The Automotive Marketplace for E-Textiles and Smart Composites Is Thriving
New developments in Printed Electronics (PE) and Flexible Hybrid Electronics (FHE) were shown at this year’s LOPEC held in Munich on March 5-7, 2024. This is a field of growing market significance for e-textiles, and smart composites with market applications across health and medical, transport, energy and industrial – essentially anywhere that electronics are conventionally being used. This review concentrates on transport, and the automotive in particular, from dynamic smart surface pattern to road safety to weight-saving and smart batteries. In some instances, fibers and textiles are already being used, while in other examples there is strong potential for textiles to replace other flexible materials so that opportunities and barriers are discussed.
“The technology is already an integral part of vehicle construction today and is indispensable for the mobility of the next generation,” according to Wolfgang Mildner, General Chair of LOPEC and CEO of the consulting and technology company MSWtech. There are a number of attributes that appeal to the automotive sector such as the thinness and flexibility that brings a reduction in weight and allows them to be integrated more seamlessly coming closer to, or even onto the surface of the vehicle interior. Design, color material finish (CMF), haptics, integration with textile and lighting are all combining to raise consumer and brand interest. There are now well-established examples of PE and FHE in transport, from seat heating and occupancy sensors to airbag control and surfaces with button controls giving way to a more streamline interface with touch functions.
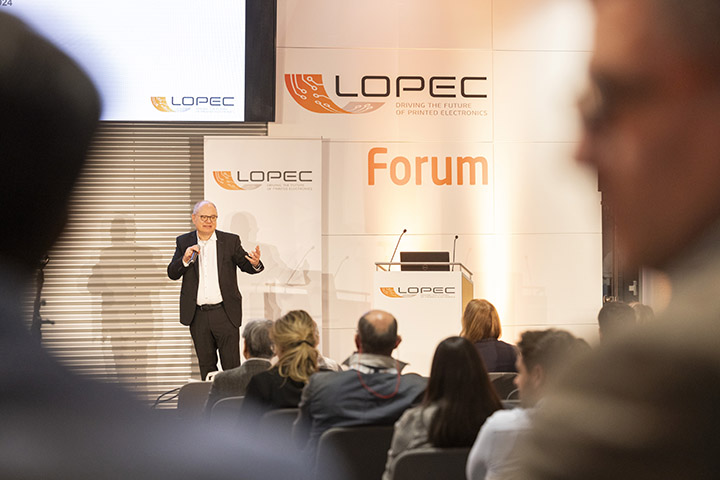
Indicative of the strength of innovation in the automotive sector were two LOPEC awards given to the sector this year. The Public Choice Award at LOPEC went to EURECAT for their 3D HMI Automotive development that showcased an HMI just 3 millimeters thick. This allows users to interact and communicate with a machine, software or intuitive system with integrated LEDs and capacitive sensors designed to be embedded into the central electronic control system of vehicles. The Best Publicly Funded Project went to Joanneum Research, Arkema Piezotech Innovation Lab and Rise, for their smart wheel energy autonomous sensor system for smart tires amongst other applications. The development harvests mechanical motion and vibration from the environment, converting it into electrical energy using piezoelectric elements to power sensors and transmit data. These self-powered sensors are especially useful where they are needed in places that are difficult to access and where the use of batteries requires a high level of maintenance. The growth in rental e-bikes has led to a need to monitor bike conditions remotely. The smart tyre is particularly aimed at this market, as it can be used for the automatic remote monitoring of the pressure of bike tubes helping to reduce maintenance costs and decrease energy consumption. The bicycle tube uses a thermoplastic polyurethane (TPU) found to be more robust and resistant in needle penetration tests than conventional butyl rubber. The pressure of the bicycle tyre affects ride comfort, puncture resistance, grip and rolling resistance. The latter impacting on the battery life. In the automotive sector tyre pressure monitoring is required by law. E-bikes are generally not classed in the same way as yet; however Alaska has classified e-bikes as “motor-driven cycles” requiring a license to operate one but not registration or insurance. In North America e-bikes are subject to the Energy Labelling Rule (16 CFR Part 305), that applies to electrical products and appliances. This points to one of the challenges in compliance and standards for new products, showing that in addition to product area specific regulations, developers may also need to take account of additional directives directed at the product as a whole, a subset component or function.
