Materiality is rising to the forefront in some of the latest research and development in wearables for healthcare applications. The Wearables Collective symposium co-hosted by the Royal College of Art and UC Davis held in March 2024 highlighted this, looking at the motivations and case studies across North America, Europe and Asia.
A number of drivers to this trend were identified during the symposium and the accompanying exhibition: The first is technological integration that is moving towards greater invisibility. The result here is wearables that look and feel more like regular clothing. A second impetus is coming from user-centered design that addresses how researchers listen to the needs and preferences of users, then the mechanism for bringing the data into design. A third driver is textile designers and makers who are keenly interested in the possibilities of the e-textile structure to deliver in a way that makes the user want to engage. These are all interconnected prompting new forms of cooperation between the different stakeholders.
Dr. Jeanne Tan gave one of the keynote presentations titled “Intuitive surfaces with Artificial Intelligence and Knitted Textiles.” Dr. Tan is COO of the Laboratory of Artificial Intelligence in Design (AiDLab) and Professor of Fashion and Textiles at the Hong Kong Polytechnic University (HKPolyU). In her research, she focuses on the integration of AI and textiles to create interactive materials for an array of applications including wearables and rehabilitation. Her perspective is that of a textile design practitioner, specifically looking at light-emitting e-textiles with AI affording the user a highly intuitive experience. Textiles for her are a natural choice because of their omnipresence in people’s daily lives.
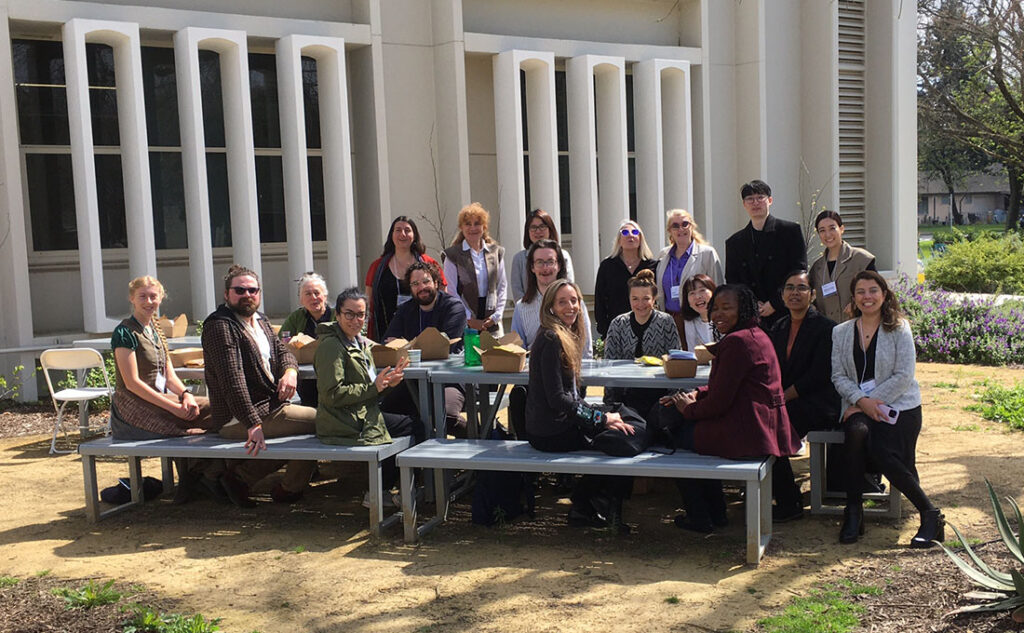
In one project, Tan has developed an intelligent textile system that is based on computer vision with deep learning and illuminating photonic knitted textiles. The light transmission is generated using a Polymeric Optical Fiber (POF), with light travelling through the core of the Poly (methyl methacrylate) (PMMA) fiber that is further enclosed in two sheath layers with the textile treated to allow light to travel from the core through the lateral sides of the fiber to become visible to the eye.
An interactive photonic dress has been equipped with a gyro sensor embedded in the motherboard to detect movement and change color with the motion of the wearer’s body.
An integrated camera has the capability to receive images that are processed by a mini-computer with AI algorithms to provide feedback via different colored illumination. The smart textile can decipher specific imagery as commands, it can be produced as a stretched knit and with a range of surface patterns enhancing the comfort and haptic qualities.
A number of different use case investigations have been undertaken. In one, the technology has been adapted to fit the needs of users with gesture-recognition for multi-sensory rehabilitation using co-design between the therapists, users and caregivers. In another, an interactive photonic dress has been equipped with a gyro sensor embedded in the motherboard to detect movement and change color with the motion of the wearer’s body.
