In the dynamic and global textile fiber industry with its various manufacturing processes and end-uses, news and information is breaking on a daily basis. International Fiber Journal is tracking stories relevant to our industry from manmade to natural to bio-based fibers, innovations in nonwoven, woven, braided and technical textiles, technologies for additives, bonding, coatings and polymers, and applications from apparel to hygiene to transportation, and more. Here we will post news stories relevant to textile fibers and their downstream applications on an ongoing basis. Please check back for regular updates. If you have news that you feel should be added to this summary report, please email it to Matt Migliore at mmigliore@inda.media.
Most recent update: December 29, 2021
Freudenberg to increase prices for nonwoven flooring and filtration materials in EMEA
Freudenberg Performance Materials announced a general upward adjustment of its prices for nonwoven performance materials for flooring and filtration applications in EMEA. This revision, effective January 1, 2022, has become necessary because of sustained and unprecedented surge in cost for raw materials, packaging, freight, consumables and energy combined with disruptions in our inbound supply chain.
Prices across all categories have by far outpaced expectations and are forecasted to remain on high levels throughout 2022, according to Freudenberg.
At this stage, Freudenberg said its business can no longer absorb the effects of such high price levels, and it will therefore adjust prices for all our Colback and Lutradur-branded nonwoven products for flooring and filtration applications by double-digit increases, depending on product types.
Freudenberg said it will continue to work hard on improving productivity to offset inflationary pressure to keep attractive price levels and to avoid further price adjustments. Freudenberg said it will continue to monitor the market development and in case of sustained and unexpected downward trends will readjust prices accordingly.
Source: freudenberg-pm.com
AATCC announces Student Chapter Faculty Advisor Award winner
In recognition of her active leadership, participation and support of the AATCC Student Chapter at Thomas Jefferson University, Janet Brady was named this year’s recipient of the AATCC Student Chapter Faculty Advisory Award. Brady became a member of AATCC while a student at the Fashion Institute of Technology in 1975. She has been an advisor with the AATCC Student Chapter at Thomas Jefferson University since 1996.
Brady received an AAS in Textile Technology from the Fashion Institute of Technology in 1977, where she graduated cum laude. She completed a BS in Textile Technology from Philadelphia College of Textiles and Sciences in 1979 and an MS in Textile Engineering from Philadelphia University in 1999.
Brady went to work for Crown Textile Company as a textile technologist from 1979 to 1981. In 1981, she joined Philadelphia University as supervisor of the Grundy Materials Evaluation Laboratory and in 1986, became an adjunct instructor. While an adjunct instructor, she also served as an instructor of the Textile Testing Training Program and developed and taught or co-taught onsite textile testing training programs nationally internationally (2000-2002). In 2002, Brady became an Assistant Professor in the School of Engineering and Textiles at Philadelphia University. From 2004 through 2012, she served as a Leader of Materials Evaluation with the Laboratory for Engineering Human Protection (LEHP) and as a member of the LEHP Garment and Comfort Teams. In 2005, she became program coordinator of Textile Engineering Technology. In 2008, Brady was promoted to Associate Professor at the School of Design & Engineering at Philadelphia University.
From 2014 through 2015, Brady was the lead investigator of the Warrior Web Research Project, a DARPA-funded project to develop an exoskeleton supporting pack weight for soldiers (a subcontractor to the University of Delaware). In 2015, she became Faculty Director of Grundy Materials Evaluation Laboratory. In July 2017, Philadelphia University joined with Thomas Jefferson University. That same year, Brady was promoted to Associate Professor in the School of Design & Engineering at the Kanbar College of Design, Engineering, & Commerce, Thomas Jefferson University. In 2020, she became Faculty Director of the Bruner Materials Characterization Laboratory at Thomas Jefferson University.
Throughout her academic career, Brady has taught students in laboratory settings and classrooms. She has supervised graduate research and served as a graduate thesis committee chair and committee member for Textile Engineering MS students. She also assisted all MSTE and Ph.D. students in utilizing Grundy Laboratory and served as an upper-level academic adviser to students majoring in Textile Materials Technology
Brady is the recipient of the 2020 Thomas Jefferson University Award for Outstanding Teaching. She has published peer-reviewed papers and made several presentations, including at AATCC conferences and symposia. She is a member of the AATCC Delaware Valley Section and serves on its scholarship committee (2014 – present); she also served as past chair of the Delaware Valley Section (2008 – 2014).
The Association presented the AATCC Student Chapter Faculty Advisor Award to Brady during the AATCC Textile Discovery Summit Awards Luncheon held on Thursday, November 18 at the Sheraton Imperial Hotel, Durham, NC.
Source: aatcc.org
Kelheim Fibres calls for government action in the face of spiking natural gas costs
Kelheim Fibres is calling on the German government to take immediate steps to mitigate the impact of the cost increases for natural gas and is committed to work to implement alternative sources of energy in the medium term.
Over the past 14 days, the wholesale cost of natural gas in Germany has risen by more than 50%. This increase presents an extraordinary challenge for industry, and there is no sign of support or intervention from the government, according to Kelheim, which predicts the the situation is likely to worsen without action.
Kelheim Fibres is entirely dependent on natural gas for the generation of electrical energy and steam and has no viable short-term alternatives. In addition, the raw materials used by the company often consume high levels of energy in their production and are also increasing significantly in cost. These increases in cost jeopardize the future of the business if they cannot be passed on though the supply chain.
In parallel, the disruption to global logistic networks that has been seen throughout 2021 is now expected to continue throughout 2022. Massive increases in shipping rates – in some cases in excess of 80% – are being imposed without notice and with no opportunity for negotiation. These costs must also be passed on though the supply chain if businesses are to remain viable.
- To address these issues, Kelheim Fibres is implementing the following measures with immediate effect:
- The increased cost of energy and freight will be passed on in prices to customers at the soonest opportunity;
- If necessary, changes or adjustments to existing agreements will be negotiated to reflect the increased cost levels;
- If the necessary increase in fibre prices cannot be secured, cuts to production will be implemented with the objective of minimising losses until the cost increases can be mitigated.