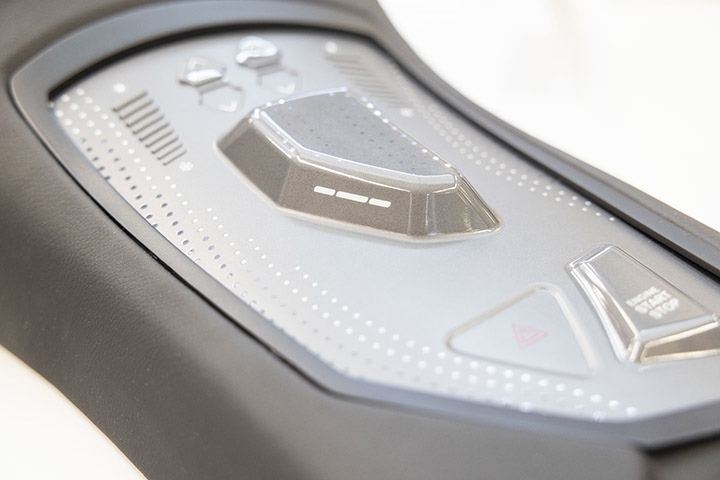
There are 1.19 million fatalities on the road each year according to IEE, with 94% of these due to human error. According to the National Highway Traffic Safety Administration (NHTSA), 42,514 people lost their lives in car crashes in North America in 2022. In addition to the human cost, the financial burden is put at a staggering 3% of GDP for most countries worldwide. Regulations are driving the process of implementing both active and passive safety systems. The growth of autonomous or self-driving vehicles (SDVs) is expected to likely to increase safety according to NHTSA, however a recent British Government Transport Committee report on SDVs echoes wider public concern about their safety. SDVs allow for the driver to take their hands off the steering wheel. However, with Hands off Driving (HOD) functionality there has to be a clear distinction between when the vehicle and when the driver is in charge as there are instances when the driver is asked to take back control. The Automated Lane Keeping Systems (ALKS) is regulated by UN R157, and this includes a “hands on” detection system to be in place as a key condition for the transition from automated to manual driving mode. IEE have used flexible and stretchable electronics integrated into the steering wheel of the vehicle to create a capacitive sensing system. This is used to monitor the presence of the driver’s hands on the steering wheel and control of the driving. It can be integrated into any steering wheel and is not impacted by additional technologies such as wheel heating systems. The technology has already been used in over a million vehicles.
Structural health monitoring is growing in importance for transport, and for aerospace in particular. Smart composites that can integrate sensors for continuous detection of impacts and cracks. Advances in manufacturing allow for sensors and actuators to be embedded reducing the number of assembly steps, materials and cost. There is an additional positive from an environmental point of view as the repair and maintenance extends the use phase of the aircraft.
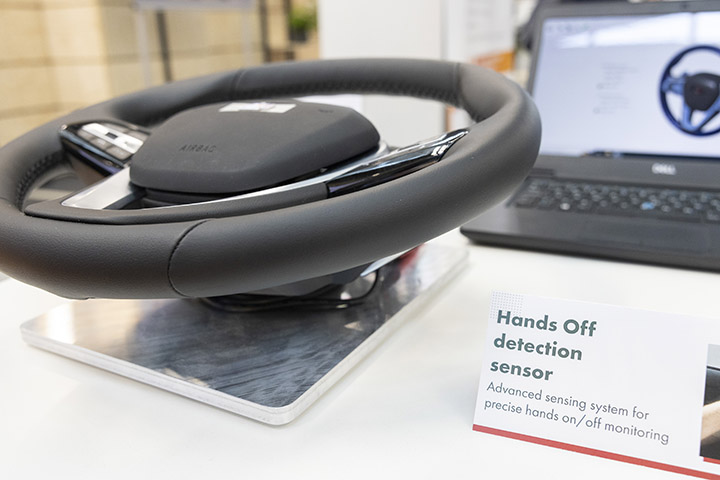
The EU-funded Morpho is concerned with embedded life-cycle management for smart multimaterial structures. It is focused on developing a new generation of aeronautical structures around the three pillars of innovative industrial processes, foreign object damage and environmentally friendly manufacturing. Fraunhofer IFAM with ten partners from six European Union countries, are undertaking research and development in engine components, with the program started in 2021 and scheduled for completion in September 2024. Their ambition is to endow engine fan blades with cognitive capabilities and to optimize their manufacture and lifecycle management. Embedded printed sensors, data-driven hybrid twin and machine learning technologies are all being employed.
Arkema-Piezotech have developed piezoelectric polymer sensors for use in the structural health monitoring of composite hydrogen tanks. The French company specialize in a unique range of electroactive polymers.
Printed thermocouples are being used for temperature measurement and printed piezoelectric sensors for impact detection, both printed on carbon fiber reinforced plastic (CFRP) composites in lightweight components. There are three layers to the printed piezoelectric sensors. The top and bottom layers both with electrodes and the middle carrying a piezoelectric layer. Thermocouples type T (Cu-CuCuNi) are applied to the CFRP using an aerosol jet printing process. These are seen as particularly useful in monitoring temperature change in components that are difficult to reach such as aircraft parts and the engines.