Researcher Robert Pettys-Baker presented a paper jointly written with Brad Holshuh both from the University of Minnesota on “Intention vs. Reality: Managing the sensory language of soft robotic skin stretch wearables.” The premise for this is the need to consider haptic experiences more holistically and without making assumptions about the wearer’s experiences. In the design of haptic skin stretch systems the aim is to develop products that produce sensations that are consistent for all users.
This relies on the creation of a device that works with the body to afford the intended perceptual, cognitive and emotional experience of a sensation. Pettys-Baker points out the tendency to prescriptively assign haptic sensations when testing, proposing a better approach that would be to first conceptualize the user’s own subjective experience of the stimuli in their own words.
The researchers are addressing this by creating two iterations of a skin stretch device located on the forearm using Shape Memory Alloy (SMA) actuators with eyelet crimps utilizing a silicone backing layer for displacement of the skin with hook and eye attachments. In one device a hook and loop closure was used, with the second using a stretch fabric and zipper. The first device recorded a more nuanced set of responses with multiple unique touch sensations identified by participants. Primary, secondary and unique descriptors were noted, for example ‘localized squeeze/pinch’ [Primary], followed by ‘tickle’ [Secondary], then ‘cat licking arm’ [Unique Descriptor]. In contrast, the second device received single descriptors for example ‘squeeze/pinch’.
Half of the participants using both devices reported the sensations to be unique and not a readily identifiable touch sensation that they tend to think about. The authors note that “a device might work, might be generally liked, but that does not confirm true efficacy without true consideration of the user.” The outcome is being used to inform the design, materials and the type of closure for the next iteration where the focus will be on a refined design and more detailed perceptive testing of the haptic qualities. At UC-Davis Hafsa Akter presented a research paper written jointly with Gozde Goncu-Berk on
“Cocoon – A Novel Smart Hospital Gown for Toddler Patients.” There are an estimated four million young children (0-4 years) admitted to inpatient care in North America each year, with around 5% of ER visits resulting in hospitalization according to the Agency of Healthcare Research and Quality (AHRQ).
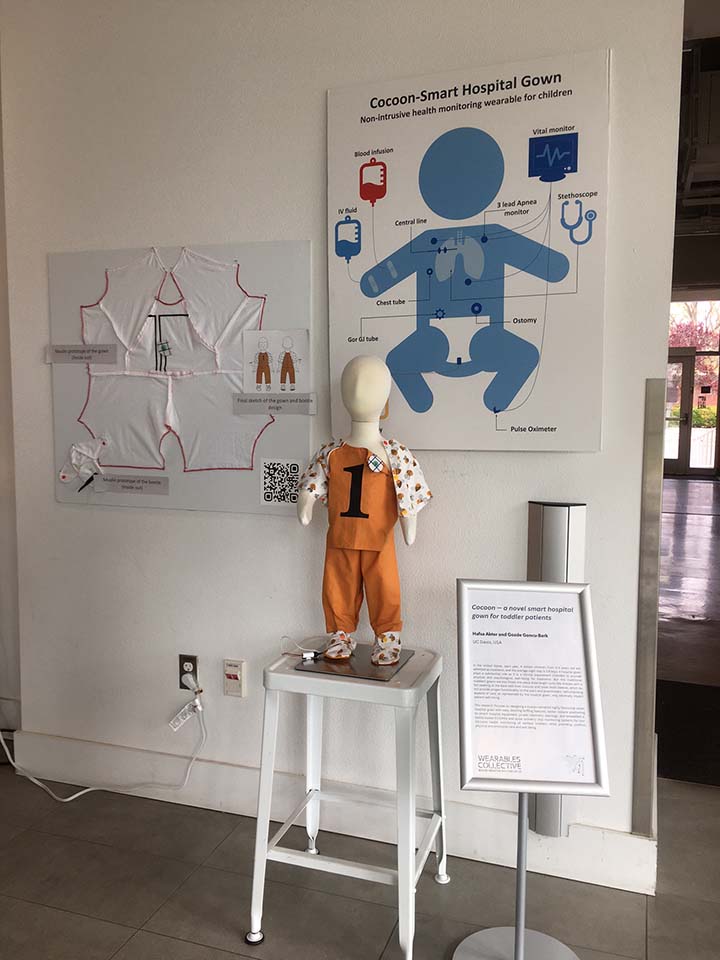
As hospital gowns play an important role in the toddler’s experience, the study presented is directed at improving the gown’s functionality, usability and comfort as well as overcoming issues around poor fit, reduced mobility and rejection by child patients. The work brings together different stakeholder perspectives such as the patient and caregiver as well as the healthcare professional. Parents described the loose fit of one-piece gowns as more uncomfortable for their children researchers found during interviews, with the reason attributed to the unfamiliarity of the form and its fit compared with the childrens’ regular clothing. Sensorial and thermal comfort needs were also highlighted by parents, while for nurses easy access for pulse oximeters is a key design problem.
