Testing New Manufacturing Processes for Composites Reinforced with Natural Fibers and Biological Resins
The utilization of biological materials as reinforcement in the development of industrial composites emerges as a potential, more economical and sustainable alternative to replace synthetic components like carbon fiber or glass fiber. However, the use of biocomposites also presents technical challenges in the case of structural applications due to their less regular and solid properties.
The Spanish technology centre IDEKO has been participating since this year in the European BioStruct project to solve the technical problems associated with the use of bio-based composites in industrial structures for sectors such as the wind energy or maritime.
The main objective of the initiative, funded by the EU’s Horizon 2020 programme, is to develop and validate new manufacturing processes to boost the use of biocomposites.
The solution proposed by the project will be validated through two use cases: the manufacturing of a hull for a six-metre electric boat and the production of rotor blades for wind turbines. In both cases, natural fibers and bio-based resins will be used as construction materials, paving the way towards a greener and more sustainable industry.
International Fiber Journal spoke with Roberto Alonso, researcher from IDEKO and a spokesman for the project, to shed light on the ongoing project that concludes in 2026.
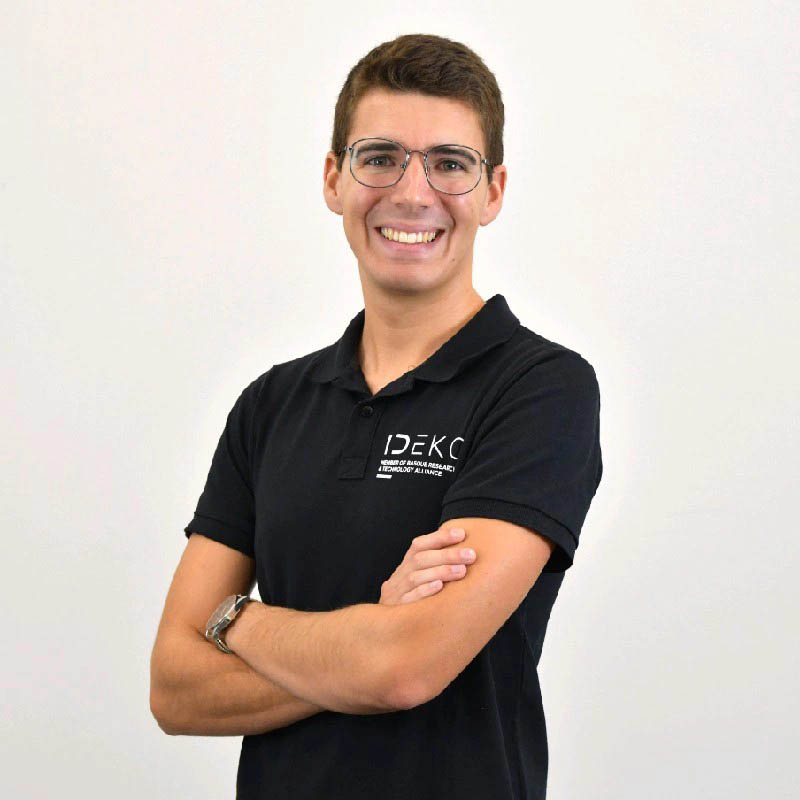
International Fiber Journal: Please provide a general description of the project.
Roberto Alonso: The BioStruct project aims at the development of advanced technologies for the manufacturing of composite parts made from biomaterials. This will enhance the use of such materials in parts with structural requirements and thus reduce the need for conventional carbon and glass fibre composites.
IFJ: Explain the process to incorporate hemp and flax into these 3D construction materials. What led to their use?
Alonso: There are persistent economical and technical problems with the recycling of conventional fibre-reinforced composites made from glass or carbon fibre. The use of biomaterials for such composites would provide a solution, but there are issues with the use of such materials in parts that have structural requirements. The BioStruct project aims to bring bio-composites one step closer to structural applications by addressing technological topics that relate to the manufacturing of such parts. The following key technical topics have been identified:
- Natural products such as bio-based fibres have a higher variability in term of dimensions, weight and appearance. Nevertheless, high precision is required when handling fabric made of natural fibres.
- The mechanical properties of natural fibres and resins need to be better understood to enable the accurate design of structural parts and thus make such material usable also for structural applications.
IFJ: What confirmed the use of hemp and flax for biomaterials in 3D structures?
Alonso: The process of handling a piece of fabric (typically glass or carbon fibre) and placing it in a mold is called draping. The main challenge is to ensure that the piece of fabric (ply) is placed in the correct location (typical tolerance: 1mm and below) and to control how the fibres re-orient themselves during the draping process (typical tolerance: ±3-5°). This re-orientation happens, when the flat fabric adapts to the complex 3D free-form shape of the mold. Controlling this process is important, because fibre orientation has substantial impact on the mechanical performance of the part. The draping strategy often includes so called seed points or seed lines from where the draping starts and propagates through the fabric.