As the drivers for the increases in natural gas prices appear to be temporary in nature, Kelheim said it will maintain any price adjustments under review and pass on any relief to customers.
Craig Barker, CEO of Kelheim Fibres, described the current situation as critical. “The cost increases we are facing are unprecedented and call for swift and decisive action. We are determined to take the necessary steps to preserve the future of our business and provide security of supply for our customers. At the same time, we are relying on the support of our customers to help us conquer the challenges our business is facing.”
Source: kelheim-fibres.com
Respin pilot line for circular leather fiber ready for startup
Respin, the joint venture between the sustainable textile material company Spinnova and ECCO’s leather partner KT Trading, has finished building a pilot production line. Respin can now begin working towards commercializing the disruptively circular Spinnova leather waste fiber.
Following the announcement of establishing Respin, a joint venture between Spinnova and KT Trading, in May, the partners now have a pilot production line ready to begin its startup phase. The small industrial scale leather fiber pilot is designed and built by Spinnova, and located in Spinnova’s facilities in Jyväskylä, Finland.
This means that Respin can start producing larger amounts of the leather fiber for R&D purposes and develop demo products with the material. While the piloting phase is exclusive, Respin joint venture partners will welcome other brands to join the development in its commercial phase. The fiber made of side streams of ECCO’s leather tanneries has great potential in many applications, including footwear.
Setting up a pilot line for leather fiber did not require further technology development from Spinnova. The technology has already been verified in Spinnova’s pilot production line that has been running for 2.5 years using wood-based fiber.
Respin will pay 2.5 million euros to Spinnova for the pilot production line and Spinnova’s R&D services in the course of the proof-of-concept phase. The piloting is estimated to take one year.
Source: spinnovagroup.com
Asahi Kasei marks 90th anniversary of its Bemberg cupro fiber business with rebranding campaign
Bemberg is the brand name of the world’s only cupro fiber, which is manufactured by Asahi Kasei in Nobeoka, Miyazaki Prefecture, Japan. It is used in various applications, such as linings, ethnic garments, outerwear, and innerwear.
Being made from cotton linter, a by-product of cottonseed oil production, as well as being biodegradable and compostable for circularity, Bemberg is an environmentally friendly material. Although it is an uncommon material, which accounts for only 0.02% of the world’s total fiber production, Asahi Kasei is pursuing value creation and sustainability together with its stakeholders as the only cupro fiber manufacturer. Bemberg senior general manager, Eisaku Maeda pointed out: “In recent years we’ve been collaborating with new stakeholders, and in the future, we will strive for technological innovation that leads to the improvement of environmental performance and benefits to society. Moreover, we will pursue enhanced added value with Bemberg as a one-of-a-kind material in demand throughout the world. “

Cotton linter as the raw material of Bemberg is currently procured from partner oil mills – cottonseed oil production factories – located in India, Brazil, the United States, and Japan.
To clearly convey the ideal and meaning of the Bemberg brand to customers, the brand is being rebranded with a new tagline of “Crafted Elegance.”
Crafted: Japan-made cellulose fiber produced exquisitely
Elegance: Not extravagance, but universal beauty
Moving forward with Bemberg, Asahi Kasei will pursue heightened value creation through technological innovation to improve the environment and provide solutions to social issues, leveraging the status of Bemberg as a one-of-a-kind material.
A new Bemberg website will provide added information on the Bemberg, Crafted Elegance, product line.
See the new Bemberg, Crafted Elegance website: https://www.asahi-kasei.co.jp/fibers/en/bemberg/
Source: asahi-kasei.eu
Fitness label LIVE! launches collection based on Sorona sustainable fiber
Brazilian activewear and fitness label LIVE! has developed a six-piece capsule collection utilizing Sorona fabric.
Each garment in the collection is crafted from Sorona, a partially bio-based polymer derived from eco-efficient processes requiring lower energy consumption. Created from the sugar in corn and fermented in a process similar to the production of alcohol, the Sorona polymer substitutes a formerly chemical process with a bio-based one.
The Sorona fibers provide the textile with greater breathability, reduced pilling and sagging, and dimensional stability that helps maintain shape after multiple wears, ultimately enhancing each products’ lifecycle. The brand has even developed tailored packaging for the capsule made of Sorona fabric to lessen its carbon footprint.
The collection launches December 1st on the brands e-commerce, as well as in LIVE! New York and Miami stores.
Source: liveclothing.com
Archroma relocates headquarters to Basel region
Archroma announced the relocation of its headquarters to Pratteln, Switzerland, just outside Basel, and a customized R&D role for its existing Reinach site.
Archroma’s new Haus der Wirtschaft (HWD) headquarters is located in a business hub that hosts the Economic Chamber Baselland with other companies, as well as a fully serviced conference and event center. The new offices have been designed to support a smooth and efficient collaborative work and visitor experience.
The move comes after a decade of growth at Archroma’s TechCenter building in Reinach, also near Basel, which evolved from being a dedicated technical center to hosting a growing number of corporate services and teams. With the opening of the new HWD headquarters, the Reinach TechCenter, designed to accommodate laboratories and technical expert teams, will return to its roots with focus on the global R&D and application development, supporting those of the Archroma Competence Centers (CC) located in Switzerland: CC Textile Finishing; CC Textile Repellents; CC Paper Coloration; and CC Paper Whiteness.
The transition will take place in December 2021.
Source: archroma.com
INDA announces updated value proposition
The Association of the Nonwoven Fabrics Industry (INDA) updated its value proposition to grow the nonwovens industry and move forward from the business challenges of COVID that impacted the ability to hold in-person events.
“We are excited to move forward with an ambitious yet achievable roadmap for INDA’s vibrant future,” said Chris Astley, INDA Board Chair and Chief Commercial Officer of Glatfelter. “This new plan reflects our intimate knowledge of the new industry expectations and positions INDA to support our members as they continue to overcome disruptions caused by the pandemic, and position themselves to thrive in the new and evolving landscape.