A design that would allow for the non-intrusive monitoring of vital signs was identified as offering an improvement to the patient’s physical and emotional wellbeing during hospital stays. The researchers have set about developing two designs. The first is a novel smart gown incorporating e-textile-based signal transmission lines to attach devices such as ECG/Apnea monitoring electrodes. The second item is for a bootie for thermal comfort with an embedded POF-based sensor pulse-oximeter to allow for the non-intrusive monitoring of oxygen saturation levels. The discussion and feedback process continued through the development, taking on board nurses’ suggestion to color-code snaps to enable easy donning/doffing. The color system was also used for navigating closures with the right side red, left sides yellow and a QR code for video instructions printed inside each gown.
Dr. Laura Davendorf is an Assistant Professor at the Atlas Institute at University of Colorado, Boulder where she directs the Unstable Institute. Positioning herself as an artist, computer scientist as well as design researcher, she explores the counterfactual narrative around “what if” questions: “What is the purpose of the Anthropocene, we’re not getting what we want might be exactly what we need.” Her presentation “Weaving and counterfactual narratives of technical progress” considers questions such as how might our relationship with devices change if we hand-crafted them with fiber, mended them with thin metals and sought out ways of adapting them to our changing bodies with crochet hooks. Underpinned by complex weaving, the practice of creating complex 3D, electronic, hybrid and robotic structures, she mixes historical textile narratives with current practice such as artist-in-residence at her lab. Davendorf’s aim is to craft a technology narrative that emphasizes humility, care and a sense of community with the AdaCAD open-source complex weaving toolkit and its international community network at its core.
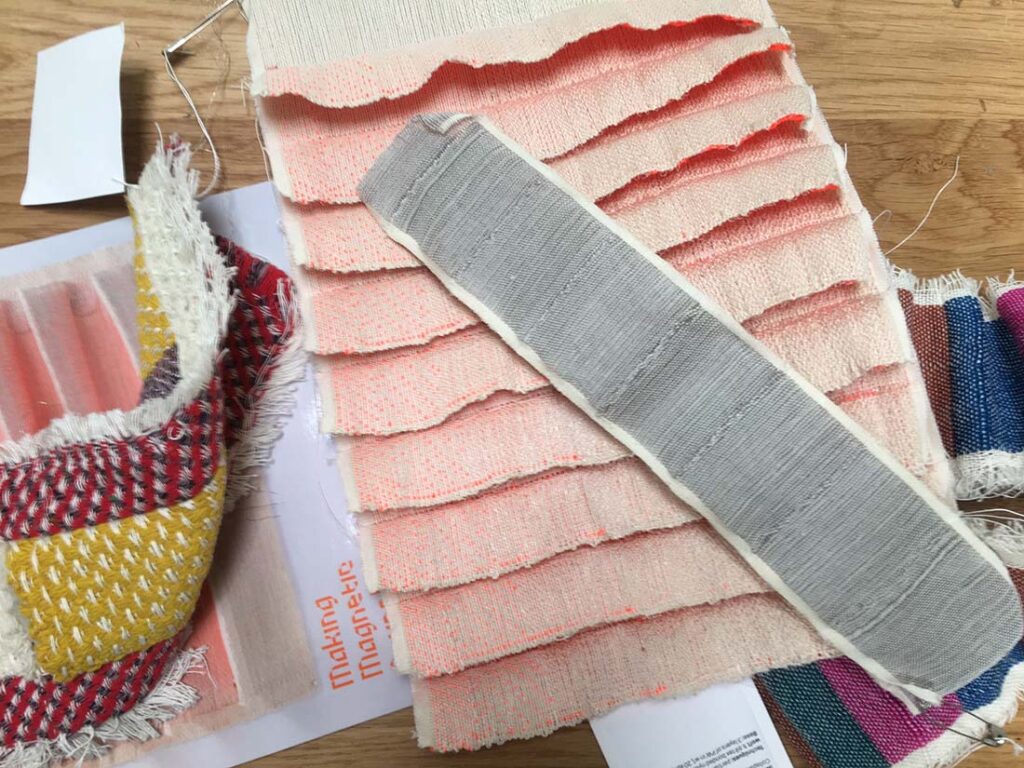
The Experimental Weaving Residency was established in 2019 with the intention of fostering a spirit of exploration and collaboration between textile designers, artists, programmers and open-sourcing new techniques in textile fabrication. Elizabeth Meiklejohn took up the residency in 2023, working with Irene Posch and Davendorf to develop project ideas.
