Training Pants and Retailer Brands Come of Age
As a leading supplier of spunmelt nonwovens to the absorbent hygiene products (AHPs) industry, Fibertex Personal Care, headquartered in Aalborg, Denmark, reports that the market is still being impacted by excess capacity in Asia.
Manufacturers have invested heavily in recent years to ramp up their production capacities in the Asian region to support the continuing growth in the AHPs market, but this is currently resulting in a very competitive environment, with an imbalance between supply and demand and resulting pressure on selling prices.
Fibertex Personal Care expects this situation to continue throughout 2024 and has yet to commence operations on its new production line in Malaysia. It is also strengthening its reliability of supply to customers by establishing local warehouse facilities. The first of these, located in Vietnam, has already been established and more are expected to follow.
The excess production capacity in Asia will remain a challenge for some time, the company believes, but the market is still expected to see underlying growth which will absorb the idle capacity over time.
Europe’s Bright Spot
A bright spot in Europe meanwhile, is the growth of the training pants market – products aimed at assisting toddlers to transition from diapers to regular underwear and, like adult incontinence (AI) products, requiring significantly more nonwovens in their construction than diapers.
According to Nielsen data for the 12-month period ending April 2023, training pants are the only volume-growing segment in Europe, with a notable growth rate of 13%, which is largely being driven by retail brands. Euromonitor further predicts that training pants will continue to grow over the next five years with the acceptance of pants among parents a key factor.
The situation is pretty similar in North America too, where capacities are generally not currently as tight, and new investments for both spunmelt nonwovens and AHPs have recently been announced.
Printing Growth
Thanks mainly to capacity investments already made in the North American market, Fibertex Personal Care has been able to expand its print operations for AHPs to include printing on laminated materials and on both breathable and non-breathables. Print operations have grown into an increasingly important part of overall business for the company in recent years.
New small digital printers now installed in both Germany and the USA will enable new value-creating services for customers, including small volume production for testing and digital approval of print designs. These are now part of the service package offered under the company’s Innowo Print brand.
In a further innovation, during 2023, Fibertex Personal Care launched a nonwoven material weighing just 5gsm, with the lightest nonwoven materials in diapers today typically weighing 8-10gsm. The lower weight product promises to significantly reduce raw material consumption, transport volumes and CO2 emissions in the value chain.
New USA Lines
First Quality Enterprises, a long-established producer of AHPs headquartered in Great Neck, New York, has also listed new training pant lines as a priority for its new U.S. manufacturing plant. The plant, at an as-yet unidentified location, will additionally house new baby diaper lines, along with a state-of-the-art automated warehouse facility. It will increase the company’s capacity for both diapers and training pants by 50% and is expected to be completed by June of 2025. First Quality currently has manufacturing sites in McElhattan, Philadelphia, Macon, Georgia, and Drummondville, Quebec.
Ingeo PLA
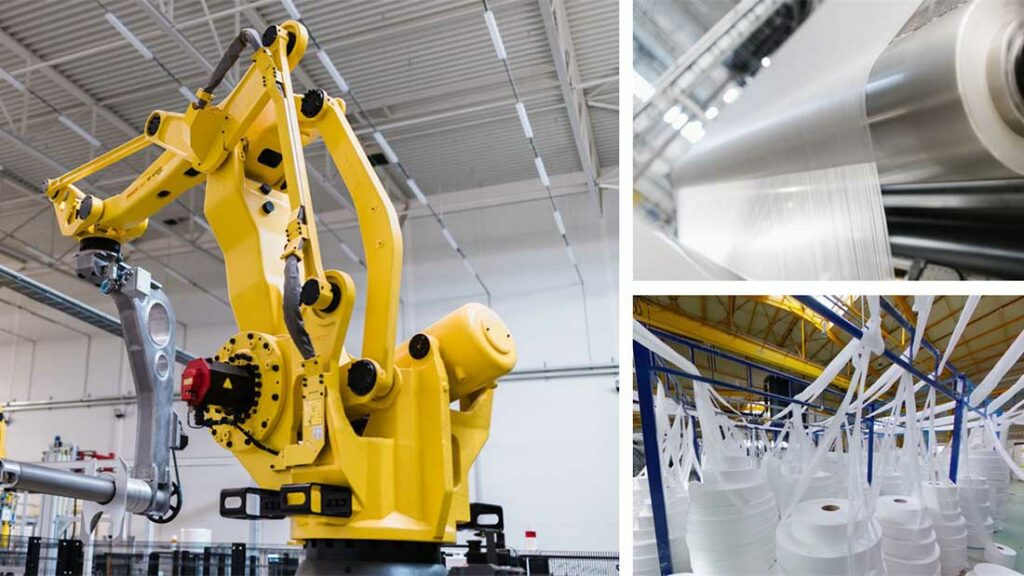
PFNonwovens, another nonwovens supplier to the AHPs market formed in 2018 when R2G, of Prague, Czech Republic, purchased First Quality Nonwovens and combined with Pegas Nonwovens, is actively pursuing use of sustainable feedstocks. A recent emphasis for PFN, which like R2G is headquartered in Prague, has been on the development of sustainable resins for spunmelt nonwovens production on the latest Reifenhäuser Reicofil 5 technology. This includes new materials made entirely from NatureWorks Ingeo polylactic acid (PLA) as a more sustainable alternative to polypropylene (PP) or polyethylene (PE).
