The fiber intermediates market continues to grow with rising demand for textiles, automotive and packaging materials, but is increasingly being driven by sustainability concerns and environmental regulations. Fiber intermediates are the raw materials used in the production of synthetic fibers, principally polyester, polyamide, acrylic and polypropylene, as well as plastics, disinfectants and other industrial products.
Fiber intermediates include purified terephthalic acid, polyethylene, ethylene glycols (monoethylene glycol, diethylene glycol and triethylene glycol), ethylene oxide (ethoxylates, glycol ether and others), acrylonitrile, cyclohexanone, paraxylene, adipic acid and caprolactam.
Market Size
A recent report from Worldmetrics.org suggests that the global fiber intermediates market is projected to reach a value of US$61.6 billion by 2026. While Asia-Pacific, especially China, is the dominant region for the production of fiber intermediates with a share of more than 50%, the Middle East and Africa (MEA) region and India are forecast to be the fastest growing regions over the next few years.
The fiber intermediates market is expected to witness significant growth over the next few years owing to the rising demand for textiles and packaging materials, as well as growth in the automotive sector with greater use of lightweight materials.
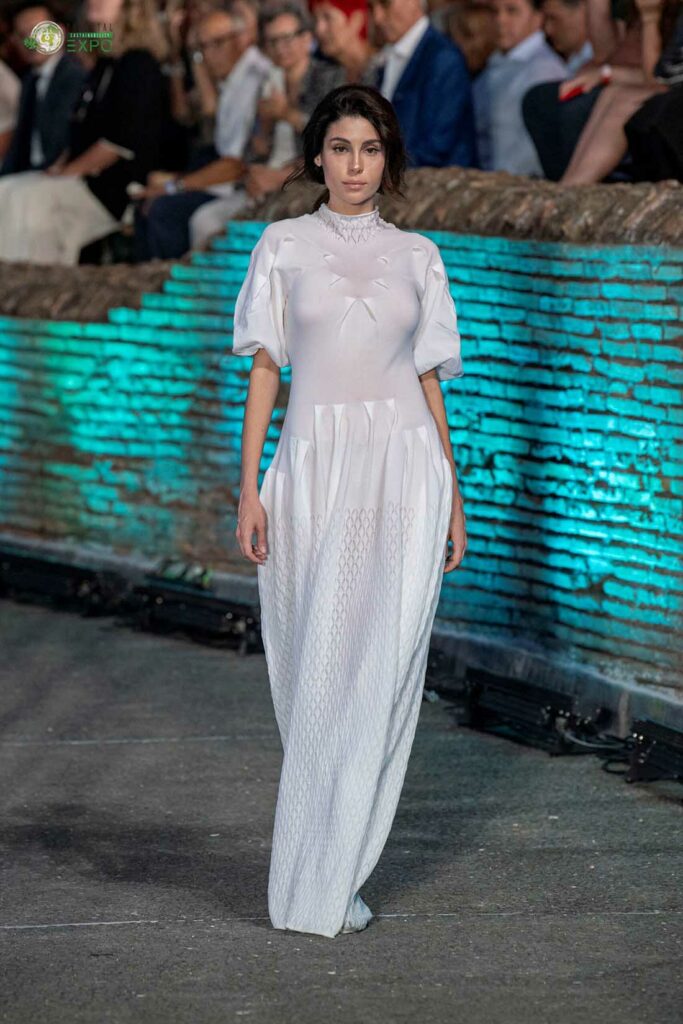
PTA: Preferred Raw Material for Polyester
Paraxylene (also known as p-xylene) is an essential chemical in the polyester fiber production process, according to Alfa Chemistry, a global contract research organization headquartered in Holbrook, New York, USA. It is widely used as a feedstock for the manufacture of other industrial chemicals, notably terephthalic acid (TPA), purified terephthalic acid (PTA), and dimethyl terephthalate (DMT).
