Technologies That Can Close the Loop From Fiber to Fiber
An emerging theme at the huge ITMA 2023 textile machinery exhibition held in Milan, Italy, last June, was the need for advanced technologies for the recycling of fibers and textiles.
By the time of the next edition of this major industry event, which will be held in Hannover, Germany, from September 16-22 2027, it’s likely that the space devoted to such technologies will be significantly expanded as a result of the current push to establish fiber-to-fiber recycling in automated closed loop manufacturing systems.
Two technology areas which were not featured to any noticeable extent at ITMA 2023 were systems for the successful sorting of textile waste prior to recycling – identified as a major bottleneck – and those for the chemical recycling of fiber-based materials that cannot be reprocessed via established and preferable mechanical technologies.
Sorting Goes Digital
At present, as far as textile sorting is concerned, NIR (near infrared) spectroscopy is widely employed, using handheld devices or sorting tables in which samples are exposed to electromagnetic waves to establish their chemical signature. With hyperspectral imaging, the detection of non-uniform materials on surfaces is also possible.
Advanced digital waste sorting technologies, however, developed to meet the needs of other industries already more advanced in recycling, such as metals, plastics, packaging and paper, are now being rapidly adopted for textiles and a leader in such technologies is Tomra, headquartered in Oslo, Norway.
This company specializes in waste management and material recovery systems with sensor-based sorting and grading technology and already has more than 110,000 installations in 100 markets operational globally. Employing 5,400 people around the world, Tomra has annual revenues of €1.4 billion.
Its Autosort sorting systems are based on flexible sensor configurations and for the sorting of textiles combine high precision near-infrared (NIR) and visual spectrometry sensors to separate whole materials by color and type.
Automated Sorting Installations
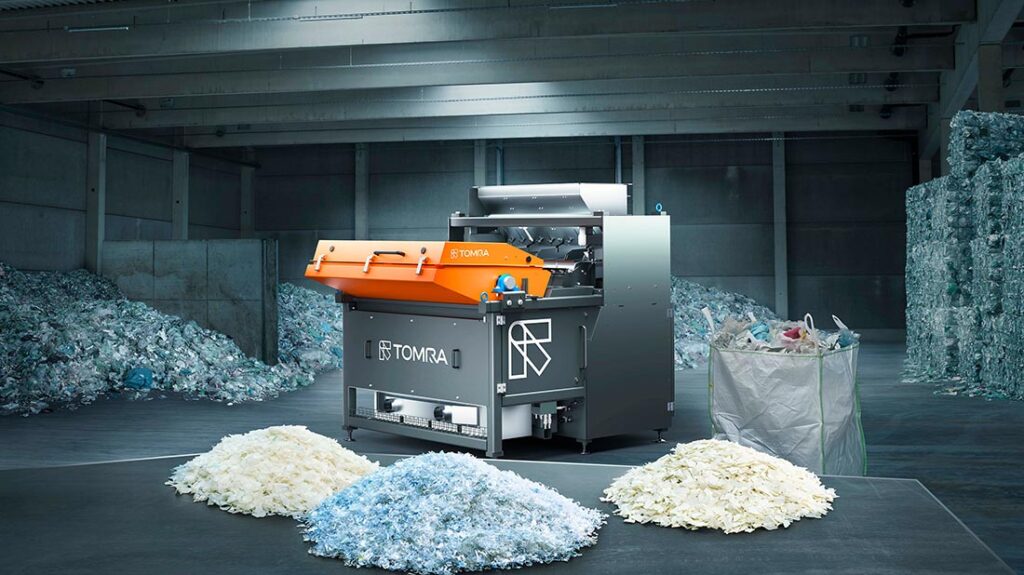
Tomra was the main technology provider to the world’s first fully scaled automated textile sorting facility, SIPtex, established in Malmö, Sweden in 2021, and this has provided valuable lessons for optimizing and reconfiguring technology for the industrial-scale sorting of post-consumer garments.
In addition to Tomra, automated sorting lines for textiles are also now being manufactured by Pellenc ST, of Pertuis, France, Picvisa, of Barcelona, Spain, and Valvan, of Menan, Belgium. Ten textile waste sorting lines are known to be currently either fully established or in development in Europe.
In addition to SIPtex, this includes two in France at CETAI and Synergies, one in Germany at Soex, Texaid in Switzerland, LSJH in Finland, Wieland Textiles in Denmark, Coleo Recycling in Spain and the Salvation Army in the UK. In addition, the fully automated sorting, fiber recycling and preparation and nonwovens production line of Nouvelles Fibres Textiles was inaugurated in Amplepuis, France, in November 2023.