INDA established five key pillars that will guide INDA activities:
- Convene and connect the industry through trade shows and conferences
- Achieve industry relevance among policy makers, end users and other key stakeholders
- Advocate for the Nonwovens Industry in public policy forums
- Deliver market insights for better decision making
- Provide training programs to sustain the industry’s innovative edge
“We enthusiastically embrace the new foundation based on five key pillars that will guide INDA activities,” said Dave Rousse, INDA President. With last month’s announcement of Tony Fragnito joining INDA as Chief Operating Officer, we are ready to implement this plan and take it into the future. I look forward to working with him to drive INDA’s continuous pursuit of excellence in providing ever greater value to our industry and our members.”
Source: inda.org
* International Fiber Journal is owned by INDA, Association of the Nonwoven Fabrics Industry (inda.org).
J. William Weaver Paper of the Year awarded to two papers
Xuehong Ren and co-authors Meng Zhang and Yan Zhang from Jiangnan University, and Tung Shi-Huang from Auburn University were recognized for their paper “Antibacterial Finishing of Vat Dyed Cotton Fabrics with a Reactive N-Halamine” published in the 2020 AATCC Journal of Research. Lian-gang Zheng and co-authors Fujun Xu, Mohamed Amine Aouraghe, Sidra Saleemi, Yanhong Cao and Yiping Qui from Donghua University were recognized for their paper “Mechanical Properties and Failure Analysis of 3D-Woven Copper Wire/Glass Fiber Hybrid Composites” published in the 2020 AATCC Journal of Research. The AATCC Publications Committee presents the J. William Weaver Paper of the Year Award to the author or authors of the best peer-reviewed paper published in AATCC Journal of Research each year.
Xuehong Ren is a Taihu Professor in the College of Textile Science and Engineering at Jiangnan University located in Wuxi, Jiangsu, China. He received his B.S. in Textile Chemical Engineering (Dyeing and Finishing) and M.S. in Textile Chemical Engineering at Soochow University in 1993 and 2002, respectively. He earned his Ph.D. in Polymer and Fiber Engineering from Auburn University in 2006. Prior to professorship at Jiangnan University, he was a Process Development Scientist at HaloSource Inc. in the U.S. He has been a member of AATCC since 2019. Ren has written or been a corresponding author on 153 peer-reviewed journal articles and has been a corresponding author on four different book chapters.
Contributing authors include Meng Zhang, a Research and Development Engineer at Tanatex Chemical Trading Company Ltd., in Shanghai, China, and Yan Zhang, an Intellectual Property Specialist at Pinghu Youpu Biosciences Co., Ltd. in Pinghu, Zhejiang, China. Tung-Shi Huang is a professor at Auburn University in Auburn, Alabama, U.S.A.
Lian-gang Zheng received his B.S. from Anhui Polytechnic University in 2017. He immediately began his graduate studies at Donghua University in Shanghai China, where he is currently a Ph.D. candidate in the College of Textiles. He has authored or co-authored seven papers and has recently received the Doctoral Academic Scholarship from Donghua University and the Excellent Paper Award of the 13th International Forum on Textile & Garment Innovation from Shanghai Textile Engineering Society.
Corresponding authors include Fujun Xu, a Professor and Vice Dean at the College of Textiles, Donghua University. Xu received a B.S. in 2005 and a Ph.D. in 2011 from Donghua University; during this time, he also received a joint Ph.D. from North Carolina State University. Xu has authored or co-authored 10 journal papers. Kun Zhang is a PhD candidate in the College of Textile at Donghua University, where he also received his BS degree. He has authored or co-authored six publications. Mohamed Amine Aouraghe is a Ph.D. candidate at Donghua University. He received an Engineering degree from ENSAIT in Roubaix, France and a Master of Research degree from the University of Lille 1, Lille, France. He has authored or co-authored seven publications. Sidra Saleemi is a Ph.D. candidate at Donghua University. She has authored or co-authored nine papers. She is also an Assistant Professor at the University of the Punjab in Lahore, Pakistan since 2014. Yanhong Cao received her Bachelor’s degree and recently completed her Master’s degree from the College of Textiles at Donghua University; she has published two papers. Yiping Qiu is a professor in the College of Textiles at Donghua University. He received his bachelors from Zhejiang Silk Institute of Technology, his masters from Auburn University, and his Ph.D. from Cornell University. He did his post-doctorate at Massachusetts Institute of Technology. He served as Dean of the College of Textiles at Donghua University from 2007 to 2013. He has co-authored ten papers and is an Editorial Board Member of Textile Research Journal and Fellow of the International Society of Advanced Materials and Manufacturing Engineering.
The award was presented at AATCC’s Textile Discovery Summit during the Awards Luncheon on November 18, 2021 in Durham, North Carolina.
Source: aatcc.org
Techtextil 2022 to feature open expert format with the Techtextil Forum – call for presentation now open
Techtextil, a leading international trade fair for technical textiles and nonwovens (June 21-24, 2022), will feature the Techtextil Forum, a multi-faceted setting for the exchange of ideas and information between exhibitors, visitors, researchers, developers and users of technical textiles with a host of lectures, discussions and interactive formats. Speakers interested in making a presentation at the Techtextil Forum are invited to submit their proposals February 6, 2022.
“As in the past, the Techtextil Forum 2022 will be held in the exhibition hall itself, which will give both visitors and exhibitors the opportunity to listen to selected lectures or spontaneously contribute to discussions between appointments. The lectures will also be streamed and available on-demand. Thus, the exchange of ideas and information within the sector will not only enrich proceedings at the fair itself but also in the digital sphere after the doors have closed,” said Michael Jänecke, director of Brand Management Technical Textiles and Textile Processing, Messe Frankfurt.
The focus of the coming Techtextil Forum will be on new developments, trends and potential areas of application for technical textiles, nonwovens and functional apparel textiles, as well as technologies, manufacturing processes and new products. Proposals for presentations can be made in the following fields: health (textiles in the medical sector / hygiene), interior, personal protective equipment and protection of objects (PPE), building textiles, (new) trends, textiles for mobility/moving around and sport & leisure. Speakers are invited to propose lectures, workshops or topics for discussion. The proposals must be submitted in English via the internet at https://techtextilforum2022.abstractmanagement.de. The contributions will be selected by an international program committee of experts.