TPA, PTA and DMT are further used to make polyethylene terephthalate (PET) polyester, which is a polymer commonly used to make polyester fibers and yarns, as well as major application in the packaging and automotive and industries.
PTA is the fastest growing segment of the fiber intermediates market and is expected to grow with a compound annual growth rate of around 10% to 2030, according to IndustryARC. It is the preferred raw material for polyester, which finds application in a wide range of products from clothing, furniture and upholstery, packaging, films and engineering plastics.
PET is a resin commonly made from the combination of two monomers, PTA and monoethylene glycol (MEG) to form the thermoplastic PET polymer through an esterification reaction. PET consists of 70% (mass percent) PTA and 30% MEG. As well as being a key component in the production of polyester fibers, MEG is also used in the manufacture of PET bottles and other packaging materials.
Increasing Urbanization
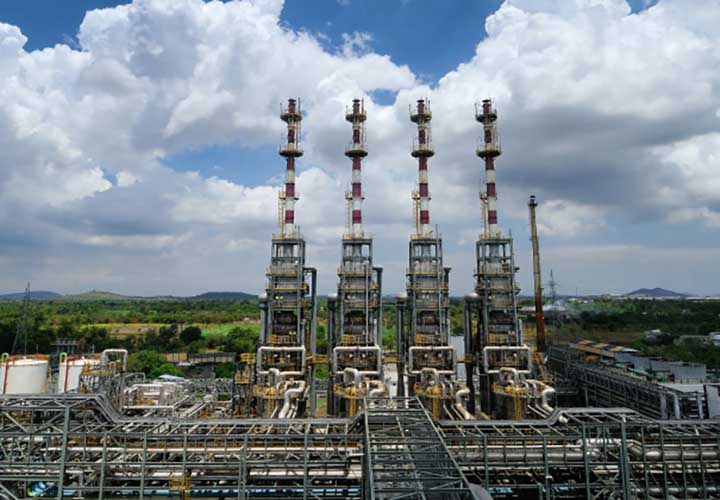
More than half of the world’s total PET production is destined for synthetic fibers, with bottle production accounting for around a third of global demand. (PET is generally referred to as polyester for textile applications, whereas the acronym PET is preferred for packaging.)
With polyester accounting for more than 50% of total global fiber production, the rising population, increasing urbanization and fast-changing fashion trends will continue to drive the consumption of polyester fiber-based clothing and home textiles, where the fiber’s key properties, such as durability, wrinkle resistance and easy care, make polyester fabric a preferred choice among consumers.
In addition, the increasing use of polyester in technical textiles, such as a automotive fabrics, medical textiles and geotextiles, will further increase the demand for fiber intermediates, as will growth in emerging markets, such as India, Southeast Asia and Africa, which are seeing increased urbanization, rising disposable incomes and rapid industrialization.
Acrylonitrile
Acrylonitrile is usually obtained by a catalytic ammoxidation process from ammonia and propylene. It is an important monomer for synthetic fibers, such as acrylic and modacrylic fibers, which are typically used for the manufacture of knitted apparel.
Acrylonitrile can be prepared by radical vinyl polymerization, usually of acrylonitrile monomer and methyl acrylate, to produce polyacrylonitrile (PAN). PAN fiber is also one of the important precursor fibers for the manufacture of polymer carbon fibers.
Major Challenge
The major challenge facing the fiber intermediates industry is instability in the price of crude oil, which is a raw material for various petrochemicals and fiber intermediates.
And as a result of environmental concerns and increasingly stringent government regulations, the fiber intermediates market is seeing a shift toward sustainable and bio-based raw materials, together with the adoption of advanced manufacturing technologies to improve efficiency and reduce environmental impact.
Examples of more sustainable raw materials include the development of bio-based PTA (bioPET), recycled PET (rPET) and bio-based acrylonitrile to cater to the increasing demand for “green” products.
bioPET and bioPTA
In the case of bioPET, the MEG fraction (bioMEG) is produced from renewable plant resources, such as ethanol from sugarcane, rather than fossil resources.
bioPET exhibits identical properties, such as high tensile strength, durability and mechanical stability, to conventional petrochemical PET. Further, it is 100% recyclable although not biodegradable.
