In the dynamic and global textile fiber industry with its various manufacturing processes and end-uses, news and information is breaking on a daily basis. International Fiber Journal is tracking stories relevant to our industry from manmade to natural to bio-based fibers, innovations in nonwoven, woven, braided and technical textiles, technologies for additives, bonding, coatings and polymers, and applications from apparel to hygiene to transportation, and more. Here we will post news stories relevant to textile fibers and their downstream applications on an ongoing basis. Please check back for regular updates. If you have news that you feel should be added to this summary report, please email it to Ken Norberg at ken@ifj.com.
Most recent update: May 20, 2022
EU investigating release of microplastics from geotextiles
The International Geosynthetics Society (IGS) is calling on the European Commission (EC) to fully understand the enormous sustainability benefits of geosynthetics when considering how to reduce microplastics in the environment. How responsible geosynthetics are for the release of microplastics is a question the EC is currently seeking to answer, in an impact assessment study that could have major implications for the sector in coming years.
The IGS on May 17, submitted its response to a European Commission public consultation on microplastics. It calls on the Commission to ensure that this important issue is addressed using the best available scientific data and case studies. The IGS also calls on the Commission to fully consider the entire lifecycle benefits of all products that use synthetic materials in their manufacture. It is inappropriate to compare single-use consumer plastics, which decompose rapidly and are often disposed of irresponsibly, with high-quality durable engineering products that deliver long-lasting benefits to entire communities. Geosynthetics present a negligible environmental risk, and where risk exists at all, it is a rare occurrence within the highly regulated disciplines of civil and environmental engineering. Potential examples such as the use of incorrectly specified products or misguided installation and maintenance practices are addressed through high technical and professional standards in the industry.
Source: IGS
Fiber Industries hires its first Chief Sustainability Officer
Fiber Industries, a leading US fiber manufacturer known for cutting-edge and innovative market leading solutions for the fabric, garment, and fashion industry announced that George Bandy, Jr. has joined the organization as its Chief Sustainability Officer. Bandy has more than 25 years of experience in the sustainability field. His expertise will help Fiber Industries reach its short-term and long-term sustainability goals.
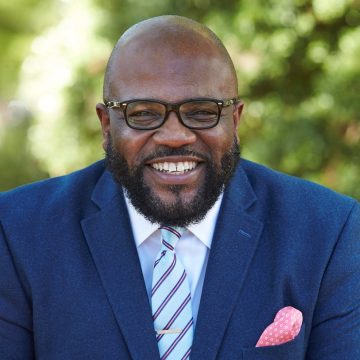
“George is a seasoned sustainability leader who will bring a wealth of knowledge and valuable industry relationships to Fiber Industries,” said Don Bockoven, CEO of Fiber Industries. “Our company has made significant strides over the last few years by embracing new ideas and leading the quality fiber industry in transparent manufacturing. We are confident George will be a key player in our sustainability journey and bring a fresh perspective to our approach. We are incredibly proud to have him join the team.”
Prior to joining the Fiber Industries team, Bandy served as Amazon’s Head of Circular Economy. He formerly served as Chairman of the U.S. Green Building Council (USGBC) and board member of Second Nature. He is currently a board member for Green Business Certification Inc., the International Interior Design Association and Trane Technologies Advisory Council for Sustainability. Bandy is a sought-after expert in a number of areas including business, social and supply chain sustainability, as well as innovative and biophilic design.
Source: Fiber Industries
Indorama Ventures achieves a record 1Q22 performance as the global economy continues to recover
Indorama Ventures Public Company Limited (IVL), a global sustainable chemical producer, reported a strong 1Q22 result, building on its record FY 2021 performance as the pandemic continued to retreat, driving demand across the company’s global integrated portfolio.
IVL achieved 1Q22 Core EBITDA of US$650 million, up 41% QoQ and 77% YoY, and a 4% increase in production volumes to 3.80 MMT. All three of IVL’s business segments grew as the company’s leading global position benefited overall in an environment of higher crude oil prices, increased ocean freight rates and a strengthening US dollar, led by resurging consumer demand and global mobility.
IVL’s Integrated Oxides and Derivatives (IOD) business benefits from a high crude oil price environment, as its shale gas advantage supports MTBE and MEG margins. As ocean freight rates increase, IVL’s PET and Fibers segments gained due to increased import parity pricing in Western markets, where about two thirds of its portfolio is situated. Management’s agile response to hedging and levying surcharges has helped to partially recuperate the surge in energy and utility costs in Europe as a consequence of the Russia-Ukraine conflict.