For more information: techtextil.messefrankfurt.com/call-presentations
Source: techtextil.messefrankfurt.com
Hemingway Apparel becomes Hemingway Sewing Solutions
Investors affiliated with the Creative Fabrics division of Beverly Knits have purchased the assets of Hemingway Apparel. The new business, Hemingway Sewing Solutions, will continue to provide legacy cut and sew services to long-time apparel customers and will also expand into the assembly of mattress covers. As a result of the increased demand, the new company expects to hire an additional 50+ employees in early 2022 to support its Hemmingway, South Carolina, operation.
Jack Marsh, the founder of Hemingway Apparel commented, “I am very pleased that the Hemingway Apparel team will continue on as the Hemingway Sewing Solutions team. This is a great opportunity for growth and further investment for the people of Hemingway as well as Williamsburg and Florence counties.”
“A combination of factors led to the decision to invest and expand,” said Parker Sytz, the managing partner of Hemingway Sewing Solutions. “Over the past forty years, Jack Marsh and Hemingway Apparel have developed a solid reputation for providing quality cut and sew services to the apparel market. We will continue to offer these services and diversify into the growing market for knit engineered mattress ticking covers. We are very excited to invest locally in the equipment and people required for this growth.”
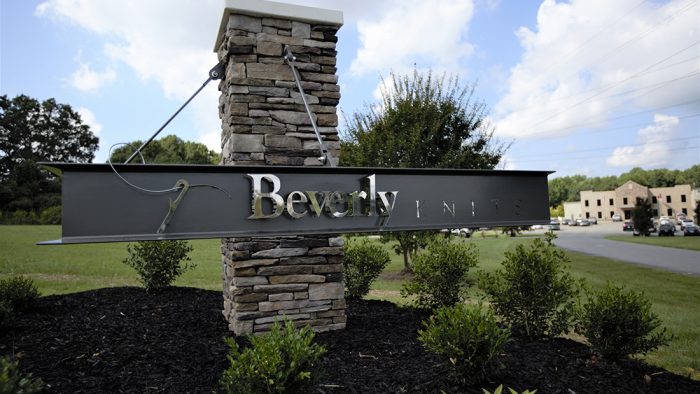
Hemingway Sewing Solutions will leverage a relationship with its affiliate, Beverly Knits, to foster what it expects to be immediate growth. With operations located just a few hours away in Gastonia, North Carolina, Beverly Knits specializes in knitting and finishing specialized fabrics and cut & sew mattress covers for the bedding market. Due to the strong growth in demand for their products, additional domestic cut and sew services are required.
Hemingway Sewing Solutions currently provides apparel cut and sew services for the sportswear, ready-to-wear and intimate apparel markets. In the coming weeks, Hemingway Sewing Solutions will begin hiring 50+ additional associates (assembly technicians through facility maintenance). www.hemingwaysewing.com
The affiliate Beverly Knits is one of the largest and most diverse circular knitters in the U.S., creating solutions for performance wear, athletic footwear, intimate apparel, outdoor products, mattress, and bedding, automotive, industrial, and medical, including PPE. Capabilities include specialized knitting, dying, finishing and cut & sew operations. The enterprise includes Beverly Knits, Altus Finishing and Creative (Fabrics and Creative Ticking).
Source: hemingwaysewing.com
B.I.G. Yarns announces investments in new yarn technology
B.I.G. Yarns announces significant investments in its next-generation Polyamide (PA) technology to help global carpet tile manufacturers meet the demands of the contract market. In addition to the investment, the company also announced its decision to become a new producer of polyester (PET) yarns for the automotive industry, offering a portfolio by the third quarter of 2022. These will be available applications alongside its EqoCycle recycled-based PA6 yarns.
The one-step 3Ply PA yarns will provide broader design options in the carpet tile segment. Total production capacity for one-step 3Ply yarns will increase by more than 20% through new lines installed at the plant in France.
“With the additional capacity in the best-in-class 1 step 3ply PA yarns technology and expanding our portfolio into a new direction with PET, B.I.G. Yarns is taking strategic steps to better serve the evolving needs of its customers,” said Emmanuel Colchen, general manager of B.I.G. Yarns. “We are opening up exciting new opportunities with a continuous focus on innovation and sustainability. We will generate an important step that will support our goal of reducing our carbon footprint. We want to build a strong future path for our business and our customers, and these investments advance that commitment in full alignment with our vision. We also like to acknowledge and thank the support of the Hauts-de-France region and French ‘Relance Program’ which supported our initiative strongly and selected our French production plant for the industrial investment acceleration fund. We are grateful for this encouragement and belief in the B.I.G. Yarns’ endeavors.”
The new lines use B.I.G. Yarns’ PA yarn technology which expands design, contrast and color freedoms for carpet tile manufacturers and increases flexibility in lot sizes. The new technology features a higher level of automation and optimized energy use, contributing to energy savings at the French site. The new product lines will be deployed mid-2022.
Source: beaulieuyarns.com
Lenzing Group awards High Fashion Group for sustainability and social responsibility
High Fashion Group was awarded the Tencel Strategic Partnership Award, China, from the Lenzing Group for its contributions to sustainability and social responsibility. The award follows the group obtaining the Global Recycled Standard (GRS) Certificate and becoming an official partner of bluesign system and Oeko-Tex.
As a long-term strategic partner of the Lenzing Group, High Fashion Group has joined hands with Tencel brand for a number of sustainable and innovative projects, ranging from innovative fabrics to sports fashion. Lenzing fibers are biodegradable and are derived from sustainable wood sources via sustainably managed forests. Tencel branded lyocell and modal fibers, Tencel Lyocell with Refibra technology, and Lenzing Ecovero branded viscose fibers by Lenzing have been used in the group’s garment production to increase product functionality and texture and embrace sustainability for environmental protection.
“Thank you Lenzing Group for supporting us throughout the sustainability journey,” said Will Lam, CEO of High Fashion Group. “This award reflects our commitment to become a leader in sustainable fashion. Other than using a range of green fibers in our garment production, we also adapt different innovative green technologies in our manufacturing sector in order to save energy, water and electricity for a more sustainable supply chain.”