While bioMEG has long been available and has become increasingly popular, replacing petroleum-derived PTA with biomass-derived PTA has been a challenge. Several companies, using different technologies, are working to develop biorefinery operations that will deliver the PTA precursor paraxylene along with other products directly from plant feedstocks.
For example, US-based renewables manufacturer Virent has developed a process to use plant-based paraxylene (bioPX) using sugar from corn that is converted to plant-based terephthalic acid (bioPTA), which Coca-Cola has used to produce a prototype 100% plant-based plastic bottle (excluding the cap and
label).
Supply Chains Established
Meanwhile, Japan’s Marubeni and Idemitsu Kosan, together with Oriental Petrochemical Taiwan (OPTC) have agreed to establish a supply chain for bioPTA produced from biomass naphtha derived from plants, with production of bioPTA planned to begin later this year in Taiwan.
Idemitsu Kosan will produce bioPX from biomass naphtha using the mass balance method. It will then be converted to bioPTA by OPTC, a PTA manufacturer under the Far Eastern New Century Group (a PET manufacturing company in Taiwan). Marubeni will be coordinating the management of the supply chain’s establishment as well as the marketing of the bio-based products.
Japanese companies Mitsubishi, Suntory and Eneos are similarly collaborating on the development of a new, sustainable supply chain for PET bottles that have been derived from biomass using bioPX produced from Neste Re, supplied by Finland-based Neste, which is made from 100% bio-based raw waste and residues, including used cooking oil.
While most of these developments have been aimed at PET bottle production, it is more than likely that spinoffs into the fiber sector are not far away.
Biodegradable Polyester
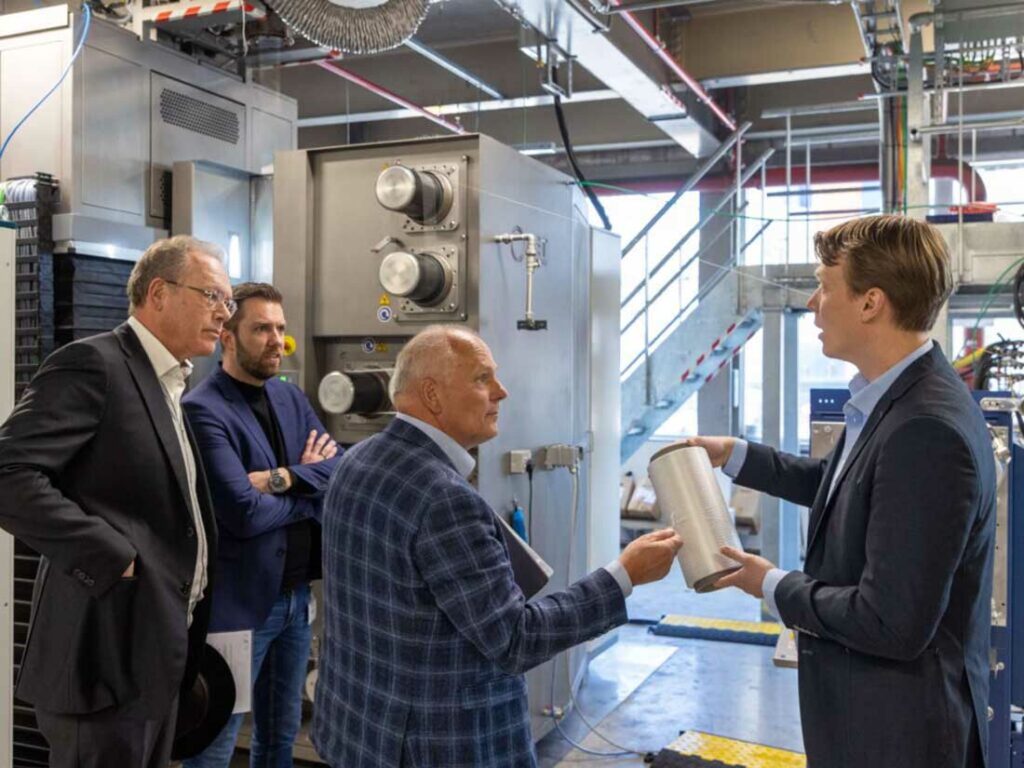
A consortium of Senbis Polymer Innovations and several Dutch universities and research institutes plans to invest €6.6 million in the development of a new biodegradable polyester. Their research projects started in September 2023 and will run for three years. The consortium has already received a €3.3 million grant through the European Just Transition Funds.