Combined PET segment reported Core EBITDA of US$435 million, up 63% QoQ and 67% YoY supported by the reset of PTA/PET contracts at the end of 2021. IVL expects the tight supply-demand environment to continue through 2022, boosted by the upcoming peak summer season.
IOD segment achieved Core EBITDA of US$126 million, up 3% QoQ and 258% YoY as MTBE margins benefited from higher crude oil prices, demand remains strong for downstream products, and as the commissioning of the Lake Charles cracker contributes to earnings in 2022. The integration of the Oxiteno acquisition, completed in April, will bring additional upside to IOD from 2Q22.
Fiber segment delivered Core EBITDA of US$85 million, an increase of 4% QoQ and 17% YoY. Demand across the three Fibers verticals is stable with domestic sales yielding better profitability, while higher freight rates weighed on margins on export volumes from Thailand, Indonesia and India, and increased energy and utility costs impacted European operations.
Source: Indorama
INDA announces three finalists for the World of Wipes Innovation Award
Sustainable products that solve problems are the themes for this year’s finalists for the World of Wipes Innovation Award® that will be presented at the 16th annual World of Wipes® International Conference, June 27-30, at the Marriott Marquis in Chicago, Illinois.
The three products vying for the prestigious award are an all-natural substitute for plastic fibers from Bast Fibre Technologies, a dual-textured 3D cleaning wipe from Fitesa and an environmentally safe flushable wipe from Nice-Pak. INDA’s Technical Advisory Board selected the finalists from nearly 20 submissions based on their creativity, novelty, uniqueness, technical sophistication within the entire nonwovens wipes value chain and expansion of nonwovens use. Participants at the 2022 World of Wipes (WOW) International Conference will have the opportunity to help select the winner following presentations by company representatives on June 28. The winner will be announced on June 30 at 11 a.m.
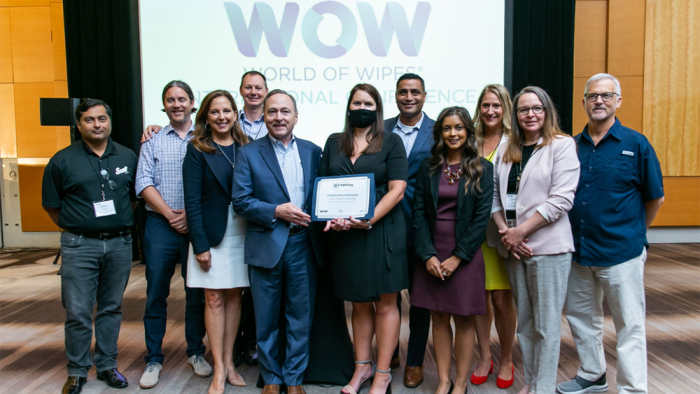
Kimberly-Clark Scott® 24-Hour Sanitizing Wipes was the recipient of the 2021 World of Wipes Innovation Award®.
This year’s in-person WOW International Conference is expected to draw 400-plus senior-level wipes professionals from all wipes segments, repeating last year’s strong live event that welcomed 475 wipes professionals from 14 countries to Atlanta, GA.
The three companies vying for the award (in alphabetical order) are:
- Bast Fibre Technologies – Sero® Hemp Fibers
- Fitesa – Dual Textured 3D Wipe
- Nice ’N CLEAN® SecureFLUSHTM Technology Flushable Wipes by Nice-Pak
Source: World of Wipes
Kaiser, Dystar develop waterless process for denim fades
Turkish laundry solutions provider Kaiser and German chemical supplier DyStar have collaborated on an innovation that achieves the sought-after lived-in look with a smaller environmental footprint. “Advanced Used Look” offers the denim industry a solution for authentic fades without all of the water and chemical usage often associated with conventional dye and wash methods. The energy- and time-saving process is waterless and free of potassium permanganate, a hazardous chemical linked to respiratory diseases like byssinosis and silicosis. The companies reported that, compared to traditional garment dyeing and washing, the solution provides higher fastness—or ease of fading—and exceptional reproducibility and levelness for scale. It’s also able to achieve the faded look on challenging darker colors.