Source: highfashion.com
Freudenberg Apparel Europe begins construction on competence center for interlinings
Freudenberg Performance Materials Apparel Europe business unit has started construction work on its competence center for finishing and coating base material for the apparel industry at its site in Sant´Omero, Italy. Further processing of base material is to begin in Italy in early 2023. The Weinheim site will then become the competence center for interlining base material.
In January 2021, Freudenberg Performance Materials Apparel Europe (Freudenberg) announced plans to set up two competence centers. In the future, the company will concentrate on manufacturing base material for interlinings at the Weinheim location. Base material finishing and coating is to be bundled at Sant´Omero. For this purpose, the production plant will be relocated from Weinheim to Sant´Omero and recommissioned in a newly built production hall.
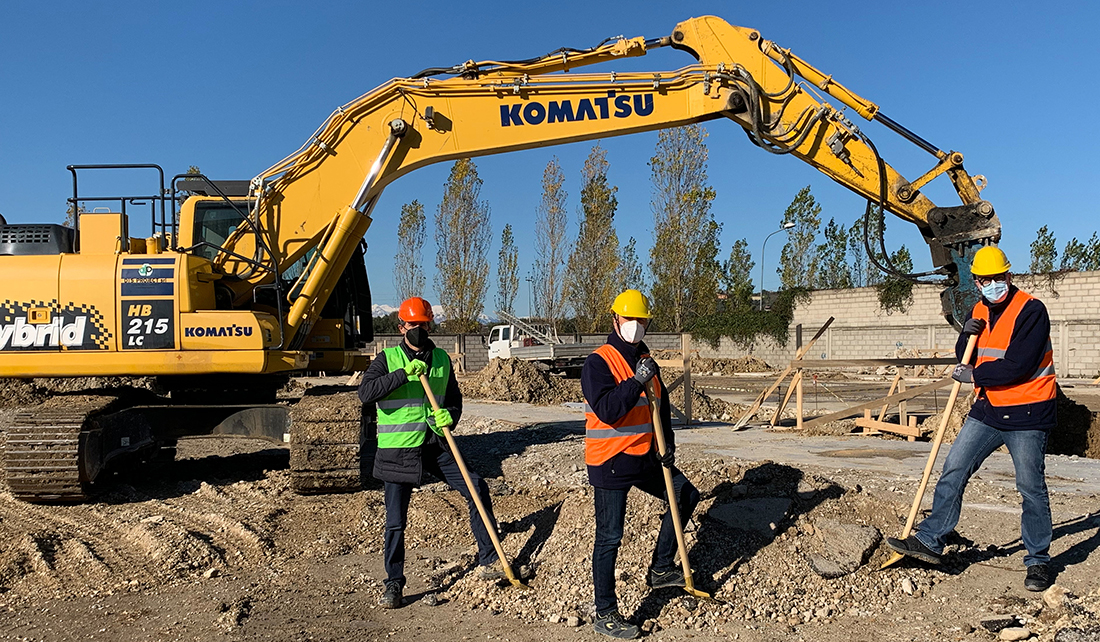
“Thanks to the outstanding work of our employees, this complex project is running to schedule despite the corona pandemic, and we have now reached this important milestone,” said Dr. Hannah Koeppen, general manager Freudenberg Performance Materials Apparel Europe. The traditional groundbreaking ceremony with senior representatives from local authorities and Freudenberg management was cancelled due to the high number of coronavirus cases in the area.
Source: freudenberg-pm.com
Trützschler in Mönchengladbach welcomes articulated robot arm from Igus
The Trützschler headquarters in Mönchengladbach, Germany, received the first Robolink articulated arm robot at its in-house training workshop. The arm robot is a gift from Igus and is intended for use in the company’s training programs.
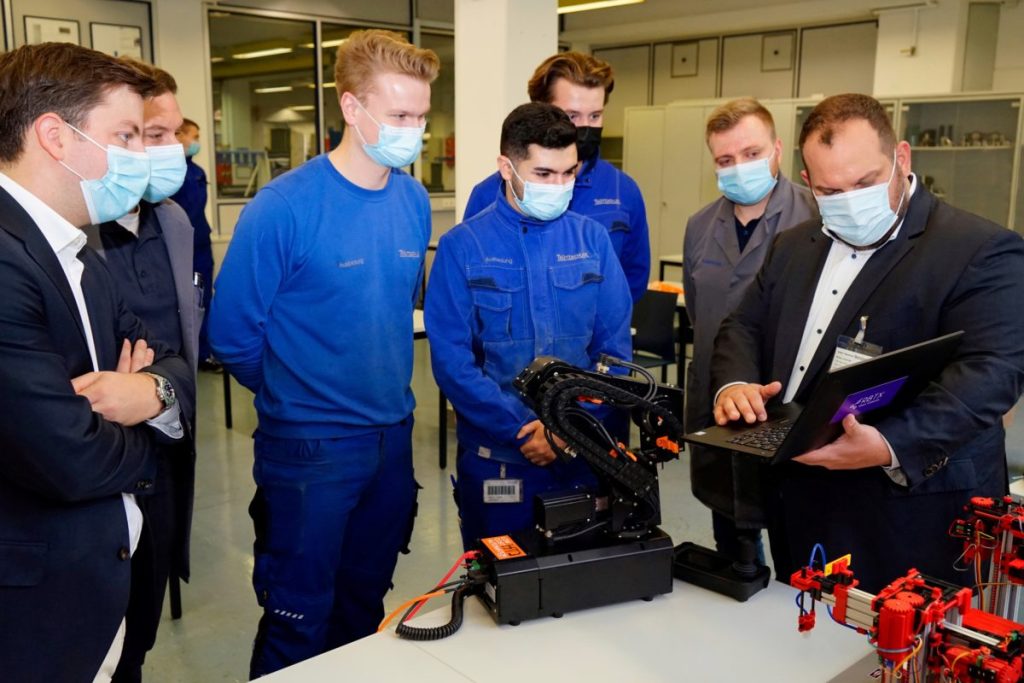
“The automation and optimization of a wide variety of processes is something Trützschler has always stood for,” said Dr. Michael Schürenkrämer. As early as the 1970s, we used the first welding robot in North Rhine-Westphalia. We strive to offer our apprentices an innovative training program that focuses on these topics. We are therefore more than pleased about this gesture by our partner Igus.”