In their BIOTT EK project, information is being gathered on what makes certain biopolymers biodegradable but also what makes them melt spinnable and achieve high performance, especially looking at molecular design and physical properties.
This insight will be used to develop new bio-polyesters that will be evaluated both analytically and through application testing via, for example, the melt spinning of fibers. Artificial intelligence is also being utilized to speed up the development and to provide new suggestions for
molecular design.
Sustainable Stretch
Earlier this year, BASF announced that it is to expand production of several of its biomass-based raw materials that are key ingredients in the manufacture of elastane fibers, which are used for a wide range of textiles such as swimsuits, sportswear and underwear, and also outerwear such as shirts and stretch jeans.
The global chemicals giant is to increase the bio-based production of BMBCert (biomass balanced certified) 1,4-butanediol, tetrahydrofuran and polytetrahydrofuran (PolyTHF), all of which are used as raw materials in elastane production, at its flagship plant in Ludwigshafen, Germany, as well as at its facility in Geismar, Louisiana, USA. The BASF plant in Ulsan, South Korea, has also been certified for the production of PolyTHF.
BASF has been supplying biomass balanced tetrahydrofuran (THF BMB) to the Roica division of multinational Japanese company Asahi Kasei to produce its mass balance grade stretch elastane fiber under the Roica brand, which is used for sportswear and other textiles. This is claimed to result in an approximately 25% reduction in carbon dioxide emissions compared with Roica’s existing products.
Bio-based Scrylonitrile
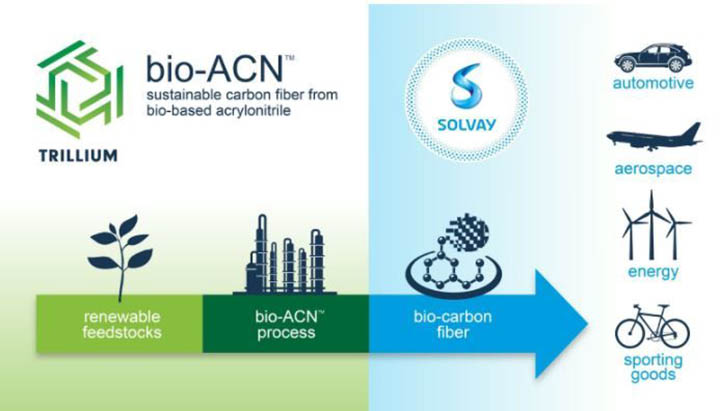
Meanwhile, Ineos Nitriles has recently begun sales of Invireo, a new bio-based acrylonitrile, for the production of carbon fiber, which is used in the aerospace, automotive, healthcare and sporting sectors, and is also essential in the water treatment industry.
Invireo acrylonitrile is produced via a controlled and certified (ISCC+) mass balance route that offers a 90% reduction in carbon footprint compared with conventional acrylonitrile-based products, said Gordon Adams, business director for Ineos Nitriles, the world’s largest producer of acrylonitrile.
Earlier, Solvay and Trillium Renewable Chemicals signed a letter of intent to develop a supply chain for bio-based acrylonitrile for carbon fiber manufacturing. Trillium’s bio-ACN process delivers acrylonitrile from plant-based feedstocks such as glycerol with a lower carbon footprint.