Messe Frankfurt brought its Techtextil and Texprocess program to a global audience, May 14-17, 2019, in its home city of Frankfurt. With a total of 1,818 exhibitors from 59 countries and, in all, some 47,000 trade visitors from 116 countries, the event broke a record for number of exhibitors and was essentially on par with its all-time high for number of visitors. By comparison, the 2017 edition of Techtextil and Texprocess saw a total of 1,789 exhibitors from 66 countries and 47,388 visitors from 114 countries.
Techtextil and Texprocess have evolved over the years to separate somewhat from other large technical textile-related events. Partnering with third-party organizations and academia, the sister programs leverage external perspectives to present unique conference programming that advances the conversation on technical textiles without overshadowing the companies showcasing their wares inside the exhibit halls.
After four days of soaking it all in at the Messe, the following represent 4 key takeaways from Techtextil and Texprocess 2019.
1. Trade Show, Or Art Show?
Following up its 2017 “Living in Space” theme, Techtextil and Texprocess worked with Creative Holland, an initiative of the Dutch creative industries, to develop a special presentation, “Urban Living – City of the Future,” which examined the role that textiles and textile composites can play in the future of cities.
With the United Nations predicting nearly 70 percent of the world’s population will be living in urban regions, metropolises and megacities by 2050, “Urban Living – City of the Future” showcased how textiles will help overcome the challenges of urban living in the future, such as construction, mobility, health, smart fashion, and functional clothing.
Partnering with Creative Holland was a natural fit, as the Netherlands has a rich textile heritage. The first textile factories in the Netherlands were built in 1850, and after 1900 the Dutch textile industry flourished, with textiles remaining an influential part of life in the Netherlands today.
Curated by Stijlinstituut Amsterdam, “Urban Living – City of the Future” featured a range of forward-looking exhibits, including the use of color and fabrics to create a sense of movement (Rombout Frieling), pods constructed from technical textiles and nonwovens developed to support Elon Musk’s Hyperloop project (TU Delft), and an artificial womb that utilized synthetically produced fibers to create an artificial uterus in which premature infants can develop to full term (Next Nature), among others.
The exhibit was unique in that it brought a museum-quality program to a technical business-to-business trade show.
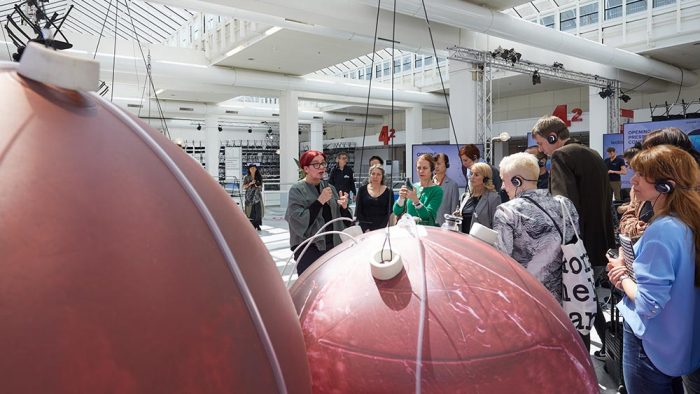
2. Technical Textiles Growing In Importance
The EU textile and clothing industry continues to post strong annual results as the second decade of the 2000s nears an end. According to data by Eurostat and EURATEX, the industry had a turnover of € 178 billion in 2018, a minimal increase over 2017’s € 177.6 billion turnover, but significantly above the 2013 figure of € 163.8 billion. Investments also increased slightly in 2018 to € 5.0 billion, continuing a trend of annual increases which dates back to 2013.
Employment of 1.66 million in 2018 marked a small annual dip compared to 2017, but remained essentially unchanged over the past five years – which EURATEX characterized as a remarkable achievement for a sector that has implemented significant labor efficiencies in recent years. As a result, the average turnover per employee has increased from 97,000 € in 2013 to 107,000 € in 2018, while turnover and value-added per employee have increased by more than 30 percent over the past decade.
According to EURATEX, exports remain a bright spot for the EU textile industry, as exports grew by 7 percent compared to 2017 and for the first time reached € 50 billion. The industry’s extra-EU exports, stand at 28 percent of annual turnover, up from less than 20 percent 10 years ago.
