Pulverized coal-fired boilers dominate the electric power industry, providing steam to drive the large turbines. The basic concept is to make use of the entire volume of the furnace for the combustion of solid fuels and as a consequence the coal, often with added biomass and other materials, is ground into fine grain, mixed with air and burned in the flue gas flow.
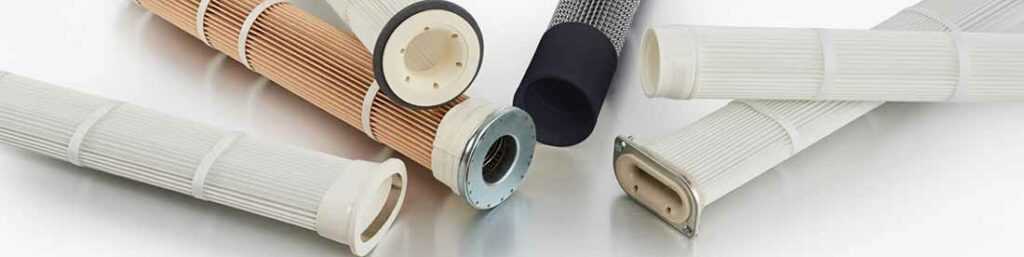
The coal contains mineral matter which is converted to ash during combustion and has to be removed at the furnace bottom in the baghouse, where the engineered durability of high-performance filter media is so critical.
Baghouses are not confined to the energy industry but are also installed in the plants of steel mills, pharmaceutical and chemical producers, food manufacturers and other industrial companies.
They came into widespread use in the late 1970s following the development of high-temperature fibers capable of withstanding temperatures of over 175°C.
These fibers include polyphenylene sulfide (PPS) meta-aramids and even higher performance polyimide (PI) and polytetrafluoroethylene (PTFE).
Efficiency
Baghouses typically have a particulate collection efficiency of 99% or better, even when particle size is very small. Most employ long, cylindrical filter bags that can be up to fourteen feet long and are usually needlepunched nonwovens or woven fabrics, reinforced with scrims. For applications where there is relatively low dust loading and gas temperatures are 170°C or less, pleated nonwoven cartridges can be used instead of bags.
The dust-laden coal gas enters the baghouse through hoppers and is directed into the baghouse where it is drawn through the bags – either on the inside or the outside depending on the cleaning method – and accumulates on the filter media surface until air can no longer move through it.
When sufficient pressure drop occurs, the cleaning process begins. Baghouses are very efficient particulate collectors because the dust cake is formed on the surface of the bags.
Cleaning methods can significantly influence how quickly filters clog and how often they need to be replaced.
In pulse-jet baghouses, where filters are cleaned with short bursts of compressed air, filter bags can last anywhere up to three years, while filters in reverse-air and shaker systems, which use mechanical shaking or reverse air flow, need to be changed less frequently, with intervals ranging from three to five years or even longer.
Substantial Contracts
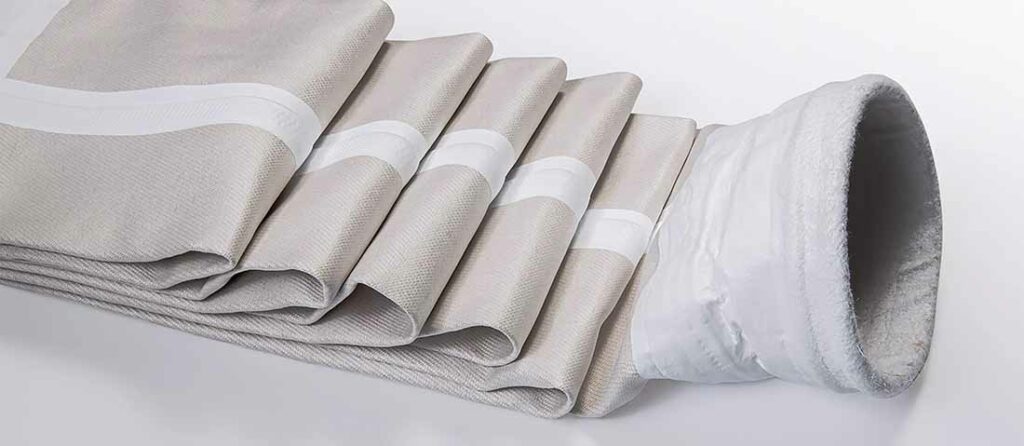
A single contract for a coal plant baghouse can be substantial.
