CuRe Technology (Emmen, The Netherlands) Garbo Srl (Cerano, Italy), gr3n (Chiasso, Switzerland), and PerPETual (Remscheid, Germany), are companies all involved in developing new processes for chemically recycling PET polyester for fabric and garment production.
Their processes all involve various depolymerization techniques to break down the polymers of waste PET into useful chemicals.
With the aim of validating and scaling up these four promising technologies, Amsterdam-based Fashion for Good has just launched the 18-month “Full Circle Textiles Project – Polyester” to encourage their financing and secure offtake commitments from the fashion industry.
The project brings together a consortium of brands, innovators, supply chain partners and catalytic funders – a structure that has already proven successful in driving and scaling disruptive innovation in the industry. Project partners include catalytic funder Laudes Foundation, brand partners adidas, Bestseller, C&A, PVH Corp., Target and Zalando, and affiliate partners Arvind, WL Gore and Teijin Frontier.
Polyester claims 52% of the global fiber market, and as the most common fiber in the world, also represents a significant portion of the 73% of textiles that are landfilled or incinerated annually. It does not naturally break down in the environment and the production of virgin fibers also perpetuates reliance on fossil fuels. Chemical recycling is a key solution that promises to address the polyester textile waste challenge.
CuRe Technology
CuRe Technology is focused specifically on the recovery of feedstocks from colored and contaminated packaging, bottles, food trays, carpets and strappings that are usually discarded.
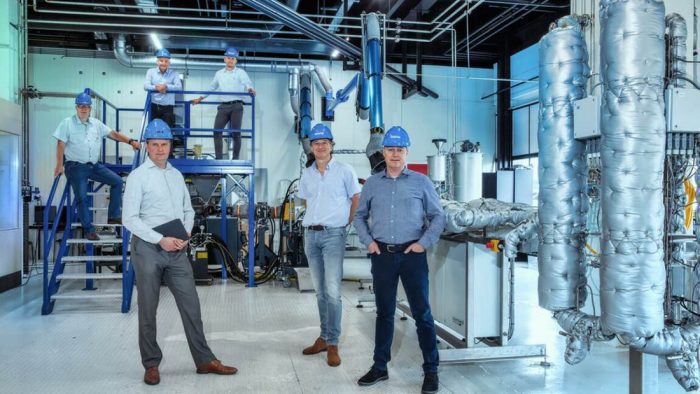
Its end-to-end partial depolymerization recycling process transforms opaque and difficult-to-recycle, food-grade PET to recycled PET (rPET) that can be used again for food and drinks packaging in a single continuous process at its site.
Garbo Srl
A chemical recycling process called ChemPET, which is also able to treat most of the PET-based waste that is currently not recoverable, has also been developed by Garbo Srl. Through a chemical reaction, the PET is transformed into an intermediate product called BHET (bis-hydroxy-ethylene-terephthalate) which, properly purified, can be used again for the production of both bottles and fibers.
The company has partnered with Chemtex Corporation to build a commercial-scale PET recovery plant in Italy capable of handling multi-material thermoforming scraps and multi-layer trays based on PET polyethylene and EVOH (ethylene-vinyl alcohol copolymer), as well as those containing aluminum or fillers such as TiO2, CaCo3 and Silica, colored PET powders and fines, black PET trays and PET/PP strapping.
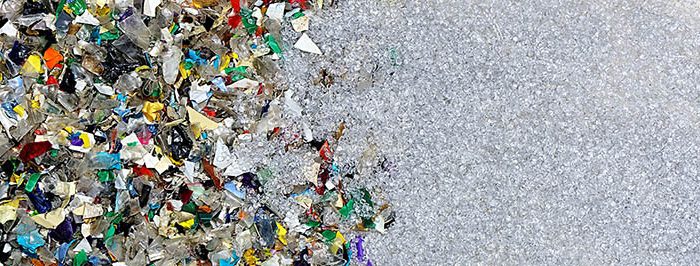
Gr3n
Gr3n raised €7.5 million in funding during 2021 to further develop its technology for breaking down any type of PET and polyester plastic to allow for potentially endless recycling loops.