The main challenge when handling fabric made from natural material is the higher variability of the material. Compared to carbon and glass fibre, the material properties vary much stronger within a batch of material, but also between different batches as the properties depend on the climate and weather conditions during which the plants have grown. In order to ensure that the handling is done with high precision, the BioStruct project needs to advance the state of the art in the following aspects:
- The weight of the fabric might be higher than this is the case for glass or carbon fibre. In contrast to the distortions of glass and carbon fibres with needle grippers, it is not expected that natural fibres are distorted or even damaged by this method which might be able to hold heavier fabrics more accurately.
- The friction between the surface of the suction heads and the fabric has impact on the draping process. To account for the higher variability of the material, control methods will be developed.
- The well-defined appearance of carbon and glass fibre makes it easy to perform accurate measurements.
- Measurement of fibre orientation will require a new approach that does not rely on the particular reflectance properties.
All of the measurement systems mentioned above will be equipped with real-time capabilities to ensure that in-process measurements can be done, and inline process control will be feasible.
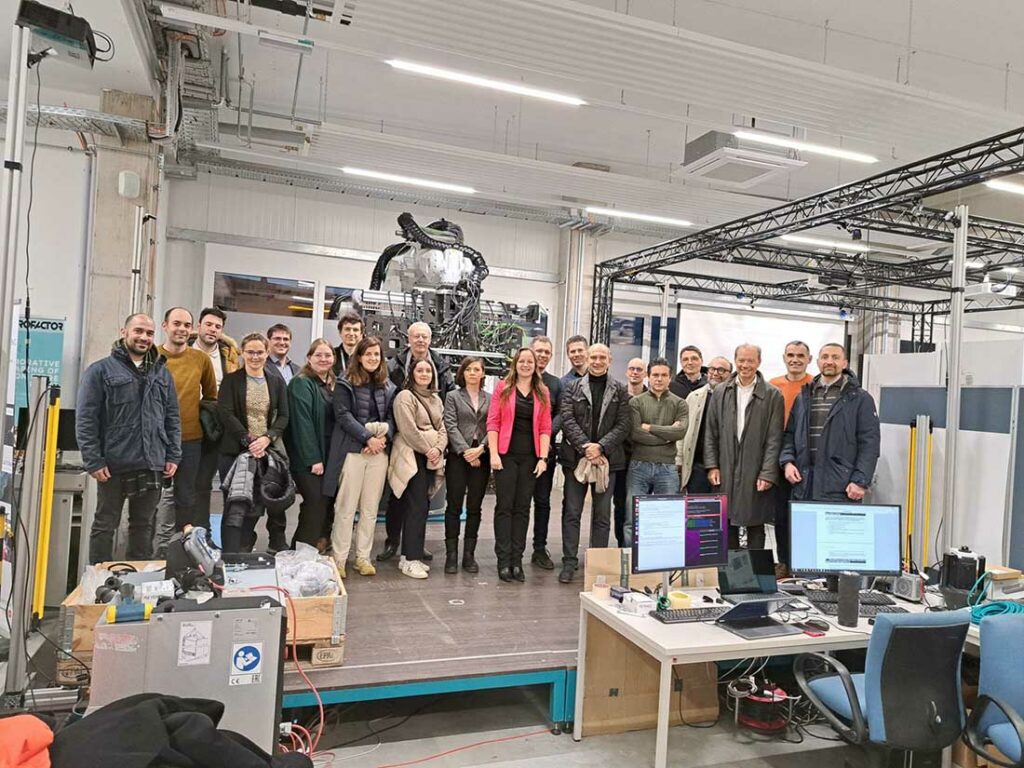
IFJ: How does sourcing from Europe add to the benefits of BioStruct and its circularity and sustainability goals?
Alonso: These developments will advance the use of bio-composites in domains, where these are not yet considered at a larger scale, e.g., in boatbuilding and sports equipment. This will replace glass or carbon fibre and thermoplastic or thermoset resins that are difficult to recycle. Based on the current use of composite materials in different domains, a share of 25%-45% of the total market could possibly be addressed through bio-composites with a potential market value of 100M€ for BioStruct technologies by 2030. It is understood that currently bio-composites are not suitable for high-end structural applications in aerospace. This domain (structural parts I aerospace) is thus not the main focus of the project.
IFJ: Explain the manufacturing processes being explored in this process.
Alonso: The overall concept of the BioStruct project is to enable the accurate manufacturing of parts made from biocomposites, with a particular focus on quality so that they fulfil requirements in terms of mechanical properties. The main developments are summarized per objective O1-O3 below and are further detailed in the following subsections.
- Handling of natural fabric: handling and draping of the fabric will have to deal with and compensate the higher variability of the material to ensure constant quality as required for structural parts.
