From basalt to recycled carbon to sustainable nylons, today’s advanced fabrics are exhibiting environmentally sound components that are sustainable and innovative.
An emphasis at the Techtextil show in Frankfurt, Germany from June 21-24, 2022 – as was also the case at the recent JEC World composites show in Paris from May 3-5 – was on the sustainable content of the latest advanced fabrics, whether based on recycled raw materials or natural fibers.
Recycled carbon
At JEC World, for example, Gen 2 Carbon introduced a new 60gsm recycled carbon fiber nonwoven fabric as part of its G-Tex product range.
Around 20,000 tons of waste is estimated to be generated each year during the production of carbon fiber composites and in many hand lay-up processes, waste material can easily account for 50% or more of the total carbon used. Some of this waste is generated as the fabric is initially being cut before impregnation with the matrix material. Additional waste is generated after the composite has been cured and during the post-processing steps where the shape of the final part is further refined.
Gen 2, formerly ELG Carbon Fibre and renamed following a management buyout in May 2021, specializes in transforming this waste and has developed the new lightweight recycled nonwoven in response to customer requests for materials that combine the flexibility of carded textiles with the lower weight usually associated with wet-laid products. The company believes it will strongly appeal to customers in several market segments due to its excellent drape, superior surface finish and consistent, low fiber aerial weight.
A second UK company, Technical Fibre Products (TFP), also introduced a range of recycled carbon nonwovens produced from fibers reclaimed from composites. The materials can be integrated into a composite structure as a surfacing or semi-structural layer, providing a viable route for the recycling of fibers previously considered as waste.
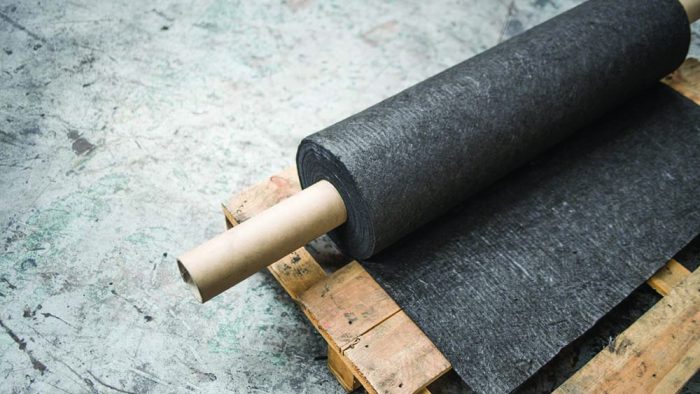
Basalt
In addition, a basalt nonwoven veil has been developed as a more temperature-stable alternative to TFP’s standard E and ECR glass veils. It is stable up to 850°C and retains its integrity when in contact with an open flame, making it suitable for applications requiring a fire barrier. Basalt, like glass, also has a high resistance to acid and alkali, which makes it ideal for use in corrosive environments.
TFP’s established Optiveil and Tecnofire nonwovens provide a wide range of solutions for composites including surface finish, improved resin flow, adhesive carriers and imparting functionality where required, such as for EMI shielding and fire protection.
Flax
Machine builder Karl Mayer introduced new solutions for composite reinforcements made from flax on its Cop Max 4 multiaxial system in Paris.
“We have been focusing on this topic for about two years,” said Hagen Lotzmann, sales manager at Karl Mayer Technical Textiles. “As a renewable raw material, flax is a sustainable alternative to glass and carbon, which can only be manufactured using a great deal of raw materials and energy.”
The European Confederation of Flax and Hemp (CELC) meanwhile showcased the high-performance properties of flax in a specially created Natural Fibre Village.
In addition to the lower CO2 footprint, the natural fiber composite structure also introduces viable options for the end of the product’s life – an issue of increasing concern for the wind energy sector.
Benefits
As a lightweight natural fiber, CELC says that flax can provide benefits such as high specific stiffness, fatigue performance, impact resistance, thermal insulation, acoustic performance, radio transparency and vibration damping, and can be engineered to create structural and semi-structural composite parts.
CELC members exhibited a range of products that have been specifically optimized for industrial scale applications – from automotive interiors to bio-composite building facades, bio-sourced panels and motorsport components.
Among highlights was the first natural fiber reinforced satellite panel developed by Swiss company Bcomp working with the European Space Agency (ESA). Based on Bcomp’s powerRibs and ampliTex sustainable light weighting fabrics, it meets ESA’s stringent technical readiness standards for the space environment.