Robolink is designed to allow tasks such as sorting components to become independent, therefore increasing efficiency by allowing employees to focus on more demanding tasks. The robot arm is controlled by a kind of joystick that can be used to train certain motion sequences.
“In principle, our applications are characterized by two special features: A low entry price by relying on high-performance plastics that are both durable and cost-effective, and an easy operation,” said Igus managing director Frank Blase. “It is a great added value that unskilled persons sometimes only need up to 30 minutes to program the robotic arm.”
Source: trutzschler.com
A.Celli Nonwovens appoints Francesco Vergentini as new General Manager
A.Celli Nonwovens– a leading manufacturer of high-performance master roll winders, slitter rewinders and intralogistics solutions for spunmelt, spunlace (hydroentangle), air-through bonded and laminated nonwovens roll goods production – appointed Francesco Vergentini as general manager.
Vergentini has extensive experience in the nonwovens and hygiene industries and is a mechanical engineer who began his career in 1997 in the production of machinery for the maintenance of railway vehicles.
He joined A.Celli Group in 2008, covering various roles in the technical and sales organization up to his role as chief technology officer (CTO).
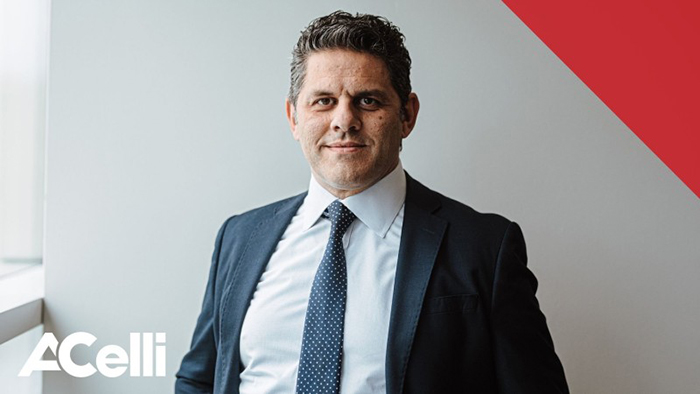
A.Celli Nonwovens
In his new role, Francesco will be involved in the development of strategic projects, increasing and implementing growth opportunities and researching and identifying business developments with priority and focus on digitalization and sustainability.
“This new assignment comes after two years that saw the company committed to making its contribution to deal with the pandemic, facing highly challenging conditions and achieving very satisfactory results,” said Vergentini. “I am proud of how the company reacted to the strong and unpredictable peak demand and of how the whole team has intercepted every opportunity and made it profitable. My mandate will be characterized by the management of these new dynamics by means of a strategy based on two guidelines: continuous improvement and organizational and process simplification. We will give priority to the product categories that are growing the most in our market and we will be agile and quick to better intercept the specific needs of our customers, with particular attention to the 2-CARE® department and to the reorganization of the offer and services related to after-sale.”
Source: acelli.it
Ehab Abou-Oaf named president of Kimberly-Clark Professional
Kimberly-Clark Corporation (NYSE: KMB) today announced that Ehab Abou-Oaf, currently managing director of Kimberly-Clark’s Middle East and Africa business, has been named president of Kimberly-Clark Professional, effective January 1, 2022.
Abou-Oaf will be responsible for Kimberly-Clark’s business-to-business operations globally, and will report to Mike Hsu, chairman and CEO.
“Since joining Kimberly-Clark, Ehab has strengthened our business in the Middle East and Africa, establishing new routes to market and grown our market share across multiple categories in developing markets including Nigeria and South Africa. Further, he has established an exceptional team in the region, and I’m confident that he’ll bring the same proven track record of leadership to our K-C Professional business,” said Hsu.
Prior to Kimberly-Clark, Abou-Oaf spent 19 years in senior management roles with Mars, Inc, including president, Mars Wrigley Confectionery for Asia, Australia, Middle East & Africa, based in Singapore. Prior to joining Mars, he spent 10 years with Procter & Gamble in packaging, product development and marketing roles. During his extensive career, Abou-Oaf has worked in Saudi Arabia, Belgium, Japan, Egypt and China.
Source: kcprofessional.com
Armand Ajdari joins Arkema as Chief Technology Officer
Effective January 1, 2022, Armand Ajdari has been named chief technology officer at Arkema and will be a member of the group management committee. Ajdari has a background with 30 years of research and development in international environments, particularly with the Saint-Gobain group, bringing technological and commercial relationship experience to Arkema.
After earning a Ph.D. in Theoretical Physics at the Pierre et Marie Curie University in Paris, and an engineering diploma at the École Polytechnique, Ajdari undertook various multidisciplinary research activities within the Centre National de la Recherche Scientifique (CNRS) for 15 years.
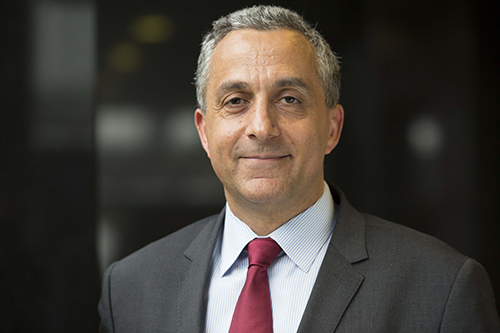
Arkema
He then joined the Saint-Gobain group in 2007 where he held different positions, including senior vice president of R&D for the Innovative Materials sector.
Since 2017, he has served as executive vice president of R&D for the Saint-Gobain group.
Source: arkema.com
Tony Fragnito will oversee INDA’s business operations
The Association of the Nonwoven Fabrics Industry (INDA) announced that Tony Fragnito has joined the company as chief operating officer, reporting to INDA president, Dave Rousse. In this new role, Fragnito will be involved in updating INDA’s strategic plan.