Meanwhile, technical textiles are an undisputed success story for the EU. While EURATEX acknowledges that exact figures for this part of the industry are difficult to compute due to the dual use of many yarns and fabrics for both technical and conventional applications, it estimates that EU industry turnover of technical textiles, (including yarn-type, fabric-type and nonwoven materials, but excluding any made-up articles) reached about € 24 billion or 27 percent of total textile industry turnover. Over the years this percentage has steadily grown and is expected to continue to do so in the future.
Italy and Germany are Europe’s biggest producers of technical textiles, each producing over € 4.5 billion worth of technical textiles per year. The highest share for technical textiles in national textile turnover is registered in Scandinavian countries, such as Sweden and Finland and central European countries such as Germany, the Czech Republic or Slovenia. The fastest growth of technical textiles over the past 10 years has been achieved by Poland, followed by Belgium, Austria and Portugal, according to EURATEX.
Labor productivity is much higher in the technical textiles part of the industry. Turnover per employee stands at € 215,000, more than twice the average textile and clothing industry rate.
In terms of international trade, European exports and imports of technical textiles have grown continuously over the years, with an almost zero trade balance in Euro terms. However, EURATEX points out that when looking into the product category types, it is clear that Europe’s trade balance is positive in higher added value products such as medical textiles, highly technical finished fabrics and nonwovens, but negative in such categories as bags, sacks, tarpaulins, or cleaning cloths.
Again the United States is Europe’s largest technical textiles customer, followed by China, which has registered very fast growth in recent years.
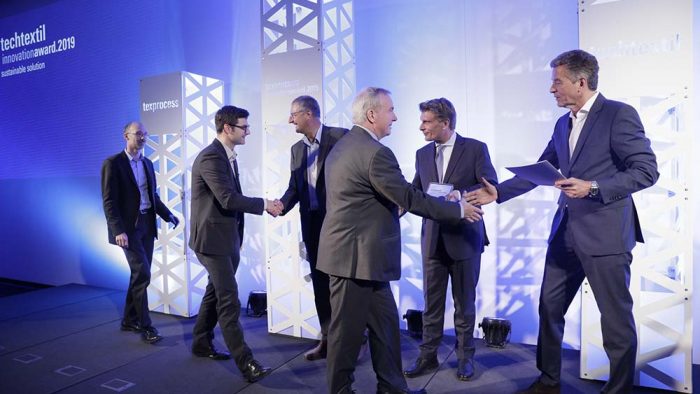
3. Much Ado About Sustainability and Circularity
As is the case at most textile-related events today, sustainability and circular economy were central to many of the exhibits and press conferences at Techtextil and Texprocess.
Taking “Towards sustainability” as its motto, Techtextil featured a forum highlighting contributions devoted exclusively to sustainable textile innovations. Chaired by Braz Costa, managing director of the Portuguese technology center CITEVE, the program covered textile recycling (TWD Fibres, Velener Textil), sustainable construction with wool (Minet S.A., Romania), sustainable textile coatings (Centexbel), biopolymers (RWTH Aachen University), traceability of GMO-free cotton (Hohenstein Institute) and low-cost, bio-based carbon fibers (Jules Verne Research Institute, France).
A Manifesto to Deliver a Circular Economy In Textiles
EURATEX held a press conference at the show to announce an initiative by European textile and fashion industry organizations to advocate for the development of the tools and systems necessary to enable the scaling of circular economy programs. As a launching point for the initiative, EURATEX and other supporting industry organizations, published a manifesto acknowledging that the infrastructure required to enable true, scalable circular solutions in the textile industry is inadequate and, likewise, many issues need to be addressed for circular economy to move from mere talking point to real-world application. Issues pinpointed in the manifesto include:
- Circularity requires partnerships and collaboration on a global, not regional, scale.
- Industry must work to empower and inspire consumers to participate in circular solutions.
- Public-private partnerships will be required to innovate and incentivize circular solutions.
- Policy incentives for both the fashion and textile sectors and the supporting infrastructure will be required to advance the circular economy.
To download a full copy of “A Manifesto to Deliver a Circular Economy in Textiles,” visit bit.ly/Circular-Economy-Manifesto (case sensitive URL).
No Textile to Waste
ClubTex, an industry association that represents technical textile companies in Hauts-de-France region of France, along with its partner organization, Up-Tex, an organization focused on helping to foster innovation and business creation for the Hauts-de-France textile industry, were on hand at Techtextil to tout a new program, Retex, which focuses on enabling manufacturing processes for recycled textile waste. The program aims to integrate recycled textile waste and post-consumer textile products into the manufacturing loop for new eco-designed textile products or non-textile applications, such as in plastics manufacturing.