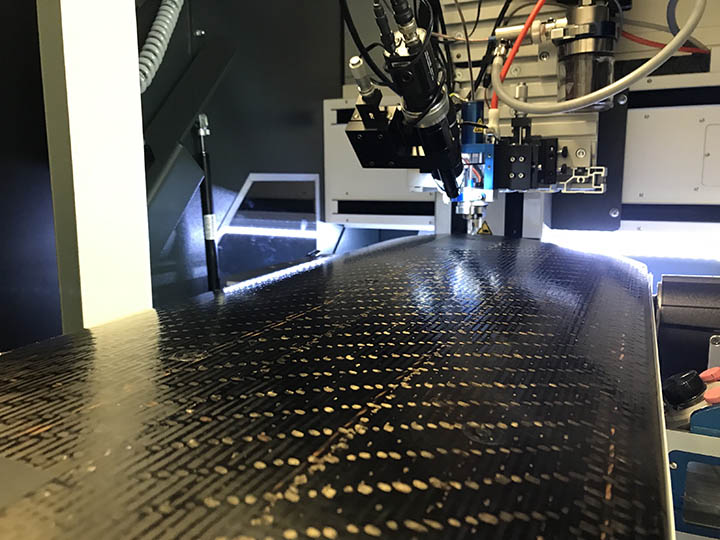
Arkema-Piezotech have developed piezoelectric polymer sensors for use in the structural health monitoring of composite hydrogen tanks. The French company specialize in a unique range of electroactive polymers. “Electroactive polymers are fine, lightweight and flexible, and can be integrated using simple procedures” according to Fabrice Domingues dos Santos, Head of Development for the Piezotech range, “They cost very little in terms of energy and offer infinite opportunities.” Looking to growth predictions of six million hydrogen tanks likely to be produced globally by 2030 (The Hydrogen Council), Arkema is developing a number of solutions that are aimed at improving the performance and the carbon footprint of hydrogen vehicles.
Their Elium liquid thermoplastic resin is being used with carbon fibers for the high-pressure storage of on-board hydrogen. This allows the polymerization to be carried out during the winding process avoiding the additional curing time required by traditional epoxy resins. This saves both time and energy with good recycling potential at the end of life. Keeping the tanks in use for as long as possible and guarding safety, the company have developed fluorinated electroactive polymers in their Piezotech range of materials. These are used as sensors embedded in the composite to provide continuous monitoring of the hydrogen tanks for shock, acoustic vibration and composite deformation.
Illumination in many forms was a focus at LOPEC for the automotive market in particular. Function and aesthetics were brought together as never before. “Light is the new chrome” one speaker quoted Klaus Bischoff, Chief Designer at VW that seemed to sum up the mood. However, it was the BMWi5 Flow Nostokana, a tribute to the 1991 Esther Mahlangu Art Car that gained attention at LOPEC. Challenging how the driver and spectator sees and considers surface pattern and color, the dynamic surface pattern is a collaboration with E-ink, using their latest E Ink Prism 3 color e-paper technology to demonstrate its capability as fully programmable, low energy and durable. The 240 segments on the BMW I Vision Dee could display up to thirty-two different colors, with the potential for tens of thousands of pattern combinations. The latest BMWi5 Flow Nostokana has been outfitted with 1,349 segments each can be individually controlled to allow for even more color and pattern designs to be created.
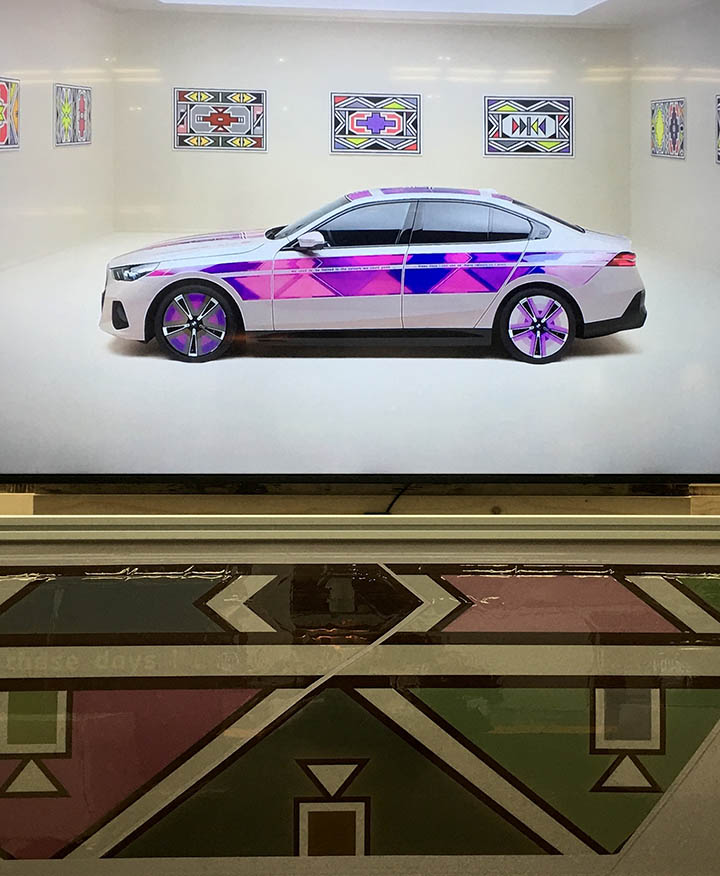
Sustainability ran throughout as speakers and exhibitors addressed the question when discussing new developments. Use of raw material, design for disassemble, recyclability and energy were just some of the topics raised around this. There was much creativity and innovation, with E-ink a good example. The company is a member of The Climate Pledge and the Science Based Targets Initiative (SBTi), committed to achieving zero carbon by 2040. A mark of this progress is that they are the first display technology to receive the Dark Sky Certification from the International Dark Sky Association and in this way helping to combat and raise awareness of light pollution.