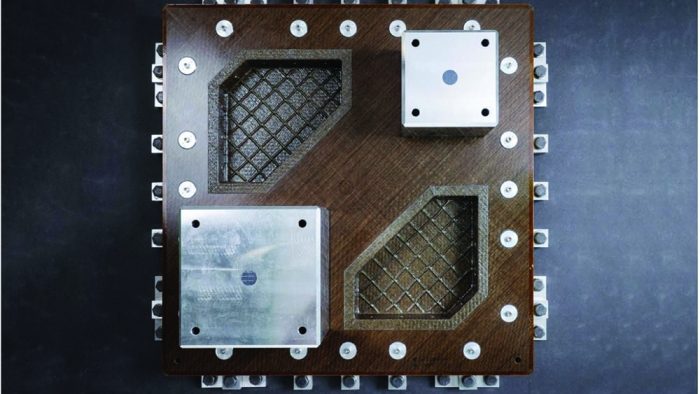
PowerRibs technology is an extremely lightweight, high-performance natural fiber reinforcement grid. Its triple flexural bending stiffness enables weight reduction and dematerialization and up to 250% higher vibration damping.
Inspired by leaf veins, powerRibs fabrics add maximal stiffness at minimal weight by creating a 3D structure on one side of a thin-walled shell element. This enables less base material to be used, lowering weight, costs and consumables in production. The proprietary technology is perfect for high-performance applications, such as replacing or reinforcing carbon fibers in motorsport bodywork or decreasing weight in automotive interior panels.
The ampliTex range of technical fabrics includes different weaves – bi-axials, twills and unidirectional fabrics – with low/no crimp and twist, optimized for lightweight reinforcement. Thanks to excellent mechanical properties and low environmental impact, the ampliTex range is extremely versatile. In addition, it can provide high radio transparency, vibration damping, UV resistance and extended design options.
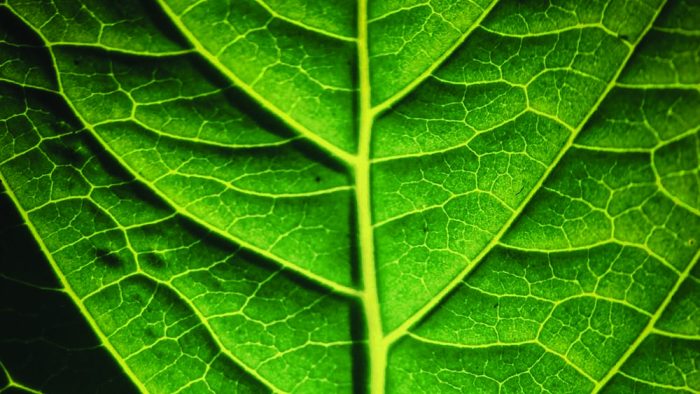
were inspired by leaf veins. Photo courtesy of Bocomp
Nacelle
Meanwhile, Greenboats, based in Bremen, Germany, has developed the first offshore nacelle manufactured with natural fiber composites.
By incorporating the ampliTex flax reinforcements, balsa wood cores and bio-based resins, the nacelle’s construction saves approximately 60% CO2 equivalent and reduces energy consumption by over 50% compared to a nacelle made with existing glass fiber reinforced plastic (GFRP) technology.
In addition to the lower CO2 footprint, the natural fiber composite structure also introduces viable options for the end of the product’s life – an issue of increasing concern for the wind energy sector.
In December 2021, the Greenboats nacelle was delivered to customer Delft Offshore Turbine (DOT) and has initially been installed onshore to undergo an intense testing program. Once this first series of tests is completed, the nacelle will be transported to a permanent offshore location.
Preforms
Lower cost flax preforms and reinforcements for the composites industry were developed in the 56-month €4.6 million French/UK Flower Interreg Project, which commenced in February 2018.
Notable developments include Kairlin monolithic and sandwich structures made from flax and PLA, which are recyclable and compostable, allowing point-of-sale and signage displays to be produced and recycled with low environmental impact. The panels are light weight and easy to machine, with a controlled thickness and mirror-like surface finish.
At each stage of the life cycle, from flax cultivation to end of life, Kairlin panels have been designed and validated at an industrial scale and are produced within a very short supply chain in Normandy. The panels are processed in a one-shot compression molding step with a very short processing time at low cost.
At end of life, Kaïros Environnement plans to collect the panels, grind them and incorporate them in up to 70% of the raw materials for new Kairlin recycled panels. The company’s patented recycling process retains 98% of the mechanical and dimensional properties of the Kairlin panels.
