In such a competitive field as textile fibers, innovation is nowadays at the center of all industrial debates: the market increasingly seeks more efficiency with novel functionalities, product differentiation, etc.
One way to achieve these performances is though incremental research – taking small steps toward the definition of a new product.
Technological breakthrough is another way of changing the range of functionalities that are technically available. With what may seem a farfetched concept, our approach was to start from scratch and basically pioneer a new way of producing fibers.
By taking on challenges and opportunities, this goal has been achieved after four years of research at the French Institute of Textile and Clothing in cooperation with the University of Reims Champagne-Ardenne.

Promising results on fiber properties and production technology benefits have encouraged further research to move from the laboratory scale to industrial production.
The main benefit of this new spinning technology is the possibility of creating a new, wide range of genuine fibers while decreasing industrial operating costs.
For several decades, manmade fiber spinning has largely been undertaken when the polymer is either molten or dissolved. Along with advances in chemistry, textile fiber producers and researchers have been exploiting these polymers, resulting in the market introduction of just a few new fibers per decade since the advent of artificial silk.
From a technical viewpoint, this new spinning process is fundamentally different since it uses a room temperature, solvent-free, low-viscosity mixture of non-polymeric raw materials.
A blend of short-length oligomers, monomers, additives and reactive diluents is poured into a reservoir and then extruded through spinnerets in the liquid state. After extrusion, a polymerization system is activated to transform the liquid into a solid fibrous structure (Figure 1).
The upstream mixture is a homemade preparation using commercially available chemical compounds. Further, the blend can be made from renewable resources, such as modified vegetable oils or petroleum-based resources. In each case, the working viscosity is only about a few pascal-seconds (Pa.s).
The extrusion parameters are set to ensure flow stability during the polymerization reaction, which occurs within a few milliseconds[1].
At the laboratory scale, an extrusion speed up to 0.9 kg/h has been achieved to produce a single monofilament that is collected onto a rotating spool. A further step of fiber drawing may be possible, although this has not yet been experimented.
By saving thermal and mechanical energy, and avoiding solvent recollection, the overall consumption has been estimated at 3,000 kWh to produce 1 kg of monofilament.
Once the technology was confirmed at the laboratory scale, fiber characterization was carried out. Surprisingly, the fiber was able to float on water with a calculated density of less than 1. This physical feature may be partly attributable to the polymerization step after extrusion whereby a three-dimensional micro porous molecular network is generated.
This specific fiber microstructure is also revealed by a glass transition temperature of less than room temperature, accounting for a rubber-like thermo mechanical behavior until thermal degradation.
The polymer does not melt owing to the absence of a crystalline phase and therefore can be classified as a thermoset. As a result, the fibers can withstand many solvents, such as alcohols and acids.
However, in the laboratory, fibers were only produced at a coarse diameter (210–400 µm) and counts of 250–500 dtex with an average tenacity of 2 cN/tex (Figure 2). The fiber is knot resistant and exhibits a moisture regain of about 4%.
In the pursuit of sustainability, not only is it desirable to process “green” raw materials, but also to reduce energy consumption. Our technology differentiates from all others because it combines both approaches.
Laboratory fibers were made from modified vegetable oil blends without the use of thermal energy during extrusion, which resulted de facto in cost savings.
But however beneficial it is to reduce operating costs, this new technology also offers additional potential for industrial fiber producers: agile and compact production lines; a short time to production regime; low waste (solid, liquid, gas); low investment costs; rapid set-up for steady production; and ease of cleaning. All these benefits could create a safer and more productive way to produce fibers while meeting new niche market needs and targeted end-performances.
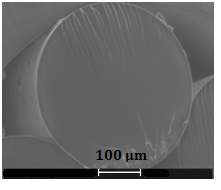
So far, there is neither a full list of attainable fiber properties nor an existing paradigm to describe this technology. However, starting from a new process, multiple combinations of blends are possible and the range of chemistries allowed by the process is endless, which leads to new industrial prospects for more demanding market-driven requirements and specifications in technical textiles (chemical resistance, lightness, etc.).
For each application (medical, filtration, composite reinforcement, etc.), tailoring the fiber is possible by engineering the formulation recipe. Thermo- or solvent-sensitive additives could therefore be employed in the dope, extruded and transformed into a fiber, bringing about long-lasting functionalities integrated into the fiber.
At this stage of the research and innovation process, further developments are expected to aim at reducing the fiber diameter while maintaining its tenacity and increasing production throughput. These two objectives could be achieved by designing dedicated heavy-duty extrusion equipment at the pilot/semi-industrial scale.
The laboratory setup has been developed in parallel with the chemistry and inherent to the requirements for high reactivity during polymerization. This comprised a metering pump delivering the low viscosity to a single syringe head used as an extrusion device. The mixture throughput could then be easily controlled to adjust the flow velocity to the reactive polymerization step.
To move beyond the laboratory scale, IFTH is now searching for industrial partners to build extrusion machineries adapted to this process.
[1] For the purpose of patent delivery, the polymer synthesis step remains confidential.