Building a Stream
The newly-established Tomra Textiles division of the Norwegian group is now teaming up with Carbios, headquartered in Clermont-Ferrand in the French Auvergne region, to establish a textile waste collection, sorting and preparation stream in Northern Europe.
The collected material will be prepared via Tomra technology and transported to the first commercial Carbios plant which is currently under construction in Longlaville, France, at a cost of €54 million. It will then be converted back to monomers for PET polyester fibers using the enzymatic depolymerization technology developed by Carbios.
“The textile industry has been optimized for cost and efficiency for centuries,” says Vibeke Krohn, head of Tomra Textiles. “Closing the gap means scaling all the elements of a circular value chain – from collection to sorting to recycling. Future recycling solutions depend on reliable access to feedstock and through this collaboration with Carbios we hope to stimulate the further investments needed to scale textile circularity.”
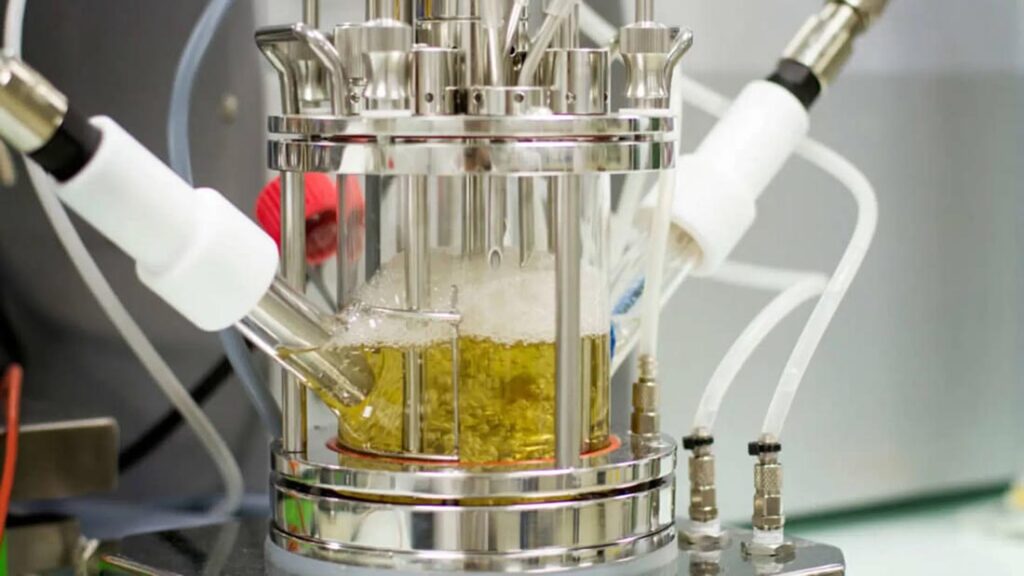
The Carbios process deconstructs any type of PET – the dominant polymer in bottles and trays, as well as textiles – into its basic monomers, which can then be reused to produce new PET fibers and plastics with equivalent quality to virgin.
Carbios already has take-off agreements with major apparel brands for the regenerated PET from its Longlaville plant, including On, Patagonia, Puma, PVH Corp., and Salomon, but in addition to operating its own plant, is seeking to establish itself as a leader in chemical PET recycling technology via licensing agreements.
Partnership in China
This July, Carbios signed an agreement with Zhink Group to establish a new PET polyester recycling plant in China.
Zhink Group is one of China’s Top 500 private enterprises and specializes in both PET polyester and textile production.
The two companies are planning a long-term partnership beginning with a first licensing contract to build a plant with a minimum annual processing capacity of 50,000 tons of prepared PET waste.
China is the world’s largest PET producer and also currently accounts for 78% of all recycled PET, at present largely from bottles.