The European Flax label provides composite manufacturers with fully traceable and certified premium-quality flax fibers that are sustainably grown in Western Europe and account for 80% of global production.
New nylons
As noted in the lead feature of International Fiber Journal, Issue 2 2022, much progress is also being made in the development of more sustainable nylons and at Techtextil, C.F. Weber of Leutersdorf, Germany, presented the first fabric samples for workwear made from Cordura re/cor recycled nylon 6.6, initially to be launched in black in three different weave types.
In terms of quantifiable benefits compared to virgin nylon 6.6, the production of Cordura re/cor RN66 produces 83% fewer greenhouse gas emissions, consumes 82% less energy, and uses 57% less water. It is made from 100% pre-consumer fiber material that is 100% GRS (Global Recycled Standard) certified.
“Until now there has been no nylon that meets the high demands for performance and sustainability, especially in workwear,” said C.F. Weber managing director Stefan Friedrich.
Q-Cycle
Montemurlo, Italy-based Pontetorto – celebrating its 70th anniversary this year – is introducing a new collection of fabrics made entirely with Fulgar’s Q-Cycle yarn.
Q-Cycle is obtained from end-of-life tires, considered to be among the most difficult items to dispose of and also highly polluting globally. Every year in Europe, 1.37 million tons of tires – 40% of total production – are mostly incinerated, with high CO2 emissions.
Q-Cycle yarn is produced by a pyrolysis process as part of BASF’s ChemCycling recycling system, in combination with Fulgar’s spinning technology. The process is said to be self-sufficient since the waste portion which cannot be transformed into raw material is pyrolyzed into gas and used to generate the energy required for the process. The recycled content is allocated to the final product by using a third-party controlled mass balance approach.
Q-Cycle is also said to retain all of the functional and aesthetic benefits of virgin polyamide including lightness, strength and resistance to produce high-quality and eco-sustainable fabrics.
ByNature
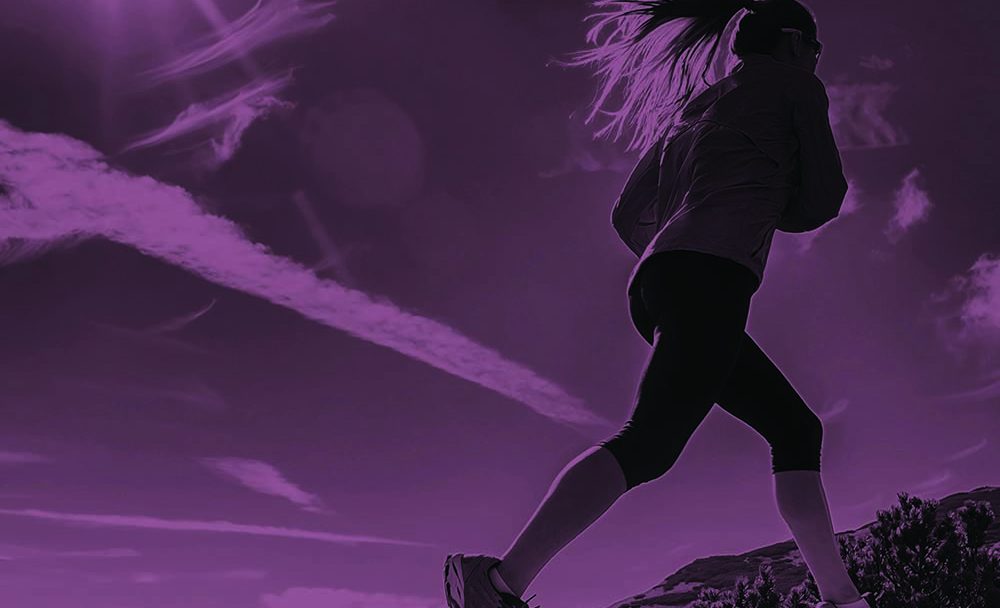
Nilit’s new Sensil ByNature nylon 6.6 also employs a certified biomass balance (BMB) material from BASF to replace fossil fuel-based raw materials with a renewable feedstock.
“Sensil ByNature will significantly reduce carbon footprint while providing the highest quality manmade fiber for apparel,” said Nilit general manager Ilan Melamed. “This is the kind of radical product development that the textile industry requires to effectively and quickly reduce its environmental impact and move to a more responsible position in the global marketplace.”
“We are very excited to work with Nilit to expand our BMB material to the apparel sector,” added Frank Reil, head of marketing, new business development and sustainability polyamides at BASF. “Together we will create innovative new products that substantially improve the textile and apparel industry and reduce environmental footprint.”