BWF Envirotec, for example, a major supplier of filter media headquartered in Offingen, Germany, lists amongst its references the contract supply of 16,640 of its needlona PTFE glass fiber nonwoven filter bags to a pulverized coal plant in Czech Republic, and a second contract to a similar plant in South Africa for
the supply of no less than 36,960 needlona bags.
Geotextiles
Nonwoven geotextiles are meanwhile essential components in civil engineering projects, serving as a versatile material used for filtration, separation, reinforcement, protection and drainage.
Made primarily from polypropylene (PP) and polyester (PES), they are commonly used in applications such as road construction, embankments, retaining structures, landfills and for erosion control. Understanding the lifetime expectancy of nonwoven geotextiles is crucial for engineers and project managers to ensure the longevity and durability of the structures that need to be supported.
The lifespan of nonwoven geotextiles can vary widely depending on a number of factors including the material composition, and both PP and PES are inherently resistant to ultraviolet (UV) radiation while exhibiting chemical stability and mechanical strength.
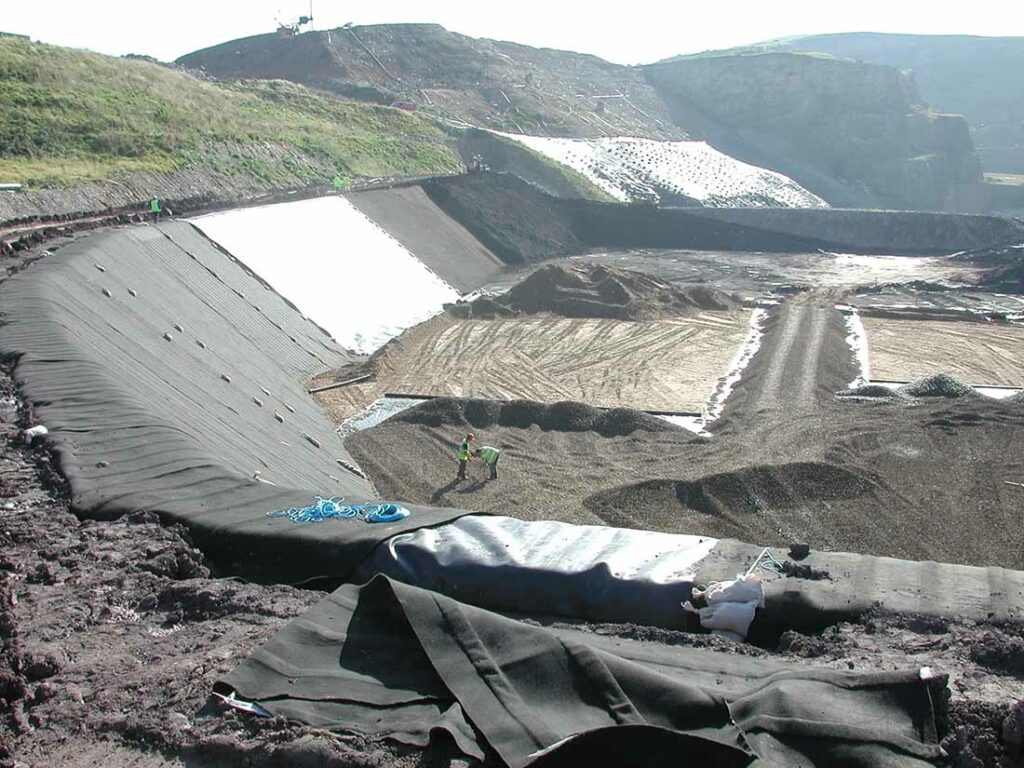
Expectations
Continuous exposure to environmental factors such as UV radiation, temperature fluctuations, chemical exposure and biological activity, however, will still degrade nonwoven geotextiles over time, with UV radiation, for example, causing the fibers to become brittle and lose strength.
The mechanical stresses that geotextiles endure during installation and throughout their service life, including tension, compression and abrasion, can also impact their longevity, as can interaction with the surrounding soil, which may contain aggressive chemicals or microorganisms which can lead to chemical or biological degradation.
In medium-term applications where the geotextile is used for its mechanical properties over a moderate period, such as in road construction projects or certain types of embankments, life expectancy is up to 25 years, but in permanent installations where the geotextile is expected to function for the life of a structure, such as landfill liners, long-term erosion control and certain types of foundation stabilization, the expectancy is for a lifetime of up to 100 years.
All performance tests indicate this to be the case, but since nonwoven geotextiles were only introduced in the 1960s, full proof of this longevity will only be ultimately confirmed from an existing site in the future.
Integrity
Nonwoven polypropylene geotextiles have, however, been excavated from sites after 30 years and shown minimal degradation, indicating that they retain their structural integrity and continued to perform their intended functions effectively. The physical properties, such as tensile strength and puncture resistance, were found to be largely intact, demonstrating long-term durability.