Its depolymerization process is achieved through a microwave-assisted alkaline hydrolysis, which makes the reaction time – less than 10 minutes – much faster than usual. The process can be repeated an unlimited number of times, without any degradation or side effects, the company says, because it is practically “erasing” the history of the polymer and of its physical and chemical properties. The Gr3n process also enables the removal of impurities like dyes and colorants, leading to perfectly clear recycled PET.
The reaction output is a mixture of building block derivatives, which are then isolated and purified. Often the most critical part in a chemical reaction is not obtaining a product but obtaining it in as pure a state as possible, to avoid potential side effects in any of its further uses, the company says.
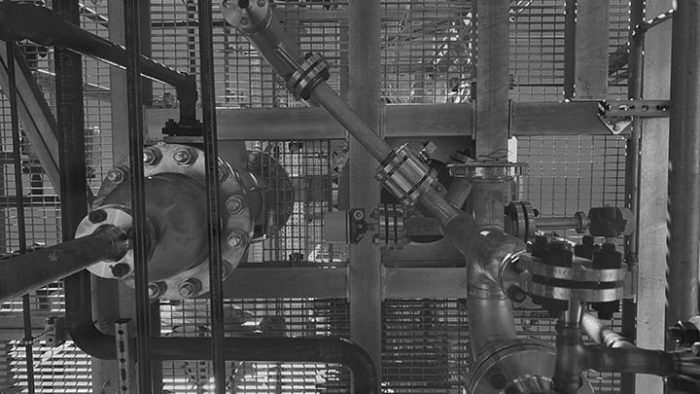
PerPETual
Similarly, the PerPETual process depolymerizes used plastic PET bottles into sustainable esters (monomers), using a low temperature process and MEG (mono-ethylene glycol) as the chemical solvent.
Since MEG is one of the two components of PET, there are no chemicals that are foreign or toxic to polyester to be concerned about in the PerPETual process.
The pool of sustainable esters are then subjected to proprietary micron-level filtration with customized filter media to remove all contaminants ready to be reformed into long repetitive chains, using the same equipment and comparable process conditions as would be used for conventional petrochemicals.
PerPETual, which was established back in 2006, is currently already converting over two million PET bottles a day into high-quality filament yarns. In 2008, it acquired a majority stake in Polygenta, an India-based company, which was retrofitted to use the PerPETual technology and expanded in 2019. Plans are underway to further increase the capacity of the plant in 2022.
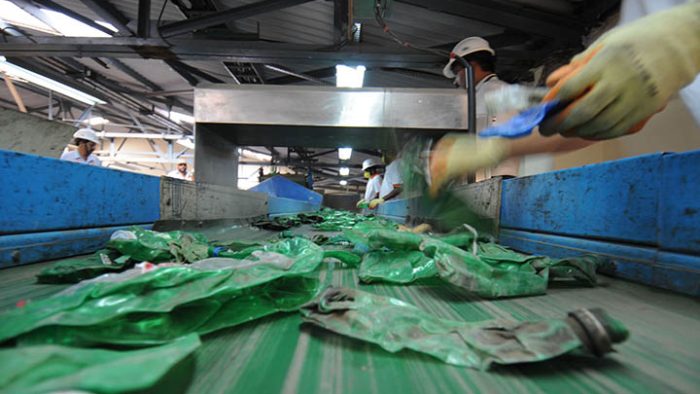
Cellulosics
The new Fashion for Good project complements the ongoing “Full Circle Textiles Project,” launched in September 2020, which is focused on economically viable and scalable solutions for cellulosic chemical recycling and producing new man-made cellulosic fibers and fabrics from cotton and cotton-blend textile waste.