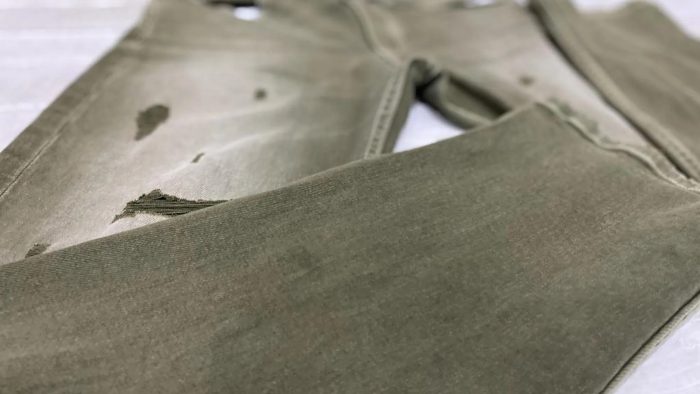
The denim industry is looking for environmentally friendlier solutions for garment fading. As part of its Aqualess Mission, a combination of technologies that allows garment laundry processes to use 75 percent less water, chemical specialist Officina +39 recently introduced Aqualess Fade. The technology recreates the bleaching effect of chlorine on fabrics without water and high temperatures. In November, vertically integrated denim manufacturer Soorty developed Zero Stone, a stonewashing method that produces vintage-inspired wash effects without the use of pumice stones, which have long been considered a detriment to the environment.
Source: Kaiser
Freudenberg experts meet sustainability
Following their merger, Freudenberg Performance Materials, Low & Bonar, Mehler Texnologies® and Filc will be presenting their innovative solutions at a joint stand for the first time at this year’s techtextil exhibition in Frankfurt, Germany. The focus is on sustainability. Among the highlights are Evolon® RE, a microfilament textile for a wide variety of applications and markets, FILFLEX, a sustainable padding material for car seat covers, and the truck tarpaulin POLYMAR® 8556 ECO CF. Customers will find the world’s leading manufacturer of technical textiles at Stand C51 in Hall 12.1.
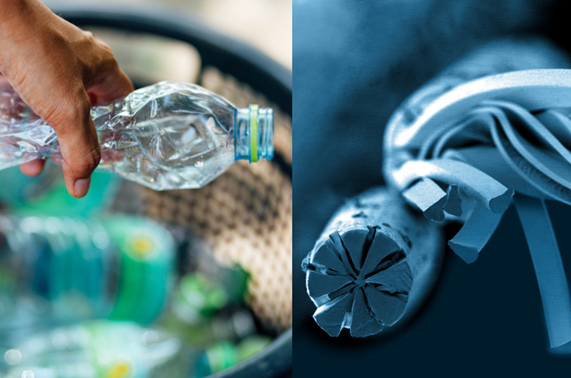
With Evolon® RE, Freudenberg Performance Materials is presenting an even more sustainable version of its high-performance microfilament textiles. Evolon® RE is manufactured from an average of 70% recycled polyester, which the company makes by cycling post-consumer PET bottles in-house. Evolon® RE products are available for various applications such as technical packaging, in weights currently ranging from 80g/sqm to 300g/sqm. For high-tech wiping, lightweight Evolon® RE is now available starting from 30g/sqm. The material meets the needs of cleaning specialists for more sustainable wiping solutions. Evolon® RE offers the same high quality and material performance as all other Evolon® textiles.
When it comes to tarpaulins on trucks, both protection of the transport cargo and advertising for the transport company place high demands on the material. Mehler Texnologies® tarpaulin material ranks among the premium products for truck tarpaulins. The company is a pioneer in sustainable development and is showcasing POLYMAR® 8556 ECO CF. This unique material has a 25% share of recycled raw materials in the coating mass. In addition, the material is made with 100% R-PES yarns. The input materials undergo a complex separation and filtering process.
FILFLEX is a soft and flexible padding layer made from nonwovens for automotive and furniture seat covers. It prevents leather from creasing and improves the dimensional stability of the seat covers. In terms of sustainability, its benefit is its 100% PET composition, making FILFLEX easy to recycle. FILFLEX offers customers easier handling during sewing and the seat covering process. End users benefit from the high seating comfort.
Source: FreudenbergPM
RadiciGroup closes 2021 with positive results
With total sales of EUR 1.508 million generated by over 30 production and sales units in Europe, Asia and America, RadiciGroup closed its 2021 financial year with positive results, despite the difficulties due to the lingering effects of the pandemic and the steep increase in the cost of raw materials and energy, especially during the latter part of the year.