Utexbel, a company that participates in the Retex program, showcased garments made of its recycled yarns. Utexbel is currently participating in a project set up by Retex, which has succeeded in closing the manufacturing loop by producing a fabric for nursing apparel based on end-of-life garments collected from Dutch hospitals. The end-of-life garments are processed down to the fiber level, and the fiber is then used to produce new work clothes for nurses.
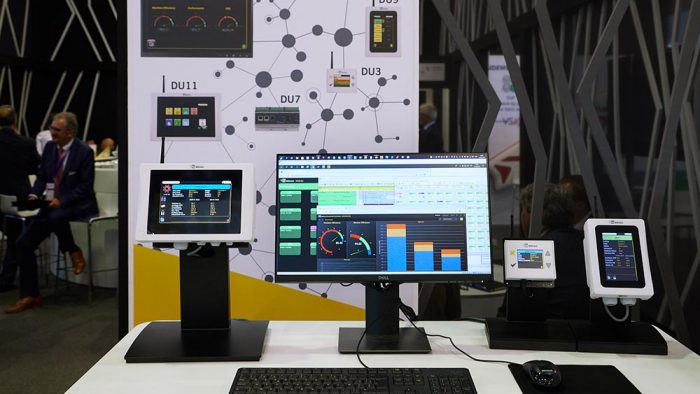
2 Awards Recognize Sustainable Solutions
For the first time, two awards were issued in the “Sustainability” category of the Techtextil Innovation Awards program. The first of which went to a working group comprised of Comfil (Denmark), Chemosvit Fibrochem (Slovakia), the Fraunhofer Institute for Chemical Technology ICT (Germany), and the Technical University of Denmark and Centexbel (Belgium) for BIO4SELF, a fully bio-based, self-reinforced polymer composite based on PLA fibers. The composite can be used in the fields of automobile manufacturing, the sports industry, and medical technology.
The second award went to PICASSO, a joint venture of Portuguese project partners for the development of a coloration and functionalization process for garments based on natural extracts from residues and/or species of mushrooms and plants, as well as enzymes. Project partners include the Centre for Nanotechnology and Smart Materials (CeNTI), the Tintex sustainable textiles company, spice and herb producer Ervital, biotech company Bioinvitro Biotecnologia, and the CITEVE textile technology center.
4. Digitalization and Industry 4.0
Texprocess, which is focused on the machine, plant and process side of the textile industry, was heavy on digitalization and what has come to be known as Industry 4.0. From fully networked production lines in the form of micro-factories and machines capable of autonomous learning to cloud-based collaboration between designers, product developers, manufactures and retailers across national boundaries, it was clear automation and big data will be playing key roles in the future of the textile industry.
VDMA, the mechanical engineering industry association for Germany and Europe, and its Textile Care, Fabric and Leather Technologies business unit, a conceptual partner in Texprocess, emphasized the progress textile manufacturers are making on digitalization, automation, robotics and artificial intelligence. Elgar Straub, managing director of VDMA Textile Care, Fabric and Leather Technologies, noted that many manufacturers are already working on digitizing the entire value chain: 3D body scanners and 3D simulation software are used in design and collection creation; materials are cleared on cutting tables with robots and gripping systems; and manufacturers of sewing machines are already networking complete factories across national borders, with real-time analysis of the machine data obtained.
VDMA Textile Care, Fabric and Leather Technologies also hosted an Industry 4.0 press conference highlighting several case studies from member companies as a build-up to the ITMA textile machinery trade show, June 20-26 in Barcelona. Herzog, a leading company in braiding technology, introduced the company’s latest Industry 4.0. product – an app-box that allows customers to easily access the data of Herzog and other machines, e.g., on a PLC (Programmable Logic Controller).
Mahlo, a provider of measurement and control systems for textile manufacturers, showcased a new platform for grouping, optimizing and standardizing “services” to enable the creation of modular hardware and software function blocks that can also be retrofitted. The optimized hardware and software results in a faster and more efficient controller solutions.
Lindauer DORNIER, a leader in weaving machines, discussed a new portal offering based on database technology that provides an online shop with permanent availability for original parts for all product lines. The solution will also facilitate remote maintenance and networking of weaving machines – to improve run characteristics, for example – with the aim of making the job of machine operators and production planners easier.