With the focus on process and community cooperation, a form of design bookkeeping was established. This included detailed notes directed at a future self that might one day want to extend the work, so that the bookkeeping is not simply a documentation of the techniques, but also a recording the ‘why’ of the decision making: “This is the only weft sequence that will work!” This process of community sharing and feedback is gaining traction in a sector that is particularly guarded of its IP as much in academia as in industry.
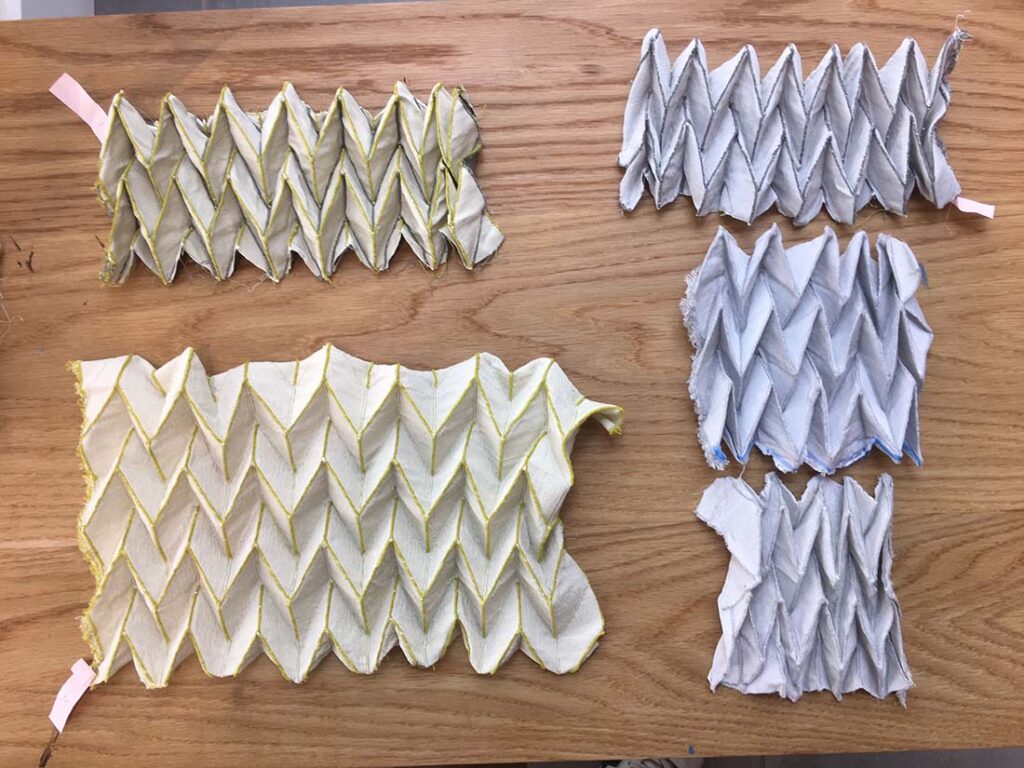
Traditional weaving as a basis for woven pleated e-textiles is the subject of Bine Roth (RCA) and Dr. Kaori Ueda’s (Saga University) research discussed in their joint paper “Nishijin Weaving and Pleating to Create Textile Sensors.” The work looks at ways of creating stretch in weave to move more easily with the body, as an alternative to knitted structures. The main challenge is in using the traditional weave to craft sensors that unfold and align easily with the movement of the wearer with the potential for use in movement tracking for health applications. Nishijin weaving is a Japanese technique that uses hatcho nenshi (involving significant twisting of silk yarn that shrinks when immersed in hot water) and creating a doubleweave structure with a brocade-like texture. Used here, the high-twist yarn allows the material to “shrink” into the pleated structure with the conductive thread also responding to the heat causing it to contract, effectively giving the fabric the properties of a shape memory material. The addition of sensors monitor body movement or vital signs, with the well-defined folds allowing for accuracy in localized sensing placement within a finished garment.
Materiality is a vital component in comfort and user-engagement for wearables, and there is no single way to achieving this. Academia brings a particular lens to bear on how these questions are looked at and in solution-finding to the benefit of the whole sector.