INDA, Chief Operating Officer
Fragnito brings decades of leadership experience assisting trade and professional organizations in realizing their organizational and operational potential. A certified public accountant, Tony also brings strong financial acumen in addition to extensive technology, human resource and program management accomplishments from organizations representing a variety of professions and industries. He most recently served as chief financial officer for the International Society of Automation (ISA) in Research Triangle Park, NC. Before that he was chief executive officer of XBRL International, Inc. an international consortium of companies, which developed and promoted technologies for the collection of business and financial data. He is a graduate of George Mason University.
Source: inda.org
* International Fiber Journal is owned by INDA, Association of the Nonwoven Fabrics Industry (inda.org).
Bio-based Sorona faux fur featured on Bravo’s Project Runway
Bravo’s Project Runway surprised contestants with a competition featuring faux fur made with Sorona. Sorona, in collaboration with Ecopel, developed Koba, a bio-based faux fur collection. In the Avant Garde challenge, designers were paired up and asked to select from over 200 yards of the plant-based and recyclable faux fur in a wide range of colors, patterns and lengths. Judges Nina Garcia and Elaine Welteroth were joined by guest judge Esteban Cortazar and famously avant garde actor and singer Billy Porter.
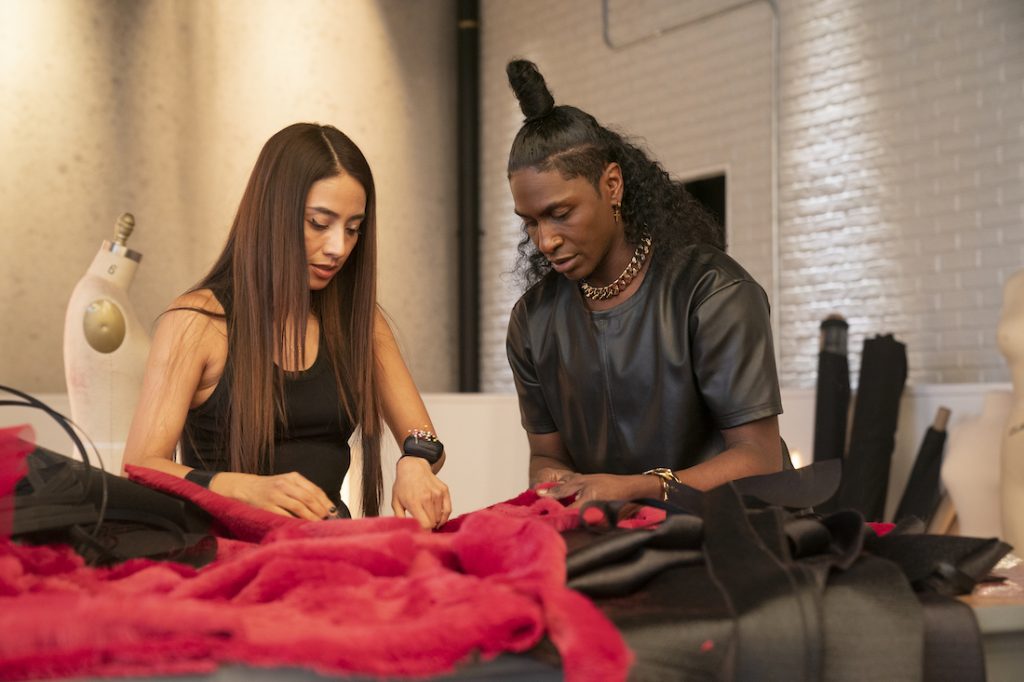
“This episode of Bravo’s Project Runway is a call to action for the industry. Luxury and faux fur are not mutually exclusive,” says Sorona global brand & communications leader, Alexa Raab. “The world’s most influential thought leaders in fashion and media are advocating for innovative, sustainable fabrics. We’re proud to answer the call with options like the bio-based faux fur we offer in collaboration with Ecopel, called Koba.”
The faux options mimicked leopard, cheetah, coyote, wool and rabbit. The ethical alternative is also sustainable as faux furs made with bio-based Sorona polymer fibers can be recycled.
Sorona has been used by brands and designers such as Stella McCartney, Maison Atia and Karl Lagerfeld.
Source: sorona.com
Spinnova-Suzano factory makes headway in Finland
Woodspin, the joint venture of Spinnova and Suzano, is proceeding with its factory project on the south side of Jyväskylä in Central Finland. The production spaces for manufacturing the sustainable Spinnova fiber are expected to be ready for technology installations at the end of summer 2022, with the factory set to be completed by end of 2022.
The factory complex will include Spinnova’s and Suzano’s joint venture Woodspin’s fiber production, Suzano Finland’s micro-fibrillated cellulose (MFC) refining, as well as Spinnova’s headquarters and some of its product development functions. For Suzano, the MFC refining investment is the company’s first investment outside of Brazil.
Spinnova has also designed the factory’s energy solutions to ensure a low-emission facility that runs on 100% renewable energy and recovered heat energy. In addition, the factory is planned to transfer excess energy back into the district heating network.
Source: spinnova.com
Multi-million dollar grant awarded to pilot decomposition of textile waste technology
The Biomimicry Institute has been awarded EUR 2.5 million to lead a multi-year initiative called Design for Decomposition. By embracing true decomposition—the way leaves break down into soil to build healthy ecosystems—the initiative will demonstrate scalable new pathways for the ~92 million tonnes of fashion waste discarded annually. The initiative is a follow-up to the Institute’s The Nature of Fashion report in 2020, which identified decomposition as the missing link for the sector.
Together with Laudes Foundation, Hong Kong Research Institute of Textiles and Apparel (HKRITA), Yale Center for Green Chemistry and Green Engineering, Metabolic Institute, The OR Foundation, and Celery Design, the Biomimicry Institute will pilot technologies that convert wasted clothes and textiles into biocompatible raw materials. The multi-year Design for Decomposition initiative will host pilots in Western Europe and Ghana, testing the most viable decomposition technologies that are commercially viable but have yet to scale.
