With the development of more diversified post-consumer products for technical applications or nonwovens, fiber producers are challenged to produce an increasingly high variety of fiber types, even though most of the fiber consumption is used for spun yarns for the production of textiles, which are mainly “cotton-type” fibers. Polyester plays a dominant role and is still growing worldwide with a 4% average per year.

Cotton type staple fibers
Typical fiber lines currently have capacities of 150-225 tpd and are directly fed by PET melt coming from polycondensation reactors, which are spun and drawn with a 2-step or conventional process. These fibers are not low-grade products, but require reliable production equipment and consistent manufacturing conditions. The melt should have a minimum variation of viscosity, temperature, homogeneity and stable chemical composition. Each variation may quickly be reflected in increased filament breaks or undesirable variation of fiber properties. In order to reach a typical capacity of 240 kg/h per spinning position, and final tenacities beyond 5.7 cN/dtex, spinning and quenching in the Trützschler spinning system, which is based on a Technip-Zimmer license, has been further optimized by FEM simulation. The number of filaments and the dimensions of the capillaries in the spinneret are adapted for the corresponding fiber size to reach the maximum fiber quality. For absolutely uniform application of spin-finish, the combination of a ring and a slot oiler is used. Drawing and tow plating are carried out with the established draw off, feeding and traversing units from Trützschler.
The subsequent drawing of these fibers is carried out on the well-proven FLEISSNER fiber lines. The highlight of the equipment is the jumbo crimper having a 660 mm working width. Of course all the other equipment, draw stands, calenders, baths, and ovens are known to have a high reliability and sustainability and therefore are still the preferred choice of all leading fiber producers.
Beside textile fibers, applications for nonwovens, fiberfill and short cut have reached remarkable market shares.
Short cut staple fibers
Fibers for hydro-entangled nonwovens are produced more or less on lines with the same equipment as for spun yarn applications. Fibers for other applications often need special equipment and technology. While fibers for fiberfill applications are “forgiving” some disturbances during production, short cut fibers have to be free of fiber breaks and must have high fiber tenacity and low elongation. Every drip from spinning and fiber loops from other process steps may cause a break of cutting knives and is not acceptable within the final product. Experience has shown that the SDD-module of Trützschler MMF with individual torque drives for each roller reduces disturbances to a minimum, while perfect fiber properties are reached. The cutting machine of Trützschler allows the production of short cut fibers with a minimum length of 4 mm. The monitoring of the blades has been further optimized with a new sensor technology and offers an improved production safety.
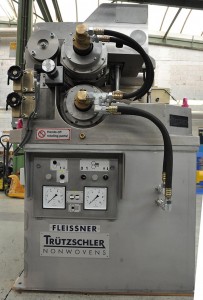
Hollow-conjugate staple fibers
Fiberfill fibers are mainly produced from PET flakes and are available as 2D and 3D crimped fibers. Typical fiber fineness of 6 or 15 denier is sufficient for most applications. New nonwoven types require 3D fibers with even lower fineness. An improved spinning process with an asymmetric capillary geometry opens new prospects to produce hollow-conjugate fibers with improved hollowness and bulkiness. There is also a potential to produce fibers at lower fiber fineness. With this technology the cross section of the fibers has a D shape and is therefore easily recognized. Capacities of 240 kg/h per spinneret have been successfully reached.
A challenge is the uniformity of the silicone coating through the complete fiber bundle, especially for capacities higher than 60 tons per day. Here, Trützschler MMF has also developed a new method avoiding a sheath-core effect of silicone within the fiber tows. A higher uniformity of this distribution avoids problems during carding and reduces the tendency of forming lumps in pillows, the most common application of fiberfill fibers.
Spinning using PET Flakes
Generally all fiber types can be produced from bottle flakes provided the raw material quality is consistent and has a sufficient purity. For compensation of remaining variations Trützschler has successfully installed twin-screw extruders, which have a superior homogenization behavior. In combination with suitable screen changers, fibers smaller than 3 den can be produced without having trouble with broken filaments or fused fibers. The latter is the most critical problem for carding machinery. The major business of Trützschler is producing machines from blow room to combing for the subsequent processing of staple fibers into spun yarns and nonwovens. This know-how enables the company to fully understand the needs of their customers – the fiber producers. Many of them own a combination of Trützschler staple fiber lines and carding machines.
Compact spinning process
Compact spinning lines are a very economic alternative for the production of nonwoven fibers, especially for fibers with fineness higher than 3 den. Typical capacities are between 24 and 48 tons per day at typical crimping speeds between 120 and 160 meters per minute. Those lines are also used for Polypropylene (PP), especially for the production of fibers for geotextiles with tenacities even higher than 6 cN/dtex. Advantages are lower investment costs compared to conventional lines, higher flexibility for melt-dyed fibers and less personnel. The components of Trützschler Man-Made Fibers are known to be optimized for this process and are absolutely reliable. In particular, for the use of PET flakes, their technology has proven extended spin pack life and improved quality levels regarding broken filaments and fused fibers.
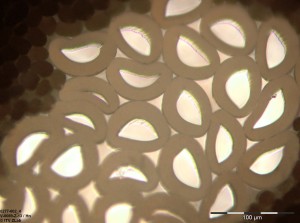
Process technology
In Trützschler’s technical centers in Germany, it is possible to produce fibers and to convert them into corresponding products. Trützschler Laboratory Equipment in Egelsbach consists of several spinning positions and one pilot draw line for the production of staple fibers. These fibers can be converted into nonwovens either at the Aquajet, a hydro-entangling line, within the same building; or with needle-punch and thermobonding technology in the technical center of Trützschler Nonwovens in Dülmen. The preparation of fibers for the conversion into spun yarn is possible in the technical center in Mönchengladbach where the newest equipment from blow room to combing is available. Together with the existing engineering capacities it is possible to get turnkey fiber lines for complete process chains, which will meet the needs of the individual fiber producer.