“Developing 100% PLA spunmelt nonwovens that meet the industry expectations posed substantial challenges,” explains Simon Frisk, global R&D director at PFN. “PLA differs greatly from the usual synthetic resins in both processing and properties. Overcoming these obstacles required intensive in-house and collaborative development work. The Reicofil 5 technology played a pivotal role, ensuring top-notch quality, consistency and performance in the final products.”
Bornewables
Bornewables, developed by Borealis, headquartered in Vienna, Austria, are a second product being incorporated into nonwovens for AHPs by PFN.
Bornewables can be used as direct drop-in replacements for comparable fossil-based polyolefins and in PFN’s nonwoven production require no changes to the existing manufacturing process while delivering the same high quality and performance as non-renewable virgin materials.
The Bornewables PP being used by PFN is made with second-generation raw material feedstock derived entirely from waste and residue vegetable oil streams. The renewable content in all Bornewables products is mass balance accredited under the ISCC (International Sustainability and Carbon Certification) PLUS certification standard, confirming authenticity and fully transparent traceability from the raw materials to the finished products.
Mass balancing makes it possible for customers to meet ambitious sustainability targets and stay on top of changing legislation. For every ton of certified Bornewables PP used in production, a maximum equivalent amount of nonwoven material can be certified as renewable.
“Anticipating the growing demand for more sustainable nonwoven solutions, we have focused our development resources over the past few years on the circular sphere,” says Tonny De Beer, chief product, technology and sustainability officer at PFN. “Using the Borealis Bornewables instead of standard fossil-based resins will significantly reduce our carbon footprint, even enabling products with a carbon footprint below zero.”
Private Label
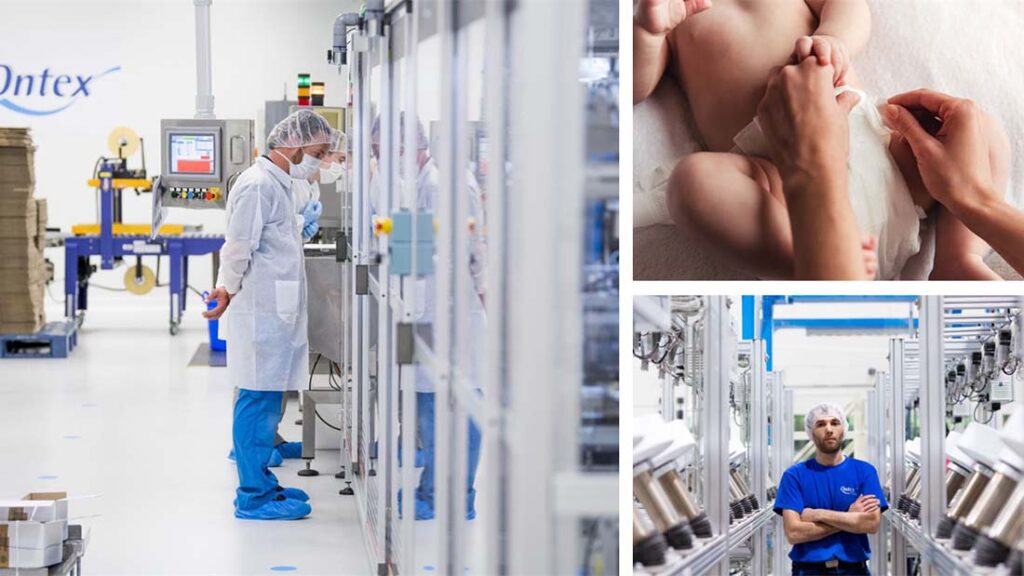
Further innovations for training pants, in addition to AI products, have been incorporated into the private label retail products of Aalst, Belgium-headquartered Ontex. The design of training pants, the company observes, has now evolved to provide a true alternative to traditional open diapers rather than for transitional use.