Turkey as Near-Shore Partner
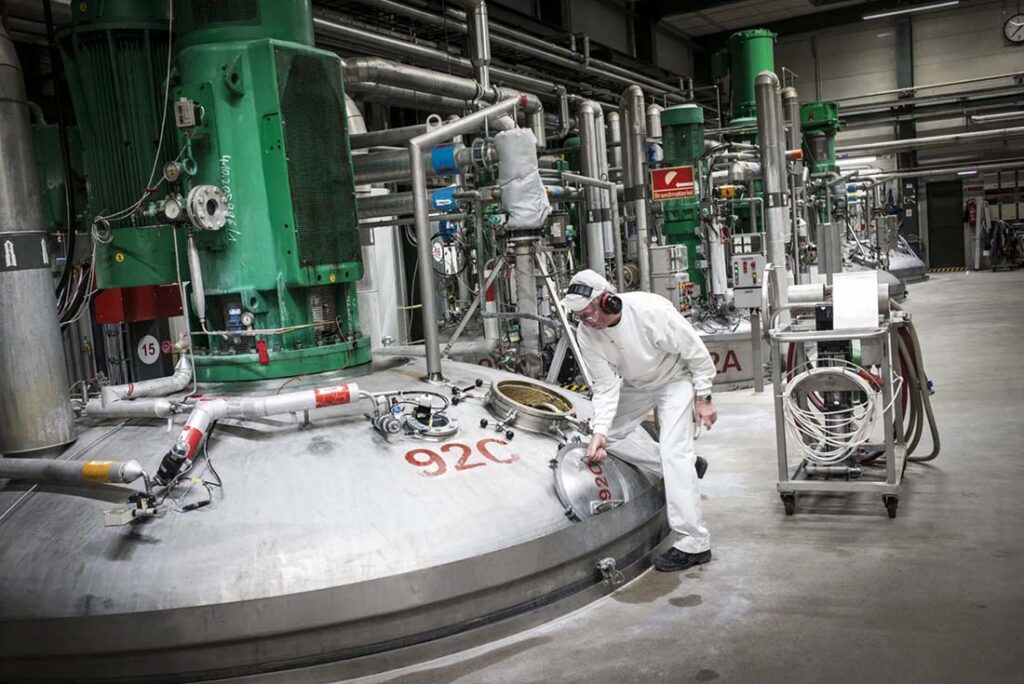
In August Turkey’s SASA announced that it is also in discussions with Carbios to license a PET biorecycling facility with an annual capacity of 100,000 tons that it will build and operate at its site in Adana.
“As a leading producer of polyester, it’s our duty to pave the way in terms of sustainability and environmental responsibility,” says SASA general manager Kemal Oz. “SASA needs to be a part of the recycling business and our partnership with Carbios reinforces our commitment to innovation to advance a circular economy for textiles.”
As the EU’s closest near-shore partner, Turkey is ideally positioned to lead the field in the conversion of fiber-to-fiber recycled materials into new products.
In fact, this is already happening, and it’s no surprise that many European machine builders are partnering with Turkey’s fiber and fabric manufacturers for the next big opportunity.
“With the creation of a major PET yarn and fiber manufacturing capacity on a European scale, we believe Turkey will play a pivotal role in the expanding textile market,” observes Carbios CEO Emmanuel Ladent. “Partnering with SASA is a natural fit for our international ambitions for licensing our biorecycling technology.”
As the EU’s closest near-shore partner, Turkey is ideally positioned to lead the field in the conversion of fiber-to-fiber recycled materials into new products.
SASA’s Ambitious Plans
This is only a component of SASA’s current ambitious plans that aim to see Turkey soon become entirely self-reliant in the raw materials for polyester production.
A new $1.5 billion SASA Polyester plant for purified terephthalic acid (PTA) is poised to come on stream this year in Adana, with an annual capacity of 1,750,000 tons. In addition, the company, which is owned by Erdemoglu Holding, plans to have a second $400 million PET polyester fiber plant also operational before the end of this year, adding a further annual capacity of 402,500 tons.
This will instantly position Turkey as a net exporter of PET, rather than a net importer. Oz points out that raw materials self-reliance is how both South Korea and China strengthened, stabilized and significantly grew their textile industries.
Waste Management Interest
Finally, the UK has been announced as the latest potential location for a licensed Carbios enzymatic depolymerization PET recycling plant.
Doncaster-headquartered FCC Environment, one of the UK’s leading recycling and waste management companies, has signed a letter of intent with Carbios to jointly study the implementation of a plant in the UK using the technology.
For Carbios, this confirms interest from the waste management sector, in addition to from plastic and fiber producers, and would mean a foothold for its technology in the UK.
“We need to think creatively about how we recover the value in materials that society no longer wants and textiles – as we know from our work promoting a reuse culture – pose a huge challenge,” says FCC Environment CEO Steve Longdon. “We are keen to explore with Carbios what contribution this technology could make to the UK circular economy and to examine further its place in the UK waste hierarchy from a firm evidence base.”