Sources such as the Geosynthetics Handbook, published by the Geosynthetics Materials Association headquartered in Roseville, Minnesota, as well as studies by industry experts have documented similar findings, reinforcing the reliability of nonwoven geotextiles for subgrade stabilization in various environmental conditions. The use of geotextiles has also been shown to significantly extend the lifespan of road structures, reduce maintenance costs and improve overall performance.
Alternative Fibers
The durability of nonwoven geotextiles has recently become something of an issue, however, as manufacturers seek to use more sustainable alternatives to oil-based PP and PES fibers.
Geotextile manufacturer Naue, headquartered in Espelkamp, Germany, reports that it has recently introduced a high-performance range of nonwoven geotextiles called Secutex Green, which are available in a weight range of 300-1,000 gsm and based on biobased PLA (polylactic acid) fibers.
The Secutex Green range was developed in response to demands from specifiers for products that are 100% plastic-free, but at the same time, guarantees of a long performance life of up to 50 years are required.
“The problem we face is that under the current European Union Construction Products Directive, geotextiles based on bioplastics, as well as recycled products, can only receive a durability rating of five years,” explains Chris Quirk, managing director of Naue Geosynthetics UK. “This is as opposed to fabrics based on virgin plastics like polypropylene which have proven durability.
“It means that our new PLA products can only be used in temporary works at present, although we know that PLA has far greater durability than the guarantee we are allowed to give.”
At the same time there is a rise in the application of bans on the use of plastics in construction works, notably in National Parks in Europe, California and New Zealand.
“For some challenging applications, fossil-based plastic will always have to be used and there is good bio-based plastic too, but this is not yet understood by regulators,” Quirk says.
Bentofix Green
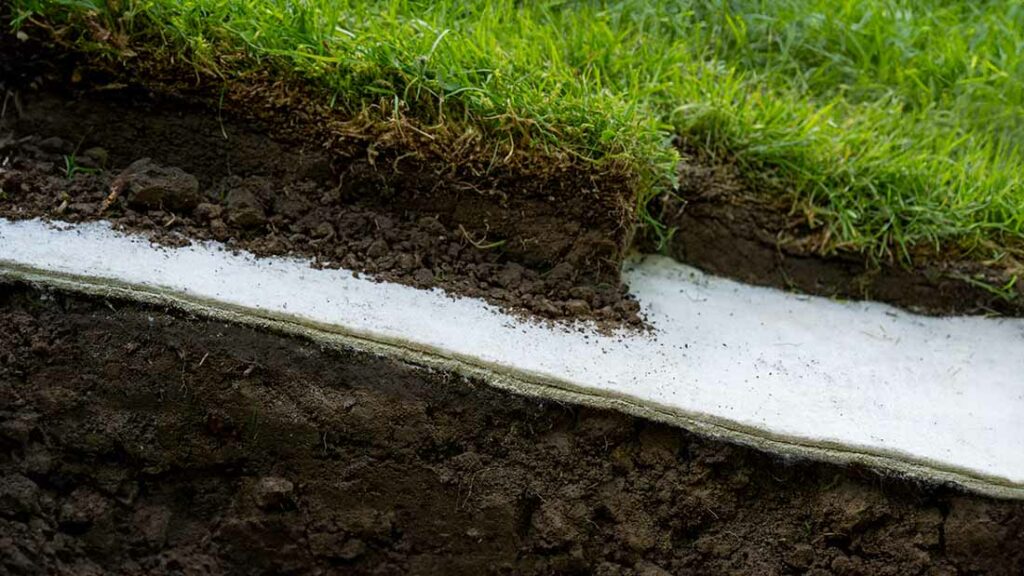
Such frustrations, however, are driving innovation at Naue, and its latest product launch is the patent-pending Bentofix Green, which is designed for sealing operations on ponds, streams, ditches, dams, rivers and banks.
Bentofix Green consists of a geosynthetic clay liner which sandwiches bentonite powder between carrier and cover layers of Secutex Green nonwovens.
Sodium bentonite powder is a highly effective waterproofing mineral and a one centimeter layer of it has a sealing effect of several decimeters.
Once the Bentofix Green has been installed and poured over, the bentonite begins to swell under the influence of moisture and forms a homogeneous sealing layer. Bentonite has the ability to close punctures or dry cracks on its own, so that a lasting sealing effect is achieved.
In effect the nonwoven layers are simply an installation aid, engineered to disappear over time – completely turning the tables on the usual requirement for durability in nonwoven geotextiles.