- Material models of bio-composites: to enable the use of bio-composites in structural applications, accurate material models are needed for finite element simulations and to obtain high-performance part designs that have minimal weight.
- Integrated load sensors: to enhance the applicability of bio-composites, a manufacturing technology for integrated load sensors will be developed to monitor of loads and deformations.
IFJ: What is the role of 3D scanning in the research process?
Alonso: 3D Measurements will be used to assist with the development of the material models. The main technology is 3D scanning that use the laser triangulation principle to obtain a dense cloud of points. The second technology is 3D scanning by photogrammetry. This technique allows the fast measurement of all the details of the shape, along with inner and difficult-to-access surfaces. The first development in this objective will be a correct fusion of these techniques.
IFJ: How is BioStruct expected to increase productivity and quality in high-precision manufacturing to meet the EU objectives?
Alonso: Reductions in the use of materials, waste, defects and energy consumption, also lead indirectly to reductions in GHG emissions. Through the manufacturing technologies resulting from the BioStruct project, a substantial reduction of green hour gases can be achieved. Due to the focus on structural applications of bio-composites, the market potential is up to 45% of the total market, assuming that there are no applications in aerospace. This is somewhat of a worst-case estimate because there is certainly a potential for the use of biomaterials in aerospace interior parts.
The rough balance in terms of CO2 emissions is shown in the table below on the example of hemp fibre (flax will have similar numbers) in comparison to glass and carbon fibre. The main factors are the reduction of CO2 through the replacement of carbon and glass, the sequestration of CO2 during the growth of hemp and the CO2 generated during the processing of hemp fibres. The BioStruct project
thus has a potential of saving between 2.5 and 4.3 Mt of CO2 per year, assuming that a significant market share in non-aerospace applications can be achieved.
IFJ: What industries were chosen as the project’s first focus?
Alonso: The current competitive position of Europe in carbon and glass fibre manufacturing is not very strong. 80% of all such fibres are manufactured outside of Europe and of the remaining 20% about half of it is manufactured under foreign licenses. This creates a dependence on other countries. Biocomposites will be one possibility to reduce such dependence, especially if it is possible to take the step from single prototype and ‘decorative’ parts to a wider range of applications in series production of structural parts. The BioStruct project aims at achieving this step.
Aside from the aerospace and defense market, where very tight restrictions exist in terms of materials and processes (and for good reasons), the whole remaining composite market is relevant for bio-composites. The total market share (by weight) is about 50% with sports equipment, wind turbines, automotive, construction and maritime applications being the most relevant ones. The BioStruct project directly addresses 25% of the market, through the use cases in the field of boat building and wind energy.
However, there is also big potential for applications in sports equipment (contacts with Decathlon already established) and automotive, which will increase the share to 45% of the market. Through the introduction of biomaterials, the project has the potential to reduce the dependence on foreign raw materials. Hemp is grown all across Europe, with France (62%) being the largest producer.
Currently about 32.000 hectares are used for hemp cultivation, producing more than 150.000t per year. Similar numbers apply to flax, where 80% of the flax needed in Europe is also grown here. Consequently, by using natural fibres, the dependence on imported goods will substantially reduce, thus enhancing the autonomy of the European composites industry.
IFJ: How does the partner consortium work together on this project?
Alonso: The consortium has been selected to cover all key components to demonstrate high-precision manufacturing of biocomposite parts. The project was co-funded by Horizon Europe, the European Union’s research and innovation program, and this public-private European partnership involves 10 organizations European organizations, both public and private: Profactor, Abele, Amura, Bladeworks,
CIDETEC, Enginsoft, IDEKO, Lumoscribe, NOMA, Techtera.
Amura and Bladeworks will provide the manufacturing lines for manufacturing of a boat and a rotor blade. This manufacturing line will be equipped with additional systems for process control for draping (Profactor, Abele), for cure monitoring and 3D dimensional measurement (IDEKO) to enable high-quality products in the presence of higher variability of the materials. A process for manufacturing and integrating bio-based load sensors (Profactor, lumoscribe) will be developed. The bonding process will be provided by CIDETEC. Enginsoft will provide the simulation support for part design, including new material models, and for process monitoring (draping, curing).
All processes mentioned above will be integrated into the manufacturing processes for the final demonstration.
Bio-resins will be provided by NOMA, bio-adhesives will be provided jointly by CIDETEC and NOMA. Natural fabric and the cure monitoring systems are available on the market and will be used for the purposes of the project but are not in the focus of the developments. Techtera will support the consortium with dissemination activities and perform a mapping of suppliers of biomaterials in Europe.
IFJ: What is the next step in BioStruct?
Alonso: Currently, the first test coupons of these materials are being developed while the technical specifications are being defined to begin the initial measurements.
IFJ: We will be following your progress.