The four selected innovators for the first project – Circ, Evrnu, Infinited Fiber Company and Renewcell – have all been able to validate their technologies and produce garments for brand partners to their quality specifications. The next phase of this project is focused on scaling these solutions and encouraging brands, innovators and supply chain partners to collaborate in creating long-term partnerships.
All the gold that’s ever been sourced is still in circulation – it gets melted and casted over and over again. That’s our goal for textile fibers.
CIRC
In August 2021, CIRC, based in Danville, Virginia, announced a partnership with Austria-headquartered technology group Andritz to bring its patented textile recycling technology to commercial scale.
CIRC’s technology is capable of separating and recovering mixed polymer streams – specifically any blend of polyester and cotton, which accounts for most fabrics manufactured.
“CIRC’s technology is positioned to capture a significant portion of the global circular textile market, and Andritz can enable that success with our expansive engineering and equipment capabilities,” said Jorma Latva-Kokko, vice president of mechanical pulping at Andritz.
Infinited
At the end of December 2020, Andritz also signed a cooperation agreement to develop the process and equipment solutions for Infinited Fiber Company’s textile fiber regeneration technology.
Infinited’s technology can turn any cellulose-rich raw material, including discarded textiles, used cardboard or rice or wheat straw, into cellulose carbamate fibers – unique, high-quality textile fibers with the look and feel of cotton, according to the company.
In April 2021 Infinited announced plans to build a €220 million plant in Finland to be operational by 2024. The company currently operates pilot facilities in the cities of Espoo and Valkeakoski in Finland, with a combined nominal capacity of 150 metric tons per annum. The planned flagship factory will have an annual capacity of 30,000 metric tons per year and will use textile waste as feedstock.
In July the company then announced €30 million in new financing, with brands adidas, Bestseller and H&M, and viscose producer Sateri among the new investors.
Evrnu
In November 2021, Evrnu, based in Seattle, Washington, raised $15 million in Series B financing to scale and meet the demand for its NuCycl fiber regeneration platform.
The financing will be used to expand Evrnu’s operations in South Carolina and bring high volumes of NuCycl fibers to the fashion industry.
Having developed technologies to address the recycling of over 90% of all apparel, with one patent granted and several others pending, Evrnu says it is on course to deploy technologies that allow for all textiles to be successfully recycled by 2030.
“All the gold that’s ever been sourced is still in circulation – it gets melted and casted over and over again,” says Christopher Stanev, CTO of Evrnu. “That’s our goal for textile fibers – our technologies enable them to stay in circulation, while maintaining their performance attributes.”
Evrnu has advanced R&D contracts under way in fashion, as well as in other markets, such as home furnishings and automotive.
Renewcell
The textile recycling technology of Renewcell transforms a high cellulosic portion fabric into a high-quality recycled dissolving pulp, branded as Circulose. The process does not require any harmful chemicals and the pulp can be fed into the commercial textile production chain. Commercially active at an industrial scale since 2019, the company launched its first product in March 2020.
In an important development in December 2021, Renewcell signed multi-year purchasing agreements with three different European textile sorters — Soex in Germany, Texaid in Switzerland and Sysav in Sweden.
These companies will supply thousands of tons of textile waste each year for recycling at Renewcell’s new facility in Sundsvall in Sweden. The deliveries to Renewcell will consist of clothing and other textiles collected from consumers that it is not possible to sell second-hand.
“The issue of textile waste management is a priority within the EU, and from 2025 onwards, new mandatory requirements for separate collection and preparation for textile waste recycling will apply to all member states,” said Martin Stenfors, COO at Renewcell. “We continue to build a strong regional supplier network for textile waste fractions that are suitable for recycling with us.”
Galvanized consortiums
“Textile recycling is a key focus for Fashion for Good,” said the organization’s managing director Katrin Ley. “With the success of the first Full Circle Textiles Project, and proof that a galvanized consortium of stakeholders from across the industry can truly shift the needle, we can now turn our attention to applying these learnings and steps to scale to another critical area – textile-to-textile polyester recycling.”