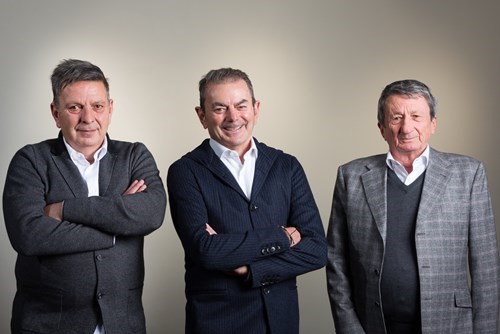
The Group – led by brothers Angelo, Maurizio and Paolo Radici – continued to pursue its strategy of focusing on the core businesses considered to be strategic and synergistic, such as nylon chemicals, engineering polymers and advanced textile solutions, while, at the same time, introducing new products, such as a line of personal protective equipment for medical and industrial use.
EBITDA reached EUR 268 million, and net income for the year was EUR 150 million.
Source: RadiciGroup
MAAG Group acquires AMN DPI
MAAG Group has acquired the French tool manufacturer AMN DPI (AMN) effective May 02, 2022. Maag is thus consistently continuing its path as an integrated supplier for systems in the plastics industry from extruder tip.
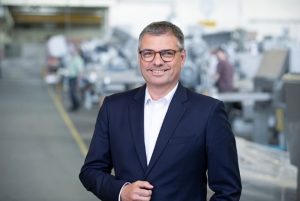
Founded in 1979 and based in Normandy, AMN, a developer and manufacturer of polymer pelletizing dies and die plates, brings a wide range of know-how to the MAAG Group for both the processing and the extrusion and recycling industries. The globally positioned company with expertise also in biodegradable, highly filled recycling materials concentrates its activities primarily on the European market.
“For us, the acquisition is a consistent further step towards even greater customer centricity. Toolmaking for granulators and systems can now be carried out completely in-house. This increases the availability and delivery reliability of Maag products, and production times are reduced,” said Ueli Thürig, president of the MAAG Group.
AMN’s die plate production also increases Maag’s service thanks to increased support options for continuous operation at the customer’s site.
Source: MAAG
James Heal promotes Neil Pryke to Managing Director
Having been part of the James Heal team for over 25 years, Neil Pryke has been promoted to the position of Managing Director of PPT Group UK, a role in which will cover not only James Heal, but also partner brand Mecmesin located in West Sussex. An engineering company based in historic textile mills in Halifax, James Heal design and manufacture a comprehensive range of state-of-the-art textiles testing solutions, with 80% of their products being exported around the world.
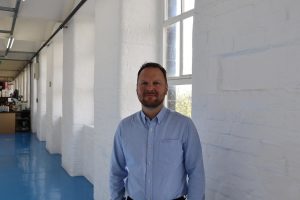
Having joined the company’s Innovation department as a Mechanical Design Engineer, Neil worked his way up to become Operations and Innovation Director, and Manager of the Halifax site. He was a major player in setting up and developing manufacturing facilities and operations in Halifax, and the creation and development of instruments such as the best-selling Titan CRE tensile tester. Vitally to the company’s continued success, Neil was instrumental in developing the James Heal brand, working with the Design Council in 2011. Together they created the most visually appealing product range, with a focus on user-centred design, quickly setting James Heal on a course to become market leader.
Established in 1872, James Heal is celebrating its 150th anniversary this year and is a globally known brand in the textiles industry.
Source: JamesHeal.com
Aurora Specialty Textiles Group wins awards for operations excellence and social responsibility
For the third year in a row, Aurora Specialty Textiles Group has won awards for outstanding business and manufacturing practices from the Valley Industrial Association (VIA), which represents the manufacturing industry in the Fox Valley region of Illinois, a large industrial hub outside Chicago and a major Midwest manufacturing region.
This includes winning the association’s award for Operations Excellence for the third year in a row. VIA’s Excellence in Operations Award recognizes leadership in operational strategic planning and implementation, as well as continuous improvement and employee engagement.
Aurora also won the award for Social Responsibility, which reflects a company’s continual improvements and contributions in the areas of sustainability and corporate social responsibility. Aurora was a finalist for this award in 2021.
The awards were announced April 27, 2022, at the annual VIA Spark Awards Benchmarking for Excellence celebration.
Since the founding of VIA in 1902, the organization has grown from 16 to more than 200 members and Aurora was a founding member company. The VIA gives area manufacturers a place to connect for professional growth and share information and common resources that can help operations and support the wider regional manufacturing industry.
Aurora Specialty Textiles Group, Inc. is a global leader in coating, dyeing, and finishing of woven non-woven and knit fabrics.