The initiative begins with a deep-dive into biological research about the various types and circumstances of natural decomposition and then matches those approaches to the hundreds of known decomposition technologies to determine which best model nature. In the pilot phase these approaches will be tested in Accra, Ghana, which receives about 15 million used garments each week, and also in a city like Amsterdam or Berlin with more established waste management infrastructure. Simultaneously, researchers at Yale will be looking at what really decomposes and how.
With catalytic funding from Laudes Foundation, the initiative is part of its fashion materials portfolio
More than a third of all microplastic pollution—some 500,000 tonnes—are released each year from clothing, most ending up in oceans. Knowing that over 60% of garments are plastic-based and nearly all apparel is made with toxic processes, dyes, and coatings, the foremost question in the initiative is: what will this post-consumer waste decompose into that is not hazardous? All decomposition technologies are being screened through this lens, and the team has engaged toxicology partners from the Scripps Institution of Oceanography at UC San Diego, University of Ghana, and Yale.
After proving that advanced decomposition is viable locally, the joint partnership plans to prove that this system change can scale globally.
Source: biomimicry.org
Sateri becomes China’s first lyocell producer to be Oeko-Tex STeP certified
Sateri’s Lyocell facility in Rizhao, Shandong Province, China, has been awarded the Sustainable Textile Production (STeP) certification for responsible production, making it the first lyocell producer in China to be certified to the standards set by independent Swiss-based certification organisation Oeko-Tex. Sateri’s lyocell facility has also obtained the highest ranking of level three in the certification assessment scoring for exemplary implementation of best manufacturing practices.
Together with its earlier achievement of the Standard 100 by Oeko-Tex certification that confirms its lyocell fiber is free from any harmful substances and complies with European standards, Sateri’s lyocell products are qualified to carry the “Made in Green” product label by Oeko-Tex.
The STeP by Oeko-Tex certification comprises three levels describing the extent to which a company has achieved sustainable production and working conditions of factories in the textile industry. The areas of assessment include chemicals management, environmental performance, environmental management, social responsibility, quality management, as well as occupational health and safety.
Sateri’s lyocell fiber factory in Rizhao commenced operation in May 2020, with an annual output of 20,000 tonnes of lyocell fiber. The same site houses a 5,000 tonne lyocell pilot production line dedicated for the development of lyocell application technology. In March 2021, the group announced plans to expand its lyocell annual production capacity in China up to 500,000 tonnes by 2025.
A natural and biodegradable fibre, Sateri’s lyocell is made from wood pulp sourced from certified and sustainable plantations. It is manufactured using closed-loop technology, requiring minimal chemical input during the production process, and utilizing an organic solvent that can be almost fully (99.7%) recovered and recycled.
Source: sateri.com
Aeon launches line of pure white undershirts made of Celliant infrared fiber
Aeon, the largest retailer in Asia, is introducing a line of undershirts called Topvalu Select Celliant, using the first-ever Celliant fibers from Hologenix that are pure white in color. The offering will be available in about 350 stores throughout Japan and at Aeon’s official online store, Aeon Style Online.
Topvalu Select Celliant offers the benefits of Celliant fiber, a responsive textile that captures and converts body heat into infrared, with the pure white color Aeon customers have requested.
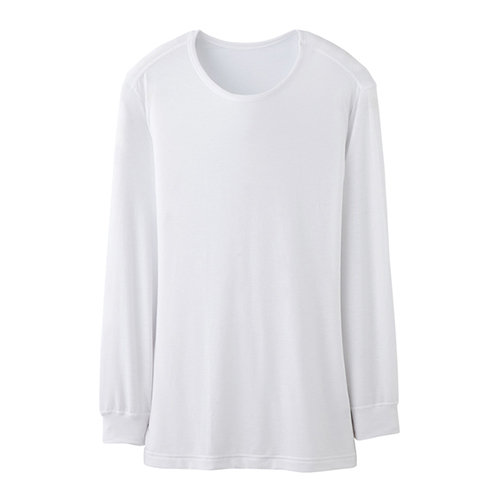
Many men prefer to wear white undershirts under their business shirts in Japan. In response to such demands, Aeon planned and developed the pure white Celliant undershirt for the first time. Topvalu Select Celliant is registered as a general medical device in Japan.
Celliant mineral-infused fabrics have been shown to help regulate body temperature and improve local circulation in healthy individuals for faster recovery, better sleep and stronger performance during the day.
“We are very excited by the introduction of the first-ever Celliant product in pure white,” said Seth Casden, Hologenix co-founder and CEO. “Achieving this pure white color took a lot of dedicated effort from our global research team and we commend Aeon for being the first to introduce it to the consumer market.”
For more information: https://aeonretail.com/list/celliant.
Source: celliant.com
Mondi remains in top 1% of companies assessed by EcoVadis with Platinum rating for sustainability
Packaging and paper manufacturer Mondi has maintained its platinum status in the EcoVadis CSR ratings in recognition of the group’s strong commitment to sustainability. The award places Mondi in the top 1% of companies assessed globally, a position it has held since 2015.
EcoVadis is a recognized business sustainability ratings organization covering 200 industry categories, 160 countries, and 75,000 companies of all sizes worldwide. Every year the organization assesses companies’ performance in terms of how well they have integrated the principles of sustainability into their businesses and management systems. The methodology is built on international sustainability standards, including the Global Reporting Initiative, United Nations Global Compact, and ISO 26000, and covers 21 indicators in four key areas: environment, labor and human rights, ethics, and sustainable procurement.
Mondi’s overall EcoVadis score of 85% for 2021 is up from 82% in last year’s assessment, with 90% in the
Environment and Labor & Human Rights categories.
Mondi announced its ambitious Mondi Action Plan 2030 (MAP2030) sustainability framework and commitments at the beginning of 2021. MAP2030 sets out the actions the company will take to meet its sustainability goals in the coming decade. The commitments focus on three action areas: circular driven packaging and paper solutions; created by empowered people; taking action on climate. All areas are aligned to the UN Sustainable Development Goals as part of Mondi’s focus on being sustainable by design. Find full details on the Mondi Action Plan 2030 here.
Source: mondigroup.com