In a latest evolution, Ontex is introducing the Dreamshield back pocket to upgrade leakage protection and enable extended use, including during the night. Dreamshield consists of two layers – a soft-to-the skin outer layer and a robust and secure absorbent containment layer.
The market for AI disposable pants is also growing. “We know that many people have moderate incontinence and lead active lives, so we make sure our pants are affordable, discreet and easy to wear,” says Annick De Poorter, chief innovation and sustainability officer at Ontex. “We estimate that one in four women over the age of forty and one in nine men over sixty have some form of incontinence, so adult incontinence pants can enable many people to live a normal life.”
The new Ontex X-Core is channeled to provide instant absorption in adult pants and keep humidity away from the skin in a discrete pant that is said to feel closer to regular underwear than ever before. The channel’s unique X-Shape allows for extra distribution at the back of the adult pants and further prevents leakage. Product lab testing has shown a substantial improvement in absorption speed and instant dryness.
North Carolina Expansion
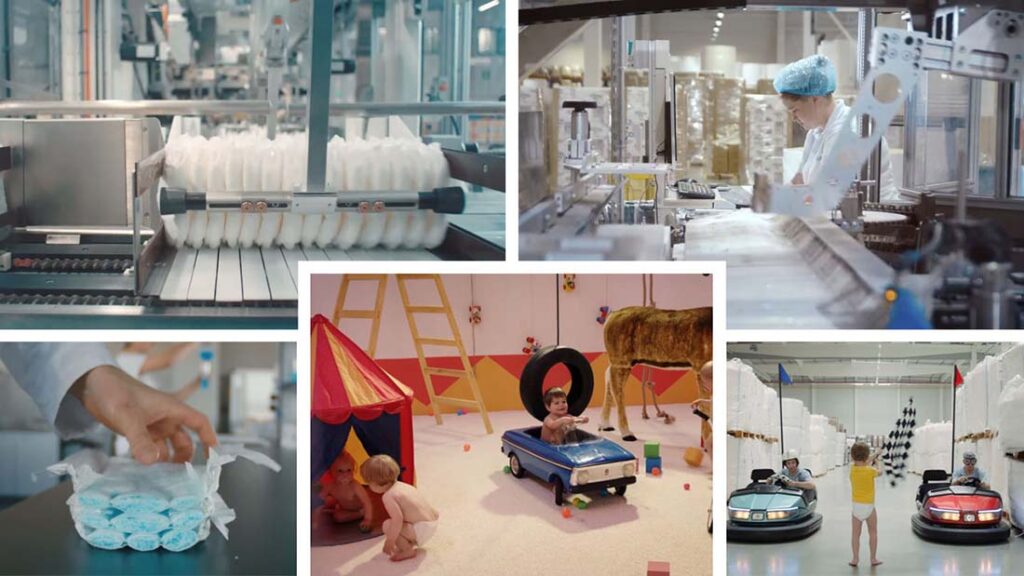
Another major supplier of private label AHPs also headquartered in Belgium (in the municipality of Zele) is Drylock Technologies, which has just announced the expansion of its baby care product manufacturing capacity with a new plant in Reidsville, North Carolina.
With an incontinence product plant established seven years ago in Eau Claire, Wisconsin, Drylock purchased Presto which had been making incontinence products for possibly decades. Drylock is making a further multi-million dollar investment in the USA to meet the increasing demand for baby care products from North American customers.
“People have often asked me when I would be establishing a baby products plant in the USA and I’m very happy to say that the time is now,” says CEO, Bart Van Malderen. “With a localized manufacturing presence, we can support faster product development for our US customers and empower them with unparalleled speed to market.
“The move is part of our strategy to follow our customers – it is answering the increasing demand for baby care products among our valued North American customers and serves as the perfect addition to our plant in Wisconsin, which has served as the bedrock of our incontinence products business in the USA for seven years.”
Drylock, which achieved record sales of more than €1.2 billion in 2023, reports that the private label sector of the market, and particularly retailer own brands, has seen significant growth in recent years, driven by enhanced product quality and range extensions, optimized positioning and high innovation levels, in addition to bringing more sustainable solutions, all designed to compete directly with the national brands.
The new facility will create significant employment opportunities for the Reidsville region, with some 300 direct positions and a significant number of indirect jobs to be created in the local area.