Source: Aurora Specialty Textiles Group
Lenzing rides out significant cost pressure to report solid first quarter
Lenzing Group was affected by rising costs and the extreme developments on the global energy and raw material markets. Lenzing was nevertheless again able to increase sales in this period compared to Q1/2021, reaching a plus of 25.7% to €615 million.
This was primarily due to continued high demand for wood-based biodegradable specialty fibers and higher fiber prices. Specialty fibers’ share of fiber revenue currently stands at 73.3%. The earnings trend reflects trends in energy, raw materials and logistics costs, although the company’s continued focus on measures to improve structural earnings in all regions mitigated this negative effect. EBITDA decreased by 7% year-on-year to €88 million. The EBITDA margin reduced from 19.3 to 14.3%.
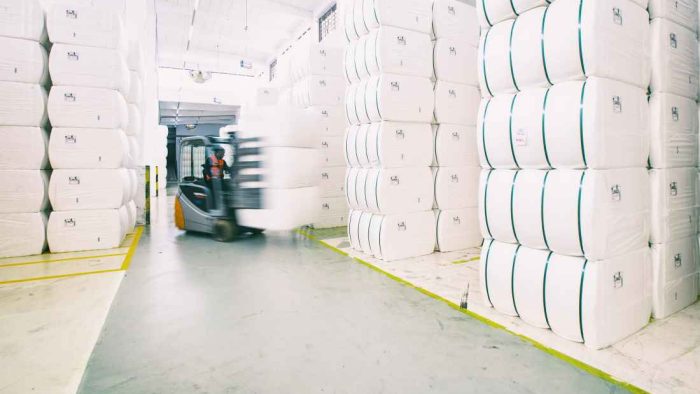
In March, Lenzing AG, Lenzing/Austria was able to start up a new, state-of-the-art lyocell plant in Thailand. The production plant, which is the largest of its kind with a nominal capacity of 100,000 tons/year, went on stream on schedule after 2,5 years of construction and despite the pandemic-related challenges. The capacity expansion will enable Lenzing to better meet growing customer demand for lyocell fibers.
Lenzing’s goal is for more than 75% of fiber sales to be generated from the business with wood-based, biodegradable specialty fibers of the Tencel, Lenzing Ecovero and Veocel brands by 2024. With the opening of the lyocell plant in Thailand and the investments in the existing production sites in China and Indonesia, the company will increase its share of specialty fibers in fiber sales to well above the targeted 75% already by 2023.
The implementation of the pulp project in Brazil secures the Group’s own supply of dissolving wood pulp and thereby also strengthens specialty fiber growth in line with the corporate strategy sCore TEN.
With the implementation of the 2 key projects in Brazil and Thailand, as well as with the investments at the existing Asian sites in China and Indonesia amounting to more than €200 million, Lenzing continues to push forward Group-wide climate neutrality. In 2019, the company became the first fiber manufacturer to set a target to reduce its carbon emissions by 50% by 2030 and to become climate neutral by 2050. This carbon reduction target has been confirmed by the Science Based Targets Initiative.
Source: Lenzing
Anne Dierkopf strengthens management at Kiefel
KIEFEL GmbH, a market leader company for thermoforming and joining technology for plastics and natural fibers, has a new member on the management board. Anne Dierkopf took over the role of CFO at Kiefel on May 1st, 2022. She replaces Richard Schmidhofer, who filled the position on an interim basis for around a year.
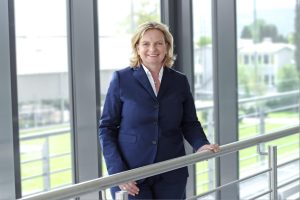
Anne Dierkopf thus completes the management board with CEO Thomas Halletz and CTO Stefan Moll. She is responsible for the areas of finance, purchasing and IT. Her tasks will focus, among other things, on securing the supply chain and finalizing the deployment of SAP S/4HANA. In addition, she will continue to drive forward the organizational and systemic development of the company during high growth.
Source: KIEFEL
Kraig Biocraft Laboratories strengthens Q2 Spider Silk production expansion
Kraig Biocraft Laboratories, Inc., the biotechnology company focused on the development and commercialization of spider silk, announced that it has strengthened its second-quarter production expansion with a new vendor quality assurance program. This new program will allow the Company to screen numerous mulberry suppliers and grow its database of trusted vendors.
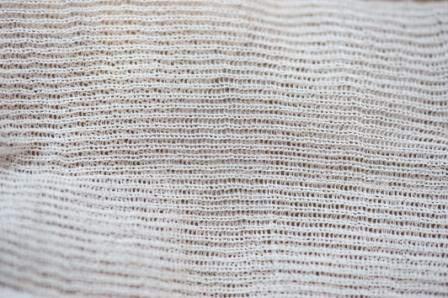
This new vendor verification program was put in place to address the Company’s growing demand for high-quality mulberry as a feedstock for its expanding production of recombinant spider silk. As the primary raw input for the Company’s spider silk production, growing its supply base of verified mulberry producers is a crucial component for the continued production expansion.
Equipment and processes refined in the first quarter have positioned the Company to focus nearly all of this quarter’s operations on finished yarn production. 85% of all silkworms produced this month are slated for spinning and use in finished fabrics and garments. These materials will be dedicated to the Company’s joint venture apparel brand, Spydasilk™. The remaining 15% of production will be devoted to the Company’s regenerative breeding program and growing the production base for the third quarter and beyond.
The relationship between nutrition and high-quality silk production cannot be overstated. Nutritional management is one the most important factors in maintaining optimal colony productivity and wellbeing. This new vendor verification process will play an essential role as the Company looks to the future and outgrowing its existing production footprint and supplier base.
Source: www.KraigLabs.com
Savings in CO2 emissions
Textile fibers are estimated to be the single largest contributor of greenhouse gas (GHG) emissions in the fashion industry. A new assessment for Spinnova’s first commercial factory reveals that the company has a positive climate impact: the Spinnova branded fiber saves 6.5 kg CO2e (CO2-equivalent) when replacing conventional cotton.
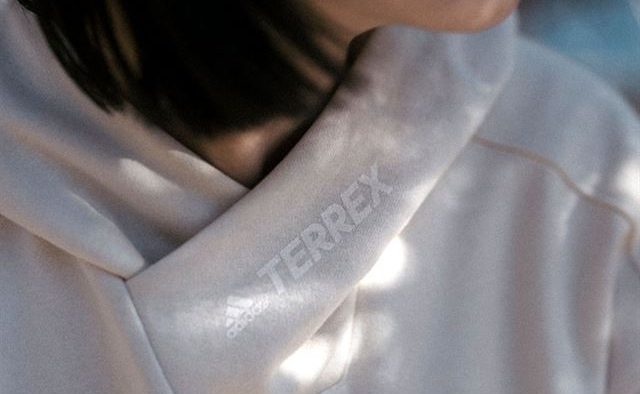
Spinnova Oy, Jyväskylä/Finland, has now verified its climate impact with an expert assessment with the help of an external climate business consultancy. Their assessment shows that Spinnova’s carbon footprint is 1.28 kg CO2e/kg fiber which is 72% lower compared to conventional cotton (4.6 kg CO2e/kg fiber).
Spinnova’s low-emission technology includes use of CO2-free energy and smart energy systems. The factory only uses wind power and heat recovered from its own process as its energy sources. The surplus energy recovered from the company’s process with heat pumps is recycled into the local district heating network, reducing the local energy provider’s emissions by replacing energy sources such as peat.
When replacing conventional cotton with Spinnova, fashion brands can save 6.5 kg CO2e/kg of fiber produced. This positive climate impact is called the carbon handprint, and it compares the climate impact of 2 products intended for the same use.
Source: Spinnova
Avient to acquire DSM Protective Material business
Avient, a provider of specialized and sustainable material solutions, has entered into an agreement with Royal DSM NV, Netherlands, to purchase the DSM Protective Materials business (including the Dyneema brand) for US$1.485 billion. In conjunction with this proposed acquisition, Avient Corp., Avon Lake, Ohio, USA, has also announced that it plans to explore sale options for its Avient Distribution business.
The foundation of the protective materials business of DSM is the renowned technology brand Dyneema. The ultra-high molecular weight polyethylene (UHMWPE) specialty fiber is 15 times stronger than steel and is used in demanding applications such as ballistic personal protection, marine and sustainable infrastructure, renewable energy, industrial protection and outdoor sports. Estimated sales and EBITDA for the Dyneema business in 2022 are approx. $415 million and $130 million, respectively. The business includes 6 production facilities, 4 R&D centers and approx. 1,000 employees located around the world.
Avient’s composites platform with the Dyneema business will represent over 50% of the company’s Specialty Engineered Materials segment sales.
Source: Avient